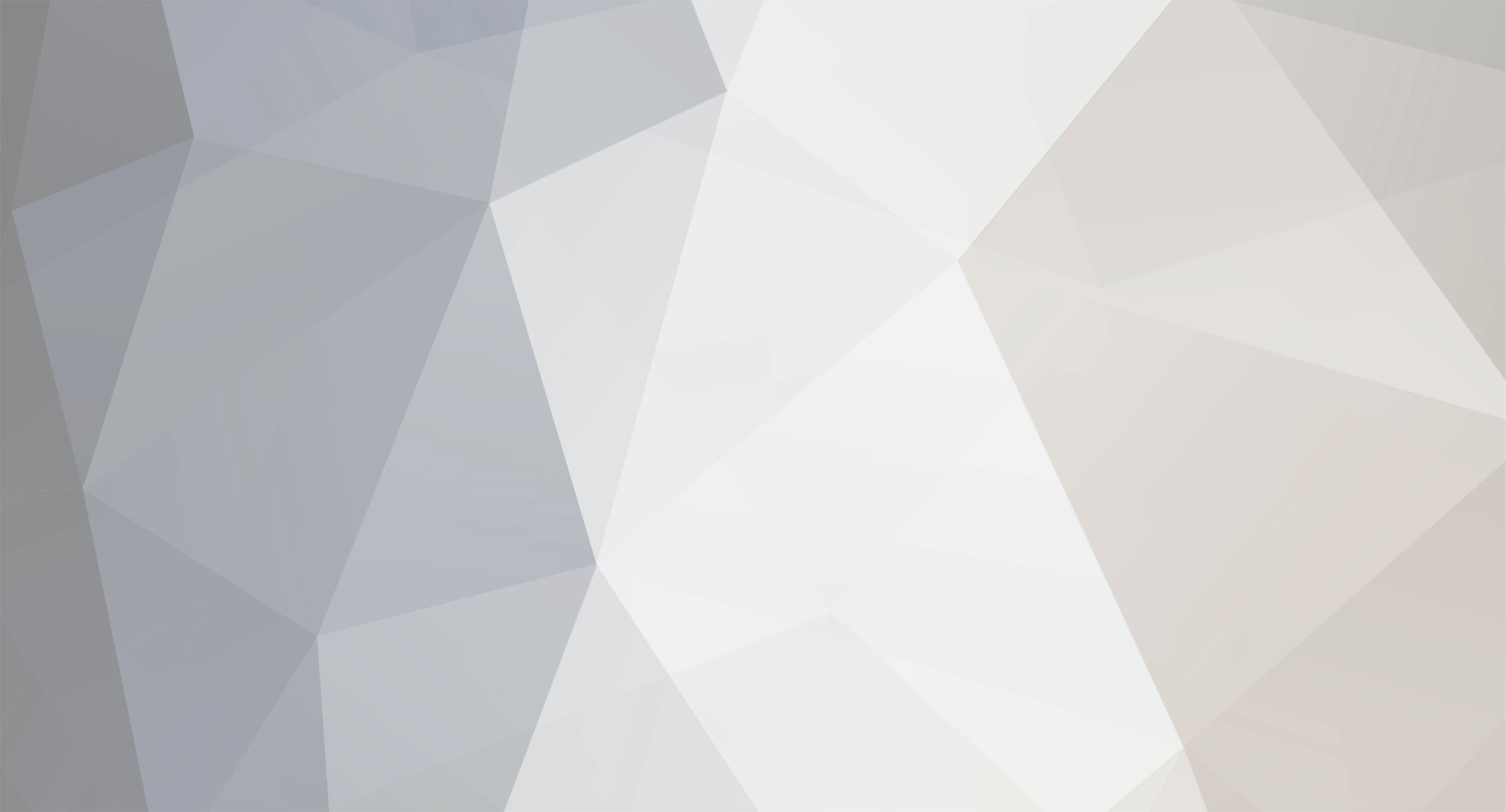
Gaf
Members-
Posts
225 -
Joined
-
Last visited
Everything posted by Gaf
-
Yeah I’m torn on this. Dropped in to four local timber suppliers and they all initially thought I was showing them photos of battens in a really old house. When I said it was a new build there was an unequivocal ‘get them ripped out and replaced’ and there should be no mould on newly installed interior timber.
-
So likely most houses have battens like that? And cause no issues from a mould growing perspective?
-
Attached photos of timber ceiling battens that were installed. Are the dark mould patches just something you have to live with when using timber or would this be too much? Plasterboard to be screwed to these, then skimmed.
-
And just to understand, even us getting cornices in that would hide any line where the old skim and new skim met, that wouldn’t make it any less of a can of worms? As in, the plasterer wouldn’t have to do as much to hide any line because the line would be behind the cornice?
-
The plasterer who has to do the work isn’t the one who caused the issue, but I do appreciate getting the question answered on which is the more difficult piece of work.
-
Mould infestation on the paper backing of all ceiling plasterboard. If we were getting cornices put in afterwards, be fair to say that any uneven feathering could be disguised as long as the area that is ‘cut’ is behind the cornice?
-
-
All our flat ceiling plasterboard that was skim finished has to be removed due to an error. Two options for removal have been offered (A vs B in attached photos). Person who made the error prefers A, which is cutting all boards up to 5cm from the wall, replacing cut out boards and skimming back up to the 5cm. They say it’s significantly easier to reskim this and significantly cheaper. Option B has been recommending by external crew who reviewed the issue. B involves cutting the boards on the walls approximately 10cm down from the ceiling, removing this 10cm section, and removing all ceiling boards. Person who made the error says this is prohibitively expensive and much more difficult for the skim plasterer to neaten up. Said can’t guarantee a neat flush finish on the wall with option B but can with skim flush with ceiling with option A. I haven’t included the error causing this as my main priority is identifying if there’s any real difference for a skim plasterer (forgive incorrect term) having to neaten / reskim A vs B.
-
Meant to mention as well, just only checked again, and the shade variation between the bottom half and top half that I thought was caused by lighting is actually due to different shades of wood being used. It looks to us like two very different types of wood were used and now that I see it, I can’t unsee it!
-
Would you say the packing to one side a bit of a lazy approach to the install instead of just getting it centred? Reckon that split in the string can even be improved? Appears some sort of filler was used on some parts and sanded down. Ours luckily is only above the utility room. But I had assumed that piece of wood in the middle was a temporary support, must check that with installer.
-
I can be picky so am curious if my pickiness is OTT on new solid oak stairs. Couple of things that I was going to raise: 1. String on the left is ~2cm thicker than the string on the right. 2. Where the treads meet the risers, there are gaps along the strings. Dust collectors? 3. The joint along the left string, where two strings join looks a little sloppy to me. 4. Similar sense of some joints looking a little sloppy, like the joint between the thin pieces 'covering' the top of the string (IMG_1205) I've no sense of whether the work underneath the stairs is good or not - will post those in next post as file size too large. This stairs crew came recommended by our builder.
-
I'm just a civilian but have done a build and run into trouble between the various professionals involved. I am currently going through some structural issues requiring remediation and, based on my experience, I would trust your SE above all others. I've had the 'ridiculous' comments and the 'overengineering' comments thrown at me when communicating the SE's evaluations - but everyone went quiet when the SE produced the data. Your SE will be the one who can provide the most robust rationale via calculations cross referenced to building regulations. Everyone else, in my experience, will provide unbelievably confident opinions but if things hit the fan, opinions will count for naught. Based on my conversations with an SE, base foundation depth of 600mm is a minimum best standard to ensure your deep enough for suitable soil stability and frost protection, so (although just a civilian) this doesn't look ridiculous.
-
Your buildup looks far better than ours and looks to have been well thought through to allow for the patio being at internal floor level. Your DPC looks nice a high on your walls. Attached is our internal floor build up. We have an underfloor DPM (acting as radon barrier also, Moarflex RMB 400) which is unbroken and running from external leaf to external leaf. As in the blue line in the image is the DPM and it is one whole fully connected piece.
-
Internal floors are all done and dusted at this stage unfortunately. Only when moving ahead with the patio did I come across the DPC requirement... would have thought the architects and/or builder, knowing we said we wanted this, would have flagged the need for the DPC to be higher.
-
@Andehh @bmj1 Just to check on the DPC. Are yours like the one on the right side of the attached image? So you DPC went up over two blocks high or was it two blocks above your internal floor level. So your DPC is one further block higher than the right hand side version on the attached? My buildup is on the left side. I'm assuming I'm screwed now and won't be able to have the patio up flush with the internal floor level. Edit: "Pation" should read as "Patio"
-
Please share, thank you. What was the makeup of your DPC? Cheers for the image. Those thin linear drains look the business. What is your DPC makeup? Is the patio level with the DPC (orange line in OP) or below DPC (pink line in OP)?
-
Plan from the beginning of build was for our patio to be installed at the same level as our internal floor area. The patio is accessed from our open plan area through a large sliding door (3.5m). Open plan is an L shape and the patio is in the ‘gap’ in the L (if that makes sense) as the plan was to create a sense of the open plan ‘continuing’ out onto the patio. This was communicated to both the architects doing our drawings and the builder prior to starting. The plans have an Aco channel drain specified where the patio and sliding door meet. As the build has progressed and I’ve learned more about regulations, and I’m wondering if the makeup of the wall and DPC will allow us to do as planned with the patio being at floor level. Attached image shows the makeup of the build at the external wall - it's 150mm cavity. The blue is the DPC – there is the DPC membrane running from high on the internal leaf down one block (215mm) to the external leaf, then an additional single piece of DPC running along the external leaf blockwork. We had hoped to have the patio height set at the orange line. Does this DPC makeup allow this, or will we have to keep the patio lower (150mm below DPC) so somewhere approx. at the pink line? The Paving Expert website only seems to include details where the DPC is just one horizontal piece on a single leaf, rather than double leaf house with the sloped DPC.
-
Induction Hob Extractor Hood Comparison: Faber vs Galvamet
Gaf replied to Gaf's topic in Kitchen & Household Appliances
Contacted one of the MVHR installers locally and he had an interesting take. Said a potential reason the cheaper Galvament unit might be causing the condensation issues is actually, paradoxically, because it's more powerful than the more expensive Faber unit. With airtightness levels in houses, he said a more powerful unit will suck out so much air that the MVHR can't compensate to get enough air into the house, so the fan in the extractor might just start spinning but not actually extracting, leaving the humidity in the air above the hob resulting in the condensation. He also wasn't a fan of the recirculating ones and advised venting externally to remove grease that isn't properly filtered out so that it's not getting up into the MVHR. Said just to crack a window whilst the extractor is on and that's sufficient. -
Induction Hob Extractor Hood Comparison: Faber vs Galvamet
Gaf replied to Gaf's topic in Kitchen & Household Appliances
Id be for this but herself wants the cooker hood as a feature in the kitchen. Getting it custom made and ordered already… 😬 -
Induction Hob Extractor Hood Comparison: Faber vs Galvamet
Gaf replied to Gaf's topic in Kitchen & Household Appliances
-
Induction Hob Extractor Hood Comparison: Faber vs Galvamet
Gaf replied to Gaf's topic in Kitchen & Household Appliances
Did not know that! Just searched here and online. If I've understood it, recirculating is for grease filtering while the MVHR generally takes care of the rest? Can I ask what make/model you have? And I can't seem to locate Miele discount outlet - is that in the UK? Meant to mention the extractor has to be a built-in / integrate one as we're getting a timber hood made for it. -
Will have an 80-90 cm, likely 5 zone, induction hob with hood extractor. Extraction will be to the outside via the wall the extractor is mounted on. We also have MVHR. Kitchen crew are recommending a specific induction extractor. The 'standard' extractor they do is a Galvamet, but they're recommending a Faber. I compared the specs against each other and almost across the board the 'standard' Galvamet wins out against the 'induction' Faber (attached image comparison of specs). I mentioned this to kitchen crew who said it's the Faber 'Steam Off System' that makes them still recommend the Faber. Said they switched to recommending the Faber because they were getting feedback from customers who had the Galvamet, but when these customers later upgraded to an induction hob, they were getting loads of condensation dripping off the Galvamet. Faber is 500 bucks more than the Galvamet. We're at the last stages of a new build, over budget, so don't want to be unnecessarily spending but also prefer to get this right if it needs it. The Faber has that steam system and is 10cm winder than the Galvamet, but the Galvamet has better fluid dynamics, stronger air flow, and is quieter. Any ideas why the Faber, with poorer specs, may be the better option?