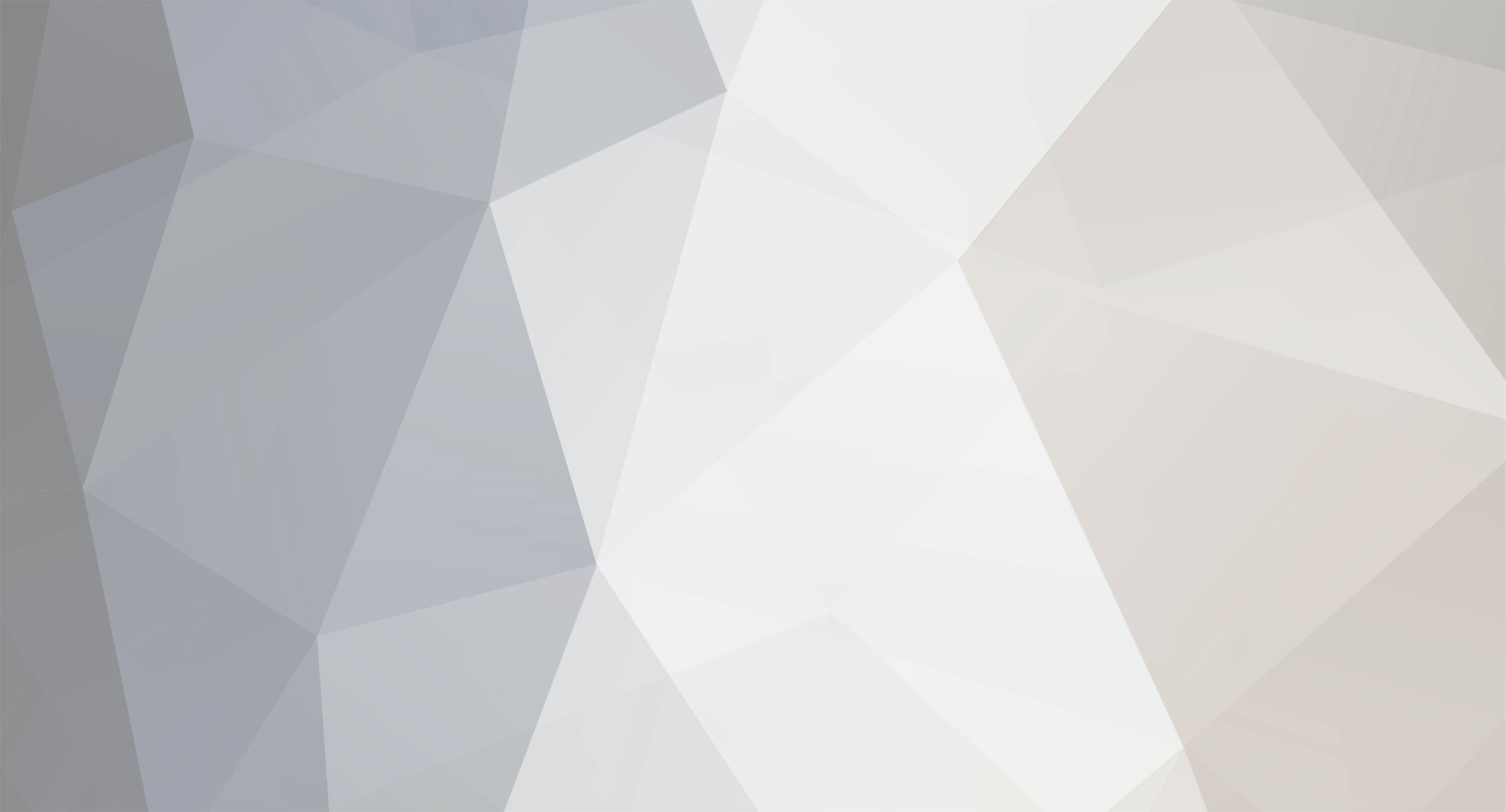
Gaf
Members-
Posts
221 -
Joined
-
Last visited
Personal Information
-
Location
Ireland
Recent Profile Visitors
The recent visitors block is disabled and is not being shown to other users.
Gaf's Achievements

Regular Member (4/5)
17
Reputation
-
And just to understand, even us getting cornices in that would hide any line where the old skim and new skim met, that wouldn’t make it any less of a can of worms? As in, the plasterer wouldn’t have to do as much to hide any line because the line would be behind the cornice?
-
The plasterer who has to do the work isn’t the one who caused the issue, but I do appreciate getting the question answered on which is the more difficult piece of work.
-
Mould infestation on the paper backing of all ceiling plasterboard. If we were getting cornices put in afterwards, be fair to say that any uneven feathering could be disguised as long as the area that is ‘cut’ is behind the cornice?
-
-
All our flat ceiling plasterboard that was skim finished has to be removed due to an error. Two options for removal have been offered (A vs B in attached photos). Person who made the error prefers A, which is cutting all boards up to 5cm from the wall, replacing cut out boards and skimming back up to the 5cm. They say it’s significantly easier to reskim this and significantly cheaper. Option B has been recommending by external crew who reviewed the issue. B involves cutting the boards on the walls approximately 10cm down from the ceiling, removing this 10cm section, and removing all ceiling boards. Person who made the error says this is prohibitively expensive and much more difficult for the skim plasterer to neaten up. Said can’t guarantee a neat flush finish on the wall with option B but can with skim flush with ceiling with option A. I haven’t included the error causing this as my main priority is identifying if there’s any real difference for a skim plasterer (forgive incorrect term) having to neaten / reskim A vs B.
-
Meant to mention as well, just only checked again, and the shade variation between the bottom half and top half that I thought was caused by lighting is actually due to different shades of wood being used. It looks to us like two very different types of wood were used and now that I see it, I can’t unsee it!
-
Would you say the packing to one side a bit of a lazy approach to the install instead of just getting it centred? Reckon that split in the string can even be improved? Appears some sort of filler was used on some parts and sanded down. Ours luckily is only above the utility room. But I had assumed that piece of wood in the middle was a temporary support, must check that with installer.
-
I can be picky so am curious if my pickiness is OTT on new solid oak stairs. Couple of things that I was going to raise: 1. String on the left is ~2cm thicker than the string on the right. 2. Where the treads meet the risers, there are gaps along the strings. Dust collectors? 3. The joint along the left string, where two strings join looks a little sloppy to me. 4. Similar sense of some joints looking a little sloppy, like the joint between the thin pieces 'covering' the top of the string (IMG_1205) I've no sense of whether the work underneath the stairs is good or not - will post those in next post as file size too large. This stairs crew came recommended by our builder.
-
I'm just a civilian but have done a build and run into trouble between the various professionals involved. I am currently going through some structural issues requiring remediation and, based on my experience, I would trust your SE above all others. I've had the 'ridiculous' comments and the 'overengineering' comments thrown at me when communicating the SE's evaluations - but everyone went quiet when the SE produced the data. Your SE will be the one who can provide the most robust rationale via calculations cross referenced to building regulations. Everyone else, in my experience, will provide unbelievably confident opinions but if things hit the fan, opinions will count for naught. Based on my conversations with an SE, base foundation depth of 600mm is a minimum best standard to ensure your deep enough for suitable soil stability and frost protection, so (although just a civilian) this doesn't look ridiculous.
-
Your buildup looks far better than ours and looks to have been well thought through to allow for the patio being at internal floor level. Your DPC looks nice a high on your walls. Attached is our internal floor build up. We have an underfloor DPM (acting as radon barrier also, Moarflex RMB 400) which is unbroken and running from external leaf to external leaf. As in the blue line in the image is the DPM and it is one whole fully connected piece.
-
Internal floors are all done and dusted at this stage unfortunately. Only when moving ahead with the patio did I come across the DPC requirement... would have thought the architects and/or builder, knowing we said we wanted this, would have flagged the need for the DPC to be higher.
-
@Andehh @bmj1 Just to check on the DPC. Are yours like the one on the right side of the attached image? So you DPC went up over two blocks high or was it two blocks above your internal floor level. So your DPC is one further block higher than the right hand side version on the attached? My buildup is on the left side. I'm assuming I'm screwed now and won't be able to have the patio up flush with the internal floor level. Edit: "Pation" should read as "Patio"
-
Please share, thank you. What was the makeup of your DPC? Cheers for the image. Those thin linear drains look the business. What is your DPC makeup? Is the patio level with the DPC (orange line in OP) or below DPC (pink line in OP)?