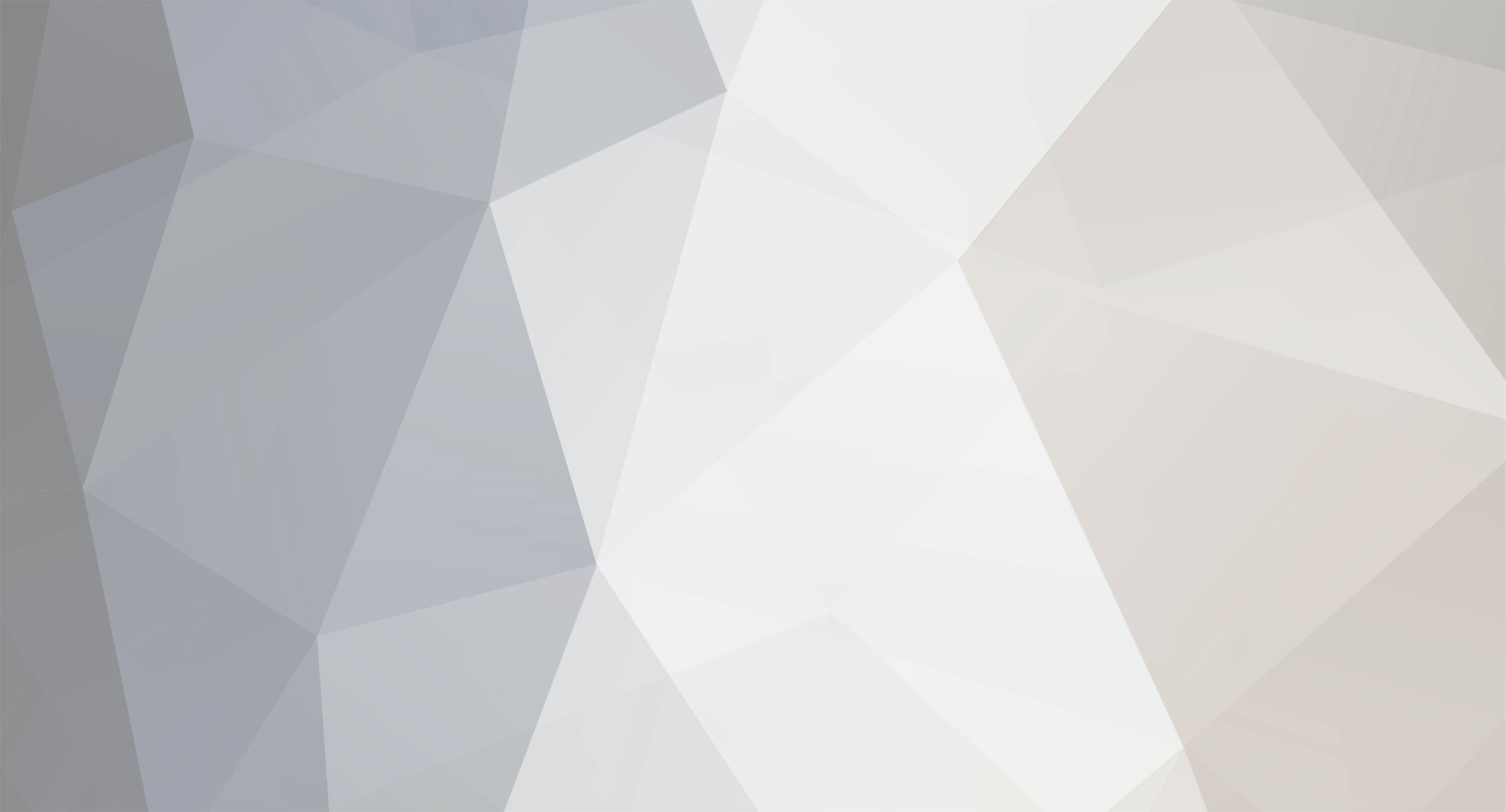
Jimbobjones
Members-
Posts
14 -
Joined
-
Last visited
Personal Information
-
Location
Gwynedd
Recent Profile Visitors
The recent visitors block is disabled and is not being shown to other users.
Jimbobjones's Achievements

Member (3/5)
5
Reputation
-
Looking for example projects and extensions built on rock
Jimbobjones replied to Jimbobjones's topic in Foundations
Thanks for the input Gus and agree with Dave that knock down rebuild is looking appealing RE:septic tank lots to think about and ultimately depends on convincing the seller the current site is unusable -
Extending house which is already too close to septic tank
Jimbobjones replied to Jimbobjones's topic in Waste & Sewerage
thank you I understand the interplay better now, I'll ask around the local area to see if anyone has encountered BC related problems relating to septic->PTP upgrades -
Looking for example projects and extensions built on rock
Jimbobjones replied to Jimbobjones's topic in Foundations
Or just use big boulders like this house I saw tonight -
Extending house which is already too close to septic tank
Jimbobjones replied to Jimbobjones's topic in Waste & Sewerage
if there is no suitable location for a PTP then does that mean no planning / no change to existing property will be allowed ? -
Looking for example projects and extensions built on rock
Jimbobjones replied to Jimbobjones's topic in Foundations
yes that's exactly what I thought assuming you mean 500mm not 500m it's a similar principle to the Japanese Hikari-tsuke where they profile the bottom of timber frame to match the contours of a rock which acts as a foundation pad for the house I've think I've seen similar commercial structures in Scottish trail centres / bird watching visitor centre type places, often out in the wild. Sometimes with eyelets which bolt onto structural members. Struggling to find contemporary domestic examples for reference -
Hello, Looking at a potential project which has an existing (old) septic tank of brick construction on edge of property boundary that drains into a stream. It is registered exempt / permitted. My plan for the project requires partial rebuilding and extending the property, which will require planning. The existing septic tank is located close to the house, less than the current required minimum distance. In this situation does anyone know what happens if I submit plans that would: Rebuild the existing walls (solid) for cavity - so no change in distance to septic tank. OR Extend (slightly) closer to the existing tank My assumption is planning would deny (2) but not sure about (1)
-
Looking for example projects and extensions built on rock
Jimbobjones replied to Jimbobjones's topic in Foundations
It's an outcrop of what looks like tuff, about 1m high at rear of house and gently ascending. The house is sitting on rock that has been cut away to make the site more level, I'm assuming it was originally a mostly natural site within the outcrop with some under soil rock, vernacular build ~150years ago I guess so any work was done with pickaxes (or rudimentary blasting?) Sounds like boring holes and glueing steel bar / rebar deep into the rock is DIY'able with some expert direction (i.e not requiring a piling rig) pending geo survey / engineer assessment. If the rock fractures and doesn't bear load then this wouldn't work, but in that scenario at least I'd have the option of breaking it out Any rough ideas about the concrete base once the anchoring steel has been signed off? I can't see how a volumetric and pump lorry would get to site, a landrover and trailer is just about doable so I might be limited to mixing it on site, if I did small areas of form work on the rock tied to the steel anchors and across with mesh that is doable. I'm assuming compression strength (making crush cubes and getting the signed off) isn't the limiting factor here as the loading small. The principle concern is keying to the rock and bonding sufficiently as there is no soil compression around it to keep the base secure? -
Looking for example projects and extensions built on rock
Jimbobjones replied to Jimbobjones's topic in Foundations
Found this mansard loft extension on stilts, similar principle but not exactly what I had in mind 🤣 -
Are these (leaking) Velux installed correctly?
Jimbobjones replied to sniederb's topic in Windows & Glazing
Next time it is leaking, as soon as the rain stops, open and inspect the edges of the window If the bottom frame is wet then the corresponding tracks of water should be present on the bottom edge of the window which would support the hypothesis the wind is blowing the water in However, if the sides of the window are wet and the water is running down the edge and collecting at the bottom then it is most likely the window cover parts (well it was on my velux which had the same damp spot under bad weather) -
Hello, I've got my eye on a very small scottish cottage which has been built on a plot cut into the rock (19th century). rear of the property is 3ft solid stone walls, rubble construction, ~3ft gap between rear of the property and rock terrace of ~3ft high. As expected the back of the property is perpetually damp and consequently so is the interior side of the wall. The property is sold as seen with no planning atm and I'd like to avoid going through the gamble of planning for a full demolition and the cost of excavating 100s of tons of rock which would ruin the charm of the site. Instead I'm thinking of extending upwards and to the rear so it is supported by the rock terrace (i.e avoid breaking it out as machinery is near impossible to access). I'm looking for inspiration from any projects with a similar constraints so I can see how it was overcome; pictures, videos, stories etc. Attached is a sketch of my current idea; concrete piers/plinths, supporting pillars (timber / steel / engineered wood), supporting a beam (RSJ / Timber / concrete) which would cantilever a first floor from the existing rear wall of the property. Failing that I would likely opt for the simpler option of a load bearing wall instead of a beam with pillars. In both instances I like the aesthetics of a house 'perched' over the rock. Obviously I'm not an engineer I'm just assuming this is doable in principle and it's just a question of sizing the components. Would appreciate any links or experience with this sort of constraint to build up my confidence that I have multiple workable options for making the property bigger before I buy and start work with engineer and architect and planning etc. Alternatively, any links to examples of foundations / builds on rock would be much appreciated so I can learn more about what other options there are (e.g steel frame)
-
Raise ground floor level in an old church
Jimbobjones replied to Jimbobjones's topic in Floor Structures
Thank you @Gus Potter for all the considerations (matches my list, hopefully the only changes I will have is moving sockets and redoing all the doorways...). Perimeter insulation did not make my list so thanks for pointing out, I thought this was just for screed. Thanks @saveasteading for the cheap fill tip, I've checked with the local quarry website and they seem to have 7x different fill mixes so I'm sure one of these is the budget special. I'm reluctant to add a lot of stone build up due to my access; I could potentially go with a bulk tip but no doubt this would cause tutting in the village especially if we get more rain like last week. Alternatively lots of bags is just not worth the cost IMHO, would rather just fill it up with more insulation. I'm going to get some proper room measurements and stop working on the back of an envelope, then reassess all options -
Raise ground floor level in an old church
Jimbobjones replied to Jimbobjones's topic in Floor Structures
We think late 90s based on what old planning docs I can find I haven't done a calc yet for every room, but did a fag packet estimate for the biggest room as things are now: 150W/sqm and I currently have oil fired condensing boiler. I could also drop ceiling and add wall insulation to bring the heat loss down but I still think the radiators would be needed - given all that and the cost of UF plumbing and screeding I just don't think its worth it. The pain of retrofitting -
Raise ground floor level in an old church
Jimbobjones replied to Jimbobjones's topic in Floor Structures
Unfortunately the property already has a concrete floor that must have been poured as infill when it was converted, and the block internal walls were built up from this base. Therefore I don't think breathable floors like glasscrete/limecrete would be of any added benefit as the damage has already been done. If the subfloor was rammed earth then I'd certainly be looking at this opption for the reasons you stated. I'm also going to avoid UFH as it wouldn't be able to heat the space sufficiently, I'd still need lots of radiators. I'm hoping a floating floor and carpets would be 'good enough' compared to the current toe freezing situation -
I live in a converted church and I'm planning to raise the ground floor level significantly as the windows are too high up. With a solid concrete floor, internal block walls, and 30" stone walls this is a great opportunity to add some insulation and make it less of an ice box. I want to add around 10-14" (TBC) over the whole ground floor living area 90sqm (hallway, 4 rooms, toilet, bathroom) I'm looking for some opinions on my proposed floor buildup: Level the existing concrete subfloor where needed (as level as I can make it) 1200 DPM lapped up to skirting height 100mm EPS100 (e.g Jabfloor100 £10 sqm) 100mm EPS100 100mm EPS100 (overlap all joints) Vapour barrier 22mm T&G P5 chipboard (glued joints, floating floor) Carpet in rooms / vinyl sheet roll in bathrooms Things I'm not sure about: Installing EPS: Foil tape all the joints? Does each layer freely float on the layer below? How should I cut the insulation around internal doorways; do I notch and run a continuous bond, or do I cut a break at the door threshold? Support areas: Where should I have a timber frame; Under the shower tray and toilet? Do I do anything different on corners to add strength? Services: Can I run anything in the insulation layer (between DPM<>vapour barrier)? Not water pipes or wires. Soil pipe? Shower waste? Building Control (Wales): When do I need to get them involved? Will gladly buy you a drink if you can help me out, Yaki da!