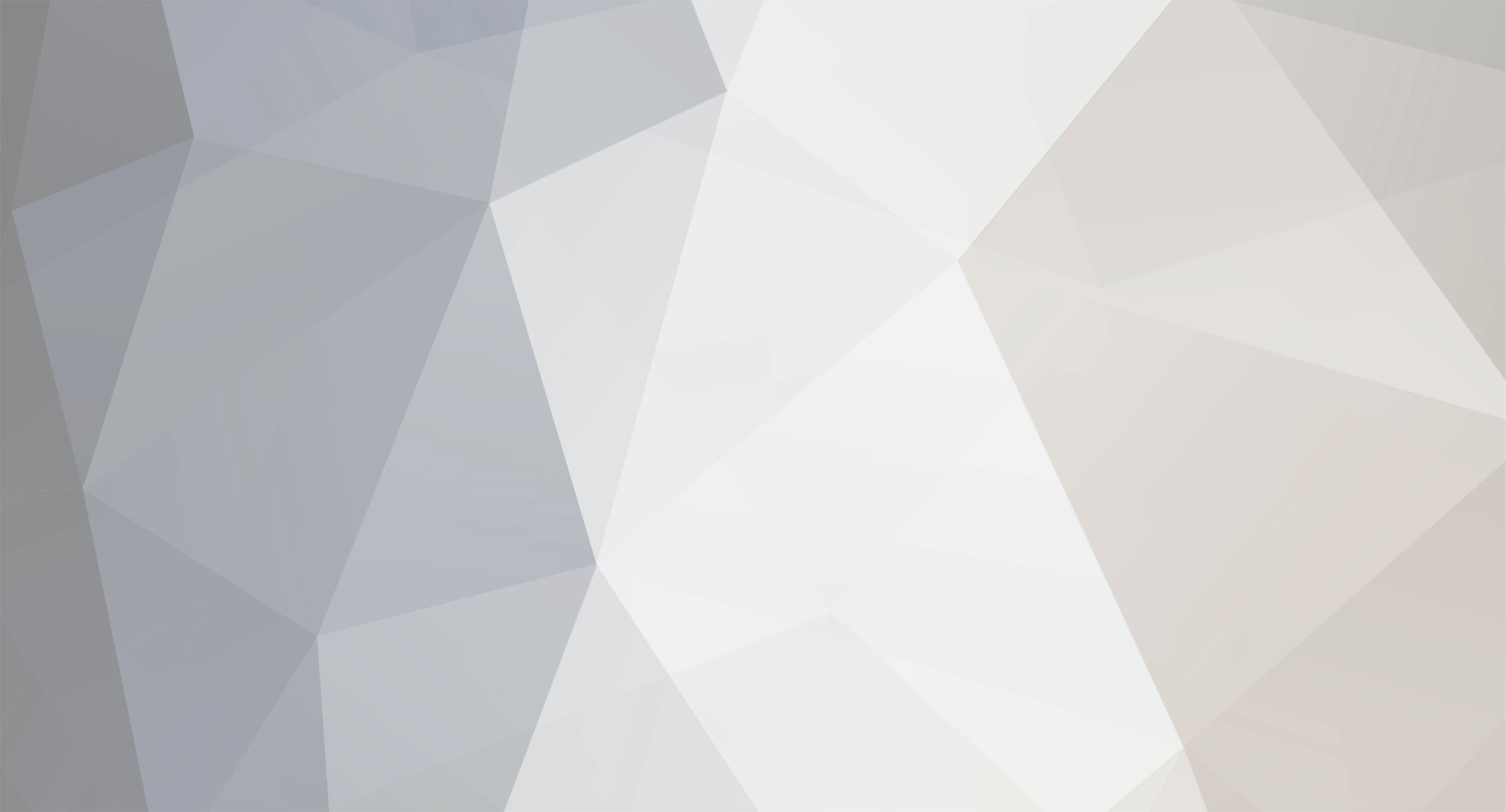
allthatpebbledash
Members-
Posts
27 -
Joined
-
Last visited
Everything posted by allthatpebbledash
-
Red/Brown/Buff bricks
allthatpebbledash replied to allthatpebbledash's topic in New House & Self Build Design
They do look nice. Still undecided on the brick yet. Thanks for sharing images though, does help if we go red brick or not. -
Presumably to @Iceverge much sought delight, I embark upon my next point of discussion here, should I go back to the idea of a full demolition and new build? To understand the context of the post, you can read this topic here. Okay so, I have a stripped out house that’s standing as a shell. Bricks, blocks and timbers with a roof on. Externally it’s covered with pebbledash which I want to get rid of. Insulation is poor in the cavity walls with none at all below ground floor. Being empty for 2 years means my VAT is going to be 5% for this, so a huge saving there. I am/was planning on retrofitting, so all new windows and doors, new ground and intermediate floor decks, removing the old roof and putting on a entire new roof structure, rewiring, new plumbing, improve insulation, essentially fitting it all out again. The retrofit plans require demolition of all the rear wall and adding a new single storey extension and then rebuild the first floor wall, and there’s also demolition of half of the front house wall and adding a new double storey extension here. This is now suggesting to me given everything else being taken out, I might as well do a full demolition and build a new house. Much better built, better insulated, more comfortable, better looking (externally), overall a slightly less of a headache. But, I have concerns over the cost. The existing house floor area approx is; 145sqm GF 135sqm FF 280sqm TOTAL I understand from reading various topics on the forum, and elsewhere, I can estimate a build cost of £2000sqm. With that in mind, I think a replacement 2 storey house is ideal. If possible, go into the loft for added floor space as I understand this won’t add much cost on to the build. If built back to the same floor area, I’m looking at a construction and fit out cost of approx £560,000. Can someone elaborate based on their experience and knowledge, firstly if I’ve reached a correct understanding of this, and if there’s ways to reduce costs? Like for instance I already have services connected to the plot as there’s an existing house there, can I knock £25,000 or more off that figure? The existing footprint is ideal for us, so drainage around the house can be reused in some or most parts? How much would that knock off? And the BIG question here, given the existing footprint is ideal, can I reuse the existing foundations? How much would this knock off that figure? Obviously the challenge here would be for the architect to creatively fill the floor space within this. If I also then went for a fuss-less finish, how much less can that per sqm estimate figure come down to, £1500sqm? Or even less, £1000sqm? Let me hear your thoughts, advice, suggestions, experiences, all of it.
-
Red/Brown/Buff bricks
allthatpebbledash replied to allthatpebbledash's topic in New House & Self Build Design
What brick was that, and any chance of a closer image of the wall in the middle? Also, the second image is great. Looking to have rough render off white and red brick too. So Weinerbeger manufacture it? Interesting, I wonder what it goes as under their brand. Look forward to seeing the full wall photos. £993/thousand seems in ball park of others I’ve had priced from them, few others have come in £1280 plus. Anything less than a quid a brick is budget I’ve set myself. Will look into this one on the website you’ve given. Nice brick, even better price! How did you manage such a bargain? Prefer a full red or full buff though. Interesting, these guys are next on my list to enquire. Would you happen to know if they have offerings for about £1 a brick or less? -
Long shot but there’s bound to be someone who’s built a wall of sorts on here with either of the above colours in brick? I’m thinking a red brick would be easier to swallow for the planner due to site appraisals, but brown and buff could be thrown down too. Would people be kind enough to post an image or two of their walls and what brick they used? I find the online edited/filtered images used to sell them aren’t a true reflection, neither are sample boards showing 4.5 bricks laid with no mortar. Currently I’m looking at these options from Wienerberger. Reds Autumn russet sovereign stock Oast russet sovereign stock Mellowed red sovereign stock Marpessa multi Jasmine blend Woodbridge claret stock Warnham red stock Waresley red stock Olde southwater Blue velvet Browns Pagus brown/black Buffs Anglesey weathered buff Weathered gault blend St Ives creams rustica PT450 iron Oakington buff Marziale As you can tell, need to narrow things down a bit, before looking at other manufacturers. Looking for a nice stock, waterstruck, or handmade brick. Something you won’t see on a Barret house.
-
How the brick market works and getting good pricing
allthatpebbledash replied to ed g's topic in Building Materials
Okay thanks, I’ll look in to last 3. Wasn’t aware they did them also. -
How the brick market works and getting good pricing
allthatpebbledash replied to ed g's topic in Building Materials
I learnt this too when considering a new build, circa 26,000 bricks needed. I was lucky however as the first BM I had asked to get an estimate didn’t inform me of the “address lock” method. I thought the quote given was reasonable. But, as I have a friend, architect, who works for a major national practice and relationships in the construction industry due to position in the company, they introduced me to a major supplier of materials for multimillion pound projects. Said supplier has a fantastic relationship with said manufacturer of the brick. After an informal discussion with senior person in the brick manufacturers organisation, email sent to appropriate person stating certain facts, I was successfully able to have the “lock removed” from BM and now locked to above major supplier instead. As a result, the new estimate provided by the major supplier was surprisingly 20% less! TLDR; find the brick you want. Enquire with the manufacturer who they do preferred business and large off takes with, then approach that BM/supplier to source the bricks and lock the address. I find that is how to unlock huge savings, should the manufacturer not be willing to deal and supply direct. Now on to the brick discussion. I’m also considering linear bricks. Not as many as project has changed from demo and rebuild to retrofit with extension. Would you be willing to share data on prices you’ve been getting? The Kolumba bricks are priced out for me. Been given a flat rate of £250 sqm supply. I’m looking for alternatives. The standard 215x65mm brick in red and buff tones I’m seeing average £40-60 sqm. Grey/white/black I’m getting £55-80 sqm. Seeing as you’ve looked at alternatives already in terms of linear bricks, have you had estimates or any figures back? -
Most probably what I’ll do. Can you show and explain more of the image? Was this something you’re doing or have completed? Thanks. LOL Come on, I can’t knock it down. It’s gonna be a headache I can imagine, but it’s too much money to bulldoze now. Especially if the VAT is 5% for me too.
-
Coming around to the idea I will be adding EWI to the existing structure and rendering over. I have 2 existing external wall build ups, so want to understand if one solution would work all around. Both walls have engineered brick exposed above ground level, 3 courses to one side and 7 or so at the other as the site slopes. 1960s brick cavity house, with few blockwork additions as it’s had few extensions previously. Property is detached with 5m minimum to boundaries on all sides. New roof going on so eaves can be detailed as required. As well as new doors/windows/ground floor/intermediate floors. It’s a deep retrofit, house is a shell right now, back to brick etc. Wall 1. 100mm brick 70mm cavity (filled with blown wool) 100mm brick 10mm pebbledash Wall 2. 100mm blockwork 70mm cavity (has 50mm PIR in) 100mm blockwork 10mm pebbledash I’m tempted to remove the pebbledash first as I can’t see how fixing the EWI boards to it won’t leave gaps in between? Anyways. Would I better using 100mm of mineral wool slabs instead of EPS for this? Or won’t it make a difference? I’d like a well insulated and air tight house, and been thinking what if I doubled the thickness to 200mm? I read somewhere but couldn’t fully understand I need to be careful with the dew point and condensation risk. Although I am looking to spec an MVHR system too as part of the works. Would this mitigate said risk? Finally, doing EWI would allow me to hide the orange engineering bricks externally too as I understand I should take 50mm PIR into the ground. Or is this not really necessary? Would like to hear some thoughts on this.
-
Rebuilding outer leaf
allthatpebbledash replied to allthatpebbledash's topic in Costing & Estimating
I agree, seemingly option 3 is most likely candidate. Existing original foundations in areas are under bearing. Engineer thinks it’s okay as settlement and all that, and I’m very close to sandstone too. But potentially can be corrected with localised underpinning if needs be. Don’t need to do the whole footprint. I’d be very interested in hearing the figures and sums that led you to determine this route. Wow. The cavity is filled so I understand EWI would be okay to use. Cavity is filled. But could top it up. And close up. I seem to be changing course more frequently than a ship without a rudder. As per my partner anyway. Thanks lad. So. Don’t think I will rebuild the outer leaf. Don’t think I will erect a third skin of brick creating 2 cavity’s. I really don’t want to knock down and rebuild. Thinking the most likely course of action is to either; Strip off pebbledash, affix EWI, render over. OR Affix EWI straight to pebbledash, render over. Whilst render is something I don’t particularly want as a finish, suppose I’ll have to get a craftsman on it to give it a half decent chance in looking good. -
Rebuilding outer leaf
allthatpebbledash replied to allthatpebbledash's topic in Costing & Estimating
DELETED. -
Rebuilding outer leaf
allthatpebbledash replied to allthatpebbledash's topic in Costing & Estimating
Yeah lots, anything specific you want to see or just elevations? What’s the sunk cost fallacy? What about building a third leaf creating 2 wall cavity’s that are filled? Basement was an option early on, but we decided against it. As for the new build planning, I already floated one application of a new build through the council. They wanted a CMRA which is fine, but then comments from biodiversity department were suggesting they request a bat survey prior to even any consideration of looking at the application. According to a neighbour friend of mine, it can take months to have one completed, theirs had taken 30 weeks! I think it actually always is about the pounds and pennies. The carbon implication conversation is just a calling card at election campaigns. If not, the government would be incentivising retrofit applications as opposed to nil rating the demos and rebuilds only. Given the majority of the populous I believe only extend and renovate and pay full VAT for doing so means more cash in the kitty. True. Okay so yesterday I happened across an old episode of grand designs. Maybe taking down the external leaf and rebuilding it is a terrible idea, but building a third leaf is a better one? Already spoken to the engineer who’s done this and the house in question is a beautiful award winning house. Here’s the idea. Increase width of foundations. As we need some underpinning in areas as it is, this can be done as part of the works. Then, build a third leaf of facing brick, insulation in the now 2nd wall cavity, which gives a more better insulated and air tight external wall. What is the opinion on this? -
Rebuilding outer leaf
allthatpebbledash replied to allthatpebbledash's topic in Costing & Estimating
Interesting. That’s 2 I’ve read about now saying it can be done. For it being empty, I bought it as long term family home. Never moved in as we planned a remodel. But then remodel came in pricey with not much space gained so I went in with an application for a full demo and rebuild, but larger footprint. The planners were having none of it. I either rebuild to same footprint more or less, or refurb it. So now I’m back at refurb. But this time plans are to retain almost all the walls, and extend at the rear. Time since purchased to now is just over 2 years now. The property is in good condition, it got stripped out after application 1 got approved and the structural engineer wanted to understand make up of existing walls. This is why it’s sat as a shell now, everything needs putting back in. The future value in this is irrelevant to the discussion. I don’t plan on selling. I was thinking the leaf would sit at same width so footings remind same, and you’d use batts that are 75mm to fit existing cavity? This is where I got stuck. I previously did look at demo and new build, but the planners wanted it to be same footprint near enough. I couldn’t overcome the cost of demo, new footings, only for house to be of same size? That’s not including the fact if I go back in now to say we will demo and rebuild as planned for the refurb, the application would take another 12 months? New roof going on. Can be put on same footings so no increase in cavity? If few sections at a time are put on support, built up, and move along to next, surely it’s possible? All new windows and doors, lintels, and ground plus intermediate floor. Does this change things? Great advice once again lad. Here’s how I’m looking at it. Currently it’s sat as a shell. Everything needs putting back in. Planning approval for refurb only. Tax at 5% or nil rated for some items. New build application would take another 12 months or so, I presume. Cost of demo/excavations and new foundations I estimate will be high in current climate. Existing masonry shell probably has a built value of £100k at least. To demo (circa £20k), new foundations (circa 40k, based on nearby friends build). I’m effectively looking at £200k cost to get back to where it stands now? Or have I missed something? -
Rebuilding outer leaf
allthatpebbledash replied to allthatpebbledash's topic in Costing & Estimating
How will it cost more? As for performance, that’s subjective based on initial goal of what I’m looking to achieve. I don’t want a passivhouse, enerphit maybe. But still, why demolish a building that has no real structural fault? Yeah I appreciate that. Should’ve mentioned this was material prices. Labour can be found at whatever rate someone is willing to do it for and you’re prepared to pay. But materials more or less have a trend line so can at the very minimum count on that for estimation purposes. Yeah, should’ve mentioned I’m looking at materials prices at moment. Hard for a contractor to gauge labour charge. More if stand alone job, but could be less if done as whole package. Hahahaha. My 2 year old would love option 6 for definite. But that would surely cost more? New foundations, cost of demo and clearance? New planning and extra delays? Being that I’ll be paying 5% VAT regardless for everything and 0% VAT for some of the stuff, hardly see the point in knocking it all down to save 5% more? Property has been vacant for 2 years so I get the VAT on the whole refurbishment. Oh yeah, a proud moment this lol. Tell me then, what was the now 2nd worst idea I just topped? Always wanted to be best in class. Thanks. As property is empty for 2 years, my entire refurbishment will come in at 5% VAT cost, some items are of course nil rated. Hardly makes sense to knock it down to save further 5% on the tax considering cost of JCB and new foundations. My only issue is the pebbledash, maybe I should just own it? Paint it white, dash showing and all? See my comment above to this, the VAT saving is minor, so definitely can’t be cheaper than working with it. Nah absolutely not, I enjoyed the laugh. I recall your previous comments to things I’ve asked regarding retrofitting, I find your input seriously valuable. All the things you’ve mentioned are exactly on the table right now being talked about. This is where the idea of the topic came from lol. Rather than sucking it out, refilling etc. given I want to freshen the facade, taking the outer skin off, use batts, and re skin would be easier and probably more cost effective? This was the point of the discussion. I think the cost of sucking out the mineral wool, blowing in new graphite EPS beads, hacking off the pebbledash, re point where necessary, then render again is looking to be more costly than carefully sections at a time, remove outer skin, fix batts for insulation, rebuild with fresh brick. I’ve come across this idea on another forum (PistonHeads) where someone has done exactly this to an old police station. Can post a link if anyone is interested? Their builder did a half wall at a time, the end result is fantastic. Like me, they dislike render too. Anyways, I’m seriously considering this. If anyone is interested, can I post an Instagram handle here for people to follow along? -
In planning stages of a deep retrofit. House is detached, and neighbouring houses are brick, various shades of red and brown. Some have been rendered to the sides over years. My house is the same I suspect. Make up of the existing walls is ‘50-60s brick cavity walls with some mineral wool blown in place, and other half (previously built extensions) is dual skin blockwork with 50mm PIR in the cavity. Approx cavity in all the walls is 75mm. All the walls are covered in pebbledash! As part of deep retrofit, I will be having all new ground floor structure and intermediate floor, a full new roof, all new windows and doors, and rebuilding the rear wall of the house due to structural complications and building a modern rear extension. That’s just to give idea of what project entails. Question is, how should I freshen up the rest of the house? Option 1. Remove pebbledash, inspect underlying brickwork/blockwork and make good, render over. Option 2. Remove pebbledash, inspect underlying brickwork/blockwork and make good, leave original brick as finish. Where there is blockwork, render over. Option 3. Leave pebbledash in situ, inspect to make sure no cracks etc, fix EWI straight on top and render over. Option 4. Take down external leaf, replace insulation with full fill cavity batts, probably wool, inspect wall ties etc, rebuild with nice red brick as finish. (Being red bricks are cheapest around, but it’ll allow the house to blend right in the street scene too.) Option 5. Take down external leaf, replace insulation with full fill cavity batts, probably wool, inspect wall ties etc, rebuild external using blockwork and render over. I have some understanding of the costings involved based on initial conversations with a few trades. Based on 200 sqm of external wall. Remove pebbledash £20 sqm Render £60-140 sqm (pending type) Blockwork £25 sqm Bricks £30-£60 sqm (pending type) EWI £40+ sqm (min 50mm) Wool batts £18 sqm (min 75mm) I feel option 4 would be the best overall. But. Would love to hear some thoughts and ideas if there are other ways? Or if someone else has done something similar, how did it go? Lessons learned? Thanks.
-
BUS voucher and gas line
allthatpebbledash replied to allthatpebbledash's topic in Air Source Heat Pumps (ASHP)
Yeah this is the chosen route now. The 5% VAT for the renovation makes it nice. It’s all up for discussion but currently we’re looking at a slab, unsure about thickness of insulation. Or even type to be honest. Once we have a first draft of technical drawings done, I intend to post and gain advice on certain aspects on the forum. At the moment we’re early stages. -
BUS voucher and gas line
allthatpebbledash replied to allthatpebbledash's topic in Air Source Heat Pumps (ASHP)
Thanks. It didn’t occur to me when I had heard the statement off our architect to go looking at the government websites. So during the same meeting I started searching the forum, and thought can’t see nothing, lemme post a quick question. There’s a wealth of knowledge on here and someone’s bound to know and will reply far quicker than I would be able to find it trawling through legislation. Been a good response too, can’t wait to begin our retrofit and grab more insight into various other aspects of the build from others on here. -
BUS voucher and gas line
allthatpebbledash replied to allthatpebbledash's topic in Air Source Heat Pumps (ASHP)
Because we have the option to I suppose. The house is currently a shell, masonry and timbers, it needs all the services (everything really) putting back in. Was close to being a demolition and rebuild job but we’ve “saved the environment a little” and working with it now. So, all the floors are being replaced, new insulation into the void below ground with a ground bearing slab at the minute unless engineer changes his mind, and a new roof structure entirely that will be well insulated, and triple glazed windows. The current cavity filled mineral insulation will be assessed and if deemed cost effective we may hoover it out entirely and refill with graphite EPS beads. Currently it’s still in place and looks to be in good condition. We’ve ruled out EWI for various reasons at the moment. Along with this, there will be a MVHR system, PV with battery storage, and UFH across all floors. We’ll be upgrading to 3 phase also. The PV array as of now has a working projection of 15kW if both the south facing roofs are used. If just the one, it’ll be an array of 10-11kW. So we’re definitely investing into the building. But we love to cook with gas. Woks and Karahi require it for the true chefs and authentic recipes. Not to mention to make a good chai. As it stands, there is no gas boiler on site either. So it would be a new more efficient one if we opted for this route and get a water cylinder or two which we can dump the PV generation into or dumped from the battery if stored from the day before. As the property has been vacant 2 plus years, we’ll be paying either 0% or 5% VAT for nearly the entire retrofit so rebuild makes little sense. See above. As for occupancy, 2 adults and 3 kids under 10. We plan on staying a while so it’s not a ROI type of thought process, more a case of how can we make this the best we can now (budget in mind) and make it more comfortable and financially sustainable for the future. Low energy bills at the outset is the idea. Thanks 😂, and thanks to everyone else also for answering the initial question. Definitely sounds like mambo number 5 that, but them authentic Indian pans won’t work on one. So sadly can’t do nowt and cough up moolah. -
Had no success in searching for the answer on here so wondering if someone can shed light on this. Currently planning a deep retrofit. We are looking to replace the gas boiler with an ASHP for hot water and heating. And we want to keep the gas line to the property for the kitchen hob. Would the BUS grant still be available to us? I’ve been advised to double check this as been told the gas line has to go completely and we would need to go with an induction hob instead.
-
The architect has been working on PHPP modelling and data suggests extracting of blown wool CWI and refill with EPS bead would give us the target value needed. But with adding EWI we can get that number lower of course. Given the added benefit of nicer exterior finish, and better cold bridging across the envelope, is why I’m debating the extra cost. Can you share a rough section detail of your floor to wall junction/build up?
-
Hello. Done lots of reading till now but not quite come across an answer regarding my own specific situation. I am planning a detached house retrofit. Part of works will include taking the whole roof off and placing a brand new one on (we’re restructuring basically). Also, suspended timber ground floor is going and we are filling with insulation and a slab most likely. Crawl space is 400mm leading to 800mm as ground slopes. There will be all new windows and doors and MVHR. But I’m struggling with understanding the walls. Currently external walls are covered in pebbledash. Ideally we want to remove or cover this. Wall build up is brick cavity brick, 70mm cavity and (fully) filled with blown wool many years ago. As the house is stripped out, can confirm it is still in place on 1st storey and not slumped. A part of the house (previous extensions) has 50 PIR in the cavity. I was thinking to avoid IWI to not reduce footprint inside, so my options were CWI only or CWI and EWI. But concerns about condensation and air tightness. Option 1. Extract current CWI wool, refill with EPS bead. Wet plaster internally for air tightness. CorkSol or render over pebbledash externally. Option 2. Leave wool CWI in place, 80-100mm EWI with weather tight render which will become new air tight layer. New roof and ground insulation will meet EWI to create envelope. EWI will go straight over pebbledash too. Cost wise, whilst CWI is cheaper than EWI, the additional labour of extracting the wool CWI, and re rendering over the pebbledash, and wet plaster internally makes option 1 more or less same as option 2. Hence why I’m looking at this route. I am concerned about condensation and convection within the cavity. Or can this be mitigated by other means? EWI runs down below ground closing off air bricks? Or new ground insulation/slab can close it? Or cap cavity at bottom and top? Looking for advice and input from anyone who’s done something similar or can advise on the merits of the above really.
-
Hello everyone. In the process of our now third round of planning and we’re looking at aluclud windows. Idea is to have the internal frames clear lacquered to see the timber. I’ve seen GBS windows up close and the timber is jointed in many places. Rationel also appears to be the same as above. Many joints. Internorm doesn’t have joints as such but you can see where the pieces of timbers have been pressed together. Has more of a linear structure. We don’t mind this look. I was hoping if anyone has images of the other suppliers? Nordan Norrsken Allen brothers Idealcombi Velfac (same as Rationel?) There’s probably more but these are companies I know of so far. I’m trying to save trips to go see all of them in person by ruling out ones that are jointed everywhere. Thanks.
-
That sounds like an opportunity to go snap up some bricks en masse. Who’s this manufacturer please?
-
Having found out the supply of bricks is a little nuanced, I’m wondering if there’s manufacturers out there who’ll sell directly to self builders. We have a decent sized plot and could possibly off take a load at a time, maybe even a wagon load. I’ve searched the forum and come across York Handmade, but wondering if there’s others? We’re based in West Yorkshire.