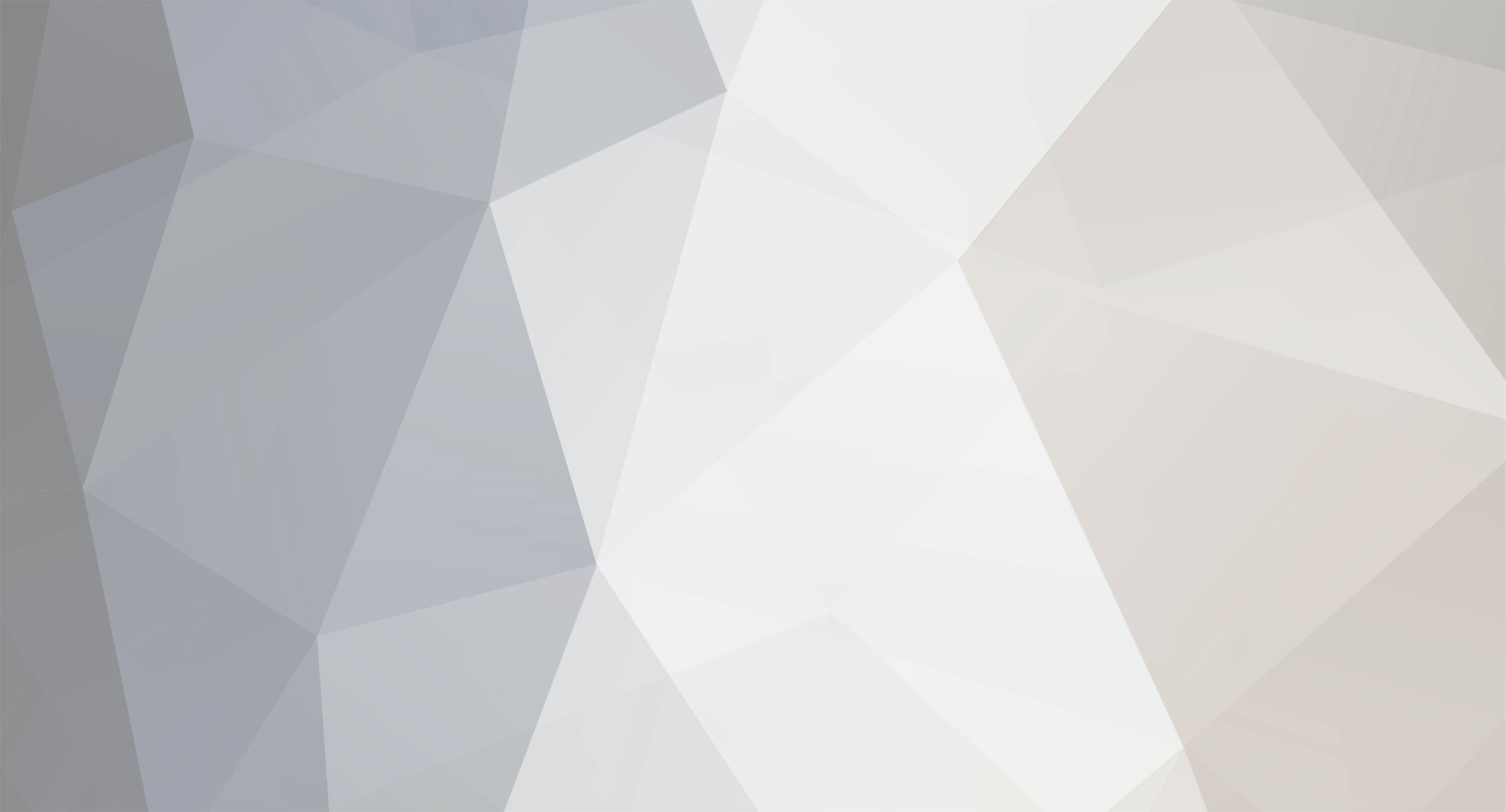
DanRobertsB
Members-
Posts
14 -
Joined
-
Last visited
Recent Profile Visitors
The recent visitors block is disabled and is not being shown to other users.
DanRobertsB's Achievements

Member (3/5)
0
Reputation
-
I've nothing against Decra in itself - and it seems this roof structure was designed with Decra specifically in mind (or something else similarly lightweight; I don't think it can take much more weight). It's more that this Decra is in very poor condition. The other issues are that access is needed to clear leaves and for maintenance, and it doesn't seem to stand up well to that; and that very few people have any experience in dealing with it. Assuming it needs replacing (which everyone who's inspected it in person or seen photos and has offered and opinion says so), the options seems to be more Decra again (noting reservations above), or another very lightweight roofing system (?). Perhaps metal sheets / corrugated metal? Without reinforcing the roof structure, and perhaps the timber frame building beneath it too (expensive, disruptive, perhaps not economically viable), OSB and EDPM would just bow given the width of the rafters (1200mm).
-
Hi I'm wondering whether it's worth* insulating and re-roofing this ground floor flat roof over a bedroom and en-suite, possibly adding a glass balustrade (it could be access via a ladder, which could be permanently attached to the side). It was leaking a little, and some of the board were spongy (hopefully now dried out), but that's been addressed with a flash band repair. Making a green roof would be great, but I doubt it could take the weight. Any advice greatly appreciated - anything from what material would be good (bitumen felt, EDPM, single ply uPVC, etc), to who you'd recommend, sequencing (e.g. if considering wall insulation), general tips, whether the "ladder and ballustrade" or green roof idea is nuts, etc. * Money no object (alas, it is), I'd just get it done. However, I'm reluctant to spend money unnecessarily, or would prefer to defer it (e.g. we might add external wall insulation in years to come - which, I assume, would be best done before re-roofing). If the current roof really is 0.20 u value, there's less need to insulate it further; the timber frame wall of the bedroom below (seemingly just studwork, plasterboard and timber cladding) is I suspect quite a big limiting factor when it comes to heat retention. Details: I have a a c 5.6m x 3.8m (+/- c.10cm) ground floor flat roof, on top of bedroom and en suite bathroom. This was an infill extension, built c. 2006 or 2007. Eaves are vented. There has been water ingress (through capillary action) where a seal is poor/has failed (poor original installation, as far as I can tell - the overlapping felt has not been properly sealed; I suspect it was installed by a builder rather than a roofer). I have applied flashband as a temporary fix. However, before the fix at least, the boards (I suspect OSB) under that section (c. 1.5 x 2.5m) were a bit spongey. They may (hopefully!) dry out if the roof is sealed and watertight (as it hopefully now is), but it may be that parts of the OSB need replacing. Despite the Building Control insulation specs applicable at the time (u value requirement for building control in 2007 was 0.20; I think it was probably that from 2002 onwards), I suspect the insulation is poor. It may be a cold roof - there are soffit vents. There may be sense in overcladding the whole lot with a VCL and 150mm PIR (I can source at reasonably prices if needed) to create a new (warm) roof on top. I’m not sure what, if anything, needs to be done about the existing roof/ventilation. The gutters could probably benefit from simplification/re-arrangement - many of them appear to be legacy gutters from before this bedroom infill extension with the flat roof was built. It’s possible we might want to install a glass balustrade across most of the open side. Depending on cost, we might also be open to a green roof, though I don’t know if the structure will take the weight.
-
Hi I suspect this roof needs insulating and re-roofing, given condensation issues. We may replace the skylights at the same time. Any advice greatly appreciated - anything from what material would be good (bitumen felt, EDPM, single ply uPVC, etc), to who you'd recommend, general tips, etc. Details: Trapezoid ground flat roof over two bathrooms, c. 9.1m x 2m (at the wide end) and 1m (at the narrow end), adjoining a masonry parapet wall and a cold roof (just a timber wall). Construction date unknown, probably 1982-4, but possibly as late as 2000. It appears to be unvented (unless they’re behind the fascia?). Roof appears to be solid underfoot, but condensation/mould issues suggests it needs attention. Both bathrooms ceilings were showing signs of peeling/mould/condensation etc around the skylights (see here). In Aug 2022, the upstands/skylights were re-flashbanded and both bathrooms ceilings decorated. Both have deteriorated a far bit since, but it’s much worse in the smaller bathroom, with clear evidence of water issues (seemingly condensation; rust on metal angle edges, etc)). This is despite very limited use (shower not used; bath used max once a week) in that smaller bathroom, so presumably interstitial condensation and/or roof leak, rather than humidity. It’s a bit odd that it’s only affecting one of the two bathrooms (the one used least) when it’s the same roof. In both rooms, on the opposite (far) side of the room to the shower (so a far way away), there’s a humidstat extractor fan and a window with a trickle vent. It may be advisable to install a further humidistat extractor fan directly over the showers and vent them directly out the roof with a (mushroom cowling). I have suitable fans to install (and can get them installed, though imagine you’d need to do at least the finishing etc on the roof side. I’m guessing it’d be best to: add a VCL and 150mm PIR, and refinish on top; probably put in new skylights; improve detailing etc where it joins the walls. There are three existing polycarbonate skylights (400x400mm externally, 600x600mm internally), with upstands. If insulating and re-roofing, can these be sensibly be re-used? I suspect there’s sense in switching them out for new 600x600 double- or possibly triple-glazed flat roof units e.g. Velux CFU 060060 0020Q, with Velux curved glass top unit ISU 060060 1093 and extension kerbs (unless cheaper/better to build these e.g. from OSB) ZCU 060060 0015. It might be that one or two of these should be electronically humidity controlled with rain sensors (e.g. Velux CVU 060060 0220Q, with humidity control unit). Open to alternative product suggestions, etc. Depending on cost and if it can take the weight, we might also be open to a green roof.
-
Hi I'm after some advice on replacing or repairing a Decra roof on a bungalow in south London. Thoughts welcome, including recommendations for who would be well placed to do the work. If replacing it with anything heavier, I expect a structural engineer will be needed to confirm whether the structure (see final paragraph) can take it. I'm doubtful it'll take much weight, at least not without reinforcements. And some of the building - the two longest sections - are only relatively lightweight timber clad timber frame (basically studwork finished with plasterboard on the inside, and timber cladding outside), though bookend on the short ends with masonry walls. As for replacement, I guess (structure willing), it could be anything from decra, metal sheet, EDPM, etc. One option would be to make it a warm roof, but I'm a bit sceptical - about 1/3 of the loft joists under the decra cold roof is well insulated at ceiling level (300mm of mineral wool), but for the rest, the vertical walls loft (and probably the whole wall down to the ground) would need insulating, there'd be increased heating costs of having to heat a large roof space (possibly justifying MHRV, etc). I'm also weary of spray foam insulation - I gather can be an issue for insurers and/or mortgage providers. But if that's ill founded prejudice, do correct me. Details below: We have a large (c. 280m2) series of sloping cold roofs. These are low angle/gently sloped - I think most/all under around 15 degrees. These have Decra Classic (thin metal composite sheet “tiles”) which may benefit from some repairs (including re-sealing of a large c1.6 x 5.8m angled skylight) and need better insulation. Parts of the Decra are in poor condition - cracked / banana’ing / patch repaired. However, we’re not aware of any obvious damp / water ingress over the past 18 months or so (though there may have been problems before that, given previous damp issues and repairs). It probably warrants at least some patch repairs. Angled roof over reception room. Note bending of Decra around chimney (suspect due to weight of leaves which we found there - now cleared) About half of these roofs (about 180m2) are cold pitched roofs built over a flat roof (which I think was probably the original external roof). For that 180m2 section: Loft is c. 150m2, with a further roof/loft extending over the kitchen (c. 30m2), and further over the car port (though the car port area does not need to be insulated). Construction appears to be uninsulated joists, topped with a flat roof made of a slab perhaps 75-100mm thick of compressed straw, covered with what looks like bitumen felt (or similar). I think this may have been the original flat roof, probably constructed somewhere between c. 1955-1967. On top of parts of this flat straw/bitumen roof, there's c. 50-100mm of glass mineral wool insulation (see photos); other parts there's nothing or boarded storage. On top of this old flat roof, a lightweight timber frame was built, covered with a black (presumably waterproof) membrane and then sheets of Decra Classic (or similar) lightweight metal/composite roofing “tiles” (with what are I think GRP gulleys). I not sure there’s any OSB or similar between the membrane and the Decra - I suspect not. Rafters are generally 1200mm. Given the lightweight construction and wide rafter spacing, I expect it will only take a very lightweight structure (unless it’s substantially rebuilt/reinforced). Appears to have poor thermal performance / need better insulation. However, given the unusual construction, it’s not obvious to me how best to economically deal with it (and to do so in a way that doesn’t create the risk of condensation issues). Would mineral wool laid out over the old flat roof work? Or PIR? Alternatives would seem to be open cell spray foam, or PIR warm roof - but probably only sensible if re-roofing (which I doubt we can afford). Loft hatch area showing straw Section of strawboard lifted to show joists (uninsulated) Showing 1200mm rafters etc Some parts have up to 100mm mineral wool insulation above the old straw flat roof To avoid a roof replacement, it might be that patch repairs (e.g. Decra can sometimes be bent back) and CorkSol SprayCork (or similar) might be useful to improve noise, weather sealing, aesthetics and insulation. But re-roofing might be more appropriate/necessary. Cost, however, is a limiting factor. The other half of the sloping roofs, also Decra/1200mm rafters, is also a cold roof. However, it’s now well insulated (c. 200mm mineral wool between the c. 220mm joists, and another 100mm laid crosswise on top). 21 solar panels have been installed on that part of that section of the roof, so it would be preferable to avoid having to remove and reinstall those. This area appears to be (like the roof over the kitchen/car port) is in somewhat better (though I suspect still pretty poor) condition. In terms of the angled roofs, the priority is the sloping section containing the large skylight, and perhaps also the sloping section with the chimney. There is a square sectioned wooden clad brick upstand (with TV aerial) in the former, which used to contain a water tank. It’s redundant and could (but need not) be removed if that’s easier. It may be brick beneath the timber (given that it's brick underneath, I suspect it is, so removing it is probably more hassle than it's worth). From outside: From inside: Insulation at the property is generally poor. We might ultimately insulate the walls, perhaps with external insulation. The walls are a mix - some are very thin timber frame with no insulation - just plasterboard and timber frame. Others are blockwork, others painted masonry. Whilst I imagine that would be ideally be done before any re-roofing works (?), the roofs are a priority in terms of insulating and weather proofing etc. Would it be possible to do any re-roofing (e.g. flat roofs) in a way that is compatible with a) any future external wall insulation and (b) any future re-roofing of the Decra Classic sloping roofs?
-
Loft insulation advice - unusual construction
DanRobertsB replied to DanRobertsB's topic in Heat Insulation
Hi Nick - thanks for the tip! May give that a go if we can't find replacements / for the worse areas. What did you spray it with? TBH, I'd not thought about adding straw. I suspect what's there (other than the panels) is a compressed straw panel that's been pulled apart for access/to put in pipes. Property has been built and rebuilt several times (before our time - history of all this is rather vague!), and working on it throws up the "Chesterton's fence" dilemma all the time - never quite sure it's safe to undo what's already there (e.g. wiring, pipework etc)! I suspect straw is a bit of a nightmare in terms of fire risk, but then I've not looked into fire ratings of other insulation materials either. There's space to play with, so I'm really just keen to get some inexpensive but effective insulation in asap, in a way that doesn't create unnecessary risk (particularly moisture/condensation/wood rot, etc). Cheers, Dan -
Loft insulation advice - unusual construction
DanRobertsB replied to DanRobertsB's topic in Heat Insulation
-
Loft insulation advice - unusual construction
DanRobertsB replied to DanRobertsB's topic in Heat Insulation
Thanks. Yes, definitely two issues (well, probably more but that's another story!) INSULATION I can put that chunk of strawboard down that someone cut out, tape it down, and roll out layers of mineral wool over most of the strawboard area (hopefully there's no sense in a VCL). There are a few potential exceptions / complications: - Some of the loft (maybe 50m2) is boarded - raised on wooden battens about 10cm off the straw board. This would need lifting, raising (perhaps on large loft lefts) and relaying. Other parts are not boarded, with things stored directly on the strawboard, etc (maybe 40m2). So a similar approach would be needed there. - There are some areas where the straw has been cut out and there's wiring/piping in it. Fortunately most or all of that area is over the utility room and/or pantry, and I'm less fussed about the insulation properties there. If it's not ok just to put 300mm mineral wool directly over this, it may be possible to fit some 150mm PIR board over it to seal it off - but I suspect for much of it that won't work (not level), so mineral wool would be preferable if that won't create any issues. Photos to follow below, showing only about 1/5 of the 200m2 section, excluding the boarded area. The priority (not least given outrageous heating bill s) is really the insulation. It's also a cheaper and easier item to tick off the list. DECRA The Decra is in poor condition. I've yet to lift the tiles, but (strongly) suspect it's not laid on any flat board, just onto the battens (with that black - presumably waterproof - membrane underneath). I think it's also borne the weight of a fair bit of leaves and been walked on (not following the proper instructions) for maintenance etc a fair bit over the years (I suspect decades). Seems to be reasonably water tight but at the very least needs patch repairs. I'm not sure the structure will take anything heavier, which I'm guessing limits the options to Decra and perhaps sheet metal. TBH I'm struggling to find anyone willing to work on it - almost everyone (save for one who wanted to do the sheet metal) wants, e.g. with EDPM over PIR. The whole section of this roof is about 200+m2, and then there's a further c. 100m2 (some with solar panels), so that's a massive job. And it's unclear the structure would take the weight. No ones provided a finalised quote, but to do the whole 300 odd m2, the suggestion has been it might be c. ÂŁ100k+ (yikes). Which seems kinda crazy to me (and beyond the budget) ... Patch repairing with some new Decra therefore seems rather more appealing, if I can find someone to do it. -
By warm side, do you mean on top of the plaster of the boarded side? I.e. inside the room. If so, how does one go about that, and what should be used? There are LED spots through it too, so it wouldn't be continuous. But I plan to fit Loft Lids to the back of the LEDs (not entirely air tight, but ... Or do you mean the wood on the cold side of the loft (so behind where the current insulation is), which would then be covered with either 300mm mineral wool or 140-150mm PIR. So that'd be the warmer side of the cold side (!).
-
- 1 reply
-
- skylight
- secondary glazing
-
(and 3 more)
Tagged with:
-
Hi I have a large (c. 5.8 x 1.6m) skylight, on a low pitched roof (I'd guess c. 15 degrees). This appears to be made of two sheets of 10 or 12mm polycarbonate. I suspect it was built in around 2006/2007. The polycarbonate has since turned somewhat cloudy – so a little translucent now, rather than clear (clear would be preferable). The roof is an unusual and lightweight construction – see Since it’s a single sheet, thermal performance is terrible – there a lot of heat loss, and a lot of condensation in winter months. So it either needs to be: 1) Replaced with a glass double glazed unit (quotes seem to be c. £12k-20k), and a structural engineer would be needed to confirm whether the loft can bear the weight of a glass unit, so quite apart from the huge cost, it might not even be viable. On the plus side, this would be professionally installed, stay clear, provide decent u values, and could be done in UV control glass, etc. 2) Secondary glazed with acyrlic. I suggest with a sheet of 12mm Perspex (clear cast acrylic), either on the inside or outside, with a between the two sheets. It might make sense to replace the existing polycarbonate at the same time with new, clear sheets. Vastly cheaper (perhaps £1k-2k, including labour and materials). Thermally not quite as good as a proper double glazed unit with inert gas between the layers, but should make an appreciable different for a much lesser outlay. I’ve had a few thoughts on how this might be done by building a frame on top, or a frame underneath, but ideas would be much appreciated; also on how best to re-seal the outside of the skylight to the roof (flashband would probably work … though it seems a bit temporary!). I’m a bit concern that 2 might be a false economy in the long term. But since we may ultimately need to replace the Decra roof, I’m equally concerned that replacing this with a glass unit (1) should only really be done once the roof’s (re)done …. Step 1 of course is getting a structural engineer in, but in the meantime, thoughts welcome – as would suggestions of inexpensive glazing companies for sky lights.
- 1 reply
-
- skylight
- secondary glazing
-
(and 3 more)
Tagged with:
-
Hi I'm keen to insulate a loft with unusual construction (see below). I'm hoping that can be the usual "roll out some mineral wool" but am weary of condensation risks (all the more so as this is a timber frame, timber clad house). ROOF: There's about 180m2 cold pitched roofs, seemingly built over an older, pre-existing flat roof. Construction appears to be uninsulated joists, topped with a flat roof made of a slab perhaps 75mm thick of compressed straw, covered with what looks like bitumen (or similar). I think this may have been the original flat roof, probably constructed somewhere between c. 1955-1967. On top of parts of this flat straw/bitumen roof, there's c. 50-100mm of glass mineral wool insulation (see photos); other parts there's nothing or boarded storage (there are also parts where some of the straw's been removed). On top of this old flat roof, a lightweight timber frame was built, covered with a membrane and then sheets of Decra Classic (or similar) lightweight metal/composite roofing “tiles” (with what are I think GRP gulleys). Rafters are generally (a wopping) 1200mm. The whole structure appears to have very poor thermal performance, and so need better insulation. However, given the unusual construction, it’s not obvious to me how best to economically deal with it (and to do so in a way that doesn’t create the risk of condensation issues). Parts of the Decra are in poor condition - cracked / banana’ing / patch repaired. See attached report from Langley. However, we’re not aware of any obvious damp / water ingress over the past 18 months or so (may have been a problem before that). Probably warrants at least some patch repairs. Note bending of Decra around chimney (suspect due to weight of leaves which we found there - now cleared) Loft hatch area showing straw - between ceiling and cold roof Inside of roof - section of strawboard lifted to show joists (uninsulated between joists) Showing 1200mm (uninsulated) rafters etc. The thin Decra is then on top of this. Some parts have up to 100mm mineral wool insulation above the old straw flat roof Would mineral wool (up to 300mm) - or possibly sheep wool ( (more expensive but no nasty loose fibres in the cold loft space, which is used for storage; good resistance to any moisture) laid out over the old flat roof (i.e. on top of the bitumen felt) work? I'm hoping/guessing a VCL isn't necessary (or the ceiling and//or bitumen already acts as one). The (considerably more expensive) alternatives would seem to be: - Open cell spray foam of the entire inside of the loft. But concerns about impact on insurability/mortgagability, etc - seems some insurers/banks won't touch homes insulated with the stuff. - PIR warm roof - but probably only sensible if re-roofing (which I doubt we can afford). But the structure may not support the weight of PIR plus new roofing materials. Ultimately, however, finding a solution to the roof may be necessary (perhaps just patch repairs/replacing the Decra).
-
I’m looking to insulate a vertical wall onto a cold roof in London. The wall, from inside to out, is paint / presumably plaster / sheet timber (unsure whether OSB / plywood / something else) and a few supporting battens / cold roof. In the winter, I guess you’re looking at temperature difrentials of perhaps max 23’C inside (typically lower – 18-20’C) and say -4’C outside / in the cold roof. I’m unsure how best to do this – particularly given: (i) dew points / risk of interstitial condensation / whether a VCL is needed; and (ii) the likelihood that we may need access to this wall again, since we’re eventually likely to either replace the large c. 5.8m x 1.6m single sheet polcarbonate skylight that’s at the top of the wall, or secondary glaze it. It’s possible that may require additional structural support. Of course, in an ideal world, we’d do the glazing work first but that may get held up for various reasons, and the heat loss through this wall in the meantime is bad. Even once the glazing’s done, I’m still not sure how best to approach the insulation. Space isn’t an issue. Seem to be sequence is : 1. Glue downlight covers over LED lights 2. Somehow (?) add a VCL [?] over the all the plywood, studs and downlight covers (so there's a VCL on the warm side). a) This may not be necessary, given (i) the painted/plastered wood; (ii) if using PIR, the dew point for interstitial condensation would probably fall inside the PIR, which I expect would be fine as there’s not likely to be much moist air in them. Haven’t done a WUFI calculation though. b) If a VCL is advisable, what should be used? 1000 gauge polythene? Would any of the SuperFoil products be more appropriate? c) If it is advisable, how;s it best attached? 3. Cover VCL with insulation. This could be: (a) 300mm of mineral wool (quick, cheap, easy to work with, breathable), held in place by chickenwire. I have both already. Easy to remove and replace for access. Since mineral wool is breathable, and the wall is plastered and painted, would a VCL be needed on the inside of the timber before the insulation? (b) As above, but sheep wool insulation (more expensive but no nasty loose fibres in the cold loft space, which is used for storage; good resistance to any moisture). (c) PIR. Probably in two layers (40mm between the studs, 100 or more over the top). More expensive, harder and more costly to cut and fit, harder to remove and refit once fitted. But perhaps doesn’t require a VCL…? Struggling to see much advantage. (d) A hybrid. 40mm a or b – or RW3 rockwool sheets – between the studs, the overclad the lot in PIR. I suspect 3a or 3b is the way forward – just wondering whether the hassle and expense of VCL (2) is sensible. And if a VCL is fitted, does that create the risk of water gathering between the VCL and the wood, which would presumably cause damp/wood rot, etc? Thoughts greatly appreciated! Loft side of wall/skylight support Wall and skylight from inside