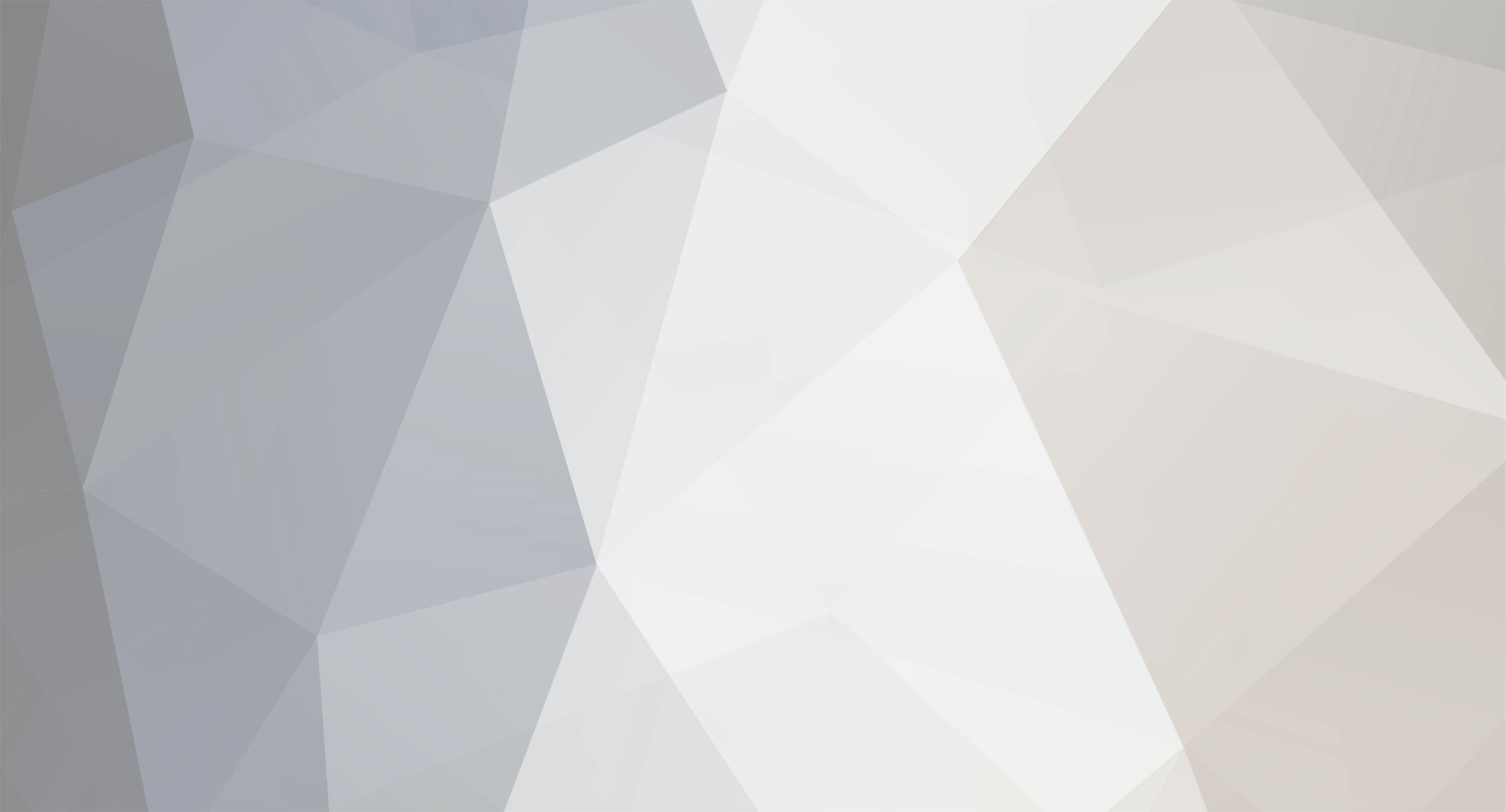
-
Posts
21 -
Joined
-
Last visited
Everything posted by Google
-
Hi Joe...I'm slightly confused...I thought the plots were in West Lothian, not South Lanarkshire? I recently completed my build in West Lothian, so have a bit of knowledge there.
-
Hi all, can anyone give some ball park figures for laying floor tiles please...just the labour cost? Tiles are large 1.2m x 1.2m...and will cover 100m. also, regular 300x600 tiles in bathroom...floor and wall. thanks in advance.
-
Can anyone give me a ball-park figure for laying concrete roof tiles? The felt and batten has been done, but due to unforeseen circumstances, the roofer has had to leave. I've now got someone coming tomorrow to price for just the tiling...400m2 of Russell Grampian concrete tiles....just wanted a rough idea of what to expect. 75% of the tiles are also already loaded. £5/m...£10/m ???
-
Ok...To clarify...I guess what I meant was, I have a builders supply account who deals with Brett Martin...got my foul and surface drainage there. And I also have a relative with a plumbing/bathroom supplier where I'm given a terrific discount. However, if I get a decent quote, all in, for supply and 1st/2nd fix, I'll be happy.
-
Yes...Manifold distribution. The loft space will be cold, however there is a plan to develop the loft space(attic trusses have been erected)and if I can insulate the loft roof now, rather than later, then I will be doing that. A hot water recirc pump is not entirely necessary, but a nice to have if affordable...at this stage I would say Yes. Taps are monoblock Flexis or fixed? No preference Copper on show and Hep2O elsewhere..? Yes
-
It can be supply/fit or fit only...I would actually prefer fit only as I have access to trade accounts for the materials, but either is fine. I don’t mind if it’s copper or Hep20...I know some plumbers have preferences. Either is fine with me.
-
Sorry...First and second fix. I have all of the sanitary wear bought for the en-suites/bathroom already. 1 dishwasher, 1 washing machine, 1 Quooker tap, 4 showers(1 of which is electric), 2 baths. UFH is all carried out by ASHP company. Huge service voids open in the roof space. Hope this helps...need any more info, please ask.
-
Looking for some guidance on what I should expect cost-wise for the plumbing on my self build. I'm getting wildly conflicting prices from plumbers. Ball park firgure will do...£4k?...£8k? It's a large 300m2 bungalow...total of 4 bathrooms all with showers, 2 have baths, utility, kitchen. Installing an ASHP too with underfloor heating, although this will be carried out separately by the ASHP company. Plumber would just have to supply the flow and return to the pump. 02 - ground floor plan.pdf
-
Thank you!!
-
Thanks for the advice. We have the offload sorted fortunately. I may see about laying the panels on the concrete slab...that way keeping them flat. And the blocks is a good idea to keep things out of the wet. I already have an area cleared with terram put down where I can stand the trusses upright(On blocks)
-
Next question folks.... So I have things happening to get the steel corrected, and also should have a new team of joiners lined up shortly, however, the kit is due next week and the joiners may be a week or so (perhaps 2)behind that. So, will that cause any issue with the timber kit? I’ve had someone suggest that it could warp if it’s not stored correctly and it gets wet from lying out in poor weather. Is this true? Should I store the panels flat and cover with tarps, for example and have the trusses stood upright? Obviously, it’ll be fine once it’s bolted/nailed together but if it lies for a week or 2 first? I have to accept delivery as the manufacturer doesn’t have the facility to store for me...I’ve already managed to get it delayed till next week. All advice welcomed.
-
Thanks for the replies folks. The architect is supposed to be overseeing the build, although not full project management...that's our job. He is also providing our warranty and technical audits. The kit supplier also supplied the steel, however, they have supplied exactly what they were instructed to supply by the architect and structural engineer. We wanted the kit company to supply both the steel and timber as well as the windows, so it should all fit together. The kit company sent the steel drawings to the architect for approval prior to fabrication. He admitted to not checking them properly, hence the steel is now wrong. There was a height to the steel which should have been to the bottom of the beam...it was made to the top of the beam...so it's out by 300mm(the depth of the beam). Not the kit manufacturers fault...they made what they were told.
-
Okay....so now I've just found out that our architect didn't check the drawings properly and the steel that has been erected(3 sets of goalposts)is all 300mm too low!! The fabricators took the heights to the bottom flange of the beam rather than the top, and our architect didn't spot it. He thought the beams would be sitting on top of the columns rather than be bolted to the side. We only saw the problem when it was up and we measured it. The guy is a balloon....made some smart remark along the lines of "ach well, it won't cost much to fix". Our bloody kit arrives in 10 days time and I'm supposed to be able to get the beam extensions fabbed, dismantle the steel, have the new bits welded on top of the existing columns and re-erect and bolt on the beams!!...and have all that done for the kit and joiners arriving. Goodness knows how long it will even take just to get the steel I-beam extensions. Wanted to punch his lights out....he couldn't even be arsed to come to the plot..says he got waylaid. We have kit arriving, with steel at the wrong height due to his failure to check the drawing correctly, and yet something more important has his attention. And of course, the chances of anything being done at the weekend are zero.
-
We were originally looking at a 1 1/2 storey but the plot is 1.6 acres, so decided to spread ghe house over 1 floor. Our plans have been approved for another 2 bedrooms and a mezz in the attic, so we’ll do those before we sell in the future. Planning on doing this again...all being well.
-
The frame includes the internal partitions, so I'm talking about the wool insulation, ceilings and plasterboard throughout. 02 E - ground floor plan.pdf
-
Thanks everyone for the advice so far. Wish I'd found this forum months ago. Would anyone be able to give an indicative time/manpower requirement for the 300m2 roughings stage? 4 bed, 4 bath bungalow, lounge(vaulted ceiling), kitchen, utility, snug, garage. Ballpark timescale would be brilliant.
-
From what everyone is saying 2-3 weeks sounds a reasonable timescale for the erection, perhaps less as it's on one level. Just need to get a decent estimate on the roughings now. Thanks everyone for all your help
-
We're using Claymore Timber from Cupar in Fife, who've been brilliant.
-
Thanks for that Christine.
-
Thanks for the quick reply Dave. The panels are built already. I guess a fair estimate based on your timescale would be 2 double up the time, so 4 guys 2 weeks to get the kit up, perhaps less given it's only 1 level. Would internal roughings be approx the same timescale as erect, or more...say double? We're also putting in velux for the future attic conversion at this stage and we're being told 4 hours per window installation. Realistic? I'm in West Lothian, 5 minutes from Livingston.
-
First time poster on here, and first time self builder in Scotland. We're self project managing too and up to now everything has gone well....founds, underbuilding, drains, slab all complete without any major headaches. Steel is in place and scaffold up. However, our joiner friends who've been lined up to erect the kit for us now seem to be trying to take advantage and after being very evasive over the price now indicate something much more expensive than first intimated. Cash job. They make £250-300 a day normally on site, cash was to be £200-250 We are building a 300m2 bungalow with roof trusses to enable future conversion. Initially, they wanted to put 2 boys on the job to erect, for 3-4 weeks, wind/watertight in 5 weeks. So estimated at 11k total cash. Now they say 4 guys 6 weeks. Can anyone give an indication of what timescale/manpower is realistic?