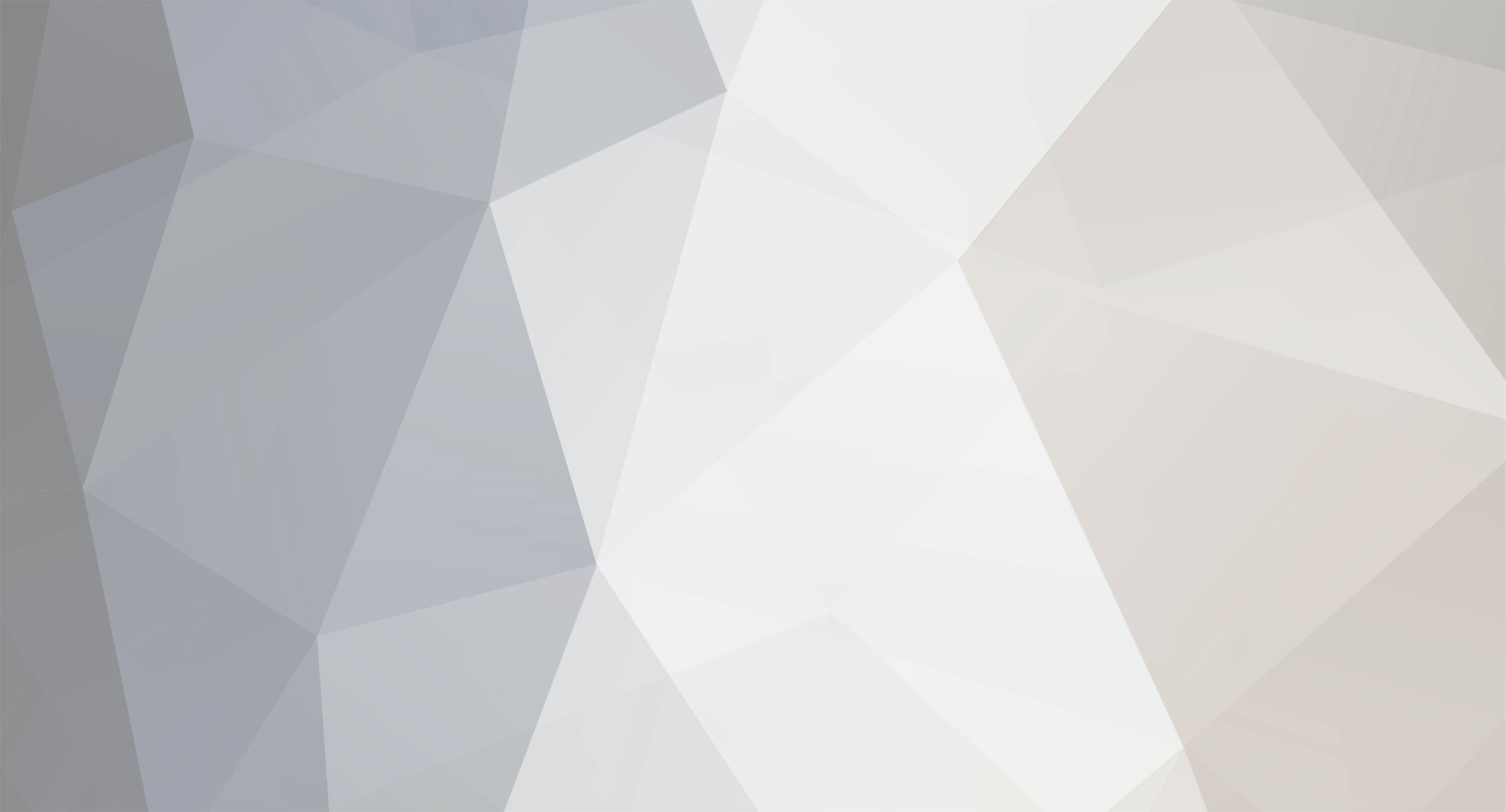
Erik79
Members-
Posts
14 -
Joined
-
Last visited
Personal Information
-
Location
London
Recent Profile Visitors
The recent visitors block is disabled and is not being shown to other users.
Erik79's Achievements

Member (3/5)
0
Reputation
-
New ASHP installation (Samsung monoblock)
Erik79 replied to Erik79's topic in Air Source Heat Pumps (ASHP)
It is a 8kw monoblock, gen 6. Not entirely sure what will constitute small diameter in this case(?), it supplies our cast iron radiators and we have a series of 22mm and 15mm copper pipes connecting them. -
New ASHP installation (Samsung monoblock)
Erik79 replied to Erik79's topic in Air Source Heat Pumps (ASHP)
Thank you, it is good to know what to expect as the final product. -
New ASHP installation (Samsung monoblock)
Erik79 replied to Erik79's topic in Air Source Heat Pumps (ASHP)
When we asked how we will operate the system we were told that we will do it via the Samsung app and we were advised not to get a Nest or other type of app based thermostat. -
New ASHP installation (Samsung monoblock)
Erik79 replied to Erik79's topic in Air Source Heat Pumps (ASHP)
There is no buffer tank (this is what is called I think ?) installed and they said they will come back to install it in the new year but the system was handed over to us like that to start using. After it went live the pipe with the cable tied on started leaking and what you see (the temporary patch and the bucket) is our attempt to prevent flooding the floor below.. We got since then two error codes (e911 and e101) and the system has stopped working. I don't mind giving anyone the benefit of the doubt that when it is finally finished it will look amazing but our worry so far is that the installation lacks attention to detail. For this to be MCS certified do contractors have to submit photos of the final installation to someone to be approved? -
New ASHP installation (Samsung monoblock)
Erik79 replied to Erik79's topic in Air Source Heat Pumps (ASHP)
-
We had recently installed a new ASHP, including new cylinder etc. The cylinder and pipework installation looks a bit messy but it is inside a cupboard so happy if it is just 'ugly' but otherwise works ok and is safe. Some of the things I noticed: -There isn't an isolation valve for at least one of the pipes coming out of the cylinder and feeding the circuit. There is no way to tell what is the mains cold water feed vs the warm water unless you know what you are looking for as none of them seems to be labeled. -The cables connecting the control kit to the various bits seem to be touching the pipework at places. -The only drain valve on the system seems to be on the radiator, neither externally or inside the cylinder cupboard I can see another one (maybe is not needed?). -I was told I would be a able to use the Smart things app to remotely control the Heatpump but there is no WiFi kit installed, again maybe not needed for that? -Externally apart from bits of insulation missing there is no drip tray installed at the moment,again is this just optional? Apart from the installation manual that came with the heatpump is there any other document I can consult for the installation mandatory requirements? It would be good to have some peace of mind as this installation has been quite a headache for us and now that it has been 'done' we would like to ideally forget all about it!
-
We had recently installed a new ASHP, including new cylinder etc. The cylinder and pipework installation looks a bit messy but it is inside a cupboard so happy if it is just 'ugly' but otherwise works ok and is safe. Some of the things I noticed: -There isn't an isolation valve for at least one of the pipes coming out of the cylinder and feeding the circuit. There is no way to tell what is the mains cold water feed vs the warm water unless you know what you are looking for as none of them seems to be labeled. -The cables connecting the control kit to the various bits seem to be touching the pipework at places. -The only drain valve on the system seems to be on the radiator, neither externally or inside the cylinder cupboard I can see another one (maybe is not needed?). -I was told I would be a able to use the Smart things app to remotely control the Heatpump but there is no WiFi kit installed, again maybe not needed for that? -Externally apart from bits of insulation missing there is no drip tray installed at the moment,again is this just optional? Apart from the installation manual that came with the heatpump is there any other document I can consult for the installation mandatory requirements? It would be good to have some peace of mind as this installation has been quite a headache for us and now that it has been 'done' we would like to ideally forget all about it!
-
We are retrofitting insulation to our Victorian property (2 stories) and we want to install a dMVHR in the kitchen/dining room in the ground floor. It is open plan and the dMVHR will be opposite the kitchen and next to the patio door. Patio door and kitchen window do not have trickle vents. We also want to install dMEVin the bathroom to try and manage the high humidity levels (semi-basement), there is a window in the bathroom with trickle vents. Does this plan sound ok? Is there a reason/advantage to go for dMVHR in the bathroom as well?
-
You are right on that one, the original entry seems to be at the base of the railing and expanded from there. Previous owner seem to have tried to DIY the crack by some form of resin and cement mix but obviously it failed and led to more damage. We are restoring the railings as well along with the slate slab. I wasn't aware of lithomex I will look it up.
-
We have a slate balcony that has suffered years of water damage. One of the edges has the most extensive damage, borderline compromising the structural integrity of the slab as directly underneath that edge is one of the pillars holding the balcony (the crack goes all the way almost the depth of the slab in that place). We therefore need a solution that will not only provide waterproofing but also structural bonding. I have got a couple of quotes to use a waterproofing system based on PMMA resin. This will cover the whole balcony and the contractor says that it will also provide structural repair once it is applied and cured within the slate cracks. The (only) stonemason that came around to see it suggested to insert reinforcement bars prior to waterproofing. I want a good solution but I also dont want to do unnecessary repairs if the PMMA resin is the solution that can offer both waterproofing and structural integrity?
-
I decided to buy the bullet and go for the goal post. lifted he floorboards today to look at the condition of the subfloor before proceeding with the goal post installation. There needs to be a 120x120cm concrete base on each end, flash with the wall. The concrete base needs to extend 50cm past the external wall (and equally where the other end meets the internal wall). This means that it needs to go past the existing masonry foundations. Does anyone has experience on what is considered best practice in this case? Do they need to go underneath the existing foundations or replace them? I am spooked by the various experiences with tradespeople and this is one of the tasks that we really need to get right. Second photo shows the subfloor next to the external wall (masonry footings).
-
The 350£ for brickwork support was that strike me as odd as well, that and the 400£ for concrete cill/lintel. From a quick google search you can get both for 150£ (200£ max if you are looking for the most expensive prices).
-
I need a new window opening in my kitchen (1.5 by 1m), it is actually an old window that has been bricked up and we are essentially re-installing it. Structural engineer came around was very reassuring that it should be straight forward plus or minus needing a new lintel. Builder came around and said that there are cracks going through the lintel so it might be that when they remove the bricked up opening the arch will fall (window opening is at the ground floor of the house). He then quoted the following: Labour £400+vat Mats £80+vat New concrete cill and new concrete lintel £400+vat Temp support for brickwork £350+vat Does this look ok to people? Is this a fair price (we are based in London but still!) including the price of materials?
-
Hi everyone as a bit of background we want to join 2 rooms on the ground floor of our property by opening up one of the walls. Overall the building is 4 storeys split into 2 different properties (build around 1875 on clay soil). Had the structural engineer coming in a few weeks ago and originally asked him to make a plan that completely removes the existing wall so there is a seamless transition between the 2 rooms. He suggested to replace the existing wall with a steel goal post on top of new concrete pads which is more invasive and expensive that we thought originally. After he send the calculations through we discovered that the wall that we want to open is actually not aligned to the rest of the walls on the next 3 stories above (it has a 20cm or so offset). We asked him to come back for a second opinion and also asked him to run calculations that will allow us to keep part of the existing wall (maybe if we keep 50cm or so on each side of the existing wall and we just make the opening smaller, between 1.5-2meters). We were hoping that in this case we wouldn't need a goalpost and the concrete pads and just a lintel will suffice. SE came back to say that this is not possible now because of the off set and the new support needs to be aligned with the rest of the walls above and eliminate the offset that exists for the last 150 years or so...I dont want to go against the science here but what am I missing? Does it make sense to 'correct' in retrospect the original plan of the house? We also dont want to go through all the extra trouble (and cost) that comes with installing the goalpost and the cement pads if by making the opening smaller will allow just a lintel to take the load. The wall we want to open is between the bathroom and the dining room and is marked with red in the image below. This kind of secondary consideration but the house is build on clay soil and high risk for subsidence but not entirely sure that adding a steel goalpost and concrete pads will actually make the risk less given that the rest of the foundations will still be on the soil. We are planning to get a second opinion from another SE but would appreciate peoples views on this.