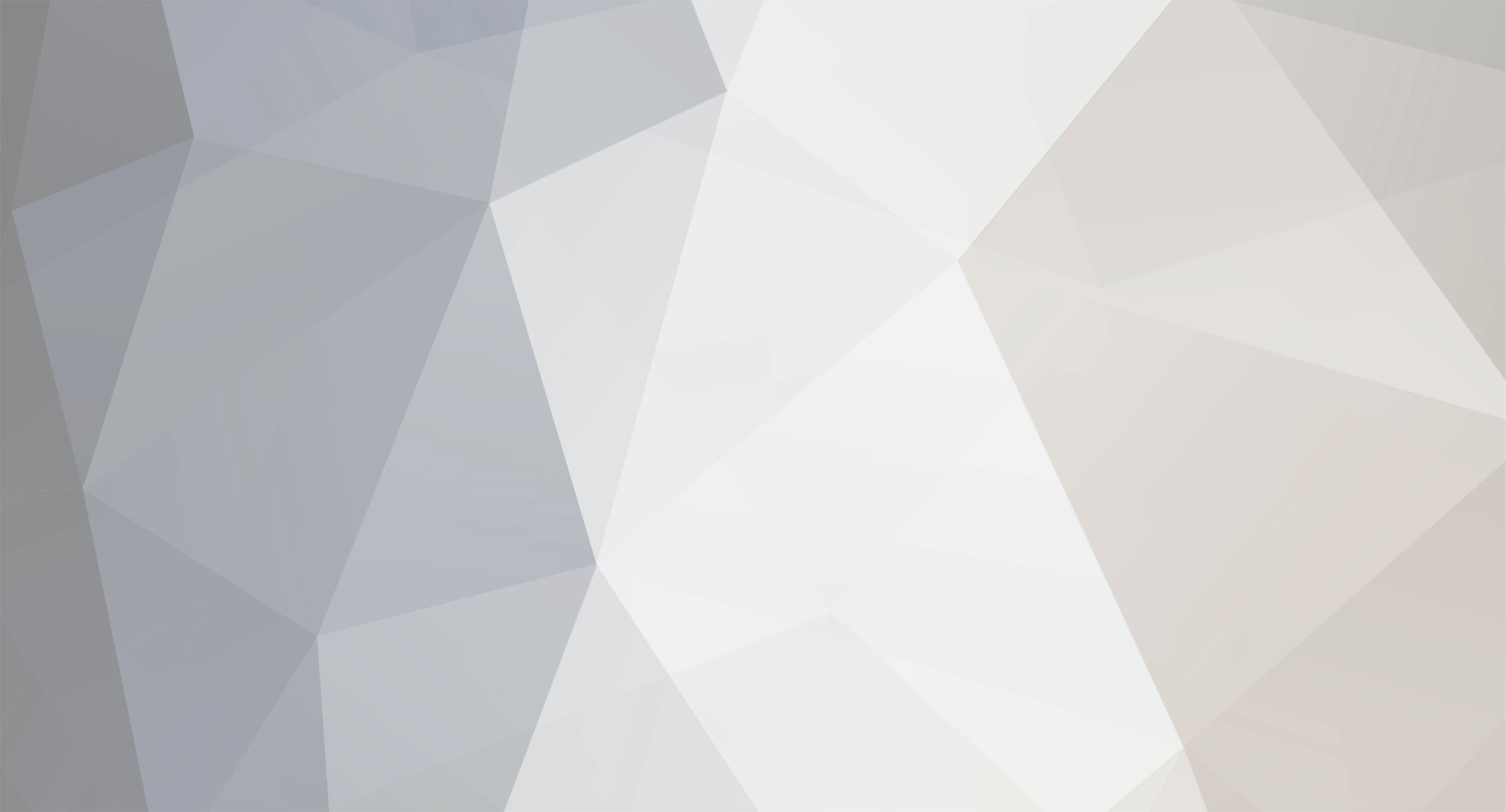
osprey
Members-
Posts
64 -
Joined
-
Last visited
Everything posted by osprey
-
An interesting idea, and I would imagine it would be a lot better than nothing! I believe part of the subfloor ventilation in houses of that age came through the gaps between the floorboards in the wooden floor itself. Later house with T&G flooring tended to have more airbricks.
-
I am just going through the same process. My integrated extractor fan (Kneff) came with lightweight butterfly flaps to prevent back drafts. They fit on the fan outlet to the ducting, are small, came in a separate packet, and are easy to miss. Are you sure your fan does not have them? I was wondering if this was sufficient, as I have a couple,of meters of 150mm solid ducting to the outside wall, and I would rather not have cold air in there when the fan was not running. The same company that does the Bullnose vent mentioned by Spinny also does s/s vents with backdraft prevention. I also wondering how much they compromise performance. https://www.amazon.co.uk/dp/B09H5DTS9D/ref=twister_B09P4KVWW6?_encoding=UTF8&th=1
-
Having seen a wall that I had filled with Eps beads partially taken down for an extension build, I agreed with the nook and cranny part!
-
I think I have found it, or at least it looks the same. Thanks all! https://www.wrekinproducts.com/products/access-covers/recessed-trays-floor-finish/38mm/c271m060045
-
Thanks for replies. Those hooks look about what I had in mind. I have done picture searches, but nothing comes up. Maybe a chat at a drainage merchant,mas you say.
-
Hello you helpful lot. Any guidance on how to lift this drain cover (picture attached)? Is it latched in some way, or is it 'just' a matter of getting the correctly shaped tools into the holes and lift? IS there a special tool/key for the job? I have tried a robust screwdriver, but cannot get any lift. Thanks in advance!
-
Lower power consumption to meet regs.
-
Thanks. I went for 2400 in the end (as I had not seen any replies) so I am glad I withing your range. 300mm downstand looks about right.
-
I am having an extension built to make a kitchen diner (8 x 5) where the 'diner/dayroom' part will be approx 5 x 5. I will be having lift and slide patio doors. The doors are aluclad, as I like the chunky frames, and it fits with the 1920s period of the rest of the house. I can't make up my mind on the height of the sliders though. I know it is personal preference, but any thoughts? Sliders will be 3m wide, ceiling height 2.7m. The rest of the house windows (bays etc) go full height, but have toplights. I want a bit of a downstand and full height would too much imo. The frame is getting on 200mm wide at the top, before the glass is reached. I am thinking 2.4m high aperture (glass to 2.2m) so 300mm downstand but that seems a lot of glass! (Urban setting, but not overlooked, garden 23 x15 meters) Too high? Too low?
-
Large glass sliding door set - extra solar coating?
osprey replied to osprey's topic in Doors & Door Frames
Ah, I changed my search terms and founf that this has been asked a few times before.... -
The plan is to have a 2 panel, triple glazed sliding door set (3 x 2.4m, U-value <1) on the new extension. This will be facing SW. Would it be worth getting an extra solar coating to reduce heating effect? I was considering it for double glazing, but I imagine triple glazing reduces the issue anyway. This would be in addition to the normal e-glass coating, of course. Also, for anybody who has had it done - is the additional tint noticeable? I would probably have voiles to reduce glare, anyway.
-
Yeah, when they quoted, the LV installers assumed they would be doing the 'double' pour, but they said they were happy if the UFH installers did the first one. (They checked, and said they use the 'same one as Wunda recommend', but I didn't know Wunda recommend two at that stage).
-
Great reply, thanks for the detailed help. I am really worried about not having a warm room, after all this work, but also worried about not taking the opportunity to have UFH where possible. (Even my architect has Wunda in and extension she did for her own similar age house). As I have already got 30mm height buildup, and I would want to insulate under the existing floors whatever the heating system anyway (100mm celotex), adding retrofit UFH seemed an obvious next step. The plan is to have the 'new solid floor' diner part of a separate circuit to the 'suspended floor' kitchen, as different heat loss, as you say, but also cooking generates it's own heat... Doing the hallway as well (while leaving radiator in place) was a more speculative idea - main heating by the radiator, but some radiating heat from the floor as background for now, but UFH heating in place should I get around to further insulating the rest of the house (e.g. with EWI). I appreciate balancing would be an issue, even with this relaxed requirement. But just the new kitchen/diner as UFH would be great, but a catastrophe if I had to rip it up to reinstall radiators! With the screed, I am told it would take two layers to get the right depth. The builder could do the first layer, or the Amtico installer could do both. Not sure if the Amtico installer could/would use the Mapei stuff. (WRT plinth heaters, is there no problem with hot air >>27⁰ being blown across the surface of Amtico?)
-
I think that is overstating it a bit. Just to be clear, in the new kitchen diner it is ONE system over two floor types - insulated solid and insulated suspended (the uninsulated solid part is small enough to leave out).
-
Using the in-screed system in the new extension was my first thought, but: 1) Amtico flooring must not be heated above 27⁰, so Wunda supply a temperature sensor for the floor. Not sure if this would work for screed, but even if it did, the 'access' pipe lay to the extension would run with the surface mount stuff across the kitchen, and may get too hot 2) Having a mix of UFH and radiators AND a mix of floor types put me off having a mix of UFH systems as well!
-
Correction to original post: a large part of the kitchen floor will be covered by cupboard units, of course, so the 'solid' part under UFH would only be 1 x 1.8m. The remaining 'suspended' part under UFH would be more like 12sq metres. (The diner is new solid floor, kitchen is mostly suspended wood, if that was not clear in OP)
-
I am getting close to starting my extension build, and keep second-guessing myself on heating method, so would appreciate thoughts on my current plan. The extension will be a 5 x 5m single-height extension to my 1920s built house. It will be knocked through to the original kitchen, to make a kitchen/diner/utility room. The new kitchen part will be 5 x 3m. The floors will be a mix of new insulated slab over block/beam in the extension/dinner and suspended wooden floor, with a smallish area (3 x 1m) area of old solid floor, in the kitchen area. The extension will be built to latest insulation standards, and the suspended floor has 100mm joists, so 100mm celotex insulation will be relatively easy to install. The kitchen area has 50mm filled cavity, and will have another 50mm insulated plasterboard added internally. The current floor has ceramic tiles, cement screed, and plywood on top of the original planks, so it has 30-35mm of height build already, that I can remove and install UFH. I would like to install a retrofit UFH system, something like the Wunda system, across all three floor types, divided into 2 heating areas (kitchen and diner). I would also like to do the hallway (a third heating area) in the old part of the house with the same system, as it currently has the same floor covering over suspended wooden floor, which has to be removed wiring reasons anyway. I would leave the existing radiators in place here, as well as in the rest of the ground floor (living and sturdy rooms) and upstairs, which are also in the old part of the house. Proposed floor covering over the pipes would be 10mm latex self levelling compound and Amtico. Any thoughts of viability of such a system/layout? Thanks.
-
Yes they do aluminium ones as well. Any comments/feedback on product, service etc?
-
Yes those are the guys. (Sorry, an 'l' slipped into the body of my post, but not the title). Good to know they have been around for a while. Any need to call on them for support? Incidently, I note that their beading for the glass is internal, which means you don't have to remove the alu cladding to replace the glass. Rationel etc have external beading: I guess for the smoother internal look?
-
Has anybody here used or had experience of Rawlington aluclad windows? They seem to have a reasonable product, a showroom in Gloucester, but I cannot find them on this forum. They seem to be one of the few suppliers that offer an installation service as well.
-
If the rockwool sags, then you will have an unvented air space over it. A sheet of foil covering would give that air space an R-value of 0.5 m²K/W, according to the .pdf. Pretty good.
-
Horizontal? Do you mean the insulation layer is horizontal, or the heat flow? If the former, the in nearly all cases the U value of insulation that uses a gas as it main insulation material is worse when installed other than horizontal? If that latter, then they are nor considering convection within the insulator would change with orientation. it may (or may not) be a small effect. However, I used PIR under my floor, suspended using membrane. It got me thinking: even if the PIR was not cut perfectly, the gaps would be fully protected from drafts by the membrane and would therefor be a static column/pocket of air: probably a better insulator than the PIR! Therefore, would not a loose layer of Rockwool withn the protective membrane be even better? A static gas being better than any solid for conductive transmission. How good would bubble wrap be in the horizontal orienation!
-
Yes, but I dont think it answers my question.
-
I have been thinking about insulating under suspended wooden floors, but I have not found an answer to the following: I think U-values are calculated with the material in a verticle orientation, but the orientation must have some affect? (I have seen examples where a double glazed window U-Value drops from 0.29 to 0.4, when going from verticle to 45⁰). With underfloor insulation, the heat source is above, the sink below, so heat transfer by convention should be almost non-existent. Should not e.g. Rockwool have a higher U-Value for this use?
-
They will not do installation, or suggest someone.