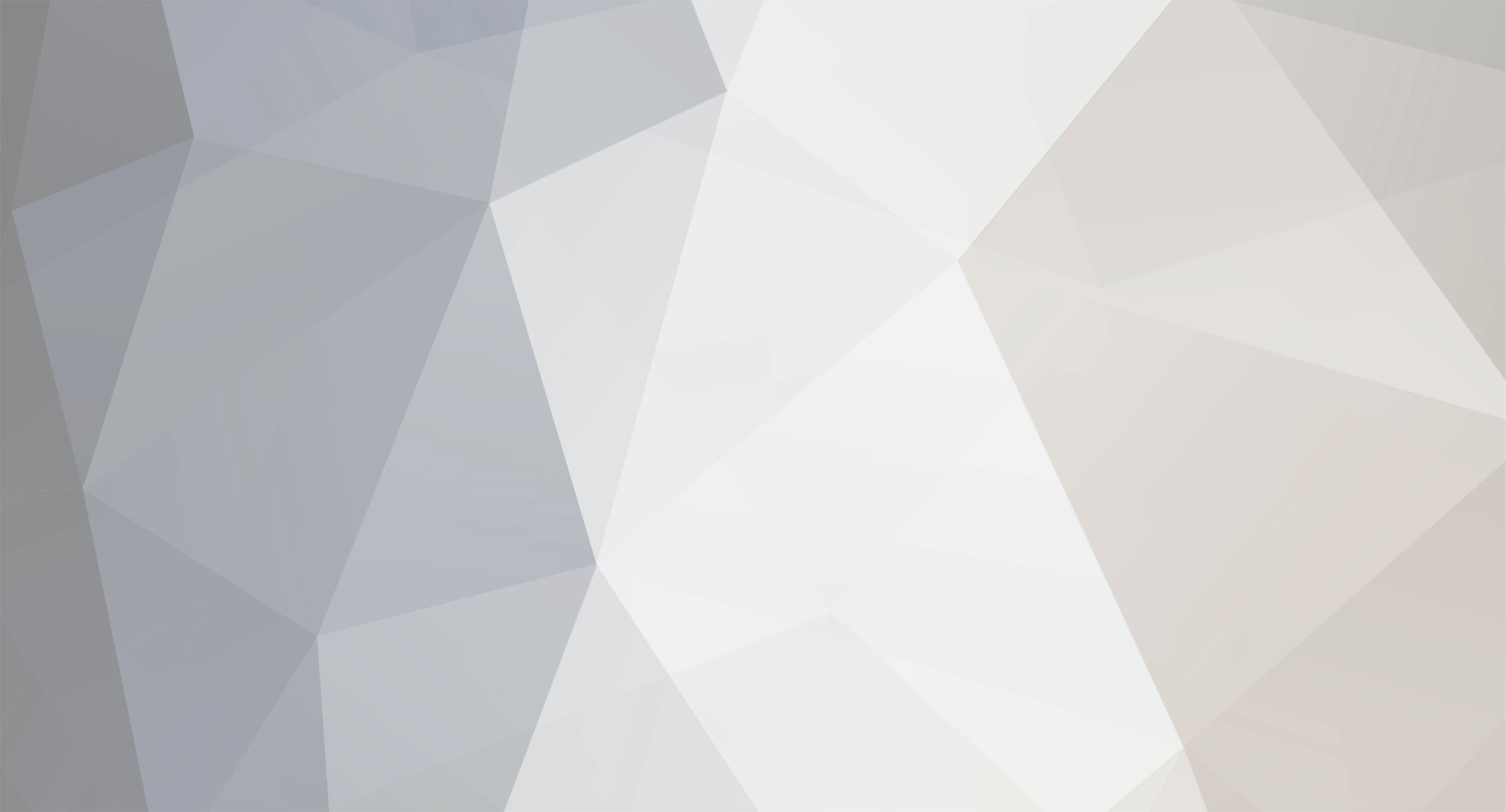
grahamA
Members-
Posts
23 -
Joined
-
Last visited
Personal Information
-
Location
Lancashire
Recent Profile Visitors
The recent visitors block is disabled and is not being shown to other users.
grahamA's Achievements

Member (3/5)
0
Reputation
-
Thanks nod. It looks like you had the flashing of the single storey already in though? Did you have any issues with the finish up to the windows once these were installed?
-
I have a bit of a conundrum. I am trying to decide whether it would be too much of an issue if i rendered a new extention (which has the new front door location) before installing an external dual pitch porch over the front door. In an ideal world i'd get the porch built and then render up to the proch roof flashing etc however there are a number of reasons why i want to get the render done first and the porch done later. When the extension was built (concrete block) no lead flashings were installed in the blockwork as i was unsure what porch and size etc, therefore this will have to be retrospectively installed in the blockwork. If i get the extention rendered will it be possible to install the porch without undermining the rendered wall or limit the damage to that be locally repaired which won't cost an arm and a leg? A few other options could be: 1 - Install the lead flashing only and render upto to this. 2 - When I render the extension don't render the entire wall where the porch will be installed (This is not a preferred option)
-
Properly fitting a closure place in old fireplace
grahamA replied to grahamA's topic in Stoves, Fires & Fireplaces
Any tips on how best to shape it? -
I've opened up the old fire place in a pre 1900 property and planning to install a multifuel burner (already purchased) and have put a new 6" liner down. I'm in the position where i think I need to fit a closure plate in but i'm scratching my head as to how to fix / cut the plate so that it fits snug in such an uneven chimney (None of the walls are striaght or even). Also there is an old hood still insitu which i was thinking to leave as it reduces the opening but not sure how to fix the closure plate to it. I was planning on fixing the closure plate at the top of the hood and try to seal the bottom as best i can, is that a good idea? Would a cement board be easier than a steel plate?
-
Hi Markc, I do have the option to run it at joist level however i'm wondering if a lot of heat would be lost between the build up of say a 22mm ply board and then a tile backer board overlaying the pipes? By renewable heating system i mean a large multi-fuel burner with back boiler to serve the heating and hot water (we have an abundance of wood) and a heat pump back up with solar PV for when the multi-fuel burner isn't running.
-
I'm looking for some advice on what options i have for the floor build up to install a wet underfloor heating system within a shower room. Most underfloor heating within showerrooms / bathrooms seem to be associated with the electric. This isn't the solution i want to use however as I have a lot of free energy in the form of hot water because of the renewable heating system we are putting in. The shower room will be located on the 1st floor and therefore the floor build up with be over existing joists. I would like to keep the floor build up to a minimum. As we are tiling the showeroom I would ideally like a backer board we can install tiles directly onto that also accommodates 12mm/16mm UFH pipes, but can't find many options here. I would also like the shower tray former be able to accommodate UFH pipes but can't seem to find any options for this unless I rout the pipework routes myself within the former? is that even possible? Any advice on what options I have and how I should build up the floor would be much appreciated Thanks Graham
-
Thanks John. Good to know.
-
The main reason is that its going to be an open plan area joining into an exisitng slab which isn't insulated but which i want to install underfloor heating on without adding too much floor height. UFH panels across the whole floor was what i cam up with to ensure i get an even floor across the two floors. When you say 50mm eps, would that sit on top of the slab, where you would then install the UFH heating pipework in screed above?? Not sure if i'll be able to do that as the builder is planning to tamper the concrete off of the blockwork which is already at the intended height. Any thoughts on my initial question?
-
Any one see any issues with instaling 75mm PIR insulation as an upstand in terms of its ability to support a finished floor on top? This will be only in areas where we are continuing the floor build up to the outer leaf (bi-fold door opening). Other areas will be a 25mm upstand. Floor insulation will be 150mm and slab 150mm. Plan for above the the slab will be 5-10mm self leveling compound (marrying upto exisitng floor), 20mm underfloor heating panels and then 22mm floor tile.
-
Yes this is what i am experencing in. A lot of things seem to fall through the gap in the detail. The consequences of one detail affecting something else (thermal, asthestics, structural) is often overlooked by each profession. My builder just wants someone to tell him what to do so can't relay on design decisions from them.
-
Apprcieate the lengthy response, thank you! When you say bring the steel inside the insulated envelope, i totally agree but won't adding insulation between the steel / frame and on the inside head put the steel outside the envelope? I would have thought to bring it inside the envelope I would have to insulate outside of the frame over the edge of the lip and then around the top of the steel? Not sure how to acheive this though. Is using something like Maramox thermal block an option above the steel?
-
I'm concerned with regards to a steel that my SE / Architect have specified and its liklihood of causing a cold bridge. The steel sit on the inner leaf on one side and an outer leaf coloumn on the other side via a an 8mm bottom plate (and fabricated plated coloumn) to support the wall above (two storey extension). This is part of a corner glazing detail and bi-fold doors. I've kind of fallen out with my architect given the lack of details he has provided when it has come to the build therefore i don't hold out much hope getting an answer from him anytime soon, however i am trying! I have no sectional detail for this part of the build and therefore i am guessing somewhat as to what to tell my steel fabricator in terms of sizes. What options do i have to reduce or elimate this thermal bridge of the steel plate span over the cavity? I assume the bridge it will be similar to that of most catnic type lintels therefore am i making a big deal out of nothing? The large span worries me though. Should I be allowing more height in the steel coloumn section so i can install insulation / insulated plasterboard to the underside of the steel plate? Will that affect how the bi-folds / glaxzing is fixed? What about the top side of the plate / steel?
-
Why would there be mositure in there if they are installed at the same time? Its what the architect has specified and i assumed it was to stop the insulation getting damaged from the concrete pour?
-
Yeah i'm concerned about frezing over night temps this week. Its supposed to be -4 / -5 later in the week in the North West and thats the earliest we could pour. I do have access to some carpets etc to put over the top but not sure thats going to be sufficient given the weather forecast??
-
I'm not to sure thats just what the SE has specified! It does seem somewhat over kill now i've done some research. It not load bearing i don't think given the inner leaf walls will take the first floor and roo with their own footings and its just going to be used as an open plan kitchen and utility room. Kitchen is 25m2 and the utility is 12m2 (ajoining with an internal structural wall).