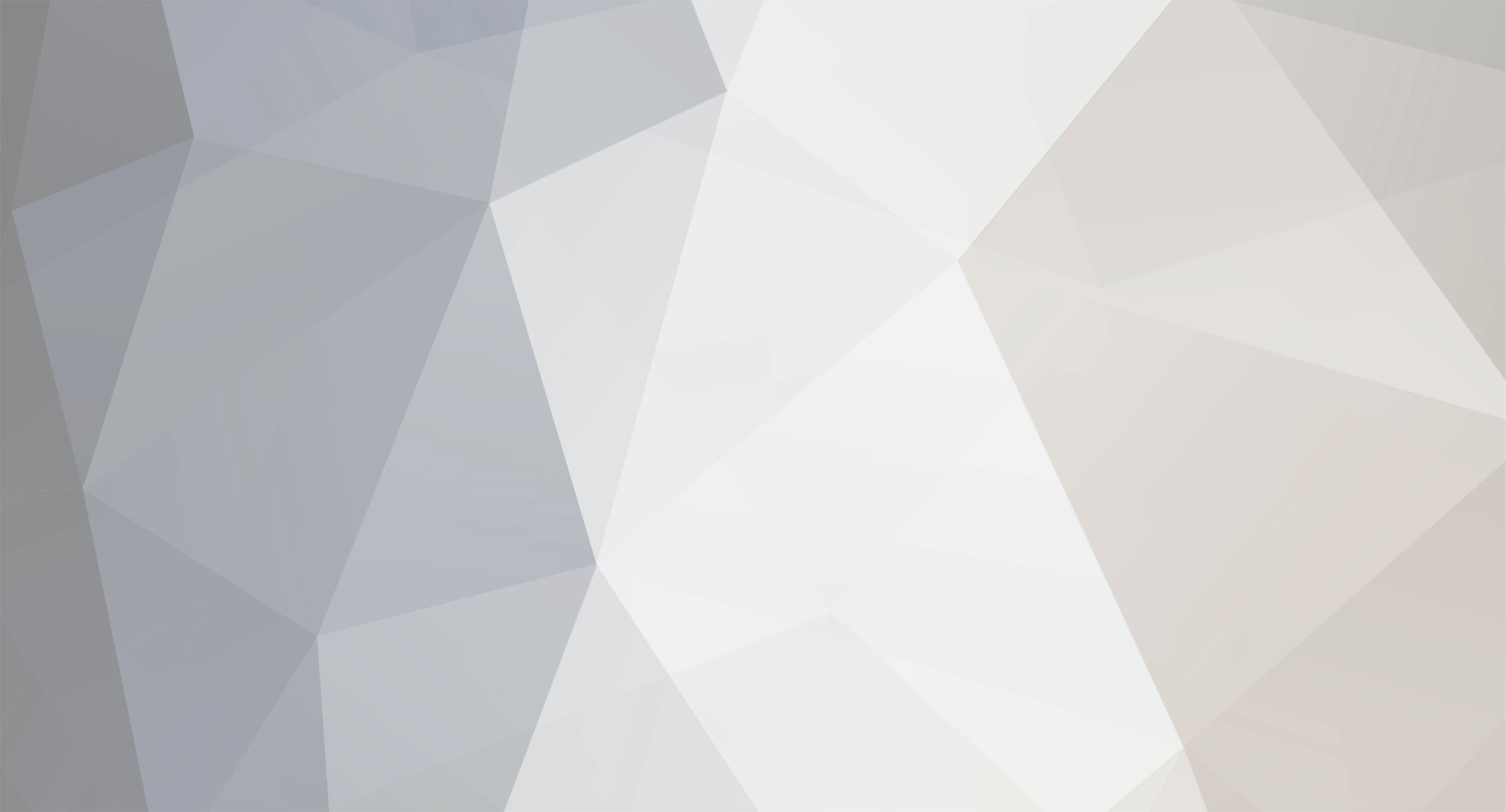
HandyAndy
Members-
Posts
14 -
Joined
-
Last visited
Personal Information
-
Location
Fife
Recent Profile Visitors
The recent visitors block is disabled and is not being shown to other users.
HandyAndy's Achievements

Member (3/5)
2
Reputation
-
ASHP: is my installer talking sense about his design?
HandyAndy replied to HandyAndy's topic in Other Heating Systems
I do mean service the heat pump, which is a requirement of the LG guarantee. -
ASHP: is my installer talking sense about his design?
HandyAndy replied to HandyAndy's topic in Other Heating Systems
A further update on this - unfortunately not a completely happy ending. While NAPIT have had some success - getting the installer to replace the thermal store with an unvented cylinder and some minor actions. However they have not been able to get the installer to remedy everything - and have also discovered similar problems with his other installations. The positive is that the system performs much better than it did. In the end, NAPIT coudl not get the installer to do all the required actions and their ultimate sanction was to remove membership if he did not comply. He has now been struck off NAPIT and MCS membership - so at least he won't give other people difficulties. The downside is that we are left to complete the actions which the installer did not deliver on. So NAPIT don't always deliver. We are now looking for someone who can service LG heat pumps (not easy to find them as information on LG's website isn't accurate). If anyone has ideas on installers in Fife (St Andrews), I'd love to hear from them... -
sorry for quality of pic - best I could do with the angles available ... the top of brown below-ground drain is essentially at finished floor level - the grey branch and pipe are above floor level.
-
Yep, there's a boss on the branch - problem is that's above the height of the shower waste! - hence the need to take an alternative route out.
-
Hi - thanks for the fast reply. There is a branch though it immediately goes into a rest bend. I don't think I can get a connector in there as the only options are the collar of the rest bend (too big), and the bend itself (too curved!) hence the approach of taking a separate shower waste out and joining outside.
-
As part of renovations, we are putting an en-suite in. The original plan was to use a single stack which would be used for basin, shower, WC. Unfortunately the subcontractors put the new drain connection too high to allow the shower to be connected to this ... As a result, the proposal is to make the shower run separately to the outside 110mm drain, where it would connect towards the top of the pipe. Apart from the shower, all connections are to an internal sub stack with AAV. For the shower, the plan is to use 45' bends for flow/ rodding purposes. I think this is OK (certainly from a technical perspective) - though before going too far would like to test people's thoughts on how this may be viewed by building control. I've tried reading building regs though didn't get too far with them ... for what it's worth, we are in Scotland though assume the principles are the same as England! Cheers ...
-
ASHP: is my installer talking sense about his design?
HandyAndy replied to HandyAndy's topic in Other Heating Systems
A long-overdue update on this in the hope it'll help others. In brief, in the previous months we've been escalating with NAPIT, the installer's professional body. To their credit, they've continued to engage and been useful. There have been a few rounds of engagement with the installer, which were unsuccessful. Ultimately, I have asked for an independent technical review (by NAPIT) of the design including the heat demand calculations and system design. They sent an assessor to us. The upshot was they upheld our concerns, and identified issues with: - assessment of heat demand - documentation (of all types including electrical certification and insurance-backed guarantee) - lack of evidence that the thermal store is appropriate ... (and if the installer can't provide this, they will expect the store to be removed and replaced with an alternative cylinder) - installation (e.g. no insulation to heat pump pipes, and not sleeving pipes through the walls) The installer continues to maintain that the issue is with us as users, that NAPIT are not independent (!) and that their system is more efficient than NAPIT realise. While they visited and did some remedial work, they have not done all actions required (there were at least 11) and NAPIT say they will apply sanctions to him if he does not fully deliver. It's all disappointing but useful to know that NAPIT are supportive and prepared to engage. We still have some way to go before it's fully resolved! -
ASHP: is my installer talking sense about his design?
HandyAndy replied to HandyAndy's topic in Other Heating Systems
All. thanks for the various replies and at least making me laugh with the comments and advice ... There are 12 radiators currently; it's a 2 storey house so not massive drop; max distance from thermal store to outlying radiator is c 18m; and flow/return to and from the heat pump ranges from 51-44 to 59-52 in the monitoring I've done in the last day when there's been no heat demand. Oh, and it's a 9kW output model ASHP. System is set to 55'C. It does appear to maintain 55'C when there is no DHW demand, though when that kicks in the store temperature drops 7-8'C. You're right, it is a Macdonald store, and has a 3m2 coil. @Temp I think it was a 24kW boiler previously; interesting re the heating capability of the ThermaV: the product fiche it came with suggests 7kW rated heat output (though I now see this is "average", however they calculate that). So at least that's slightly reassuring, though probably only tinkering at the edges ... It would be tempting just to let it lie given his stonewalling and trying to blame user error for the performance though think I'll continue with NAPIT process (who I think have been helpful so far) - and hope that escalating will mean they involve an independent technical person to mediate between us. I'll let you know how it goes if useful to forum members. -
ASHP: is my installer talking sense about his design?
HandyAndy replied to HandyAndy's topic in Other Heating Systems
Thanks for the fast replies ... @ProDave, in hindsight I should maybe have been far more inquisitive about the system and how it worked. Ho hum ... Radiators: they are new, and typically double-walled. However, I'm not convinced that they are over-sized: eg in a 20m2 room with 2 external walls, 2 600x1000 K2 radiators were proposed. They appear to have a surface temperature of 32 and 34'C - which I think is on the low side for effective heat transfer! The installer considers that the delta T temperature isn't relevant Heat loss calculation was done by the installer, though not provided to me before installation commenced. Heating was gas central heating beforehand, and I don't have accurate demand figures as we have only recently taken the house over. @JohnMo - good questions - the store is pressurised. And I meant to say that the thermal store has secondary inputs from immersion heater (including an iBoost to divert excess solar PV generation) and solar thermal. But as we know, they work beautifully in the summer, not in the winter ... when the energy demand is greatest! -
I’d like to test my experience with an ASHP installation which I’ve been unsuccessfully discussing with the installer. It’s in a 1960s 3-bed detached house in Fife which I’m in the process of improving thermally (triple glazing, better roof insulation), and extending (50m2 extra including 1 more bedroom/ bathroom; an en-suite; and bigger kitchen/dining room). The system is based on an LG Therma V ASHP (9kw), with a 200 litre thermal store. The store is used to provide both heating and hot water. New radiators have been installed throughout, which are connected using plastic pipe (15mm for main flow and return, with 10mm supplies to each radiator). The system didn’t perform particularly well during the winter, when it appeared to struggle to produce hot water and heating has been variable (some rooms are hot, others cold even with radiators on maximum). The supplier thinks I’m not using the system appropriately (and to be fair, we have learned as we’ve gone on), but he has been unable or unwilling to explain how he has designed the system to meet current and future needs. As examples: 1. Initial demand was calculated at 7250W, which I was assured would still leave 1750W capacity for the extension. But it appears that the actual output of the pump in Scotland is 7kW – so already appears to be under-powered. He tells me these figures are not relevant 2. 10mm pipes appear to go against MCS recommendations, which say they will rarely provide the output needed. A practical impact of this appears to be that the radiators furthest from the thermal store are the coldest (though he also admits that the system has not been properly balanced) 3. The installer says that the temperature drop across the radiators is irrelevant and does not need to be taken account of when sizing radiators. I’m surprised – a quick calculation using the Stelrad tool suggests it makes a big difference 4. Having one bath makes a fairly substantial drop in the TS (say 5’C). The supplier suggests this can be overcome by temporarily increasing the temperature to 60’C before a bath. Apart from the faff, I can’t see this being an efficient way to run the pump While I think these are questions he should be able to answer, I’m beginning to question whether I’m talking sense or not. I’d hugely appreciate views, and quite happy to be told I’m wrong!
-
Stumbled across this debate - v interesting. I have invested because I thought accessing a wind farm's electricity was complementary to my house's PV - will provide electricity at night, and without the cost of batteries (which I think will have a v long payback time). Also, buying into a larger development should bring economies of scale (bigger turbine, better performance). Of course, there are downsides with turbines needing more maintenance than PV, and the management overhead of Ripple. On balance though I'm prepared to take the risk and see what happens ... As I understand it, they have 3 projects (Graig Fatha - built; Kirk Hill (being built); and a third that's ramping up). I'm in the second one, so no electricity yet though I'm prepared to take the risk of someone else running the site on balance. Obviously you do have to have some faith upfront during the build process, especially as you don't get an immediate return. I'll be able to tell you if it's worked in a bit!
-
Plasterboarding over new insulation with sloping roof
HandyAndy replied to HandyAndy's topic in Plastering & Rendering
All - you're heroic - MANY thanks for the fast input ... I'd got myself into a tailspin about what to do - great to have your input to move me forward! -
Morning. I've been struggling with this for a while and not found the solution here, so posting my query. I've been insulating the previously uninsulated sloping roofs in my 1960s house, taking existing plasterboard off and adding 75mm PIR insulation between the rafters. It's already had a satisfying 3-5'C improvement in the surface temperature of the roof! I'm thinking of adding 25mm insulation underneath the rafters, followed by a VCL (+ tape) and then plasterboard finish. I'll have it all professionally skimmed once done. I'm not clear how best to finish off the join with the existing plasterboard. I've knocked up a possible cross-section in the attached photo and would welcome feedback. While I'd taper the insulation, I was planning to leave the plasterboard butt-jointed (screwed into the existing horizontal plasterboard), leaving the finer details of taping, filling and finishing to the plasterer. Does this sound like a reasonable approach - or would I just be better leaving the boarding to a plasterer who can then do the whole job from start to finish?!
-
Hi - we are renovating a 1960s house in St Andrews, taking over the family home from my father who liked it just the way it was (including original kitchen and bathrooms (complete with mint green suites!)). He was into renewable energy, so we benefit from PV electric and thermal solar, and he had replaced the original Crittall windows with double glazing. We've made some progress so far, including self-replacing end-of life/ draughty UPVC with highly efficient triple glazing (it was fun lifting 90kg windows to the first floor!). I'll also share the mixed experience of having an air source heat pump installed. Currently adding copious insulation into the large, uninsulated vaulted hall and finding a satisfying 3'C temperature rise as a result. Next piece in the jigsaw is to have an extension built, and finding that builders are like the proverbial hens teeth ... I've appreciated lurking on this site for ages and being able to draw on people's thoughts ...