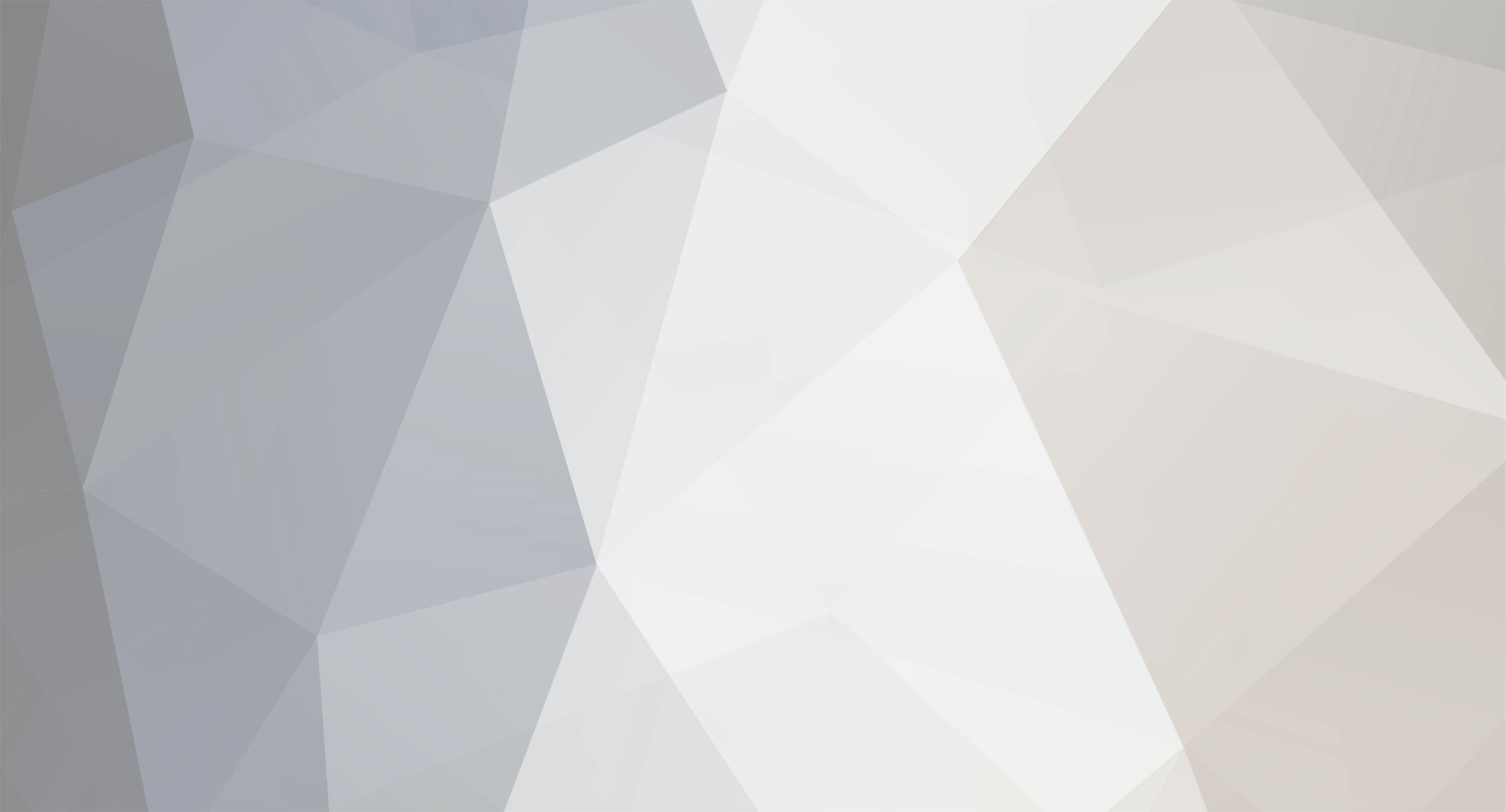
Stoph43
Members-
Posts
13 -
Joined
-
Last visited
Personal Information
-
Location
Warwickshire
Recent Profile Visitors
The recent visitors block is disabled and is not being shown to other users.
Stoph43's Achievements

Member (3/5)
0
Reputation
-
Week 4 - Out of the ground, just.
Stoph43 commented on Benpointer's blog entry in Contemporary build in north Dorset
HI Ben, great work. Its really taking shape. Can i ask what size ducting you used for each of your services? Did you place them in the footing before concrete pour or did you have to build in a block lintel type arrangement? A picture here would be ideal if possible? Cheers- 5 comments
-
- foundations
- ducts
-
(and 1 more)
Tagged with:
-
Hello Gang, we looking to get your thought / advice or any experience from anyone who has used Marmox Thermoblocks. - Where building a simple timber frame 2 story new build - Frame delivery is in a few months 140mm wall with an additional 100mm PIR inside, on concrete slab with 150mm PIR on top followed by screen - We're just finishing excavating the strip foundations and about to order the concrete. Cross section of the foundations below - Is it worth us adding a layer of Thermoblocks in between the 2 x 140mm block courses? (shown in RED arrow) Would they benefit in our situation? Would be great to hear your thoughts, Thanks
-
Thanks All, the concrete is in pretty good condition, i'll have a better idea on levels once its fully cleared out and @saveasteading i'll follow your method. @Mr Punter- levels we should be able to have room for 225 as you suggested, thanks for this. @nod- Yeah agree on the 300 mil DPC @saveasteading I automatically 'assumed' I would need a second DPM as to allow it to run above the slab and into the new internal skin block and join to the DPC. The current DPM would not have any excess to allow for the raised blockwork around the perimeter of the slab to meet the new floor level, i thought this would be a concern, hence a new DPM would need to be laid?
-
Hi team, looking for some advice: We'll be conducting a new build using the previous slab from a barn. We're taking the barn down and keeping the existing concrete slab (approx ~200m thick and pretty level for a barn) The slab currently has its own DPC. We'll be digging down around the slab to instal new foundations, but we'll be building up above the slab breaking into it in some places to add foundations for supporting walls. The thought is to build up from the current slab with new insulation, under floor heating and screed. My question is, can we simply put a new DPC on top of the existing slab, with insulation and screed on top? Will this still work and will it require any form of sand binding or similar underneath etc? Rough picture below to help explain. Thanks for your help
-
HI all, we're getting a new electricity connection and i need someone to act on our behalf to work with the national grid to support wayleave requirements. We're based in the midlands, south Leicestershire (if it matters?). Does anyone have a contact of a suitable (hopefully not too expensive) solicitor or legal representative that they've used for this manor work? It should be be fairly straight forward? I'd like to go off good recommendations and this is the ideal forum of who to use /avoid Thanks in advance
-
Class Q - Steel portal barn conversion cost estimates
Stoph43 replied to Stoph43's topic in Costing & Estimating
Really interested to hear more on your builds sound sliek you have lots of experience on different projects with this. It really depend on how the LPA feel and see it. In my area they are really against any class Q and are renowned for being difficult, so the project is really in their hands. If we get class Q ( which we tick all the boxes to say we should) then we'll apply for for planning to try and take the advise from all of you guys to knock down and start again. We really don't want anything different, the current footprint works fine, it's just a build method around the steel portal. which is really undecided still I like the idea of ICF, but it would need new foundations so full planning, just trying to look at backs options, no one has actually measured the barn yet another that the architects rough dims. part of me wants to try and add to the structure before it measured so we can squeeze som insulation and structure in as well as eth steel cladding.... it all seems like ridiculous class Q game, just to try and make the building energy efficient without losing footprint Purlins are set onto the steel portal frame (rafters?) and the fibre cement boards are fixed to the purlins (excuse me if the wording isn't correct -
Class Q - Steel portal barn conversion cost estimates
Stoph43 replied to Stoph43's topic in Costing & Estimating
@Dave Jones is this just a swooping comment or is this based on actual figures you've experienced? Thanks -
Class Q - Steel portal barn conversion cost estimates
Stoph43 replied to Stoph43's topic in Costing & Estimating
@Tosh This is EXACTLY what i was thinking, haven't been able to find any examples of this but what you've done matches my thought process. I'm guessing you've had to apply for full planning approval for this rather than a class Q? How di you finish the insides and outside of the ICF, it looks like a sensible construction method to be as you gain the thermal mass, structure and insulation without losing too much floor space which is critical in my build. Are you able to provide anymore photos. Happy to private message me if that helps. Great build!!! -
Class Q - Steel portal barn conversion cost estimates
Stoph43 replied to Stoph43's topic in Costing & Estimating
This is all really useful information thanks guys. Looks like i'm going to have to pump a lot more money into the foundations ad structure as i first thought. I will see how we get on with the pre-app and then probably take all of your advise in getting full planning as to make teh job a bit easier. To be honest we don't really want anything different, another 1000mm of roof height would be lovely but i don't want to push it. My main focus was the structure (mainly for costings and design method) and how to incorporate the steel portals within the structure to minimise the thermal bridge. SIPS on the inside of the steel uprights seems the most sensible, but it does dramatically reduce our already quite small footprint. I did wonder if i could use ICF blocks to straddle the steel uprights, but then i'd probably be in danger of going outside the overall dimensions. What has been your guys chosen build structure method? Thanks -
Class Q - Steel portal barn conversion cost estimates
Stoph43 replied to Stoph43's topic in Costing & Estimating
Mr Punter, I wasn't aware you could do this, is this a service you provide? Do you have any information on the question I have asked? Thanks -
Class Q - Steel portal barn conversion cost estimates
Stoph43 replied to Stoph43's topic in Costing & Estimating
@saveasteading, Thanks also for your reply Please see very rough image below, but you can see the roof and wall construction. Its has wooden purlins for both wall and roof, We plan to keep with steel cladding for both walls and roof (obviously insulated) build method is undecided yet as i'd really like to minimise the floor space loss but trying to work out the best solution of overcoming the cold bridge through the steel uprights, not building outside of the current floor print (class Q restriction) so still undecided. Layout is very simple also see below: What makes you think we'd need to underpin the steel uprights? i though this maybe this case, but am getting mixed opinions. Thanks again for your response -
Class Q - Steel portal barn conversion cost estimates
Stoph43 replied to Stoph43's topic in Costing & Estimating
@Tom thanks for the reply, this is very interesting and something we haven't looked hard into, as already know our local council are really tight in the class Q rules, and have been tools that getting full planning after permitted development is even trickier, but as you say it seems the most sensible solution form a build efficiency aspect and product performance out look. Out of interest how different was your build form the class Q approved building to what you actually build? foot print, height, layout etc etc, and your overall costs would also be of interest if possible Thanks again -
Class Q - Steel portal barn conversion cost estimates
Stoph43 posted a topic in Costing & Estimating
HI all, very new to the site but i've been digging through lots if really useful information in this forum. Quick question for those out there that have gone down the Class Q route, which many have already completed. I'm looking to get some early estimates for a barn conversion. Its a typical 3 bay steel frame barn, reasonable concrete floor approx 200mm thick. Barn is 10.3m wide by 13.5m long, ridge height of 4.5m, It will be mainly 1 storey, with the exception of mezzanines for the bedrooms. Would be great to get an idea on what costs you guys have spent on similar barn conversions. I have lots of other questions but we'll start here for now 😉 Thanks in advance guys