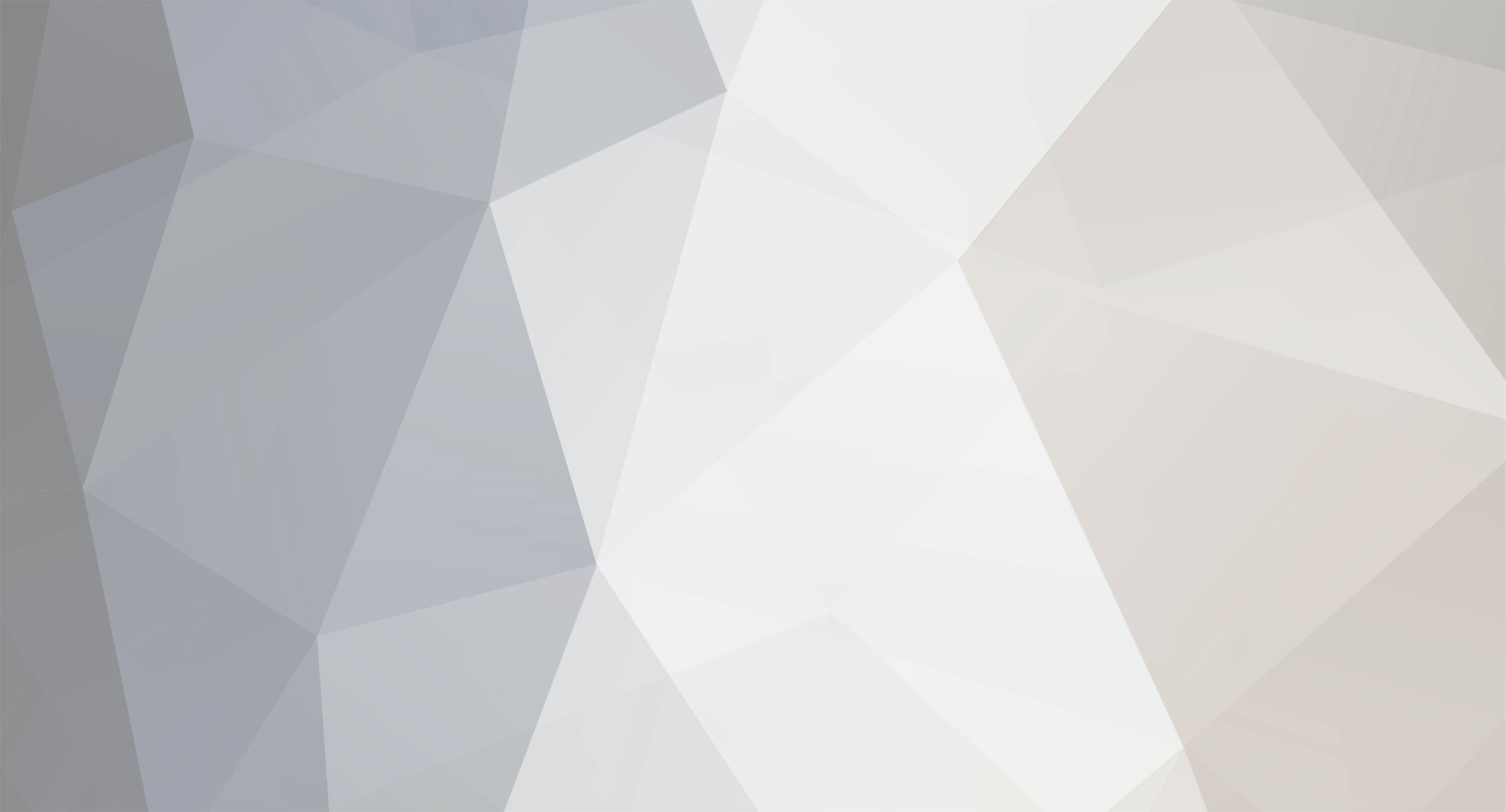
SimonC
Members-
Posts
16 -
Joined
-
Last visited
Personal Information
-
Location
Buckinghamshire
Recent Profile Visitors
751 profile views
SimonC's Achievements

Member (3/5)
3
Reputation
-
For Clayboard by Dufaylite, the honeycomb material in the former looks like a clay-cardboard material. Introducing water weakens / erodes the honeycomb leaving a void between the underlying earth and the bottom of the reinforced concrete slab (or as is being discussed, a void between the insulation mechanically fixed to the underside of the concrete slab). But I agree with you that the clay-cardboard would likely crush by any ground heave forces so why go to the bother of weakening it with water? But that is the manufacturer's installation instruction, including installing the pvc pipes (which are then later cut, capped or filled) after the one and only water pour once the concrete slab is cured. Perhaps the clay-cardboard doesn't crush in the same way that other products like Cellcore, which is a polystyrene based former.
-
Ok, thanks. The Cellcore looks different product to the Clayboard in that it seems designed to stay in situ until a ground heave event when it can be crushed. The Clayboard product on the other hand, you kind of destroy as soon as the concrete is set by flooding it with water to breakdown the former material. Just guessing, but if the ground does heave then you have the DPM holding the insulation in place, and if the boards were tightly packed or any spray foam was used to fill gaps that may assist also. But if in doubt ask your SE.
-
From what I understand, once the concrete slab is set and is supported by the piles then the heave former has done its job. For the Clayboard product you have pipes set to pour water in to erode/weaken the former in the void. A mechanical fixing would be the solution; Installed through from the underside of the insulation to be bedded into the concrete. A wire with hook bent is probably a better H&S solution than an array of inverted insulation fixing screws that would create something like a bed of nails. Next step is to check what insulation will be ok under concrete, though since the insulation wouldn't be bearing the load of the concrete - rather suspended by fixings to the underside - I expect most will be ok.
-
Not resurrecting the previous thread, but I've a question about your experience with insulation over the ground heave product. I'm in a similar situation with a concrete slab and mini piles and I want to install insulation under the slab and on top of the ground heave sheets (in my case the SE has specified 160mm Clayboard by Dufaylite) but the SE is not happy. He is concerned about supporting the insulation once the heave protection is gone and all that's left is the designed void under the slab. Did you install any mechanical fixings to tie the 300mm insulation to the slab? If not, how did you supported the insulation to stop it from collapsing? Thanks, Simon
-
Can anyone identify what this vent is for?
SimonC replied to SimonC's topic in Lofts, Dormers & Loft Conversions
Thanks all for your responses. The developer is sending an electrician around to check !? -
Can anyone identify what this vent is for?
SimonC replied to SimonC's topic in Lofts, Dormers & Loft Conversions
Thanks @ProDave -
I don't have anything solid to add. In late 2022 I contacted the working group tasked to create a pathway for the industry to provide guidelines for new spray foam insulation and to deal with surveying existing installation. At that time their work was in progress, but I am aware they have since published in March 2023 some guidance which is found from the URLs embedded within "Industry guidance" section in this government note: https://commonslibrary.parliament.uk/spray-foam-insulation-and-mortgages/. Useful to read and hope it helps.
-
My parents have moved into a newly built house and after the recent bad weather have found water has been leaking on the bathroom ceiling. In the loft, roughly above the area of leak, is this black vent on the pitched roof with dangling and seemingly unconnected pipe. The other insulated pipe is the bathroom extractor vent. It seems both vent installations are a similar product with a broadly triangular part accepting a connecting pipe above a cut out in the roofing felt. I've tried to google products but cannot find a match. I have not been to the house to investigate the loft but based on the image I am guessing the dangling pipe ought to be connected to something. I wondered if it might be a soil breather vent that has not been connected - you can just see a white pipe to the left of the image which I imagine is the soil pipe. Can any experienced eyes concur, or could it be something else? Whatever the purpose of the vent, should it have water ingress from rain in bad weather? Thanks in advance!
-
On paper I'm in a lower banded flood zone near the River Thames albeit 1/4 mile away from the river and the immediate area has never flooded. Closed cell could give a bonus in that regard but frankly I'd prefer not to test it. The walls are brick/block cavity. For the roof the main adverse issues seem to stem from SPF applied direct to roof tiles or non-breathable roofing membrane. I'm planning for a roof build up with OSB sarking boards over the roof rafters, then a vapour permeable membrane, then counter battens, tile battens and finally clay roof tiles. The SPF would be installed under the sarking OSB and between the rafters that would be much like a SIP roof panel, then an airtightness membrane, then plasterboard. When I ran this construction detail by the chap from ECON Polyurethane he saw no issues and suggested that sarking board might be unnecessary provided the membrane detail was adequate (usual caveats it was not binding advice) though I like the idea that sarking board will add strength and create an enclosed 'panel' in the warm roof.
-
I'd like to understand how to avoid structural damage - do you have experience of shrinkage or expansion in SPF and what went wrong? Are these issues solely related to closed cell and as result of poor installation, or are they a generic property of the product so will closed cell shrink over time regardless of how well it was installed? I thought I might be able to mitigate the risk of poor installation by only using an insurance backed and accredited installer from one of the main players i.e. Icynene or BASF Walltite? Do products like SIPs, which are essentially closed cell PU sandwiched between OSB, also suffer from these adverse effects?
-
I have not discounted EPS beads or cellulose at this stage; still asking questions and gathering data. Getting indicative prices for SPF is the next step. As I see it the price differential is not just reflected in the dollar amount as it includes some potentially quantifiable benefits, such as contributing to airtightness. And in present economic circumstances the payback period for either is getting shorter - if next years 75% price hike materialises without any government intervention then I'm looking down the barrel of an annual combined gas and electricity bill of over £10k. Peter ( aka @Gone West ) was kind enough to send me some information on his build and reported that he was able to achieve an airtightness of 0.47 ACH by using open cell SPF without membranes or tapes. I'm not expecting I will be able to achieve that in my 1960s renovation and extension but hope that by using a considered approach to the materials it could help to make a significant difference.
-
I have reached out to the main national players in SPF for their commentary and ended speaking direct with a very helpful chap at ECON Polyurethanes who are the BASF Walltite distributor. He reported that the industry is taking urgent action to put in place an accredited scheme for spray foam installers that will meet the needs and assurances required by lenders and insurers. An industry panel has already been setup and convened comprising representatives from lenders, insurers, manufacturers, distributors and installers. The chap I spoke with is sitting on this panel so I feel this information is reliable and the good news is the panel are aiming to deliver the scheme in Q2 next year. I got the impression that the scheme will deliver not just installation guidelines but also result in something like a certification pack containing relevant documentation/photos about the install that would create a form of provenance to stay with the property. From my perspective (yet to begin works) this is good news but I'm not clear how it will benefit existing installations. It might be that in some circumstances this could be retrospectively done where the build has been well documented and the spray foam was installed by accredited companies, though that is just my supposition.
-
Thanks, I need to read up again on the lenders and insurance issue. I thought the standing objection to SPF in the roof was primarily due to bad roof installations rather than the product. Specifically in those circumstances where SPF had been directly sprayed onto the roof membrane and/or tiles omitting a ventilation gap leading to the possibility for condensation potentially leading to rot in the roof timbers. A solution would be to include a 50mm ventilated void directly below the roof membrane - Fusion Insulation have a vent spacer to fit between the wall plate and ridge beam which provides the necessary air gap (http://www.fusioninsulation.com/thermal-insulation.html). However, the alternative approach I’m considering for the roof build up would be to install OSB sarking boards over the roof rafters, then a vapour permeable membrane, then counter battens, tile battens and finally clay roof tiles. The SPF would be installed under the sarking OSB and between the rafters that would be much like a SIP roof panel, then an airtightness membrane, then plasterboard. Of course, if there is a blanket ban on SPF from lenders and insurers then the use of SPF is a non-starter. I would be interested to hear how other forum members have overcome the matter.
-
Thanks @Iceverge - If money no object then this would be preferred, however there is a budget for the work. That being said, if the builders quotes are astronomical it would sway this point of view.
-
On paper the advertised benefits of closed cell spray foam insulation for a cavity fill appear compelling: good thermal efficiency; airtightness; vapour barrier; and strength. When used in a cavity fill I liken it to SIPs but rather than being sandwiched between OSB the insulation sandwiched between brick and block. One clear downside is price, though to my mind the price comparison is not as simple as contrasting the material price, since when correctly installed spray foam has the potential to fill the whole cavity and eliminates the burden of careful installation detail and time/labour cost of the brickie. In my renovation and extension project of a 1960s detached house I'm considering closed cell spray foam insulation to fill the existing unfilled cavity walls (around 3" cavity) and the cavity in the new extension walls (around 4"). This approach would allow for the construction of new walls with an unfilled cavity (opting to use appropriate wall ties) and then subsequently all wall cavities could filled by a specialist contractor. However, I have some concerns. First concern: If closed cell spray foam insulation is as good as it says on paper, then why is this not widely used in the UK construction industry? It seems commonplace to use spray foam insulation in USA and Canada, and if there were significant defects in the product I imagine it would have prevented continued use not to mention the litigious culture that exists over there. The manufacturers I'm considering (Icynene, Isothane, BASF Walltite, Swis Synthesia) have various certifications (BBA, Kiwa, NSAI) for their respective products. I have also read a few members on this forum who have indicated they used it in their projects and I would be very interested to hear of any direct experience - good or bad - with closed cell spray foam insulation being used as cavity fill retrofit or for new build. Second concern: Breathability of the building. The popular criticisms levied at closed cell insulation seem to target increased risk of mould, condensation and rot - though I think these are primarily issues from bad roof installations rather than cavity fills. In my project, if the building's wall cavities were filled with closed cell insulation (and potentially the roof as well to create a thermal envelope - the roof is to be replaced as part of a loft conversion in the scope of works giving some control over the design of the new roof construction), plus having a desire to adopt an airtightness strategy to reduce uncontrolled airflow, then there is a clear need for controlled mechanical ventilation. This mandates an appropriately designed MVHR system - and to that end I've been chatting with Patrick at Heat, Space and Light who has provided a proposal for a Zehnder MVHR system. My concern is will MVHR be sufficient to mitigate the potential adverse issues? It is rarely clear from critical commentary whether there was an appropriate ventilation strategy in place which caused the mould, condensation, or rot linked to the spray foam insulation or indeed whether the installation was performed correctly. The suppliers I have spoken with so far assure this is not an issue, though theirs is perhaps a bias view. I would be grateful of your experience of using closed cell spray foam insulation in the cavity walls, or in the roof. Any lessons learned or construction advice. Thanks in advance.