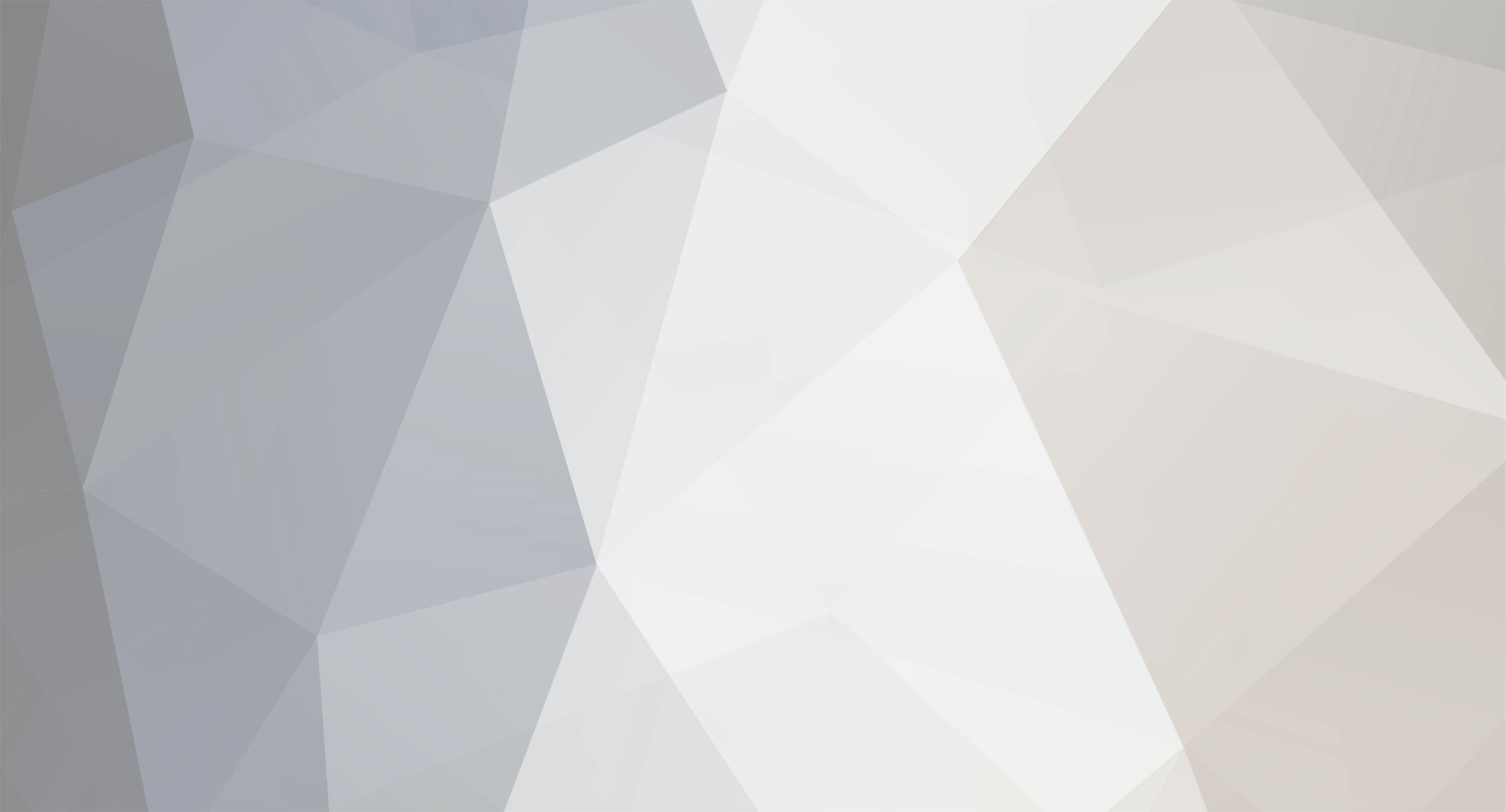
willraymond
Members-
Posts
12 -
Joined
-
Last visited
Recent Profile Visitors
The recent visitors block is disabled and is not being shown to other users.
willraymond's Achievements

Member (3/5)
2
Reputation
-
Mould on skirting boards but only in 1 room
willraymond replied to willraymond's topic in Damp & DPCs
Ground level is actually well below finished level as the landscaping has come to a halt for the moment. I have got a damp meter but haven’t probed anywhere yet. Will give that a go -
Mould on skirting boards but only in 1 room
willraymond replied to willraymond's topic in Damp & DPCs
In the attached images the room concerned is the “bedroom”, the wall with the worst mould is on the wall between the bedroom and the shop. Cavity wall with full fill 100mm dritherm 32 made up of thermalite blocks. It is a self build managed by myself -
I have a new build property with a particularly puzzling problem only in 1 room. I have mould along the base of the skirting boards of 3 of the 4 walls, all similar to the picture attached. It’s been a bit of a problematic room, there was small patches of mould on the plaster before mist coating even after the plaster was 4/5 weeks old, I had plenty of ventilation during this drying time. This mould then showed through the mist coat after a while. I probably left the mist coat 2/3 weeks before top coating with vinyl Matt, no mould has shown since on the walls but now this is showing up on the skirting. I have wiped off once already and the (small) dehumidifier has been running for a few weeks, being emptied whenever full. I have another room and a hallway which the skirtings are still to be decorated and they do not exhibit the same issues. Could it be water in the cavity coming through? We weren’t roofed and watertight til mid January and it was very wet pre-roof, the cavities weren’t covered during the build (my fault for not checking up on the contractor) or could it be something else entirely?
-
Unfortunately that photo was from a while ago and has since been fully slated, guttering on and the scaffold has been dropped. there is an open eaves detail that I need to sort out so no soffits but was fully aware I needed to pack rockwool into the space above the cavity while maintaining the air gap. Annoyingly the roofers didn’t use the eaves vent tray as shown above but did fit over fascia vents, which do nothing as they only vent the space up to the first batten and not into the roof space. So the only ventilation the roof will have is under the eaves. It will (eventually) be clad in timber weatherboarding so planning on putting a 25-50mm slot at the top and putting some mesh over to stop insects/birds. My first new build project so this is all new to me and assumed that all the trades would do things the proper way. But that’s definitely not turned out to be the case already
-
Unfortunately we were already beyond that point. We were restricted to a 6m ridge height so a warm roof would have reduced our already fairly restricted ceiling heights although I was pushing for it in the design stages. The higher ceiling heights won the argument in exchange for this headache now! also just checked the truss drawings, underside of tie to ridge is 915mm so slightly more than I estimated
-
Evening everyone, My architect has specified 450mm rockwool insulation in my raised tie trusses, the sloping section of the ceiling has 120mm PIR between (147mm thickness timbers) and 45mm PIR over the top. I did look at the comparison of PIR between the flat timbers and below but just couldnt get the same U value out of PIR vs the rockwool. However I cannot understand how to insulate quite a small area that certainly cant be crawled through. I havent got the exact measurements to hand but from the bottom of the rafter to the ridge is no more than 600mm so its almost a full fill with 450mm in there. Going to have to be very careful to not let the rockwool touch the underside of the membrane.
-
Good morning, Been given a quote by a plumber who I’ve got on with throughout the early stages of our build and like the look of his work on instagram however… I’ve just been given a quote which is roughly in the ball park however when I asked for a breakdown of the quote he says he doesn’t supply broken down quotes. Is that normal? I’ve got mixed feelings now
-
To answer the original post, I went for a factory tour, checked companies house & did a credit check on Experian (even now it shows 75 out of 100, below average risk) but I think this is only based on the last companies house figures rather than a proper in depth credit check like you can have on an individual. Regarding escrow - unless the whole amount stays in that escrow account until you have the product (which would cause cashflow issues for the company) then I would assume the same problem would occur? Or would they withdraw from the escrow in line with their payment stages. I can now see the attraction of a traditional masonry build as there is never a massive outlay and what outlays there are you should soon see on site as physical bricks and mortar.
-
Following on from this I spoke to the joinery that’s making our windows and he said they keep everyone’s deposits safeguarded for their own job but had been considering a deposit insurance scheme which would come at an extra cost to the client but would protect it in the event of this situation. In some slightly positive news I have gathered quite a few willing (and skilful) volunteers for a works party over a weekend soon to get the house built in blockwork. It was mainly all timber clad so blockwork won’t cause a planning issue thankfully
-
yours was a post I read through on my research before pushing the button on Flight. I originally got a quote in Feb and accepted the quote in June and all was rosy until last week when emails went very quiet and then today finding this out. My price from Feb to requote in June went up 10% but the payment schedule reassured me that I was relatively safe as I made the material payment a while ago. going to get prices for block construction and see if we can make anything of the little money we have left. I’m not expecting a penny back from them so anything would be a bonus.
-
Yep I saw that whilst browsing companies house earlier. Seems strange. I wonder what this mystery investment was and why they couldn’t have cashed that in to keep their business going. Also rather annoyingly my install was meant to be 2/3 weeks ago but I pushed it back due to groundwork’s delays but there’s no point in dwelling on that.
-
Anyone else been stung? Paid 90% with installation meant to start in a few weeks time and have just found out they went into liquidation yesterday. Been to the yard and there is barely a thing there. So despite one of my payments being entitled "Materials" and another "Manufacture" they have neither got my materials nor have they manufactured anything of my house. Anyone else been in a similar position? The more I speak to other trades and my architect the web of people they have let down is getting ever larger. The liquidator has informed me it'll be a week or more to get letters to all the creditors and then maybe a month or more before they know if there are any assets to liquidate. Feeling more than a little disappointed and have no recourse against them. More than that I now have foundations for a house I cannot afford to build.