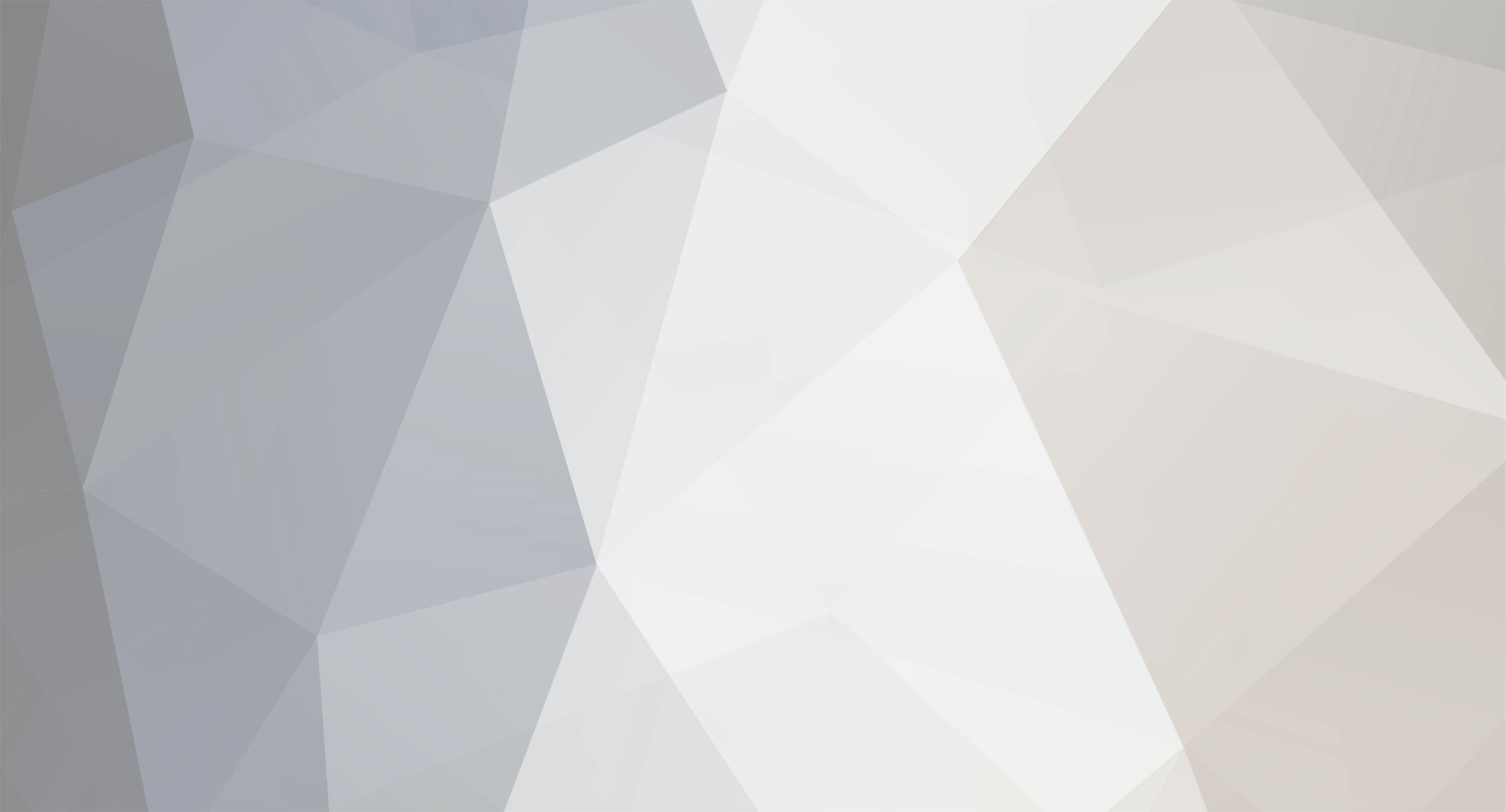
low_and_there
Members-
Posts
81 -
Joined
-
Last visited
Personal Information
-
Location
Brighton
Recent Profile Visitors
The recent visitors block is disabled and is not being shown to other users.
low_and_there's Achievements

Member (3/5)
1
Reputation
-
Hi folks, looking for some possible solutions for a slightly unfortunate waste pipe positioning. Basically, It's at about 80cm about the ground (where the WM is placed), and the plumber who installed it said he'd put a spigot on the end for the WM to empty to. There is no possibility to change that particular positioning. I thought they needed a standpipe but he assured me that a spigot was fine. That plumber is no longer around but the new one has said he thinks using a spigot risks backfilling and smells entering the WM and suggests putting a standpipe on the end with a trap. But the standpipe could only be 200mm - otherwise there's a risk that the WM may not be able to pump enough out (as it would be too high). I've drawn a picture of the layout of the pipes - there's air admitted to the pipework about 1m ish away (not sure what it's called but it's something that allows overflow from the heating system) from the entry from the WM and there's an AAV a couple more metres away - would this provide enough air in to prevent backfilling and smells or do you think the new plumber is right and better to risk a short standpipe? I'm worried that a short standpipe may result in flooding... Thanks in advance
-
Which way does the fan on your ASHP face?
low_and_there replied to low_and_there's topic in Air Source Heat Pumps (ASHP)
thanks both, at least they did that bit right -
We've finally had our ASHP installed. Total nightmare, turned out the installers really did not know what they were doing with the heat loss calcs, nor tbh, much about heat pumps, despite being an 'MCS' outfit. But anyway, here we are. Due to the various sagas since install I've not actually noticed before that the ASHP unit outside pushes air out towards the garden, rather than against the wall, which is what I expected... I've drawn a diagram, attached, showing what I mean. I'm curious if this is to be expected and how other people have their heat pumps installed? Thanks in advance
-
16mm Manifold with some loops running 12mm pipes?
low_and_there posted a topic in Underfloor Heating
We've had an in-slab UFH system installed in the new kitchen but for the rest of the ground floor we're going with an overlay system - the slab pipes are 16mm but I was hoping to use 12mm for the overlay (with tighter pipe centres). Anyone know if it's possible to use the same manifold with a reducer for the 12mm loops or is that a dumb idea / won't work? Thanks! -
How would you finish this parapet on edge of an EPDM flat roof?
low_and_there replied to low_and_there's topic in Flat Roofs
Yes, agree - the EPDM is the waterproofing layer. The Capping isn't. The section drawing shows the EPDM doing just that - lapping over completely - or am I missing something in your comment? Yes, the cladding will go higher than shown in the diagram to avoid seeing the gap. Thanks -
Looking for suggestions on both the most sensible/practical and aesthetic way to finish the parapet on our new extension. I've attached a sectional drawing. The flat roof is to be finished in EPDM as shown in the red line on the illustration. I had initially thought I'd use a GRP trim on the left but someone suggested an aluminium coping could look nicer (although it's about 4x the cost!). Any opinions on these two options or others would be welcomed
-
A question about adequate support for plasterboard... this is very noddy. I've read the NHBC guidance but looking for practical experience of what is really necessary: I'm about to line a new ceiling in dormer. Joists are at 400 centres and had planned to use 12.5mm Plasterboard. The span is around 3.8 x 2.7m. There's one set of noggins between the joists in the middle of the longer span, per SE's spec, but there are no noggins at either end of joists. However, having read the NHBC guidance it seems that for anything less than a 19mm board, there should be perimeter support for plasterboard. I take this to mean that all edges should be supported (like when laying SE Ply or OSB on a floor), not just the actual perimeter of the room. Have I understood this correctly? In the videos I've watched of people installing pb on a ceiling, it doesn't seem to be supported on all edges - only the room perimeter. In some videos from Australia, some folks appear to use 'back boards' to support joints. On site do people really install noggins at all perimeter points for plasterboard or is it often the case that they are supported along the joists and at the edge of the room (i.e. not around all edges of the boards)? NHBC reference: https://nhbc-standards.co.uk/9-finishes/9-2-wall-and-ceiling-finishes/9-2-4-dry-lining/ Thanks! *I'm not planning to skim the boards - just joint compound, prime and paint. In case that makes any difference.
-
@JohnMo under the floor isn't the only way, no - I had at some point got to that conclusion but now you ask I am actually not 100% sure that I recall why that was. It could just as well go through the external wall and in. Given what @IanR has pointed out about needing a very deep trench in order to come up vertically, perhaps that is altogether better...? To your questions JohnMo, the outside unit is going to be placed 3m from the external wall but in total about 9m (as the crow flies) to the hot water cylinder. If it comes in through the external wall it would probably need 5m outside and then about 3m along the wall inside.
-
Looking for a bit of help: We're about to install an insulated raft foundation (300mm of EPS with a 100mm concrete slab on top) and have planned for all the pipework under the insulation excepting the future route for the ASHP pipes and electricity supply to it... I was planning on putting in a route for pipes to be inserted through later on when the ASHP gets installed but have failed to get very far with an installer - is there a reasonably safe size of ducting I could use to enable future insulated pipes from the outside ASHP to be routed through under the slab and into the thermal envelope of the house? For the electrics I am just going to put in a big pipe with rodding access for cabling to be pulled through in the future. Am self-managing our renovation and like most renos it's not gone to plan or budget and all my planned dependencies have been turned upside down. thanks in advance
-
Blocks suitable to leave unrendered?
low_and_there replied to low_and_there's topic in Brick & Block
thanks very much @Mike and @ETC - "Architectural Masonry" is a keyword I was lacking in my searches. Much appreciated -
Hello all. I am looking for a conc block that we can leave unfinished as it's for a wall that we can't get to the outside of to render. BC have said such 'fair faced' external-grade blocks exist but i can't find any from searches online - I have called a couple of manufacturers who have confirmed they don't make them but also believe such products do exist. Anyone familiar with particular conc blocks that meet this criteria? Thanks
-
Good point about the blocks not being cracked. Will inspect! Yes forgot to call out that there will be a VCL on the inside of the PIR. Fire-rated pb is stipulated by BC. Yes the gap is tiny, hence the proposal to use a tanking solution to reflect that it is going to be impossible to guarantee it won't get stuff in it. It's not perfect. I don't think anything in this situation is perfect. It's not been suggested by the Builder but rather building control have indicated they've seen this used in similar situations successfully. Other suggestions welcome but anything involving leaving a bigger gap is not an option.
-
This sounds interesting - is this a 'method'? The bricklayer has said he'll do his best and also try to keep the gap clear of mortar but he was keen to flag that it won't be perfect - if there's a method he's perhaps not heard of for making the joints better then that would be interesting! Thanks @Redbeard
-
Hi folks, looking for help on a couple of questions re a new external wall we're building in the extension. For context, the wall is being built within cms of another wall so we can't render externally. Have been advised to apply a tanking slurry to the inside (a bit like you would in a basement) to acheive weatherproofing. Two questions: 1) In this context, is it worth using thermally broken wall ties or is the fact that the tie will be on a Timber stud effectively act as a thermal break? Looking to achieve a high thermal performance. 2) Is it safe to put the PIR straight onto the coated blockwork or should we leave a void? If so, how many mm for that void? Thanks! --- Proposed fabric build up from outside to in: External air (50mm max) Dense fairfaced conc block (100mm) Coated with a tanking slurry PIR - 125mm Timber studs 47mm filled with 25mm PIR lined with fireproof board plaster finish