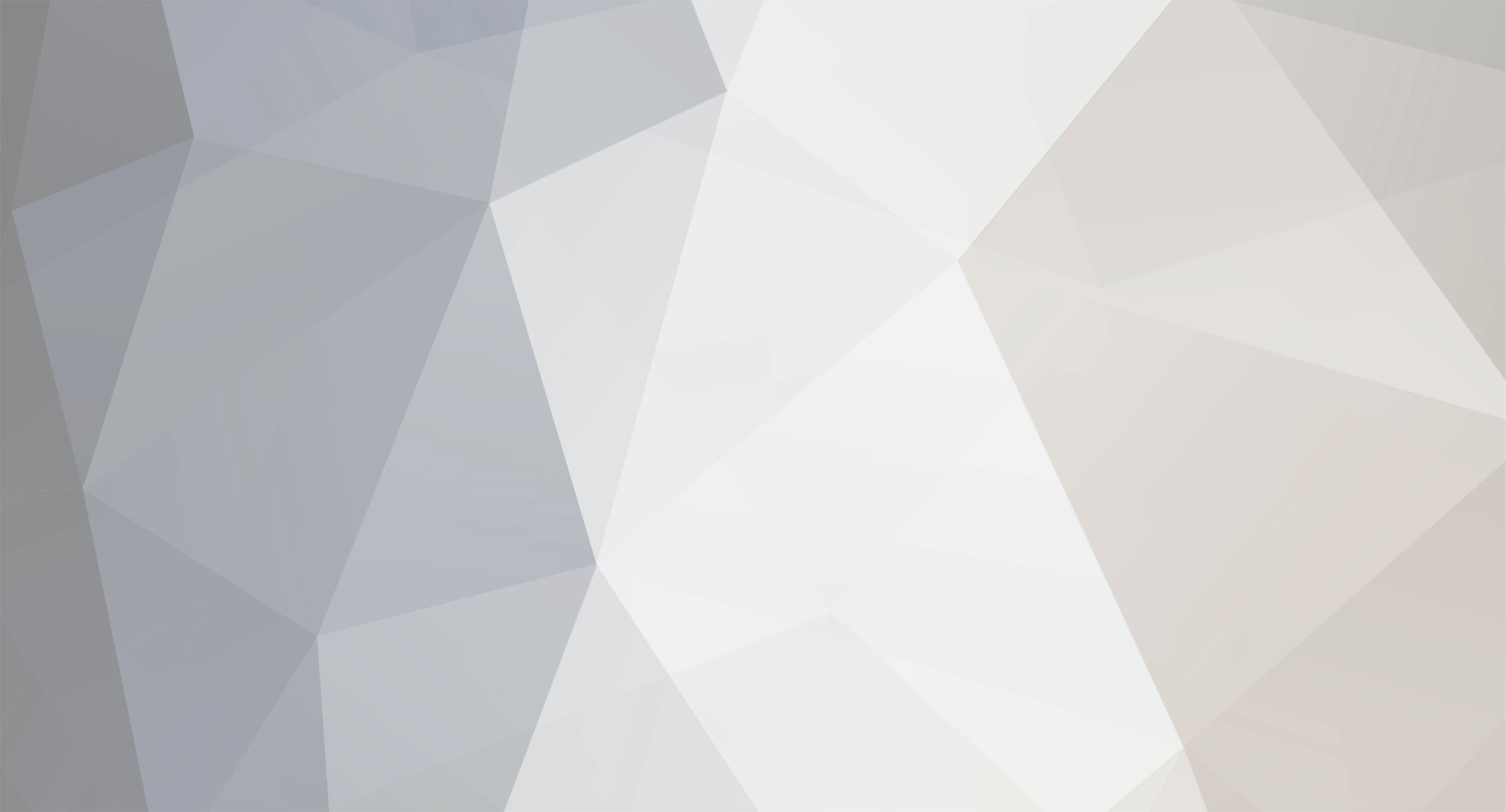
HHHAMSTA
Members-
Posts
10 -
Joined
-
Last visited
Recent Profile Visitors
The recent visitors block is disabled and is not being shown to other users.
HHHAMSTA's Achievements

Member (3/5)
0
Reputation
-
Warm Roof Overhang & Fascia Detail For Rendered Wall
HHHAMSTA replied to HHHAMSTA's topic in Flat Roofs
Hi Smurf, sorry, very delayed, didn't see your post. What solution did you go for in the end? The general consensus I received from a couple of builders was "was stuff some PIR tight in the gap and seal." -
Hi All, Hopefully a quick one please, wasn't sure what section to put this into. I drilled a brick to run three 22mm pipes from my internal garage into the upstairs bedroom floor void though the brick became loose as had no support from where I had previously knocked through the bedroom above. The internal garage is new, unheated (except for housing the boiler) and will be plastered, so keen ensure good levels of air tightness are kept and the bedroom above well insulated. I still need to run the pipework through though looking for suggestions how best I can repair the hole please either before or after running the pipework. What materials should I use, do I need to consider vapour control at all during the making good? Hopefully it's simple but I'm scratching my head! Many Thanks
-
Hi All My "roofer", after being recommended by a friend, did a pretty shoddy job all round, I won't go into all the details, but ultimate it doesn't leak which is one thing. I'm doing the internal finishes myself though noticed the VCL's don't run internally under the upstand or all the way up the outside of the upstand (both of which seem to be available details on the web). In places these don't cover the entirety of the insulation. The skylight frame is insulated. I'd like to insulate the upstands as the roof line at the lower end is very close to the top of the upstand. I've checked the forums for similar queries though no concrete advice. Obviously taking the roof up and relaying is out the question. I plan to tape over any visible insulation gaps, connecting the VCL to the upstand. If I then PIR the upstand, how to then finish with a vapour barrier. Will foil taping the PIR in place from front and taping over any gaps accessible from the ceiling suffice, or should I extend the VCL further up the inside of the rooflight frame? Any other considerations please? Thanks in advance to anyone taking time out of their day to help a man in need!
-
Medium Concrete Block Shrinkage
HHHAMSTA replied to HHHAMSTA's topic in General Self Build & DIY Discussion
Thanks Mike, think I'll just run with it and be prepared for some making good now and again, or some well placed cupboards -
Hi All, Just need some advise please, the blockwork for my extension went up back end of last year when we had rain pretty much every day through October, so the blocks got wet. I've now got many cracks in the mortar vertically, some step in places, some go horizontal and some split blocks vertically. Most are hairline, a couple slightly wider about 1mm. They're around every window, and on every wall, in some places only 2-3m apart. The long wall of the house, 13m, has brickwork on the outside skin (blockwork inside) and doesn't have any cracks in the external brickwork but cracks on the internal blockwork. The other walls with blockwork internally and externally have cracks in both skins. No cracks go below damp course, none are wider at the top, they're all pretty consistent. My understanding is the cracks are very likely to be from materials shrinkage which would make sense given the weather when the blockwork was completed. I was hoping to wet plaster the walls and the external blockwork will be rendered. I read thermal movement cracks shouldn't necessarily be filled as can stop the house returning to the original state which then leads to larger cracks over time, though if this is likely shrinkage (thoughts?), I don't believe I'm likely to see any further movement anyway. Would obviously like to avoid having to scrape out the mortar and/or replacing blocks if unnecessary. In summary: * Does this sound like normal shrinkage? * Assuming shrinkage, will plastering straight over the cracks lead to cracking of the plaster in the future? * Would future cracking in the plaster be reduced if the cracked mortar was scraped and filled, the cracked blocks were replaced or silicone simply be run in the cracks? * Would dot and dab be a better plaster solution or do the board joins just crack if the walls move anyway? Thanks in advance for any support!
-
Warm Roof Overhang & Fascia Detail For Rendered Wall
HHHAMSTA replied to HHHAMSTA's topic in Flat Roofs
Thanks Temp, the batten just made it up to a standard 400 fascia but yes, looking now cutting the joists lower would also work. -
Warm Roof Overhang & Fascia Detail For Rendered Wall
HHHAMSTA replied to HHHAMSTA's topic in Flat Roofs
Thanks for the comprehensive reply Gus and others. "I'm not shitting you.. a lot of modern joiners just can't do this simple stuff... they work with battery powered tools that have no poke.. they will faint if you ask them to cut a check they way you have detailed cut along the grain..." I did a 15 degree mono pitch roof at the front of my house including a set back porch with overhanging soffit, it took a bit of calculation to get everything right and ensure the flow of water into the gutters at the eaves, due to the low pitch, but it worked. New blade in the saw sliced through the 7x2's down grain as had to cut the ceiling joists to match the roof line. I'd be very surprised if a chippie couldn't do this, they do much more complex cuts. I can square it off though thought this is better structurally. If time is spent on detailing a correct design, certainly in my industry, the rest of the project runs much smoother, and it shouldn't matter who picks up the work as they can follow the design which has been validated and provided. Obviously things come up during construction which might need adjusting or people have their own way of doing things though the designs should be followed unless there is genuine reason not to. I would like to think tradesman cut corners only when they don't quite understand what they are doing or doing something for the first time, else why else would anyone do something incorrect. Self builders often have more time to study and understand how to do things correctly. Proper detailing and planning will always reduce risk at the construction phase. "Next scab on some 95 x 45 C16 timbers at 1200mm centres say to every third rafter. Now you have less repeating bridges, rather than every rafter they are only one in three" I ran the rafters through for additional strengthening to support any access to the roof, as you mention. The cut section is still 125x47 so would provide suitable support for a person to walk on the roof. Span table states a 125 x 47 is good for 2.4m at 400 centres and I understand projections should be no more than 1/3 of the rafter length so at only 450mm this is well below this. Would reducing to one in three, therefore at 1200 centres, impact the structural element too much? Is your thinking for the 4x2 bolted to the 9x2 to reduce cold bridging or to avoid a "complex" cut? The 4x2 would need to extend well beyond the UB internally to be properly bolted to the 9x2, at least two times the projection(?), so would this actually reduce cold bridging? Or is it improved as the 4x2 would be high in the ceiling void and not supporting the plasterboard? When thinking about the cold bridging element I compared it to a standard pitched roof at the eaves where there is very little insulation or space between the roof (tiles), the rafters and the internal plasterboard. "To the ends of the scabbed timbers attach a runner timber behind the fascia, make it straight and that gives you a continuous piece of timber to fix the gutter brackets to.. a get out of jail free card when you come to fix the gutter and fascia" The gutters won't be be fixed to the fascia due to the gulley and hidden down pipe. Can you elaborate why the WBP Ply is better than the OSB3 please as I have seen a lot prefer OSB3? Iteration of details below adjusted to some of the suggestions so far. One with continuous joist and one with additional 4x2 rafter for projection. I welcome any additional input please! -
Just to continue this thread, does it not matter water can get behind the DPM at the door opening (as it's a garage) or does this need to be considered? Appreciate the door is on the internal side of the reveal and likely also covered by the soffit at the eaves.
-
Hi All, Like others, I have searched high and wide for information before posting on here though I'm looking for validation on a couple of roof details please, hopefully these can help others also if correct as I was struggling to find the information myself. We're having a roughly 9 x 4m extension on the rear of the house, warm flat roof with a few roof lights and 450mm overhang. I was looking for a detail which allowed for a reduced height of the fascia, to avoid the store front look, which also kept everything level when viewed from the garden. I understand the joists running through can be a possible cold bridge though this isn't any different to the eaves on a shallow pitch roof so I don't see any issues here. I've attached details for the overhang and also the side fascia's. One side wall will be rendered and the other brick, though ultimately the same. Above checking there are no glaring errors, can you confirm please: 1) VCL is in the correct position. Wondered if the cavity insulation needs to be considered though not seen it as a requirement on any details, just the roof deck. 2) The soffit is fine unvented. 3) I'm showing additional cavity batts at the eaves to help reduce cold bridging. Good or bad? 3) For the side fascia detail, we will be rendering so thought it would be better to have a soffit for something to render up to. Can the soffit width be reduced to say 20mm and/or just render up to the inside face of the fascia, or is a soffit preferred? Thanks in advance for any responses.
-
Hi All, i'm looking to build a 3m x 8m garden room and maximise the available height. My garden is raised at the back where the garden room will be going so I'd like to set the building into the raised section which is about 350mm higher at the back compared to the front of where the building will be. I was looking to build with cavity blockwork which would have been easy to build up the retaining wall and waterproof though now considering a timber frame. Looking for some advise please how best to connect a timber frame to a retaining dwarf wall and what that make up might look like. I'm assuming the dwarf wall would need to be block/brick to DPC and then the frame on top though i'm not sure how best to fix the frame to the wall and if the wall would still need to be a cavity to ensure waterproofing, obviously this would add additional depth to that wall. Any advice appreciated, thanks.