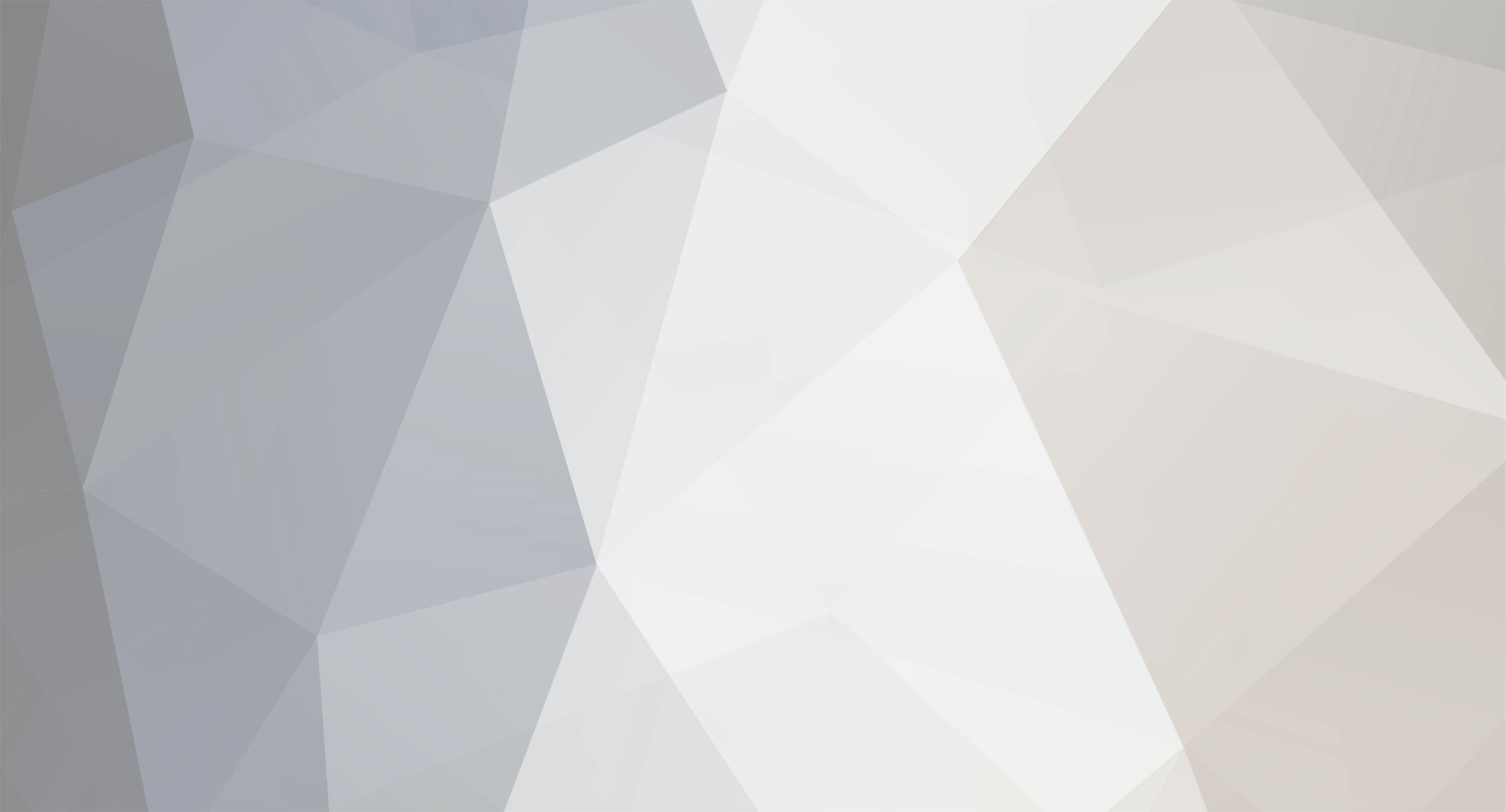
Boyblue
Members-
Posts
51 -
Joined
-
Last visited
Everything posted by Boyblue
-
1. Because we've torn down every available hill on our island to fill in slab foundations and according to one of the two suppliers left, we will run out in 5 years. 2. A lot of the remaining land is is low lying areas where even more fill will be needed than normal which will likely accelerate that eventuality. 3. Occaisionally fill is hard to get and having an alternative is prudent, especially if you're trying to fill a housing shortage. 4. As fill becomes scarcer the price will increase. It has already gotten to a price where larger projects have begun barging in fill from nearby islands. 5. It’s really about sustainability vs convention. There is a point where sustainable methods become more efficient than conventional methods and I believe we’re approaching that point. Born in the 60's I have a good sense of how many minutes I must have in a cellular calling plan, however I don't have a clue of how much data I need. It's the same with building materials and technology. I have a good sense of what size a conventional steel reinforced column should be for a given situation however I'm not familiar with lintel beams reinforced with pretensioned wires. I was just hoping someone here has the experiance. 1. With the use of pretensioned reinforcement for undergirding, along with beam and block, 20 - 35% less steel & concrete is needed, but with a higher cost of production, you could be right, the savings could be marginal. 2. However, there would be significant savings on fill. For example, for a 140 m2 home there would be a $3,500 savings on the needed 200yds of compacted fill for a standard 3 course installation. 3. The amount of labour needed is close, but there is an inverse requirement for skilled/unskilled labor. With the need for more unskilled labor and less skilled labor, there is a net saving with standard beam & block installation (1 meter floor height or less) and significantly more as height increases. 4. Although not a direct cost savings, there is about as week savings in time, for the aforementioned 140 m2 home.
-
All of the videos I've watched shows intermediate walls used to shorten beam spans with beam & block floors. If you were building on limestone as we do, would piers and beams be a cost effective alternative or would you suggest block walls (we don't use brick)? When using pretensioned lintel beams 150mm x 200mm, how spread out would you suggest the piers be, to give solid support? Is 3 meters too much?
-
So, specifications given on the company websites are for a fixed set of variables. Once one variable changes (like requesting a 50mm screed), everithing else does? Once a specific order is made and 50mm screed is requested, the appropriate configeration will be detailed?
-
Some B&B manufacturers specify 65mm and others 50mm. The beam sizes are similar if not identical, so what is the unseen, that causes the difference in specified toppings. Might it be the number or placement of reinforcement wires, the strength of the concrete, the shape of the beams?
-
The answer did come to me though. The genius of what I call the UK system, is the flexibility of being able to use the narrow side to basically double the strength of a section of floor. You also have the wide beam which aids in flexibility. And besides unless you'd be applying a cementitious plaster, you could be asking for trouble skimming all those different surfaces, because monolithic above doesn't mean monolithic below.
-
The hollow flush blocks seem to tick a lot of boxes. It has the density and strength, eliminates the need for slip bricks, and it leaves you with a flush ceiling. So what am I missing here? The only disadvantage I see is that the profile looks like it will take significantly more screed, but the offset of a flush ceiling seems like a fair tradeoff presuming you're able to apply plaster .
-
Can 100mm block walls be built on top of beam and block
Boyblue replied to Boyblue's topic in Floor Structures
Room arrangement is the issue I've just landed on. The house plans here have only 215mm walls coming up from the foundation, which covers in most single story cases, only exterior walls and bathroom walls. So, there's not the labyrinth of rooms that work so well for you guys. It's either use long spans and install with a crane or add supports and make the job manageable by hand. I beleive the former would be playing at the extreme end of the of the span charts and the latter, would be in the comfort range. -
Yea shipping assembled stuff like that is a nonstarter especially when it's already pricy in its own market. Glulam has been around or years and the amazing things I see them do with it is impressive, but you’re never going to see that stuff here in everyday construction. Shucks, Insulation is available but because it’s so bulky, it’s priced beyond standard construction.
-
LOL, I spend about 10% of my time in the sun, havenbeen on the beach in 40 years even though I drive by it every day. If you lived here you'd grow weary of it as well. I always tell folks, having sunshine all the time is a blessing, but so is having our seasons. O course you're welcome if I ever turn this discovery into something.
-
70 million Brittons can't be wrong, (not to mention India and several African Countries) The more I research the more I like it. Sort o like the metric system, it just makes sense. Our good buddies to the north can be wrong every now and then 🙂 In terms of the extras, I get your point. I'd have to over order everything because a short on an item like that bracket could hold production up for days, possibly weeks.
-
Can 100mm block walls be built on top of beam and block
Boyblue replied to Boyblue's topic in Floor Structures
You precher, me chior 🙂 totally agree -
Can 100mm block walls be built on top of beam and block
Boyblue replied to Boyblue's topic in Floor Structures
Will do & I for sure can espouse some crazy ideas so I get where you're coming from. -
Can 100mm block walls be built on top of beam and block
Boyblue replied to Boyblue's topic in Floor Structures
Just checked with a buddy that builds a lot of homes and he said 215mm blocks are supported from the foundation but not 100mm. There's no building, just absorbing all of this info before I proceed in a particular direction. The blocks do carry a lot of weight, especially with scratch, brown and finish coats like we do, on both sides, however B&B has options that can handle cars so I can't imagine it's impossible, but probably not cost effective. -
Can 100mm block walls be built on top of beam and block
Boyblue replied to Boyblue's topic in Floor Structures
My qusetions are all conceptual, you're so right but apparently Bahamians have a love affair with concrete blocks, even low cost homes spec blocks. Funny thing is nicer homes do use wood and metal studs. -
I know that walls can be ran parrellel with double beams handling the load but what about if the wall is running parpendicular to the floor beams? Need there be any special provision for standard, 100mm concrete blocks?
-
Have you ever applied a 25mm screed on top of beam and block?
Boyblue replied to Boyblue's topic in Floor Structures
When it's 85°F outside, the crawl space might be 65-70°F. Winter temperatures in crawl spaces are generally warmer than the outside air due to ground insulation. For us this I guess it's a fringe benefit. -
Have you ever applied a 25mm screed on top of beam and block?
Boyblue replied to Boyblue's topic in Floor Structures
This is for the Bahamas, we have no insullation requirements. -
Have you ever applied a 25mm screed on top of beam and block?
Boyblue replied to Boyblue's topic in Floor Structures
The option is listed so I thought I'd ask, although the part about direct to slab is not indicated. I admit it is a bad idea because grouting all of those members is what makes the floor a monolith. Nowhere in particular, but I was thinking ground floor on a new build. I don't know, I have to admit it was a wast of gray matter or is it grey 🙂 -
Glad you asked. It hasn't been used primarily because our source of construction technology is the US, and beam & block is not used there because they've moved more to engineered stuff. With the additional cost of importation, that stuff is simply too expensive . Where we tend to differ are in cases where a superior alternative is more cost effective. It this case, slab on grade is used 100% of the time for our ground floors. The issue now is that fill is becoming scarce in the capital. That combined with the fact that concrete and steel prices are through the roof, could mean that beam & block may be a viable alternative. No fill, less concrete, less steel, speedy installation and the alternative to do a floating floor at ground level are all attractive choices. Fill will be barged from nearby islands so slab on grade will no doubt continue to be most popular but beam and block could gain a foothold. Second story, we use wood beams, suspended concrete, or web joists. Beam and block would be a welcome alternative there as well.