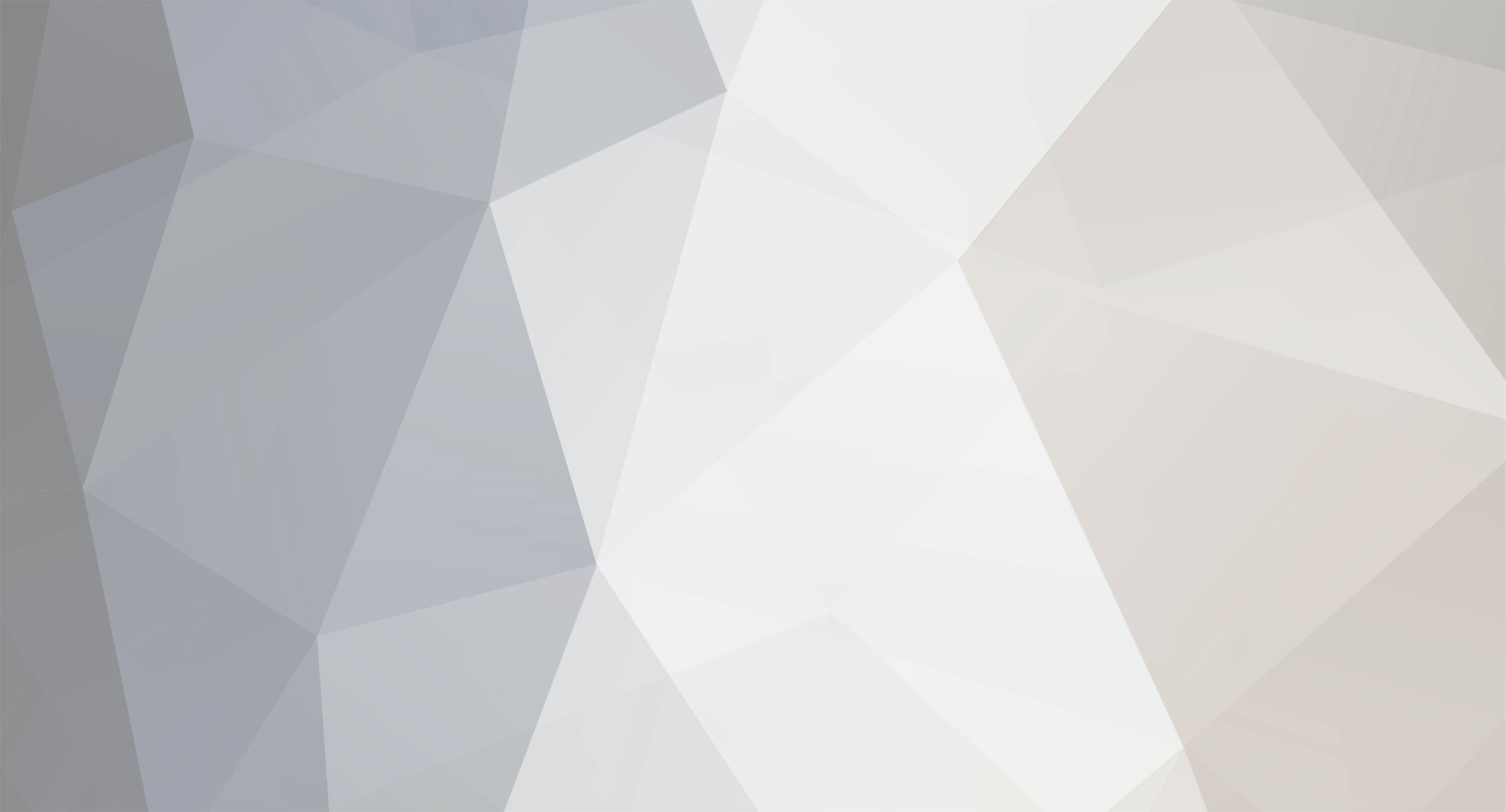
Ahad
Members-
Posts
13 -
Joined
-
Last visited
Recent Profile Visitors
The recent visitors block is disabled and is not being shown to other users.
Ahad's Achievements

Member (3/5)
2
Reputation
-
Sorry that is what he was suggesting, I think, but I’m reluctant to have all the slates stripped, feels we’d be pushing our look as despite being serviceable the roof is still quite old.
-
Thanks, good idea. I’m minded to get an application in and if we get approval we can assess when the scaffold is up. Worst case scenario is we take a closer look and decide to can the idea.
-
Thanks for the replies and particularly the advice about needing PP too. Having done some more research it looks like our council have never turned down a listed building application for solar. I can see recent approved applications for other nearby properties. So feeling quite encouraged by that. Although I spoke with an installer yesterday who said as the roof is slate it will need completely stripping to install the panel fixings. We are not intending to replace the roof, which whilst old is in reasonable condition, so plan to squeeze a few more years out of it. Not sure I fancy pushing my look by messing about with it though.
-
Does anyone have any experience of installing solar panels on a Grade 2 listed house, in a conservation area? I have looked through Listed Building Consent applications at the authority and they all seem to get approved, but presumably isn’t as easy as that. The panels wouldn’t be visible from street level. Any advice/ tips?
-
Thanks for all of the responses, really appreciated. It will be a long term home for us, so keen to do it to a decent standard. But will also consider payback on some of the spec, e.g. if payback on some energy saving initiatives is say 20 years then probably not worth it to me. In summary the feedback seems to be the quote is high for the standard proposed, and needs a proper review of specification.
-
2,000 sqft excluding the garage/ workshop, 2,450 with them included. Sorry made a typo - should have been £1,915, have corrected now.
-
This is the backing detail. Scope of work: General Notes • All screws, nails, ferrous metal straps and other misc. ferrous metalwork to be either zinc plated or galvanised. • Copies of commissioning certificates (including electrical system) to be deposited with Building Control surveyor as soon as they are available. • Demolition of existing unusable floors to commence, all debris removed from site. Foundations • 450mm wide strip foundation Gen3 concrete trenchfill of perimeter walls. • Excavate sub-soil to a depth of 1.25m below existing ground level & replace with well-graded granular stone, compacted as required. • Concrete vibrated into position to remove all air pockets. • Concrete slab to be poured to 150 thick. Concrete grade RC28/35 reinforced concrete. A252 mesh applied in top & 35 cover. 150 insulation on 1200 gauge polythene DPM on 150 compacted granular material (stone) bound with sand. Underpinning • 900 x 900 Underpinning of existing 7 column bases, size & depth to vary as required. • Underpinning to be carried out in 2 sections per base location. • Excavate & cast before moving on to next stage. Damp proof course • Marley Homegard Housing Grade Pitch Polymer DPC to be placed horizontally around perimeter no. 3 courses above ground level; 450mm laps to joints. Ground floor construction • Latex self-levelling screed to be placed across whole floor to ensure that floor levels are equal; floor finishes are to be installed outside the terms of the main contract. • 75mm cement: sand structural topping; powerfloat finish (containing underfloor heating pipework). • Polythene separating level between top of insulation and underside of structural topping. • 1000 gauge polythene Damp Proof Membrane; DPM is to be carried across cavity to full width of wall with polythene cavity trays above; all DPM joints and penetrations are to be taped with duct tape. External walls • Allowance for outer skin of walls to be cladded in larch. • 100mm cavity full filled with Celotex insulation. • 12.5mm plasterboard and skim secured to timber studs. • Cavity tray to be provided one course above DPC to enable any moisture in cavity to be shed outwards. Roof Structure • Asbestos roof removed & insulated with Kingspan tin & timber purlins. • Wall plates to be 75 x 100mm treated SW strapped to tops of walls in accordance with Approved Document A of The Building Regulations 2010 (as amended). • 6 Skylights to be installed. Roof joinery • All roof joinery to be constructed using wood grain uPVC cladding material. Optional. • 22mm thick fascia boards and 15mm thick soffits; uPVC profiles. • Deep flow uPVC Gutters. • Downpipes are to discharge directly to gulleys. External joinery • All external joinery is to be uPVC; precise door style and glazing options for front door to be agreed with client. However as per plan uPVC single front door & screen allowed for. • All joinery to achieve a U Value of 1.4W/m2k. • All doors and windows are to be installed by specialists and covered by FENSA Certification. • All habitable rooms are to be supplied with 8000mm² background ventilation, all other rooms to have 4000mm² background ventilation; provided via trickle ventilators, all trickle ventilators must be capable of being closed. • All glazing to be 4-16-4mm Pilkington “K” Glass sealed double glazed units. • All glazing below 1500mm in doors (800mm elsewhere) and within 300mm of door openings to be Kitemarked toughened glass to comply with BS6206: 1981 clause 5.3. • Allowance for up to 10 aluminium windows. • Entire gable to be aluminium & glass openings as per drawing – sliding doors. Ceilings • All ceilings to be 12.5mm plasterboard and skim throughout. Internal joinery • 25mm thick MDF window board. • 75mm architraves and 150mm skirting boards to be fixed with lost head nails Internal finishes – floors • Concrete floor to have a latex levelling compound applied in readiness to receive floor finishes; latex chosen to be suitable for the installation of engineered wood flooring, ceramic and quarry floor tiles. • All carpeting/flooring to be carried out outside the terms of the main contract. Kitchen • Kitchen to be fully discussed with client however a PC sum of £15,000 has been allowed for a based on mid-range standard kitchen from Howdens & won't be fully determined until spec of kitchen is confirmed. • Kitchen to be fitted with extractor hood above cooker with an extraction rate of 30l. per second. • All extraction fans are to be vented to atmosphere with brown plastic vent grilles. Bathrooms x3 • Bathrooms to be fully discussed with client however a PC sum of £4,900 each has been allowed for a based on mid-range standard bathroom & won't be fully determined until spec is confirmed. Electrics • Layout of lighting, light switching and socket outlets to be agreed with client on site; allow for locating an external socket outlet on the rear of the building as well as a light fitting adjacent to the front door. • All electrical works to be carried out by an electrical engineer who can self certify the installation upon completion of works. • Mains Operated smoke alarms with battery backup to be placed in new porch on Ground Floor. • Light fittings and electrical sockets to be positioned as directed by client on site within the parameters of Approved Document M; all electrical outlets to be manufactured by MK. • 50% of installed light fittings and bulbs to be energy efficient type to comply with Approved Document L1. • PC sum allowed £10,500 for electrics. Facilities for disabled persons • All light switches are to be no higher than 1200mm above finished floor level. • Electricity outlets, TV aerial and telephone points are to be no lower than 450mm above finished floor level. Foul Drainage • Access is to be maintained to all above ground waste pipework. • 110mm diameter stub soil pipe to be placed in corner of roof; fitted with a Durgo type air admittance valve 1200mm above internal floor level; soil pipe to discharge to manhole immediately outside porch extension and in turn to new treatment plant. • Foul drainage pipework to fall at a uniform rate of 1 in 60; pipework to be surrounded with 225mm pea gravel; concrete lintels to be provided where soil pipework passes through walls below ground level. • Treatment plant to be installed as per plan. • Waste pipework from back inlet gulley to discharge via 110mm diameter pipework to a system of proprietary plastic inspection chambers and eventually to existing site foul drainage system. • 110mm diameter plastic drainage pipes are to be laid to falls of 1 in 60; surrounded with 225mm pea gravel. • Proprietary plastic inspection chambers are to be used at pipe intersections and changes of direction; inspection covers and frames are to be rated to withstand both pedestrian and light vehicular traffic; inspection chambers are to be bedded and installed in strict accordance with manufacturer’s guidelines. Plumbing and Heating • Air source heating and hot water system to be installed; all works to be specified and installed by a specialist company. Smoke and heat rise alarms • Mains operated heat rise detector is to be placed in kitchen. • Alarms to be fitted in strict accordance with manufacturer’s instructions. Internal finishes – walls and ceilings • All internal walls to be plastered & finished ready to paint. • Internal walls to be painted with one sealing coat and two coats DULUX emulsion paint; colour scheme to be wall in Buttermilk or Magnolia, ceilings Pure Brilliant White unless instructed otherwise by clients. • MDF Skirting throughout. Surface water drainage • Rainwater downpipes to discharge to surface water drainage system via Hepworth trapped gulleys. • 110mm Hepworth ring seal (self coloured black) uPVC surface water drainage to fall at a rate of 1 in 80; to discharge to soakaways within garden; soakaway provision required to be sited a minimum 5.0m from dwellings. Drainage pipes to be bedded and surrounded with 150mm pea gravel; drainage pipes less than 400mm below ground level to be encased in 100mm Gen 3 concrete.
-
Noted on the VAT. Any specific items that stand out or just in general? Should have said it work out at £1,915 per sqm (ex VAT).
-
Afternoon, Would appreciate some feedback/ thoughts on a quote we’ve received. Project is a portal frame barn to be converted under class Q into a single story 3 bed house, c2,500 sqft including internal garage. In Worcestershire. Thanks.
-
Not agreed all the details yet but they all seem reasonable so far. Any ideas whether we’d need to remortgage completely (cost of barn + build) when we are ready to apply for a mortgage on the build costs?
-
Morning, first post here and would appreciate advice and opinions. My partner and I were trying to buy a barn to convert earlier in the year, which we got outbid on several months ago. Fast forward to this week and the vendor contacts me as the sale has fallen through. In the intervening period I have taken some time out from work - so currently unemployed. I have several job offers on the table, but do want some time out before starting a new job. I earn 3x my partner so need my income for mortgage purposes, which until I take up a new role clearly isn’t going to happen. The vendor has offered to lend us the purchase price, they want it sold because of impending changes to Capita Gains Tax. We are meeting them to discuss details but has anyone got prior experience of this? There are clearly many potential pitfalls and I am worried about getting finance to actually do the work. Thanks