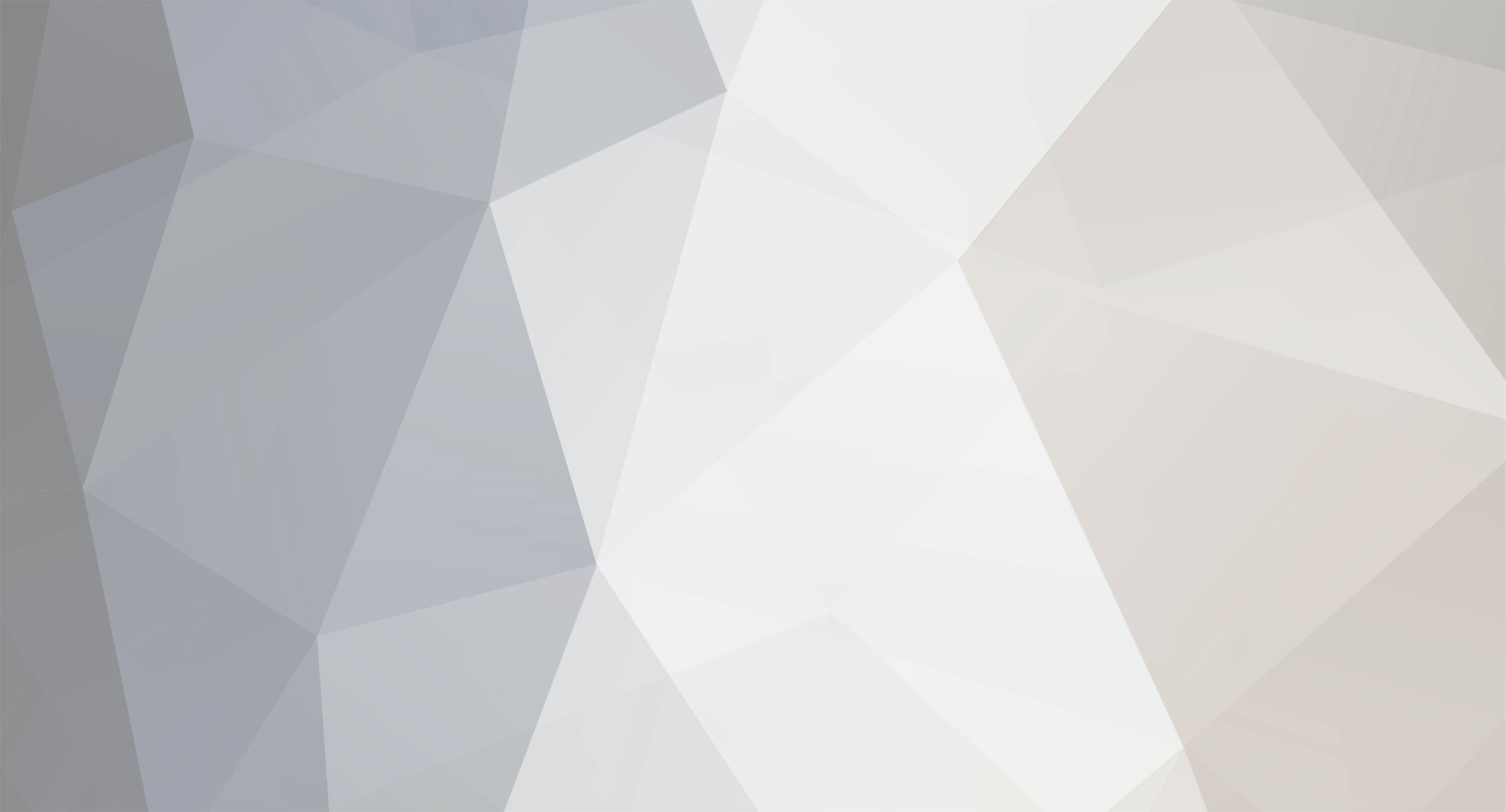
Phillymclee
Members-
Posts
10 -
Joined
-
Last visited
Recent Profile Visitors
The recent visitors block is disabled and is not being shown to other users.
Phillymclee's Achievements

Member (3/5)
3
Reputation
-
So I’m currently renovation a 1930’s semi. The bay window was not insulated and constructed of lathe and lime plaster internally on 4x2 studs with timber boards wrapped in some sort of plastic and pebbledashed over externally. I wanted to improve the thermal insulation in the bay wall and also improve the acoustic performance due to the noisy road while I was at it. (I know the large window is the main cause of the acoustic transmission but we are having new windows installed and I wanted to try to improve all parts of the bay). So I stripped the plaster off and was planning to fill between the studs with rockwool rwa45 for acoustics and then overboard the studs with a PAR board for thermal insulation. This was before I actually done a lot more research and found out that lime plaster was far better than gypsum products for acoustics even with the rockwool batts. But hey ho we live and learn. So now the problem is that upon doing more research it appears I may now also have a problem with interstitial condensation as if I insulate the bay, even with a vapour barrier some vapour may still get through and then it has nowhere to go as it’s my understanding that pebbledash is not breathable. So I’m worried if I do this I could end up causing the studs to rot. Does anyone have a solution or advice for this situation? The only thing I could think of was replacing the pebbledashing for hung tiles which in my opinion would look better but I’m a bit reluctant to do that as the pebbledash appears to be performing well in terms of keeping the damp out currently, the studs are bone dry, and I feel that tiles would be an even bigger downgrade in terms of acoustics with all of the little gaps everywhere. Anyway anyone’s thoughts would be much appreciated. Thanks in advance.
-
Hi guys. I have recently replaced the first floor joists in our renovation project for a future loft conversion. I had to remove the old ceiling along with the old coving which took the plaster at the top of the walls with it. It is a 1930's property with cavity walls and lime plaster. I intend on fitting resilient bars to the underside of the new joists so looking at resilient bar details it looks like the wall plaster should continue up passed the ceiling plasterboard and the ceiling plasterboard sit inboard of the wall plaster with a gap filled with acoustic sealant. What is the best way to fill these gaps at the top of the wall? I understand that lime is better than gypsum for breathability (but then less important for cavity walls) and I will do my best to use lime plaster where I have any large patches that have come loose but I also understand that lime doesn't really stick to timber so was wondering if the best idea would be to use bonding plaster for the strips around the top of the wall where there are timber wall plates. I was thinking to additionally fix 100mm wide galvanised expanded metal lath to the 50mm wall plate and brickwork under, sealing with PVA and then bonding over in 10mm layers. I know that I could probably do the same with lime but would need stainless EML and fixings if I am not mistaken and it just starts adding to the cost so would only do that if it was absolutely necessary. Does my approach sound reasonable and won't end up cracking all over the place or inadvertently rotting the wall plates because they can't breathe haha. Also will this approach be fine for a bathroom? Many thanks in advance.
-
First house, first renovation, 1930's semi.
Phillymclee replied to Phillymclee's topic in Introduce Yourself
Hi SteamyTea, I’ve started my first post regarding the ground floor wall alterations with a few photos you may be interested in on the RSJ, Lintels sub forum but will also take a few today of the progress so far and add to here. -
First house, first renovation, 1930's semi.
Phillymclee replied to Phillymclee's topic in Introduce Yourself
Hi Gus, thanks for the reply. Sounds like you've had an interesting career and learnt a lot a long the way no doubt. Yes as someone who spent a bit of time working as a technician for a modular builder working to tolerances of a couple of mm and detailing every nut, washer and bolt, to enable the generally unskilled guys in the factory put the modules together, I sometimes find the lack of detail we provide in a SE consultancy for smaller jobs frustrating and feel sorry for the poor buggers on site having to build it. But glad I had the experience of both as can now put as much detail as I want into my own project whilst understanding the overall structural principles and limitations which really helps me when I come to actually carry out the work. Thanks it has helped me a lot so far, always helps to be able to model something before building it and I've managed to overcome every issue that has cropped up but have also been scouring the internet for answers when I need a second opinion so thought I might as well sign up to BH as would be better to have a direct dialogue with people in the know. I am still working on the structural modifications at this stage but I expect I will be looking for advice from the plumbing, heating, Architecture specialists a bit further down the line for sure. Many thanks for all of the info, look forward to our potential discussions in the future. -
Hi guys, thanks for the replies. I agree that would be better structurally ProDave and make the job a lot easier however to give you a bit more context I want the downstand to line through with the current wall return in the dining room and not in the middle of the room as that part of the wall will remain. Also I will be removing the beam supporting the stair quarter landing and replacing with a cranked PFC connecting into the new beam so don't want the span to be to big for that. And finally the steel has already been designed and procured for the current spans so I am stuck with what I have. Please see images below for a better idea of what I mean. Ignore the messy kitchen cabinets I'm still working on all of that haha.
-
First house, first renovation, 1930's semi.
Phillymclee replied to Phillymclee's topic in Introduce Yourself
Thanks Mr Punter, yes let's hope so or the wife won't be happy haha! -
Hi there. I am removing a loadbearing wall which is currently supporting the first floor joists at roughly 1/3 span. For context there is no wall above and the joists are continuous over the wall I am removing. I have had the calcs done by a Structural Engineer, notified building control and have already procured the steel. I will be installing a 178UB in place of the current wall with padstones at each end and was planning on positioning the top flange tight up against the underside of the joists and fixing a timber underneath the top flange and use truss clips to restrain each joist rather than having a timber plate on top of the beam to minimise the downstand. I thought that this would all be pretty straight forward but when doing some last checks the other night with a laser level I noticed that the current wall plate slopes from one end to the other by about 25mm (over about 3.9m) where it looks like the almost 100 year old house has settled over the years. So my question is whether I should install the beam level and pack the underside of the joists where required or install the beam following the slope of the existing wall plate then packing out the underside so at least the plasterboard is visually level. It seems a bit of a bodge to install a new beam not level but then it would be a lot easier to install it slightly sloped especially as all of the current brick coursing is also sloped so will avoid me having to slice a bit off the top of the bricks to one side when installing the padstones. But just wanted to check what the consensus was here to make sure there isn't something I have not thought of. Thanks in advance.
-
Hi all. We recently purchased our first house which needs a 'bit' of TLC to put it lightly. Currently living in a rented flat so need to get into the new house as soon as possible but have an awful lot to do and not a lot of money to do it so it's down to me to put my DIY skills to the test and hopefully pick some up along the way. I have a background in construction being a draughtsman for the last 17 years, starting on AutoCAD and have been using Revit for the last 6 years in a Structural Engineering consultancy but I'm quickly finding it's one thing drawing something and another thing building it. I'm yet to find a straight line in our new house. So while I have an understanding of the theoretical side of construction techniques I am less versed in the actual application so will hopefully call on the knowledge and experience from you lovely people to get me through this. I have a few big jobs on my list before I can begin to turn the current 'building site' into something that resembles a home. I have just finished replacing all of the first floor ceiling joists for a future loft conversion (all calcs done by an old colleague and signed off by building control) and am now halfway through a full rewire. I will be moving the bathroom so will need to learn some plumbing skills and will be taking out a short length of load bearing wall at ground floor (again already have the calcs, steel procured and building control notified). Anyway that's a little bit about my situation. Look forward to chatting to some of you soon. Thanks