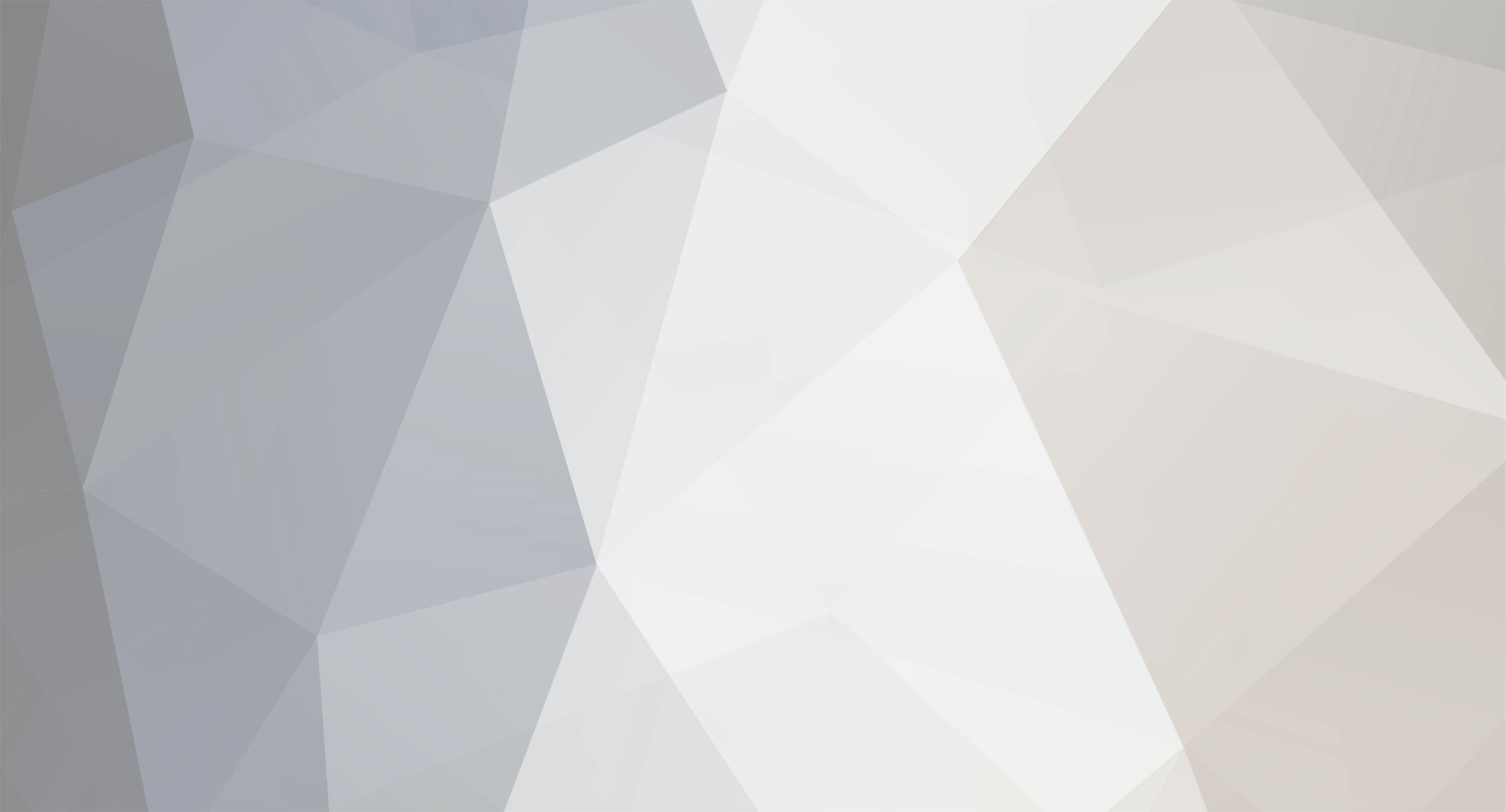
Aus_Doug
Members-
Posts
13 -
Joined
-
Last visited
Personal Information
-
Location
NSw, Australia
Recent Profile Visitors
The recent visitors block is disabled and is not being shown to other users.
Aus_Doug's Achievements

Member (3/5)
5
Reputation
-
Hi, still working on the design. To answer Steve, there should be local Hemp available. I will source mine from near Inverell, NSW. AHMC (Australian Hemp Masonry Co, an Australian company) do training on Hemp building, & have locally made renders & binders available. Personally I think the poured in place is the best method (building walls in layers. Full shuttering one side & other side liftable ~600mm shutters.) The Hempcrete is placed around a fairly standard pine frame to Australian framing standards. The only issue is any steel must be protected with bituminous paint (Hempcrete is very alkaline). The problem with Hemp blocks to my mind is they are non-structural, & it would be a hassle to cut them around the timber frame anyway. My design is to be a PassivHaus: Fully sealed, blower door tested, with MVHR air exchange system. It is now 3br, & abt 120 sq M. My main difference to ´normal´ building is I will have no eaves, & the roofing iron will overhang with supports with the guttering on G&G gutter brackets (that screw to the laps on the iron). The walls will have a lintel beam the full length above the top plate, & the trusses will sit partly on the wall top plate, & screw to this lintel. My Hempcrete will extend up to the top of the trusses at the end & lap into the ceiling 100mm so I have no air leaks in the corner. The trusses are designed so I have 270mm of hempcrete at the corner which eliminates the usual problem of reduced insulation at the ends of trusses. Having no eaves & soffits is a big cost saving: I will bracket an outrigger batten to support the 600mm roofing overhang. G&G brackets are abt $10 ea, so economical. 150mm half round gutter, with sloped ends so leaves can be swept out. btw, if you are pouring a slab, consider Cuprolex domes: saves concrete & better than Polystyrene. I will try to build for $Au3000 per sq M (tight, but I think achievable). AHMC supply to Melbourne, & there will be hemp growers in vic I guess (but they need the processing plant to reduce dust in the hemp) Otherwise, AHMC will supply. btw, well worth doing the training with AHMC: there are a lot of pitfalls if you do not....
-
Rural block, so Rain water (& occasional spring water, but usually my 100000L of water storage is enough.) The build is Hempcrete, so the Air seal layer is internal , basically the 10mm of lime based render, but the render is both sides of the wall. The ceiling seal layer is OSB, below 300mm of insulation. The OSB is sealed with WaterGlaze to air seal it, & joints taped. The MVHR will hopefully keep the internal humidity to a reasonable level. The Lossnay will transfer a little humidity to the incoming air, but basically remove humidity from the high humidity areas of bathroom & Kitchen. The A/C unit will be separate, with the idea of only lowering the temp a few degrees to de-humidify. I am hoping my Home Assistant system will be able to control the Air system, by measuring Temp & humidity (indoor & outdoor), then managing the air movement, bypass, & A/C. There will be a ventilated area under the roofing iron, using Soffit Vents & an Australian product called Vent-a-Ridge, that will cause air flow over the control membrane & under the iron. (Counter Battens, & ventilated Top Hat Steel Battens, that are actually rolled steel tophats used for trusses, but I will have them fully punched, 8mm holes, 2 rows, 25 apart so some air passes through the battens.) The Ceiling space will also be ventilated. Solar Panels will cover most of the Northern roof, mounted on S5 (rail-less) mounts . These mounts give more free airflow (& hopefully less to trap leaves!).
-
Regarding China, I visited China in 1978 (Before the gang of 4 second revolution). We saw the article about the 10000 pottery figures in Xian in the National Geographic. We chose a tour that went through Xian. When we got there the 2 local guides said the diggings were not open, but the 2 national guides pulled some strings & we got to see the diggings. The Building was just completed, (a huge building like an aircraft hanger). The diggings were fantastic. Anyway, the car park was not sealed, & the bus bogged! We had to wait for a replacement bus, & we were waiting in the curation room: a once in a lifetime experience. All in all a fantastic trip. I have a lot of respect for the Chinese: in 1948 they were basically starving. by 1978, they were fed & housed, but it was still very agricultural. Since then, the developments have been unbelievable. (probably based much on greedy US Industrialists who moved manufacturing plants to China). Now, it seems the boot is on the other foot, with the West trying to catch China. The latest EVs are just one facet. Chinese manufacturing is basically robot driven: There is a car factory that builds Volvos etc, that has 200 production employees on the assembly line. Having worked in Manufacturing (STC Telecom. in the 1980s: there were 2000 employees in Sydney), That is not many employees on the line.
-
Building in sub tropics, abt 200Kms S of Brisbane (abt 40Kms from Byron Bay, but dont hold that against me!). We get occasional High winds from the West, & heavy rainfall with Climate change (2022: Floods in Lismore, & we received 1M of rain in 24H: my rental property in Lismore flooded to the fans, 2.4M higher than white man had ever seen: I had designed the floors 900mm above previous max flood height.) Humidity is a definite problem, causing Mould. My design will use a Lossnay MVHR, & I will have a separate small A/c to control Humidity mainly. (The Building volume is abt 250 cu M.)
-
There are some incredible Chinese cars coming. The Paris Car show was an eye opener! Actually, I like the new small Hyundai (or Kia) SUV. One thing I like is having no console between the front seats (except for a pull-down one). Longevity? Who knows. Most cars are made in China anyway. All built by robot. The Chinese car manufacture is wolds apart from some of the ones from a few years ago.
-
I did not mention that I am in Paris on holidays atm. Plenty of time to think about my design... Going to the Motor Show on Tuesday: Be good to see the new crop of EVs.
-
Because it is a minimalist build, 900 trusses is worthwhile. As I said the only roof loads are solar panels * perhaps a HWS in the ceiling. Timber is expensive in Australia because most is imported. I will try to minimalise by buying sling lots/packs but not always possible. I have clipped a detail drawing of the top of the wall cross-section: I had a think on the idea of a big member at the top of the wall, then realised I could run it outside the end of the trusses. The 190x45 would be glued & screwed to the 90x45 top plate. The trusses are then screwed thru the end, which also gives some bracing. I might even get away with not tieing the trusses down with steel strap (reducing thermal bridges). I will need to discuss this with the engineer... The truss is 225mm high at the end. One other note: I returned the Hempcrete into the room that will help the insulation transition. I will nogg between the trusses at the edge of the OSB to support the edge. The OSB will be taped to the Wall render for the air tight layer. I will seal the OSB with Waterglass to reduce porosity. Also note the layer of (450mm w) Fibre Cement sheet under the counter batten at the lower edge of the truss: that gives a permanent form for the Hempcrete. It also gives a flat sheet to Fire seal the vent that is not detailed there. Cross_sect_Wall_top.pdf
- 9 replies
-
- hempcrete
- mvhr passive
-
(and 1 more)
Tagged with:
-
Just for an idea on timber price: 90x45mm studs are $au 5.85/M, where 190x45mm is $au17.05/M. That is the reason I think trussing will be worthwhile....
- 9 replies
-
- hempcrete
- mvhr passive
-
(and 1 more)
Tagged with:
-
Thanks for that. I was aware of similar techniques. (We would probably call that a Ring beam, but usually 4 sides). The difference with ´trussing ´ the frame above the windows/doors is it uses really cheap timber: probably 50x35, because it is in compression. Anything bigger than 90mm in Aust. gets very expensive (comparitively). I can also potentiall recycle some pine Pallet timbers. I will give a drawing of my roof trusses later, but basically they step down 90mm from the wall plate. This gives me plenty of room for the Hempcrete up to the roof membrane (I will use Fibre cement at the bottom of the pitch to have something to form the Hempcrete against). The idea is to have the full 270mm on radius for my Hempcrete (so no cold spots). By having my Ceiling insulation transition inset into the room, I can better manage the gaps etc. btw, the double top plate is needed because the trusses are not always in alignment to the studs. Also using small timber members gives better adhesion of the hempcrete. (Large beams need holding studs such as a large plastic washer on a spacer so the hempcrete does not separate.) I have tried to use the minimal amount of (purchased) timber that I can to reduce costs. Shuttering Hempcrete is fairly easy: 10mm OSB is adequate. You screw a long screw into the joist to the required thickness of hempcrete, then screw the shuttering next to the spacer screw. The top can be held with timber spacers that are removed when the fill gets near the top. After the Shuttering removed, remove the spacer screws & fill the holes. Pretty easy. Sometimes one will need to work around fixtures etc, but all do-able I feel.
- 9 replies
-
- hempcrete
- mvhr passive
-
(and 1 more)
Tagged with:
-
One thing I am getting my head around is the need to DESIGN EVERYTHING! Even the hole thru the wall (requiring sealing) for the porch light. Most electrical work will be inside the sealed envelope (which is the interior lime plaster in a Hempcrete house). Electrics will pass from the ceiling cavity (~125mm also used for MVHR) through a conduit to the cable end (switch or power point for example), so that conduit passes through the rendered membrane, down the wall, then back thru the membrane, all requiring sealing. Australia does not have any decent sealed wall boxes, so I must work out how to effectively seal the available boxes. Of course all of this will be installed before the Hempcrete placement. Even the MVHR air supply return will need to be installed (or at least arranged for) before the Hempcrete placement. I am thinking of ´trussing´ up the window & door heads instead of using the usual timber lintels. Accomplished by diagonal struts between studs over the window/door. I will be having the frames factory made, so I can either ask them to fit the bracing, or retrofit on site. One thing with Hempcrete is that the noggins (horizontal timber between studs) are fitted not on the flat, but rotated 90 degrees (ie 90mmx45 studs, noggins similar size but 90mm is vertical). This makes it easier to place the Hempcrete. Remember we have no snow loads, so the frames are much lighter in Australia. Usually in Australia the wall frames are braced with ply or OSB. With Hempcrete, the ply is not used, so needs to be replaced by timber bracing. In my case, with 90mm studs, & 270mm Hempcrete I have 90mm each side of the frame. The Bushfire certification needs at least 75mm of Hempcrete, so the bracing is internal. The bottom wall plate is 45mm, sitting in a ~40mm slab rebate, so my solution is to double up the bottom plate so I can have room to attach the required bracing (probably 75x25mm pine bracing, but up to the Engineer!). Being in a sub tropical zone, we need hold down for the wind load, so the top & bottom plates are screwed to the studs as well as being nailed. The bottom plates are Concrete screwed to the slab, & the roof trusses are steel strapped to the wall frames. As I said previously, there will be an OSB layer under the trusses sealed as the air seal membrane, but als giving wind bracing. The internal walls are non-load bearing (basically ending at the celing cavity so services pass over) An explanation of the No soffits, no Barge board: basically roofing iron can self support for 300-400mm, including the guttering load (no snow!). The 600 eaves are supported by a purlin supported on steel brackets off the wall. No timber due to the Bushfire zone! All the mounts for these brackets also need to be designed & fitted pre Hempcrete. I am proposing using bolts that are a woodscrew one end, & Metric thread the other. Extended by a loctited double nut & extra thread. These can be found with a stud detector after the wall is hempcreted & lime rendered.
- 9 replies
-
- 1
-
-
- hempcrete
- mvhr passive
-
(and 1 more)
Tagged with:
-
Voluntary Energy Coach: If someone has a query (usually due to abnormal energy consumption), if the Telephone support people of Enova cannot help, they passed the query to one of us. As an example, I visited a client who had really big bills, & worked out that they had a timeswitch on their (resistive 3.6Kw) HWS. Even tho the timeswitch might have 20A contacts, there is enough inductance to flash the contacts welding them shut. If one is switching currents like this, it is important to use a slave Contactor. (This was just from looking at the board from the outside, seeing no contactor & suggesting to the client they engage an electrician to install a new timeswitch + contactor. Happy client! As an aside, if one is switching an EVSE granny charger (10A plug in portable car charger for the uninitiated) with a controlled switch, use a slave contactor. Most of the Tuya etc switches will not last reliably with 10A constant power drain (again due to slightly inductive load when the load switches). Enova eventually went into voluntary administration due to the Australian Gentailers (Energy retailers who also own generation capacity) would not give Enova a supply contract where we could remain financially viable. Covid did not help too.
-
Hi, this is my 5th build: started with a decrepit timber terrace in Sydney pre pre internet. I was an inexperienced renovator, & needed to ask people how to do jobs. Bought 1972 for $au12500, sold 1999 for $au340000. The house was double the size, & quite eclectic. Built a weekender 200Kms out of Sydney, & moved a small prefab building onto the block. That was sold in 1993, when we moved to Northern NSW, & bought our current block. Designed our modest abode in the early 2000´s. It is 4 storey, & abt 700 M sq. The 4th floor ois Doug´s folley: a room that looks about 30km to the coast (with a glimpse of Evans Head). This house is built from dry stacked Hebel block (no glue) that is held together by the cyclone rods at abt 900 centres. Huge foundations (600mm wide strip, 900 deep!). Now up for 25 years. My next build is a Hempcrete house, as a 110 sq M secondary dwelling on this same block. Difference is it is fully accessible (900 wide doors, accessible bathrooms & kitchen, no steps or hobs. Designed as an extremely economical PassivHaus. Other than that, I am a retired Biomed Techniician (Medical Equipment), retired 10 yrs ago. I was a voluntary Energy Coach for Enova energy (a Community owned energy reseller, until we went broke!) My PV system is 15Kw, with 2x 5kw SolarEdge inverters, & 2 Victron charger inverters for my 12kw of Lithium Titanate batteries. We have 2 EVs: a 2020 Kona EV (130K Kms), & an Imiev that has 130000Kms. These recharge off PV. I have a Home Assistant controller looking after all my energy. (Love Home Assistant!) The new House site has a 7.2Mx7.2M carport with 6Kw of panels. 48v of 1000ah L/A batteries, (abt 50Kw of storage), controlled by a Selectronics Inverter. There is a Low current 240v feed to this site for backup. The system was bought s/h for a good price, so is now waiting for the house! What else can I say: I was chair of ´Politics in the Pub´ until during covid.. (a non-political talkfest where current topics are given by a guest speaker) Well, thats it basically.
-
Hi, just joined because I was reading all the posts about MHRV. I have the basic design of my proposed 110 sq M house: 3br, 2 disability bathrooms, superinsulated, Off centre roof pitch with the long side facing N (S hemisphere!). wrt the MVHR, it seems the most economical solution for me is a Mitsubishi Lossnay ceiling mounted. After doing some research, I have found a Chinese Co that supplies 90mm round Semiflex duct & accessories. Yet to create a manifest, but providing the freight is reasonable, should be economical. The Co is: https://www.erviguicoo.com/fresh-air-abs-distributor-with-high-quality-abs-materials-product/. So far I have a catalogue, but will need drawings, etc. The Lossnay will be locally sourced for warranty. btw, the Steib-Eltron tool is great for designing the MVHR system. Some details of the build: light construction because there are no snow loads! The Wall frames will be Pine, with the top & bottom plates screwed as well as nailed (due to Cyclone uplift). Studs 90x45, on 600 centres. The roof trusses will be at 900 centres. The roofing is Trimdek corrugated iron, but I will use 0.48mm as I will use S5 mounts for the solar PV that are rail-less (just screw to the ridges, hence the thicker steel). Hempcrete: 270mm thick walls with 10mm lime based render each side. One thing I will do differently is to raise the truss bearing point so I can have 300mm of insulation across the ceiling with no step down, The Hempcrete walls will go to the top of the outside edge of the trusses, & will return into the ceiling, sitting on a ledger. Then I can seal & attach my OSB airtight layer directly under the trusses. The OSB also gives wind bracing. (all joints sealed & taped). 300mm Fibreglass insulation above OSB. This will be built on a slab foundation, using Cupolex domes. The edge rebate will have stainless ant barrier/dampcourse. Air sealing: all transitions taped after walls are rendered. Slab is to be polished, so the concrete will be edge primed before taping . Blower Door test: I will DIY a blower door using a s/h Automotive 12v radiator fan. I already own a digital manometer, & after reading the MVHR threads will buy a Testo 425 Digital Hot Wire Anemometer (the computer connected one), & control the fan with a DC speed control to vary output. The Air volume can be easily measured with a cone over the fan, & something like a piece of 150mm plastic stormwater pipe, with a hole to insert the Anemometer probe. This anemometer is apparently sensitive enough to check for leaks around windows, etc. The Automotive fan will easily blow/suck 50 pascals. My build is also in a bushfire zone. No gaps bigger than 2mm in the outer sheath & roofing: I do not use Soffits or barges: I use a product called G&G gutter brackets that screw to the metal roofing overlap. I use 150mm half round gutter that I can easily clean (with a moon section on a pole). The gutter ends are sloped so I can sweep the leaves out. In Australia, the roof space must be ventilated, which is accomplished with about 75mm wide folded perforated aluminium sheet that runs on top of the hempcrete, to the underside of the roofing. I have designed a system that stops the embers. The vent at the ridge is a product called Vent-a-Ridge. This allows air to pass under the (raised) ridgecap, exiting through the corrugations. There will be the usual smart membrane & counter battens for air flow. Hopefully I can build this for less than a ´normal´ builders build (aiming for $au2500 per M sq) regards, Doug
- 9 replies
-
- 2
-
-
- hempcrete
- mvhr passive
-
(and 1 more)
Tagged with: