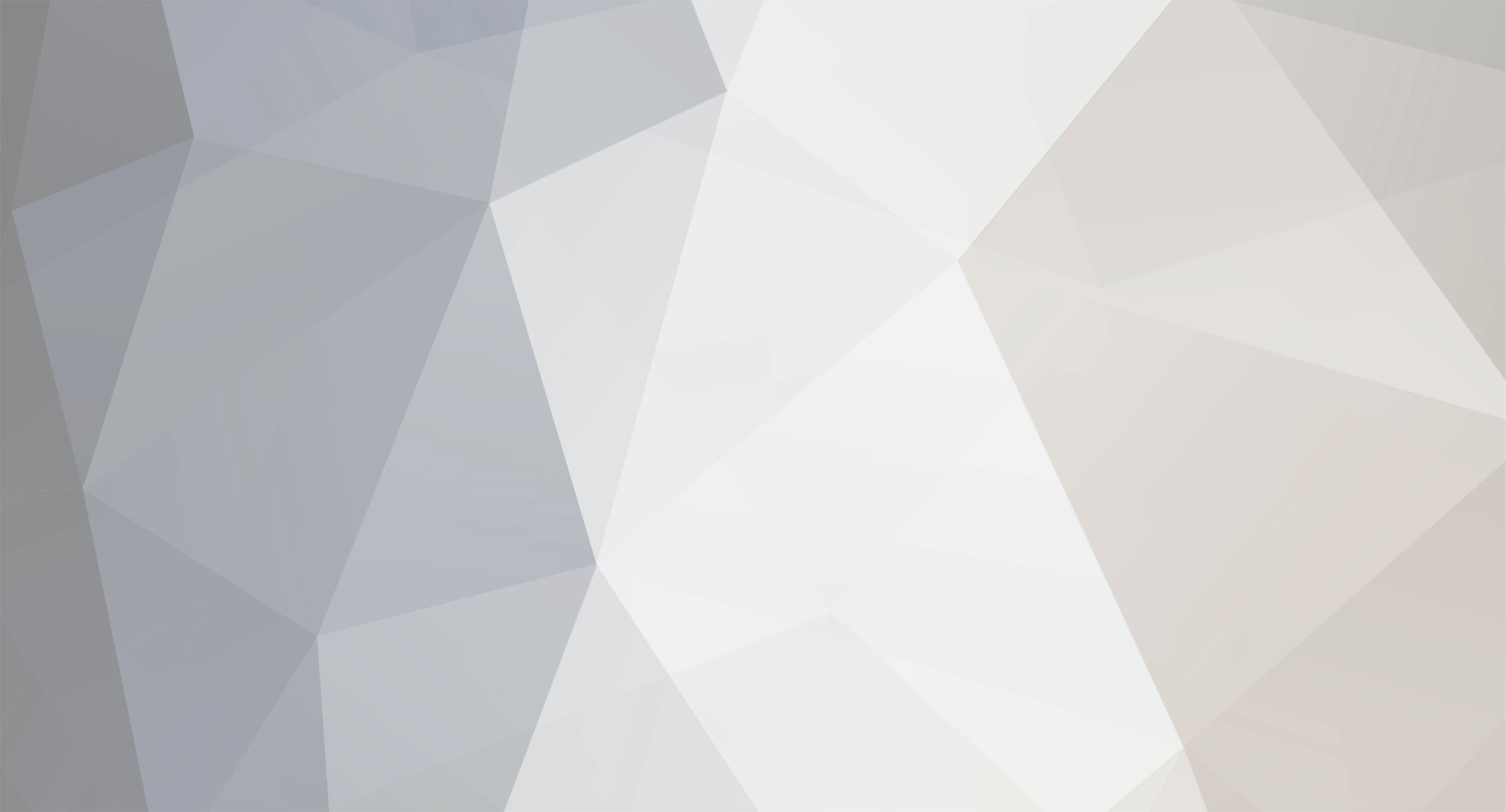
joshwk
Members-
Posts
16 -
Joined
-
Last visited
Recent Profile Visitors
The recent visitors block is disabled and is not being shown to other users.
joshwk's Achievements

Member (3/5)
3
Reputation
-
SIP wall thickness: diminishing returns?
joshwk replied to joshwk's topic in Structural Insulated Panels (SIPs)
Hi all, Coming back to this thread as we finally have a start date after 5+ years(!). Update: I've opted for the MVHR company to supply and fit, so there is one point of contact if there are issues down the line. Question: As the walls + sips are fully constructed in Kingspan, there is no insulation between the joists where we have flat ceilings. Should I be requesting this to further improve insulation and/or is should I be installing this to reduce the sound of airflow in the ducts? -
SIP wall thickness: diminishing returns?
joshwk replied to joshwk's topic in Structural Insulated Panels (SIPs)
Interesting, thanks both. I actually made a separate post on the MVHR sub-forum about this topic as I was trying to determine the pros/cons to both. In the end, we opted to proceed with a rigid branch system using a who have experience working with our appointed SIPs supplier. We were led to believe the benefits of a rigid system was that it's more "hygienic" and PasivHaus themselves opt for rigid ducting in their testing (which may have just been sales-BS). Currently, we've opted for supply only. The MVHR supplier is quoting ~£4K to carry out the install and although I appreciate it's a premium expense, I'm tempted to have them undertake this so there's a single point of contact for any issues in the future (and also avoid the headache of installing this myself). Alternatively, I could ask with my builder if they'd be prepared to take it on (and get a quote), but wonder if people have had positive/negative experience with this? -
SIP wall thickness: diminishing returns?
joshwk replied to joshwk's topic in Structural Insulated Panels (SIPs)
This sounds very sensible. Is there a tool you used to do this? I've so far committed to the fabric (walls currently 0.15 and roof 0.11 but in trying to determine if I should upgrade the walls, based on the responses so far the answer is yes) We have committed to MVHR (rigid ducting, Zehnder Q350 system) Appreciate the importance of air tightness; we will be working with the SIPs company and our respective contractors to ensure they understand the importance of this (i.e.. not puncturing holes everywhere). RE: thermal bridging, this is acknowledged in my quote ("Under new 2022 Part L Building Regulations, Thermal Bridging needs to be calculated and measures should be taken to reduce thermal bridging where possible. In the case of TEK (SIPS), where required, this involves the simple application of a secondary layer of insulation, (typically) positioned in the room side of the external wall or underside of TEK (SIPS) roof. This detail reduces our already excellent U Values further, whilst improving our psi values at the same time. A further benefit of this detail is an improvement in air permeability, due to the addition of a secondary taped layer of insulation TW55 (walls) - TP10 (roofs).". Am I right in my understanding that the extra +25mm PIR to walls and +75mm PIR to roof speaks to this? I've noticed the quote from my SIPs supplier hasn't allowed for supply/fix of VCL to walls and roof. Is this something I need? -
SIP wall thickness: diminishing returns?
joshwk replied to joshwk's topic in Structural Insulated Panels (SIPs)
@SBMS Thanks for taking the time to respond. I haven't! Is there a simple way to do this? Thank you. -
SIP wall thickness: diminishing returns?
joshwk replied to joshwk's topic in Structural Insulated Panels (SIPs)
Thanks for taking the time to respond, everyone. I'm coming back to this thread after trying to move our project along coupled with a busy work/family life. @Iceverge The "North" and "West" building in the below will have a skin of brickwork, whereas the centre of the building are large glass openings and this area alongside the "East" building will be timber clad. -
MVHR Design: Feedback & Mythbusting
joshwk replied to joshwk's topic in Mechanical Ventilation with Heat Recovery (MVHR)
Thanks for the replies.Without going into too much detail, our self-build project has evolved dramatically over the past 4 years from "full conversion" to "full demolition and rebuild" due to structural issues. We were strongly advised by our architect to pursue SIPs, due to their strong overall performance, which we committed to back in 2020. At the time, the building was ~50% conversion & ~50% rebuild so the "full demolition" opportunity allowed us to build in 100% SIPs. My understanding is that SIPs were good for air tightness but the "3m³/m².h@50Pa air permeability" figure is truthfully the first I've heard this referenced. I'll enquire with our architect now RE: air infiltration/air tightness but if we're using SIPs coupled with a high performing window (e.g. thermally broken aluminium windows), should they be able to provide a simple calculation i.e. "better than 3" or do they outsource this to a specialist company to calculate the numbers? -
MVHR Design: Feedback & Mythbusting
joshwk replied to joshwk's topic in Mechanical Ventilation with Heat Recovery (MVHR)
Thanks both, that's helpful. Sounds like the Air Tightness calculation is a question for my architect. Is this something quite standard, which should be calculated as part of the Building Regulations submission? Outside of questioning the role of MVHR - any other thoughts / feedback to the initial list of questions would be appreciated! -
MVHR Design: Feedback & Mythbusting
joshwk replied to joshwk's topic in Mechanical Ventilation with Heat Recovery (MVHR)
Thanks @IanR. We are targeting an improvement vs building regulations (I actually made a post here to try and understand SIP wall thickness and diminishing returns here). Currently, I am approaching our build on the basis that walls would be 142mm + 25mm PIR to achieve a u-value of 0.15 and roof would be 142mm + 75m PIR to achieve a u-value of 0.11 I'm less familiar with Air Infiltration/Permeability requirements; is that related to PSI vales, or is that something completely different? -
MVHR Design: Feedback & Mythbusting
joshwk replied to joshwk's topic in Mechanical Ventilation with Heat Recovery (MVHR)
Thanks for the response, @Mr Blobby@Kelvin . I will ask the designer the question RE: branched ductwork but wonder if it is because we are using rigid ducting? Additional context: Bedroom 1, Bedroom and the Kitchen + Dining/Living Room will be vaulted ceilings. There will be a small void here and within the hallway to hide the ducting. I'm not super familiar with a branch vs radial duct system (apart from what I've just read here). My initial thought would have been that a branch layout lends itself better to a house with vaulted ceilings (as there is less ducting to run/hide), however the URL I just pasted mentions that the individual ducts are smaller and can be grouped together, resulting in a smaller ceiling void. Again, I'm not sure if is suitable for us as we will be running a rigid system. @IanR: Thank you! The MVHR supplier we are using was recommended by our SIP supplier; they have worked together previously. We are currently submitting our Building Regulations (for the second time) and are about to go out to tender (we don't yet have a builder or the other trades on board). I'm not sure what the target air infiltration rate is, where should I source this? Cheers, Josh -
Hi all, My architect has been very debbie-downer on MVHR, driven largely by a lack of understanding of the technology ("they're very loud and not good if you have allergies"). Nevertheless, I'm committed to it so would appreciate any thoughts on the V1 design I've received from our MVHR supplier. Some context: Our house type will be single storey, constructed in SIPs, ~200m2 total size. We've opted for a Zehnder Q350 system, which should provide up to 350m3/hour. Rigid metal ducting with metal silencers. I understand size of rigid metal ducting in general ranges from 200mm to 125mm and the larger ducts to the atmosphere will be insulated with a 50mm isosleeve (specific details of our sizing are called out on the attached). We have one unavoidable ‘tight’ area transitioning between the utility and kitchen, where the designer has proposed a special rigid metal rectangular duct (220mm x 55mm) to hide a duct in a stud partition. Our architect is pushing the supplier to locate the MVHR system within the attic. The designer has flagged that by doing so, it could cause vibrational noise as the floor is timber made, hence, locating it on the ground floor would be less severe. The majority of systems I've looked at have the unit siting on the floor with silencers vertically mounted and ducting branching off into the attic space, which I I am not adverse to (in fact, it's probably my preference as I understand the filters need to be changed every 6 months), assuming there is sufficient space in the plant room. As the plant is located next door to a bedroom, we will also sound insulate the plant (e.g. rockwool) for peace of mind. I'd appreciate any feedback on the following: The MVHR design in general Any thoughts on the size of the ducting? This is the area I'm probably least familiar with. Any thoughts on the Zehnder Q350 system and if this is under, oversized or "just right"? Should I be concerned about i) the noise of the system and ii) the plant room being located next door to a bedroom? Even though I will sound insulate the plant room? Any pros or cons to locating the system on the ground floor or in the attic (outside of space saving)? Thanks in advance! 26791_V_R1.pdf
-
SIP wall thickness: diminishing returns?
joshwk replied to joshwk's topic in Structural Insulated Panels (SIPs)
Good tips, thank you @SteamyTea & @Iceverge. @SBMS: 142mm appears to be the standard manufacturing for TEK Kingspan. 172mm is also possible but requires additional work in cutting transition materials down to suit the non standard wall panels width (quoting the images shown above). Per the table, 172mm with no additional insulation is estimated to achieve a 0.16 U/value. To achieve close as close to a 0.1 U/value as possible based on @JohnMo's suggestion, in my personal situation, I think the best route is to use 142mm but upgrade from +25mm to +75/80/90mm to achieve a 0.11 on the walls (in line with the current estimated U-Value for the roof). -
SIP wall thickness: diminishing returns?
joshwk replied to joshwk's topic in Structural Insulated Panels (SIPs)
Thanks @JohnMo, that's a great callout. Very helpful. -
SIP wall thickness: diminishing returns?
joshwk posted a topic in Structural Insulated Panels (SIPs)
Hi all. We will be constructing our self-build in SIPs and I was curious to understand if there is a school of thought on 'diminishing returns' when it comes to wall thickness and U-value effectiveness. I realise the black and white answer is 'the lowest u-value is the best' and that there is a significant variable in the form of cost, but what I am curious to understand is if there is any general thinking on what a 'sweet spot' might be when it comes to investing into additional PIR vs the incremental gains made from improving u-value? Currently, I am approaching our build on the basis that walls would be 142mm + 25mm PIR to achieve a u-value of 0.15 and roof would be 142mm + 75m PIR to achieve a u-value of 0.11 but am wondering if I should be looking to improve the wall insulation further? Our property is not excessively large (~200sq/m total) so I am also conscious of trying to maximise room sizes. We are not going for Passivhaus but as this will be our 'forever home', I'm keen to ensure I'm building out house with the long term in mind. I have included a table below that we received from our SIPs supplier for visibility in case helpful. Thanks in advance. Walls U-Value Table Roof U-Value Table Walls + Roof Summary -
Hi all. New member to the forum (intro post here). Currently looking at MVHR and am trying to determine whether rigid vs flexible ducting is "better" when starting with a new build. So far the school of thought seems to generally be that rigid is more hygienic/longer lasting but comes at the cost of price/slightly harder to install. A salesman was laying on the fact that all Passivhaus certified equipment is tested using a rigid setup (verifying this is the recommend setup), but unclear if this is true and accurate. I don't want to hear it and wondered if rigid was 'quieter' than semi-rigid? Any thoughts or feedback much appreciated.
-
Thanks all for the warm welcome and @Nick Laslett for the helpful suggestions. At risk of breaking the rules, a few responses/questions to your comments (mods, let me know if I need to move this to individual threads or via PM if you wouldn't mind Nick): 1. Insulated slab foundation. The primary issue for our delayed start date has been structural, due to the elasticity of the soil and close proximity to a very large oak tree (we are building quite far into the root protection zone - surprised we got planning in the first place!). As a result, I'm informed the floor needs to be beam & block so assume insulated slab is not an option? 2. UFH in slab, not screed Same here I assume, for the above reasons? 3. Proper ASHP configuration. People like HeatGeek on YouTube are now advocating this stuff, but back on 2018-2019 BuildHub was already there. I have an insane quote from a Heating company in 2019 pricing my ASHP/UFH set-up @ £40,000+. I would be surprised if my ASHP/UFH install cost me more than £5000. I've watched a lot of the HeatGeek stuff and the computer nerd in myself was really impressed with what they do. Would you recommend going through them direct or shall I head to the ASHP forum to source recommendations in the West Sussex area? 4. Going from resisting MVHR, to embracing it. The sooner you incorporate the MVHR ducting solution into the fabric of your build, the easier things will be. Every structural decision needs to accommodate how the ducts are going to route through the building. Embracing! We're currently going through the technical design of our building so am keen to appoint an MVHR designer so we can do exactly what you suggest. I'm still researching whether rigid vs flexible ducting is "better" when starting with a new build. So far the school of thought seems to generally be that rigid is more hygienic/longer laster but comes at the cost of price/slightly harder to install. A salesman was laying on the fact that all Passivhaus certified equipment needs to be tested in a rigid setup, but please let me know if I'm barking up the wrong tree. 5. Ducting requirements for ground works and in the slab. The insulated ASHP pipe is a particular pita to install. Assume the same issues for the block & beam reasons here. 6. Getting an electrical supply kiosk/water supply as soon as you own the land. All these services can be changed by you later in the build without involving the infrastructure companies. Great advice. I've already had a price to install electricity to the property and RE: water, due to the fact we are off the grid, we pull this from a borehole so am arranging for a tap to be installed on the land. 7. Do your own heatloss calculation using Jeremy Harris’ spreadsheet. There is also a great MVHR calculation spreadsheet, but this might not be as robust. Just downloaded: first thought was a little overwhelming but it appears primarily just entering values into the white boxes. One of the issues I'm experiencing with steel doors is that they don't appear to have an associated U-value, they are all just stated 'Energy Rating B'. I'll take a more detailed look at the spreadsheet though - thank you for the suggestion. 8. Manifold approach for domestic plumbing. Also hot return, if applicable. 10mm pipe for certain outlets. I did all of the plumbing in my build, this was only possible because of the discussions here. The manifold photos are just eye candy to me now. Am estimating that 3 manifolds will be required and have given some thought to where they will be located (one in the kitchen/diner, one in the cupboard on the landing, potentially one in the HWC cupboard). RE: hot water return, does this refer to a hot water circulating pump? I would love to have hot water on demand in all the bathrooms in order to avoid the dreaded 'warming up wait'. Thanks again.