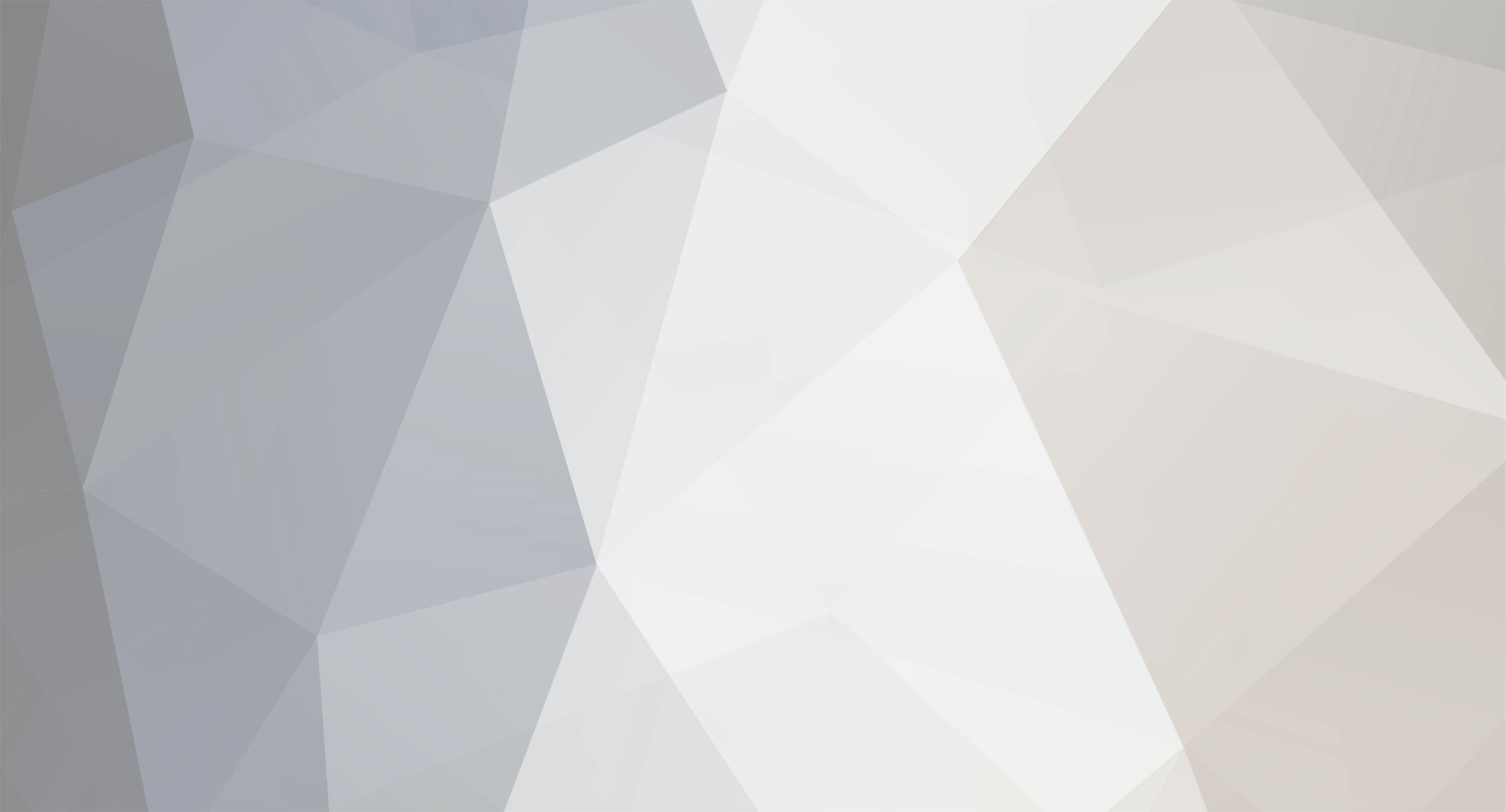
Sunil237
Members-
Posts
48 -
Joined
-
Last visited
Recent Profile Visitors
The recent visitors block is disabled and is not being shown to other users.
Sunil237's Achievements

Member (3/5)
12
Reputation
-
Hi all, An unfortunate update! Help requested. The council have responded to say this is an issue and have asked us to either remove part of the roof that's been built or put in a homeowners application for retrospective approval. Details below of why they are staying the 1m roof overhang should be counted into the measurement... We had approval for 6m. The wall is out to 5.7 and the overhang brings it to 6.7. although the council see no issue if we built to 6m and had a 30cm facias/soffit. Council explanation; "I would agree that the provision of a slight overhang to form a soffit or fascia would be considered a de minimis protrusion for the purposes of measuring a Class A extension. However, I cannot agree that the overhang in this instance can be considered slight, minor or de minimis. The roof oversails the extension by 1 metre and is not considered necessary to accommodate finishing materials or guttering etc. Page 4 of the Technical Guidance makes it clear that “given the very substantial variations in the design of individual houses, this guide cannot cover all possible situations that may arise” and does not specifically address the matter of roof oversails" Essentially, based on whoever id judging they can make up any rule according to the line stated on page 4. My architect used the points discussed in the first post but the council didn't budge. Additionally they said we need an application to cover the whole build and not just the roof as the roof forms part of the extension and that means the whole extension is not permitted. I've asked my good neighbour to submit a positive comment when the notice comes through. I had reviewed the councils guidance on planning enforcement (https://www.charnwood.gov.uk/files/documents/enforcment_policy/CBC Enforcement Plan May 2024.pdf) and i am struggling to see how their actions can be justified based on their "harm" scoring (page8) of my additional 0.5m overhang. Any advise would be appreciated, and any experience in requesting fit a different planning officer to review Thanks
-
Window removed but no lintel on outer leaf
Sunil237 replied to Sunil237's topic in RSJs, Lintels & Steelwork
I was thinking to just drill out all the mortar, 150mm either side of the opening and place the angle in from the outside face as the cavity is 50mm, and use a dry mix packed tightly above and below the lintel. Any issues or better way for a DIYer? -
Window removed but no lintel on outer leaf
Sunil237 replied to Sunil237's topic in RSJs, Lintels & Steelwork
There's definitely no lintel, I knocked off a bit of mortar to check. There is a concrete lintel on the inner wall. @Canski, it's stood firm with no cracks through the full extension build somehow without failing! 2 more days with no activities should be oka. Haha famous last words I went to a builders merch and they did recommend a steel angle lintel. So I'm going to put that in on Monday -
Glad my post came in useful, unfortunately I can't give any experience based insight as I've not lived with my system yet! I think you're making the right choice with the 15mm hot feed. I just didn't have the will left to argue with the plumber.
-
Hi folks, We had removed a window from there rear to create the entrance to the extension and there's actually no lintel in place. Oddly enough the opening has been fine for a month with excessive work taking place as we've added a flat roof above it! I wanted to make it right though, just wanted to get thoughts on what to use It's a 2.7m opening with a 50mm cavity and 100mm brickwork. I am hoping to use an angle iron on this external face, remove some mortar and just dry-bed it into the each side by 150mm - easiest DIY option Alternative would be to remove 1 corse of bricks and replace with a concrete lintel or a steel box As the plasterer is looking to crack on on Monday I'd like to get this done this weekend Any thoughts?
-
Glad to return some help 😅 My plumber said the bracket fit nicely on the 15mm manifold, but he had to use longer screws for the bracket holding on the 22mm manifold as it wasn't designed for that size
-
Thank you @Nickfromwales @torre and @JohnMo We've completed first fix and I'm super pleased with my water set up ☺️ As I have a joist in the room I can actually box off the pipework, keeping it fairly neat. I used hep2o manifolds with built in isolation, and regular branching at each room. The plumber wasn't so convinced that the manifold system will help any but did like that we could isolate the outdoor taps in winter. I used 22mm and 15mm hep 90 degree bends which the plumber found more useful than he thought they would be. The manifold bracket looks to have worked great! I see others used Munson clips but I bought the manifold mount just to try. I realise I've gone against advise here and have 22mm for the hot! Things just got done and I didn't catch on until a bit too late My components 15mm manifold (2 port, available in 2,3 &4) 22mm manifold (single port) Manifold mount 15 & 22mm 90 degree bends 3/4 iron to 22m compression 90degree manifold cap My plumber changed the end fittings over
-
They don't have an issue with the build being smaller, it's safe to assume a smaller extension has less impact on amenities of neighbours so they use discretion to not pursue that I don't know what you mean by "optional CoL" sorry I have seen that some LPAs ask to see elevations and also roof plans for more information but mine only asked for a location and block plan. Would a block plan typically only show the outline of a building brickwork or do they tend to include the facia and guttering?
-
No drawing was supplied as it was prior approval for a larger home extension, classing it as permitted development. The application stated: "Erection of single storey rear extension extending beyond the rear wall of the original house by 6.00m, with a maximum height of 3.40m, and height to the eaves of 3.20m" There was a neighbourhood consultation as there was a comment made but the conclusion is below "Conclusion On the basis of the above assessment, the Prior Approval of the LPA is therefore not required. The proposed single storey rear extension will comply with the relevant conditions and limitations of the Town and Country Planning (General Permitted Development Order) (England) 2015 (as amended) Schedule 2, Part 1, Class A and qualifies as ‘permitted development’." The only drawing submitted was the blockplan which shows the build out to 6m. @Big Jimbo thanks, I will definitely wait to hear back rather than force the matter. Just want some peace of mind and to be prepared as the fee for a retrospective application (if it gets that far) is going up by £300 in April
-
Hi all, I have a prior approval for a larger extension on a detached house. The extension has been built to 5.7m (to rear wall face) with an overhanging flat roof of 1 meter. The architect put in for a 6m extension as they believed the roof doesn't count towards the request. We should have gone to 8m for more coverage and are kicking ourselves for not! The neighbour did object the application, and the planning officer found zero issue in approving the application. Anyway within a week of the roof being on the neighbour has called the council (I assume) and the person who came to see said the overhang counts towards the limit as it's not a normal size, so we are 70cm over. I am expecting a letter/email from the planning dept soon. So far my research has led me to this technical guidance for permitted development and looking at A, G, ii https://www.gov.uk/government/publications/permitted-development-rights-for-householders-technical-guidance/permitted-development-rights-for-householders-technical-guidance#other-classes-under-part-1 It says "Measurement of the extension beyond the rear wall should be made from the base of the rear wall of the original house to the outer edge of the wall of the extension (not including any guttering or barge boards)." And has this nice little picture Is my understanding correct and are we safe or should I be worried and what would be the next best steps? Thanks!
-
The roof is currently going on but I see leaks, thankfully for the rain!! It's part built so I'll explain where they are at with it, and I would appreciate some advice on the rectification work needed Warm flat roof; Joists on, furring on, osb on (glued and screwed), vcl (alutrix 600), 150mm celotex (glued down and foamed together), osb top layer on and screwed down. They have laid dpm to protect the roof, but I gave seen two areas with leaks coming through because they have missed the joist Will be very hard to see from a picture but I've added one. It's a constant drip.
-
Steel beam installed - padstones look tiny....
Sunil237 replied to Sunil237's topic in RSJs, Lintels & Steelwork
Yes roof has gotten started, joists boards and insulation are all on.. but there's leaks as they've missed joists when screwing down the osb 😭 Rectified padstone work is on the picture here, and so far it's extremely level! +/-5mm over the 6.3m span Pads were still slightly wrong which the bco picked up on, but the structural engineer verified it was ok. So they used slate instead of steel shims and they were positioned wrong, pads not central but 160mm on the stone minimum -
Steel beam installed - padstones look tiny....
Sunil237 replied to Sunil237's topic in RSJs, Lintels & Steelwork
Thanks Canski and all! All rectified -
Steel beam installed - padstones look tiny....
Sunil237 replied to Sunil237's topic in RSJs, Lintels & Steelwork
Thanks, they've agreed to change out. How long should they leave them propped up whilst new padstones set?