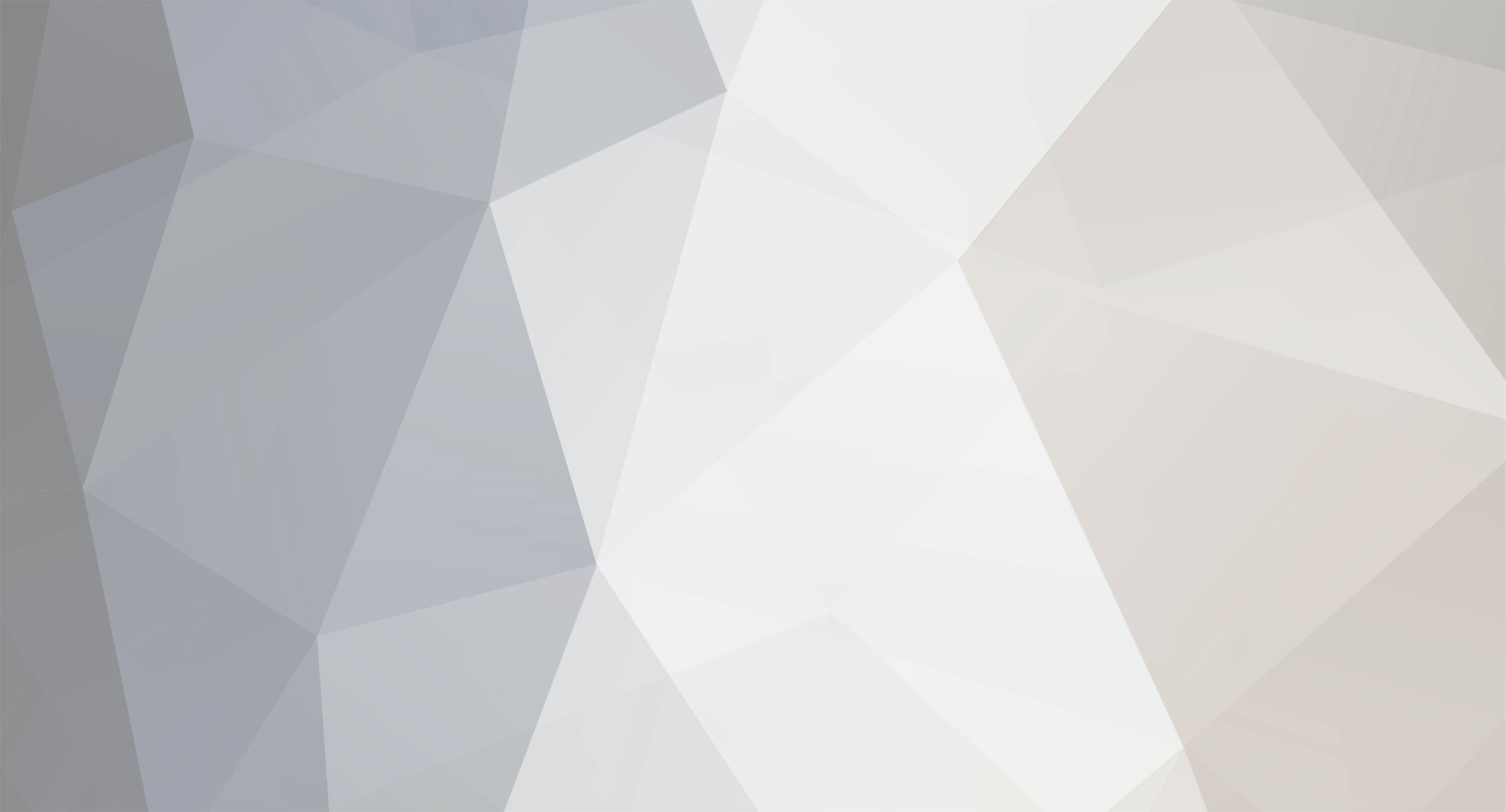
Colink
Members-
Posts
16 -
Joined
-
Last visited
Recent Profile Visitors
The recent visitors block is disabled and is not being shown to other users.
Colink's Achievements

Member (3/5)
1
Reputation
-
A family member has had new manufactured quartz worktops installed 1 month ago. Worktop now has about 8 pinholes some the size of a pin head). See image and short video attached Is this to be expected and is an epoxy repair an acceptable solution or should they be demanding a new worktop? quartz-worktops-holes2.mp4
-
@Alan Ambrose My mistake. I was looking for a way to add rows before entering the first 4 To answer part of my own question to @Mr Punter I see that adding plywood or OSB makes little difference and does not get to 1.8. Building control were a little vague on what exactly they required for upgrading the original wall. (In a helpful way) suggesting that it might not be required in certain circumstances. I am planning to send the calculation to building control and ask if they will be ok with this 1.95 in main house but that we use 75mm or thicker in the garage conversion which brings it down to below 1,7 and 100mm+ for a future extension. Note Garage is same construction and insulation as main house. Any comments or corrections welcome
-
@Mr Punter Thanks for your reply (including your comments about sealing the vapour barrier” and for doing the calculations for me. i signed up to Ubakus but having difficulty recreating your table. I only see 4 rows and cannot see how to add? Maybe I cannot with a free account. ==== I am not sure exactly what Building Control will want to enforce. From my brief online reading I see numbers of 0.18 for upgrading an existing building. Assuming we are already committed to 50mm foam (some already fitted ) and need to get to 0.18, what else could we add between battens and plasterboard eg plywood (or some other sheet) vs buying insulated plasterboard? note, the batten depth is 50mm but I assume that will not be sufficient.
-
I am not a plumber so feel free to tell me if I am incorrect in anytingng I describe or ask. My son is adding additional internal 50mm foil backed insulation to all internal walls of his 1890's timberframe hosue + a vapour barrier. Insulation supplier has calcculated minimal consensation risk to existing vapour barrier. He will also be completely replacing the whole the heating system - either Oil Boiler or Air Source Heat Pump (grant ddependent) + new radiators. He plans to add HEP2O below the bottom horizontal battern before adding plasterboard and plaster. - see attached image I would appreciate a comments on what insulation, if any should be applied to the HEP2O pipes. He is already losing some room space and keen to make battens as thin as possible. Would minimal insulation wrap around the pipes plus insulation above the pipes (below the batten) be sufficient?
-
@SteamyTea I have two question in this post - the remainder is sumarising what we will be doing. Thanks again for your input. I note your comments. I have passed on your recommendations about removal of existing plasterboard and insulation. For better or worse he has decided he will not be doing that and will be doin as per my new diagram attached. Subject to agreement with the plumber heating pipes will be going horizonatally along 3 bedrooms on one side of the house. Similar on the other side. Building control have told us to follow the guidance of the insulation manufacturer. The insulation manufacturer have also recommended removing existing insulation and plasterboard, but have also given their recommendations for insulating on top of the existing plasterboard. They have carried out calculations and determined there is very a low risk of condensation subject to adding a 1000 gauge polythene vapour control layer on top of the insulation. Even though @Redbeard and @ProDave (I think) suggested tapiing the joints we will need to follow the insulation manufactureers recommendations to keep building control happy. I am assuming taping the joints will be of no additional benefit - happy to be told I am wrong. QUESTIONS Q1 - what is the most cost effective sealer / adhesive to seal the vapour barrier against the new insulation? Adhesive tape sounds expensive, I assume some gun applied sealer or adhesive will be the easiest method Q2 - Should it be sealed / glued on the back against the insulation, or cut to the exact size and sealed around all four sides. Note - Given that we will probably be adding horizontal battens, including one at the very top (see image) the top edge of the vapour barrier will be sandwiched between the batten and insulation (presumably with sealer or adhesive between it and the insulation. I assume we will then trim the sides of the vapour barrier while being held by the top batten then sealer or adhesive (Q1) applied behind the edges or on top of the edges. Plus some more battens. Back to SteamyTea's response He will be using 50mm foil backed insulation + the void for the heating pipes. Taking into consideration your comments about insualtion he is aware he will be taking 100mm plus out of the room width.
-
@SteamyTea Thanks for our input - My son has decided to keep the existing insulation and plasterboard and follow the procedure discussed in the early part of this thread @SteamyTea @ProDave @Redbeard I would appreciate your comments on this (hopefuly) final image and answer a question about Vapour Barrier The attached image shows two possible locations for pipework. My son plans to go with the second version where pipes go along the bottom of the wall along 3 bedrooms. I have noted the importance of taping the joints of the insulation to make a good vapout barrier. Buiding Control mentioned the possibility of a plastic vapour barrier (not sure if he will want to enforce this if he is happy with the taping). What are your thoughts on taping + plastic sheet vapour barrier? Any negatives of adding the plastic vapour barrier? Someone locally mentioned the possibility of condensation forming on the plastic vapour barrier, however as it will be on the inside of 50mm insulation I assume both sides of it will be close to room temperature - hence no condensation issue (if fitted) - Comments? Any other comments would be appreciated.
-
@SteamyTea Thanks for your imput. In your description where does plumbing and wiring go (in what order)? The current insulation is fiberglass. Are you suggesting increasing stud depth and adding thicker fiberglass? Do we still add foil backed insulation. Maybe it would be easier for me to understand if you listed items / materials from the sheathing out to plasterbaord?
-
@Redbeard Thanks again for your input. I had been thinking about removing existing plasterboard and VCL. Ref order of insulation and plasterboard. Original diagam was done beforeI had thought this through and before your original reply + my type regarding "standard Insulation board". I think this new diagram is what you describe (but may remove original plasterboard and VCL). If I am wrong please advise. If you have any general suggestions or links regarding using external insulation I would be keen to read.
-
@ProDave Thanks for your reply and confirming insulation, battens, (service void) palsterboard would be the best solution - as I thought. I assume we can figure out where existing joists are located and mark the position so the new battens line up. We have given no thought to external insulation type or structure at this stage. I am assuming it will be more cost effective buit more costly. Any suggestions or comments would be appreciated. One more note - my son is a joiner so is capable of doing all the labour for this work, but would need to get the correct instructions to ensure that EWI is installed correctly.
-
@Redbeard Thanks for your detailed reply. I note your recommendation for external insualtion and condensation risk analysis. We are still considerign external insulation. I realsie we need to get local professionsl advice on this before implementation, however your replies are helping me to be more informed and be better placed to help find the right person and to ask the right questions. One additional consideration. At the same time as this work the property may be upgrded with a heat pump + new radiators, replacing the oil heating which does not work. (No Gas option). In order to get sufficient water flow to the new radiators it is liley that new 22mm heating pipe will be needed. Assuming we want to hide this pipework as much as possible I see two possibiliries to include when the new insulation is added. 1 (See right image below - left image is what you described - I believe) Add 25mm stud to the existing plasterboard, then the new insulation (green) - tape all joints then the standard plasterboard. New 22mm pipewoek goes behind the insulation 2 (no diagram) - New insulation on top of existing plasterboard (taped joints), 25mm stud + standard insulation board. 22mm pipe between new insualtion and plasterbaord. I am assuming 2 is the better thermal solution, however I am not sure how easy or difficullt it wil be to find fixing points for the 25mm stud. Any comments from you or others would be appreciated..
-
My son owns a 1980's Timber Frame bungalow . Structure is same as attached image. He is currently converting the attached garage to 2 bedrooms. The garage is already insulated, with fiberglass between the studs - same as the house. The house is unoccupied and with no furniture and he has easy access to all the walls in the house. The Northern Ireland Building Control inspector has mentioned that the insulation is probably not up to modern specification and would need to be upgraded. I believe he was correct that by adding additional internal insulation (on top of the internal plasterboard) could cause condensation to form on the plastic vapour barrier, behind the plasterboard, due to the lower temperature on the outside surface of the vapour barrier. The most effective solution is probably to add external insulation, however that will likely be more expensive and could end up with the garage part the house having a different finish to the rest of the house (not the end of the world). Is removing all internal plasterboard and the vapour then adding new insulated plasterboard a possible solution? However that means no vapour barrier - what effects would that have? Is there a better solution? The issue is further complicated by a comment from the Building Control officer that suggested there might be a requirement to upgrade the insulation for the whole building, however that would be a lot more work and cost. I am not fully clear on the reasoning for needing to upgrade the insulation of the whole house (I think it was due to him also requiring building control to upgrade the heating system). I need to call the inspector for clarification, but I want to be more clear on what is a suitable insulation solution for the garage or the whole house before I ask more questions. Any guidance on the most efficient / cost effective way to upgrade the garage or whole house insulation would be appreciated.
-
Concrete Window Sill repair - Concrete or Epoxy? - Cost?
Colink replied to Colink's topic in Bricklaying, Blockwork & Mortar
Any feedback? -
Repair render crack, partial or whole section
Colink replied to Colink's topic in Bricklaying, Blockwork & Mortar
Thanks for the comments. -
Repair render crack, partial or whole section
Colink replied to Colink's topic in Bricklaying, Blockwork & Mortar
Typo = last sentence should start with "If a partial repair ..." -
Any thoughts on which repair would be better for the broken corner of this window sill? Concrete or Epoxy repair? Any other suggested repair s? I assume in both cases screws would be drilled into the sill and the new concrete or epoxy built around the screws. Any ballpark cost for this repair? Thanks ColinK