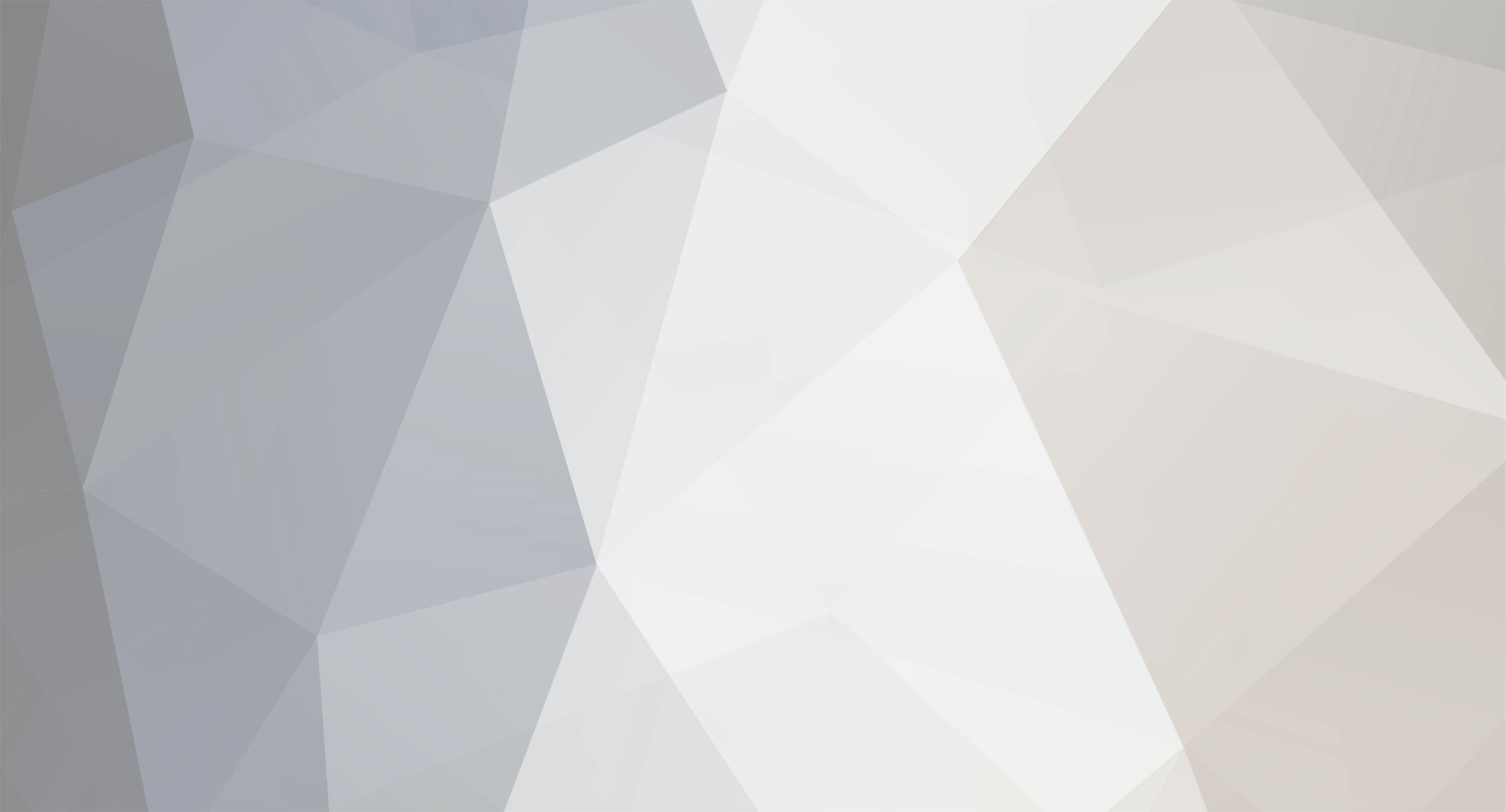
James1234
Members-
Posts
24 -
Joined
-
Last visited
Recent Profile Visitors
The recent visitors block is disabled and is not being shown to other users.
James1234's Achievements

Member (3/5)
1
Reputation
-
I am about to start work on my garage and my planned construction is timber frame with a masonry outer skin. One section of the garage is tight to a boundary wall so ideally I would erect the masonry external skin and then construct the timber frame inside it. The problem I see with this approach is being able to install the wall ties. As far as I am aware wall ties in a timber frame need to be screwed into the timber and then the cladding constructed. My back up plan is to make the inner skin blockwork in this section but thought I would ask to see if anyone knew of a method of tying the timber frame to an already constructed masonry skin.
-
Buffer Tank Hot when Heating Mode Turned Off
James1234 replied to James1234's topic in Air Source Heat Pumps (ASHP)
A fairly unsuccessful discussion with Daikin yesterday.. in summary they think the current install is very good and changing the ASHP to a smaller unit and removing the buffer tank would have a negligible impact on efficiency. Any recommendations for system designers that I could get contact to come out and review the system and give me some expert opinion to go back to the installer with? I am half an hour North of Bristol? Thanks in advance! -
Buffer Tank Hot when Heating Mode Turned Off
James1234 replied to James1234's topic in Air Source Heat Pumps (ASHP)
Thanks for the reply @JohnMo, depending on how things go this week I will see which of your steps I need to take, but I think that all makes sense as a way of making the current set up work more efficiently. I don't have this... I have two upstairs and two downstairs. I mentioned one in every room as this is what the designer said was a requirement of MCS..... but then acknowledged that he didn't follow that for my installation as it was over the top. -
Buffer Tank Hot when Heating Mode Turned Off
James1234 replied to James1234's topic in Air Source Heat Pumps (ASHP)
Thanks you @JamesPa, some useful thoughts from you there. Following discussions with the installer and the Daikin approved designer at the plumbers' merchants, a technical person from Daikin central is coming out to review the system. When I asked the designer why I ended up with a 96l buffer rather than a 20l volumizer as designed by him he said the company which did their MCS sign off liked buffer tanks and they had a 96l one in stock.... great. When I quizzed the designer about why I haven't had an open system installed he said that MCS requires a thermostat in each room and therefore an open system isn't allowed under MCS. Looking through this guide https://mcscertified.com/wp-content/uploads/2020/07/Heat-Pump-Guide.pdf it seems like there is talk of needing a thermostat in each room (which the designer acknowledged is over the top) but the below section talks about a continuous system, @JamesPa I guess your post above talking about 24/7 systems with thermostats as temperature limiters ticks both section 6.1.2.3 and 6.1.1.2 A helpful section from the guide on buffer vessels is in 11.1 I will post an update following the discussions with Daikin this week -
Buffer Tank Hot when Heating Mode Turned Off
James1234 replied to James1234's topic in Air Source Heat Pumps (ASHP)
Just looked on a supplier website and indeed the 9kw - 16kw units all look the same with the same 3.8kg refrigerant charge but the 7.5kw and below are a different looking unit with 1.35kg refrigerant charge. So yes, looks like you are correct @JamesPa It has only been running for 3 months, from the Daikin controller 114kWh electricity used, 351kWh heat produced = 3.07 -
Buffer Tank Hot when Heating Mode Turned Off
James1234 replied to James1234's topic in Air Source Heat Pumps (ASHP)
The plumber has put in what is shown in the photos but has not followed the drawing which calls for the volumiser. The logic behind the 4 zones is upstairs and downstairs, old (less well insulated) part of the house, new (better insulated) part of the house. It was a discussion the plumber and I had but it sounds like he was no better informed than me in that conversation.. I will have some discussions with the various parties and will do some more digging and get back to the thread with progress. Thanks once again for all the advice, very much appreciate. -
Buffer Tank Hot when Heating Mode Turned Off
James1234 replied to James1234's topic in Air Source Heat Pumps (ASHP)
Thank you @SteamyTea, @Nickfromwales, @IGP and @JohnMo I clearly have some things to unpick. Are there any industry standards or Daikin best practice that I could refer to when opening up discussions with the plumber? There seems to be such a wide range of opinions out there. If I was to get someone in to review the system who would you think would be best, Daikin Technical, Daikin Approved installer, Heat Geek approved installer etc? If I go back to my initial question "should the buffer tank get hot when the space heating is turned off?" It sounds like no, and the plumber's explanation of "the buffer tank is need for the ASHP to wind down after heating the DHW cylinder" is incorrect. The selection of the heat pump was done by the Daikin rep at the local plumbers merchants. He calculated a 6kw unit was needed but as they didn't have any in stock supplied a 9kw unit at the same price. I had a lengthy phone call with him at the time questioning this and he said the 9kw would be able to work at a lower temperature and therefore work as efficiently as the smaller unit. Interested in your opinions on that as well. -
Buffer Tank Hot when Heating Mode Turned Off
James1234 replied to James1234's topic in Air Source Heat Pumps (ASHP)
Thank you all for your help on this, it is really appreciated, as is the wider Buildhub, I have used it a lot for ideas, guidance and support during my build. Sorry to take a while to reply, I was keen on getting the best photos and making them up clearly to make things as simple as possible. Below are a set of marked up photos showing closer up images of the system (one which shows before the insulation and solar inverter went in). The temperature of the buffer tank is over 42 degrees (my Boots thermometer stopped working at that point because it thought the patient was suffering sever heat stroke). -
Buffer Tank Hot when Heating Mode Turned Off
James1234 replied to James1234's topic in Air Source Heat Pumps (ASHP)
Will get some more photos when back home this evening. Heating is turned off at the 4 thermostats and also selected on the black controller which I am told talks to the ASHP (you can select to turn off the DHW tank, set times that the DHW is heated to suit lower electricity prices etc. -
Buffer Tank Hot when Heating Mode Turned Off
James1234 replied to James1234's topic in Air Source Heat Pumps (ASHP)
So would you say the drawing is a correct/proper setup? But the plumber hasn't installed what has been designed? -
Buffer Tank Hot when Heating Mode Turned Off
James1234 replied to James1234's topic in Air Source Heat Pumps (ASHP)
Pipework to the manifolds is not getting hot, just the buffer tank itself. -
Hello all, moved into our extended/refurbished house a couple of months ago. We have ASHP (Daikin unit), hot water cylinder and buffer tank. The space heating has 4 zones in the house (upstairs/downstairs, old house/extension). The system was designed by the Daikin rep at the local plumbers merchants, install by local plumber and signed off by separate MCS certifying company. I am not 100% convinced that everyone in that chain has done what they are supposed to as when I quiz one they refer to the others. If I was doing this again I think I would have taken a different route. We are getting hot water and in the colder months heating was working fine. Now we are into summer I have put the master controller into 'heating off' mode. My understanding was the buffer tank was just associated with the space heating and would therefore be cold when the space heating was off, but it has remained hot. I quizzed the plumber who installed everything it who says that the buffer tank is used when the DHW tank had got up to temperature to allow the ASHP unit to wind down, as it couldn't turn off straight away. Seems wildly inefficient to have a tank of hot water sitting there for 6 months of the year. Interested in other people's thoughts and suggestions. Plumbing drawing and photo of installed system below. Many thanks. James
-
Hello, looking for some pre-made drawers for some built in wardrobes that I am going to make. I like the idea of oak drawers and so far I have found https://www.interfitco.com/oak-dovetail-drawer-boxes/ https://www.bullerltd.co.uk/oak-drawer-box.html?variation_id=8699 https://www.evabox.eu/en/drawer-boxes/ I am not looking to put fronts on the drawers, just have the oak boxes (Evabox will supply with dropped fronts for handles or I could cut the into the others myself). Wondering if anyone has any experience of using any of the above options (particularly Evabox as they would be coming from Lithuania so a longer lead time etc) or can offer any alternative options.
-
Similar costs from a few different suppliers. I hadn't found Specialist Blinds so will try them. Thomas Sanderson, Appeal Group, Sona, Grand Design Blinds, are some others. Seemingly all offering similar things at similar price points. The mounting and recessing of the blinds is a key detail. The video of the Sona Blind posted by MR10 above is a very neat solution but not suitable for our arrangement as we have a section of wall above the window before you get to the ceiling. I can see the point about the central mullion but the example in the above video seems to cope well without it. Depends a bit on how close to the window the blinds will be. If they are forward of the window I guess light will bleed around the mullion a bit anyway.
-
The sensible approach, but the structure is built and windows are ordered so we are committed to the window shape. We knew what we were signing up to at the time... just hoping that someone had discovered some great alternative....