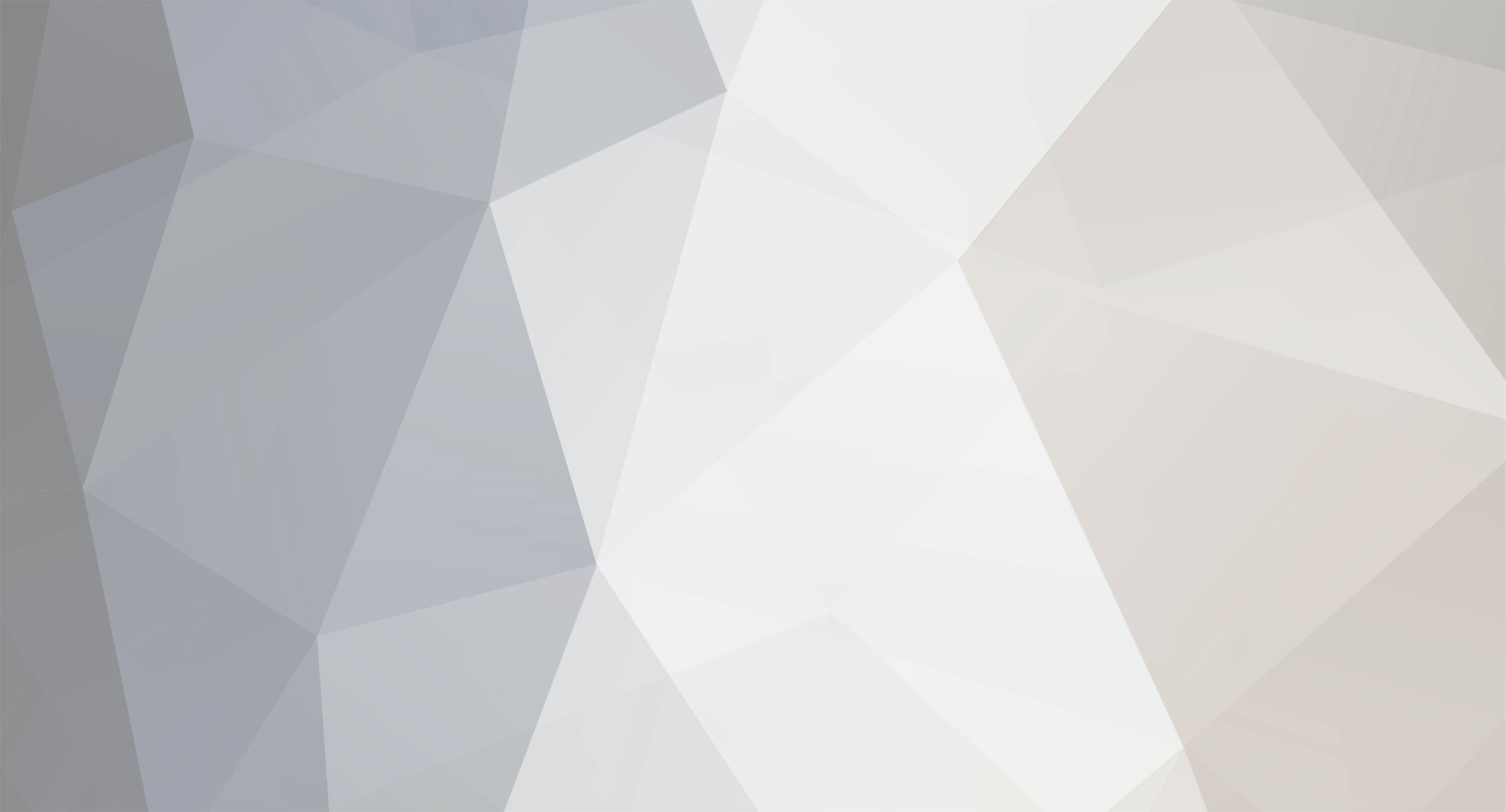
Pabbles
Members-
Posts
31 -
Joined
-
Last visited
Everything posted by Pabbles
-
Hi all. we're ready to break ground on our new detached garage. It's a whopper: 11.7m x 8.2m. Steep learning curve - but the raft, the cavity walls and roof truss structure (19.88-degrees with a vaulted area for a car lift) have all been designed and quoted. But I'm completely stuck on the roof covering. it's over 100m2 so cost is a major problem and is keeping me up at night. I've considered natural slate to match the house, Brimet Liteslate (plastic slate effect tiles), Marley Edgemere Riven (concrete slate effect tiles) and lately old school roofing sheets. A second problem is finding a roofer - it's a struggle finding one with availability, let alone one with transparent pricing. Ideally I want a quote for all four roofing systems with material costs shown so I can make a decision, but it's not reasonable to ask a tradesperson to produce four quotes. I'll be using the garage as a workshop, with some high-end machine tools so condensation and noise escape is a big worry. Does anyone have any suggestions for a sensible roof choice? Rules of thumb on price comparison would be very welcome too. If its not insulted then I'd like the ability to add simple insulation (Rockwool or Kingspan) later - without spending a king's ransom on plywood sheets to support the insulation. Really welcome any pointers that could get me back towards budget. Image from design attached with visible trusses.
-
Looking for foundations detail and cost reduction advice - detached garage
Pabbles replied to Pabbles's topic in Foundations
Thanks both - that's really helpful. So, going off @ETC's point then from the above if the building was just used for periodic storage then DPM may not apply. However in this case, the building will be used extensively (starting at 1000 hours a year and moving up towards 2000 hours as I hit retirement and contains a lot of expensive machinery. It really is an obsession of mine. As such I'd really like to have a good level of protection against moisture ingress so would stick with DPM. @Roger440. Mate, I owe you a pint. The lift manufacturer I had planned to use (TwinBusch) specified 200mm of C20/C25 concrete. However you are quite right, most alternative manufacturers specify 150mm (granted, as a minimum) even for higher capacity lifts. As such, you've just saved me a 25% of my concrete costs simply by picking another lift. Thank you! -
Looking for foundations detail and cost reduction advice - detached garage
Pabbles replied to Pabbles's topic in Foundations
@markc I'm going off the specs for the 2-post lift. Some of my vehicles weight close to 3 tonnes. The lift manufacturer specs 200-250mm of reinforced C25/C30 concrete as a base. A failing 2-post lift is a scary thing. They do offer a drawing showing how to lay a H-pattern of thicker concrete in strategic areas as you suggest, but I haven't yet been able to compare the costs of the additional shuttering/layout for a deeper H shape vs just doing the whole slab in 200mm. @ETC I thought that was standard practice? Am I missing something obvious? -
Looking for foundations detail and cost reduction advice - detached garage
Pabbles replied to Pabbles's topic in Foundations
Thank you. Yes - my ideal is to be able to draw up all three options so that I can work out the material costs for each. I won't be doing it myself, I have a great builder - we work well together but the quotation phase is always tricky. We've found a good pattern where I plan everything out to Nth degree, cover materials costs and then he quotes a healthy but transparent labour price that keeps his margin safe but means I'm not paying over the odds. -
Hi everyone. My head is spinning. I've just spent an hour on Google trying to find a detailed cross section of a suitable foundation for my new garage build. I've seen loads but can't seem to find one that is a close match for our build. The plan is attached. The only thing to add is that the floor slab will be quite thick at 200mm, reinforced (specific requirements for the vehicle lifts). Construction is 65mm Imperial Olde Shire facing brick with 7n dense blocks on the inner course with a 100mm cavity. SE has advised a depth of 1.3m based on findings from test holes. But frustratingly did not fully detail construction before we parted ways. It is quite a long length of foundations at 39m so I'd like to be able to draw and then cost up options for trench fill, trench blocks and dense block as a few pounds a metre could quickly add up. Does anyone have. nice, well proven cross section they could share? Ideally looking for one with detail on of block/brick types at each course and positioning of DPM/cavity tray. Any advice on how to keep the costs down given current concrete prices would be very welcome. I already know I'm going to feel silly when someone links to a blindingly obvious place, but I would really welcome the help as my Google and NHBC kung-fu is failing me.
-
Thanks Russell. Yes - it’s a bit of a dream of mine. We bought the house specifically because the layout of the land lent itself to a lot of outbuildings under PD (about an acre in an L shape with no neighbours). Our local authority planning team have been overwhelmed for many years, even the pre-planning advice team is shut down, so this design is quite specifically chosen to sit within permitted development regs (2m from boundary, 4m ridge, 2.5m eaves and less than 50% of the curtelage) so that we don’t need planning - but do need building regs. Seems ridiculous we can build something so large, but that’s the law. I'm a quite passionate classic car builder so the garage is a real workplace for me. It will also have an office in there for my day job. We’re lucky enough to already have a dedicated gym building so no real need to go higher and we’re loathed to start going through planning. the brick facing is important as it ties in with the area (lots of larger barns of similar construction) so will help with resale if we ever sell (not expecting to recoup the full costs but, for example, a steel clad or rendered building would hamper not help the value). I’m very much open to ideas on how to reduce the costs while keeping the brick fascia if you have any? Solid wall is obvious but that’s more brick. Single skin would be cold and less robust. Softwood is out due to longevity. I would have looked at ICF if I’d been happy with render. Steel building was my first choice and they’re cheap… unless you want any sort of insulation at which point the price gets absolutely ridiculous and brings it in line with brick/block construction that will last far longer. Even oak was cheap compared to insulated steel. there is still a tight budget, but I think (subject to me planning every brick on CAD to remove the estimating contingency) we can pull it in on plan.
-
SUMMARISED (thanks @DevilDamo): You are all quite right, that post was far too long - I do apologise. It looked smaller on the laptop but was a tome when I read it back on my phone. So, for brevity: Question 1: when designing a brick/block building, it it better to set building dimensions based on full bricks, full blocks or full trench blocks? Answer: From @Russell griffiths: Base it on full facing bricks and cut the blocks to suit. Supporting answer from @George: Use the Weinerberger chart for standard brick dimensions. Question 2: From my drawing, do I need internal piers, external piers or both? Answer: Inferred from @George, not on the outer skin. Possibly not needed at all due to cavity construction. Did the roof truss company specify a pier under the two girder trusses? (its actually four, each pair is of double truss construction). No they didn't the whole design was shown sitting on the timber wall plate. Outstanding question: are there any published standards for the size/frequency of piers on the internal leaf of a cavity wall? Sensible thought, based off feedback from @George: putting 2x piers on each 11.5m wall (4x piers in total) directly under the girder truss pairs might kill two concerns in one. Question 3: do I need movement joints as the specs seem to say every 12-15m? Answer: from @George, probably not. Suggestions from @George and @Russell griffiths: consider the type of mortar chosen and whether to include bed joint reinforcement.
-
Hi everyone. I'm in the process of redesigning a detached garage, which we're hoping to start building in the coming weeks. After a few poor experiences with an architect, we (builder and I) ended up taking on the planning process ourselves. I owe him a redraft. We'll obviously run the plans past our private building control inspector before starting, but its a bit of a chicken and egg scenario: I need to finalise the plans to agree a price so I know we can go ahead... and then keep a little back for the inevitable alterations BC require, I have three tasks: 1) Rescale the drawing to suit standard brick and block dimensions (i.e. make it slightly bigger where necessary to reduce the number of cut brick/blocks required. 2) Consider the inclusion of block piers on the internal skin. 3) identify expansion joints. The high-level draft plan is attached - currently at a nominal 11.5 x 8m footprint. Construction is cavity wall over trench-blocks/engineering brick, with a 65 x 215 x 102.5 mm facing bricks and 440 x 100 x 215mm dense concrete blocks on the inner course. 100mm (97.5) cavity. I've been redrawing the building in CAD (my happy place) - have modelled every brick and roof component so that I can accurately assemble it on the computer and produce accurate drawings and materials lists. I have a few questions if anyone would be good enough to answer?: 1) When I try to rescale the building according to the brick and block dimensions, there isn't an obvious size. If I scale it so that the bricks don't need to be cut, then the blocks do need to be cut (and vice versa) and when I lay out the trench-blocks in CAD (440mm tongue and groove) then they always need to be cut to suit the blockwork above (the tongue and groove means no 10mm mortar bond on the sides which throws the standard dimensions out). I believe it is not possible to have a size that will suit all three brick./block dimensions and that there is therefore a compromise needed. Would anyone be good enough to suggest a size I should aim for (at or above the 11.5m x 8m initial plan) that would minimise the bricklaying labour in terms of cuts and adjustments? 2) We did have a structural engineer involved. This was due to an initially complex inner roof structure. His suggestions were OTT - more steel than Wembley stadium, we quickly moved to a truss design to avoid his doubling the budget. However he did suggest that the building needed four 440 x 140mm block piers on the inner course, one each on the north, south, east and west walls. The pier on the south wall (the one with the doors) was located offcentre, between the vehicle doors and the one on the North wall was directly opposite, again offcentre. The main purpose of these piers was to support some massive steel beams, which have since been removed from the plan (part vaulted ceiling to allow for a car lift, our local truss company came up with a much cheaper and more elegant solution - see the attached image from our CAD model, you can see the part-vaulted section clearly). So, while the piers are no longer needed to support the steels, I'm sure they would still be necessary due to the length of the walls. Can anyone comment on whether we still need all four piers of would two on the long walls only suffice? We have no issue with the cost of the piers, more that it impacts floorspace. 3) Finally. The structural engineer did suggest movement joints would be needed due to the span of the walls, but these aren't included in his drawings. I have read the designing for movement in brickwork technical guide but this seems to suggest that expansion joins are only needed every 10-12m (15m max) horizontally and 9m vertically. As such, it doesn't seem like they are needed. Could anyone offer any guidance here? Again, cost isn't a factor, rather in this case it is aesthetics. The building is being put up using reclaimed-style brickwork (newly made from Imperial bricks) and the styling is intended to mirror the local barns so we don't want to have visible expansion joints if they aren't needed. Many thanks indeed for reading and thanks in advance for any help.
-
Hi all. you know that feeling when you’re one bit of info, and a subsequent Google search, away from realising you’ve been woefully naive? Well…. that. We’re building two very large outbuildings along the back edge of our property. Architect drew the outline plans, we’ve picked a private building control firm and architect is now adding building control details to his plans for review. i’d assumed strip foundations of an unknown depth, say 1m, and then a cavity construction above DPC. building 1 is 12m x 9.5m and is a garage. Interestingly on this one, I would be specifying a high spec floor (250mm of C30 reinforced concrete) due to the manufacturer requirements of a twin post car lift that would be installed. Imagine this building as being a very pretty, but functionally industrial work space. building 2 is a 8.5m x 4.5m garden office and day room. So, had a chap out for an early quote on groundworks - lovely man and reasonably priced. He points to the massive row of trees that run along the property boundary (combination of hedgerows and a number of mature trees including tall old oaks). Asks how we’re getting around the foundation requirements for them. They’re around 5m from the proposed building edges. Quick google, realise how big an issue this is. The LABC calculator says that strip foundation depth at best would be 2.5m, if they’re even possible. I haven’t budgeted for foundations that deep - I’d assumed 1m. I have enough saved to build the buildings but this issue could kill the projects if the foundation cost becomes crazy. obviously, the first physical (private) building control visit will confirm how be a concern this is, but aim fearing the worst. there is one glimmer of hope: raft foundations. I’ve been reading about them and how they’re recomended for some soil types and some problem ground. But they don’t mention trees and roots: am I right in assuming that they would be a potential solution? If so, do I dare think that this could be a bit of a silver lining situation as a structural raft foundation would also meet or exceed the requirements of the 2-post vehicle lift too - in other words a simpler, quicker combined foundation and floor slab?
-
Hi folks. Out main house has a traditional slate roof and we're putting up some large outbuildings at the other end of the plot which combined have a roof area of over 200m2. The pitch of the roof is shallow, at just 17-degrees. We have done our own roof on a past project using interlocking tiles and would be confident of carrying out the roof fitment ourselves again if we were to use tiles - but if using slate then we'd hire the pros. Just hoping for some advice here. I think I right in my understanding that traditional slate is out in this application anyway due to the roof pitch being too shallow. I also understand that man made slate can be used down to 15-degrees due to its interlocking design. So, assuming I'm using man made slate tiles, can anyone recommend a brand? Looking for high quality, long lasting at a good price. The rest of the buildings are being built from reclaimed/reclaimed-effect hand made bricks and including common local features in order to make them feel like the 19th century barns and outbuildings coming to the area (south Cheshire). So I'm ideally looking for a man made tile that has an old appearance and looks as close to a real slate roof as possible. I understand these are made from plastic or concrete - concrete instinctively feels better too me as I want this to last for a long time and have had too many experiences of brittle black pvc failing or fading. Though I've I don't know what type of plastic is used for these tiles. If I could get some tips, then I'll go and get some samples on Monday. Thank you.
-
Hi everyone. project no.2 on our new development is to redevelop an existing garage into a high-end home gym. the garage is recently build and incredibly well made (cavity walls, oak framed double glazing, etc). It currently has a slate roof and traditional trusses. We’re tackling this one straight away and the bit I’m stuck on is the roof design. The trusses don’t work due to height restrictions and we’ll need to switch to a ridge beam and rafters to give us the vaulted ceiling. We’ll also most likely include some roof lights - the existing slates will be stripped and relaid. this is an embarrassingly simple question - but who do I call first? we have an architect but it seems a waste to go via him as I’m sure he’ll outsource the calcs. Do we go straight to a structural engineer? Or do some roofing suppliers do this in house, like they do with trusses. basically, I want a design that’s compliant with regs and is comprehensive enough for me to order materials before the roofers come out. or… so I just call a roofer and expect them to self-certify it all? (for context - in all the other works ongoing at the property I’ve been managing trades directly). thank you.
-
Turfcutter or similar tool - handy for laying slab?
Pabbles replied to Pabbles's topic in Garages & Workshops
Thank you everyone. Some really sensible advice there. I’ll look into buying a mini-digger, I’ll rule out renting one and operating it myself and will look into the costs of getting an operator to do the lot. Will then make a call. the turf cutter-type tool is firmly put in my ridiculous idea pile 😊 great tips re: moving the topsoil around the site - we do have some low areas so suspect I can lose it on the property. -
We have a fair bit of landscaping and building to do (a 12m x 9m oak garage, a large new gravel turning circle and a series of gravel paths) around a 0.5acre garden. obviously this means that we’ll need to dig down to various depths to allow for, in the case of the slab, hardcore, sand, membrane and concrete (the concrete would obviously be shuttered proud of the surrounding grass) and in the case of the gravel paths and turning circle membrane, MOT, gravel mesh and gravel. in either case, I’ll only be going down about 150mm consistently across a very large area and winding new pathways through what is currently flat level grassed lawn. now obviously a groundworks company can do this, but the quotes I’ve been getting are preposterous. As an alternative, I could hire a mini digger and a driven-dumper and have the soil taken away. All this is cheap to do and is the default route. I’ve used a mini digger before for a similar job but while it was easy to learn the basics - getting an even depth over a wide area is very time consuming. which takes us to option 3: just hire an experienced digger driver and a digger. I haven’t had quotes for this yet. but my wildcard thought is a turf cutter (the really big ones) - these are pushed along like a giant caterpillar powered lawnmower and can evenly cut turf to a depth of around 60mm… so - is there a machine of a similar ilk that could go down to 150mm? It would be so easy to use and to follow the lines correctly that it seems ideal. Yes - I’d still need to lift the spoil away, but that requires much less skill and depth perception than doing the whole lot with a mini digger. I’ve also seen trench cutters that can go to 1m plus. I kind of want a hybrid of the two. any ideas at all?
-
Permitted Development checks and approach for large garage/office?
Pabbles replied to Pabbles's topic in Planning Permission
thank you - I'm off to research it all now. -
Permitted Development checks and approach for large garage/office?
Pabbles replied to Pabbles's topic in Planning Permission
Hi - I hadn't come across this before, so thank you for flagging it. I've just found the CIL policy for my local area. At this stage, I could drop the size down if I need to and the buildings are for incidental use rather than residential however I will thoroughly read the policy first. -
Permitted Development checks and approach for large garage/office?
Pabbles replied to Pabbles's topic in Planning Permission
Damo. Thank you - I’ll look it up. That may actually influence the decision of how to proceed (permitted development appears to be black and white whereas a LDC seems to introduce some level of judgement/discretion). Temp - thank you very much. That’s some pretty accurate guesswork! It took all of my GCSE maths to work out that it is going to be 18.5-degrees subject to build tolerances. For exactly the reason you’ve described, we agreed earlier today with the designer that we’re going to have man-made slates and picked one that is OK down to 15-degrees. They’re also lighter which helps with the odd forces on the ridge beam/purlins compared to a more traditional pitch. yes - while there’ll be doors on each of the bays, the interior is going to be open plan. The only concession we’ve had to make in moving to oak is that there is going to be three pillars inside the garage supporting the central ‘front to back’ beams as the max span the designer is comfortable with is about 5/6m rather than 9. -
Permitted Development checks and approach for large garage/office?
Pabbles replied to Pabbles's topic in Planning Permission
Thank you. That’s some useful background information on a past decision. Could you share the source/planning authority involved? -
Permitted Development checks and approach for large garage/office?
Pabbles replied to Pabbles's topic in Planning Permission
Thank you buddy. No - its not a requirement as far as I'm aware, I've never seen it mentioned. The only reason I flagged it is to mean that there would be no reason for any neighbour to complain about the building - PD or otherwise. Apologies for the scare. -
Arkiplan or similar online drawings - any recomendations?
Pabbles replied to Pabbles's topic in Surveyors & Architects
in the end we used a local architect to produce some inexpensive outline plans, which were used for a block quote which was compared with steel buildings quotes and both were far higher than a lovely oak building - so we've gone with the latter which includes drawings from the designer. -
I think I can close this now. We have looked at all options - initially decided on steel, got six quotes which were all incredibly high - block was higher still and have eventually settled on a beautiful 4-bay oak framed building which is actually cheaper than either solution. The drawings are being finalised now.
- 1 reply
-
- 2
-
-
Hi everyone. We plan on putting up two buildings in the garden: one large oak 4-bay garage (12mx9m = 108m2) and one large oak garden office (9mx4m = 36m2). I have been through every planning wizard, the PlanningPortal checks and the Householder (technical) Guide for Permitted Development and I believe we can build both buildings easily under permitted development - our oak building supplier has confirmed that he can design to suit. The drawings are being prepared now (after just switching away from steel on saturday for the garage due to the price vs aesthetics balance) and we're pushing to be able to start groundworks within 4 weeks. Until that point we will continue to be paying for an unsustainable level of storage for our classic cars, tools, garden office furniture etc. so we need to complete the buildings quickly. Given the investment involved we would of course prefer to get a Lawful Development Certificate in advance. However the local planning office is currently overwhelmed and has closed their permitted development enquiries service and have advised that it would take 4-6 months for an LDC application to even be assigned to an officer to review, plus they would then need to process the application - so we could be looking at anything up to 8 months to get the certificate... plus builder availability and material lead time, etc. Our understanding is that an LDC is a nice-to-have and that provided we stick firmly within the boundaries of permitted development that it isn't strictly necessary unless we plan to sell the house, which we don't, and could be gained retrospectively if we ever do sell and if it is requested by a buyer. So we're currently (and uncharacteristically, given our aversion to risk) leaning towards building straight away without going through the LDC process. I wondered if experienced members of the board might cast their eyes over our checklist to see if they can see any issues with this approach? Here are the checks carried out and design/location decisions made: Through our solicitor and our property searches we have confirmed: is the property in any type of designated land? (national parks and the Broads, Areas of Outstanding Natural Beauty, conservation area or World Heritage Sites) - NO is the property in greenbelt? - NO is the property or any part of it listed? - NO is all of the garden correctly recorded as residential garden land rather than agricultural? - YES are there any restrictive covenants re: outbuildings or Permitted Development on the property title itself? - NO have any restrictions been put in place on the property as a result of a previous planning decision? - NO are there any Article 4 directions in place on the property itself or in the surrounding/wider area that would affect Permitted Development rights? NO is there any other factor you can think of that might restrict Permitted Development rights upon purchase? NO The design of the buildings is as follows The buildings will form outbuildings #2 and #3. #1 is an existing single garage that was built to the front of the property with full planning approval some years ago. Both new buildings will be situated far to the rear of the property at the end of the garden which is bordered by fields on two sides and a single neighbour on the other. Each building will be positioned >2m from any boundary The eave height on the garage is set at just under 2.5m from natural ground level of the flat garden. The ridge height on the garage has been designed at just under 4m from natural ground level of the flat garden. The eave height on the garden office is set at just under 2m from natural ground level of the flat garden. The ridge height of the garden office is at 3.4m from natural ground level of the flat garden. Both buildings will have simple dual pitched, man-made slate roofs. Neither building will have any form of second story, platform, balcony, porch or veranda nor any living space. Both buildings will be built to building regs and building control will be consulted throughout the process. The buildings will be approximately 10m from each other and 50m from the nearest highway. Neither building is in the sightline of the one neighbouring property. The combined footprint of the proposed (108+36m2) buildings, added to that of the existing outbuilding/garage (36m2) is 180m2. The available curtilage around the house is 1,900m2. Which means we're proposing to end up with less than 10% of the available curtilage covered in outbuildings. If we have missed any sort of check or if anyone can see a problem with proceeding without an LDC, I would be very grateful for their feedback. I have been anecdotally told by a number of non-expert people that there is a max square-meterage area limit for any building under permitted development - this varies from person to person. But when I've tried to research this and have challenged planning consultants on the same, no one has heard of any limit in the area beyond the '50% of available curtilage' rule. The only square meterage threshold we are aware of is 30m2 for building regs, which we are already planning to include. Thank you very much.
-
thank you. That's been really helpful everyone. Has already come in handy with challenging costs down with building suppliers (they folded immediately). Awaiting final drawings then off to formal quotation.
-
The 2m rule is only if you want the ridge height to be the full 4m. If you're happy with 2.5m of height then you can be closer to the boundary but as I understand it some local authorities seem to have different interpretations of the rules.
-
Thanks Kelvin - that's really helpful too. 10.5x5 is about 58% of 12x9 which would make an equivalent price about £10,300.
-
Peter: that's the bit I'm struggling with at the moment, we've spoken to two architects and two planning consultants and we can't get a straight answer but all have said its technically under PD but best to go for a Lawful Development Certificate to be safe. Their reasoning is that: 1) its >2m away from any boundary (which under PD means the pitched roof can go to 4m) 2) even at that footprint it only takes up 7% of the available curtilage (its a massive garden, about half an acre and the boundaries near the building are all onto empty agricultural land) 3) The eves are at 2.5m from natural ground level 4) The ridge is at 4m or lower from natural ground level 5) its set back from the property 6) its not in any protected/greenbelt/conservation land and there are no restrictive covenants on the title. I've anecdotally heard about a 30m2 limit to PD in some areas (not the 30m2 Building Regs limit, a separate one for footprint) but haven't been able to find anything in the local authorities policies. That does seem to hit all the PD markers - bigger than they might expect, but that's due to the size of the garden. Unfortunately the PD Enquiries service is shut down at the local authority, so the only way to get some confirmation is an LDC otherwise its full planning, which I don't want to do due to the pressures that this particular planning authority (Cheshire East) are seeing at the moment - I suspect saying 'no' would be quicker for them to get it off the to-do list. Fully recognise that Building Regs are a factor being >30m2, I should have mentioned that above - yes we're fully expecting that.