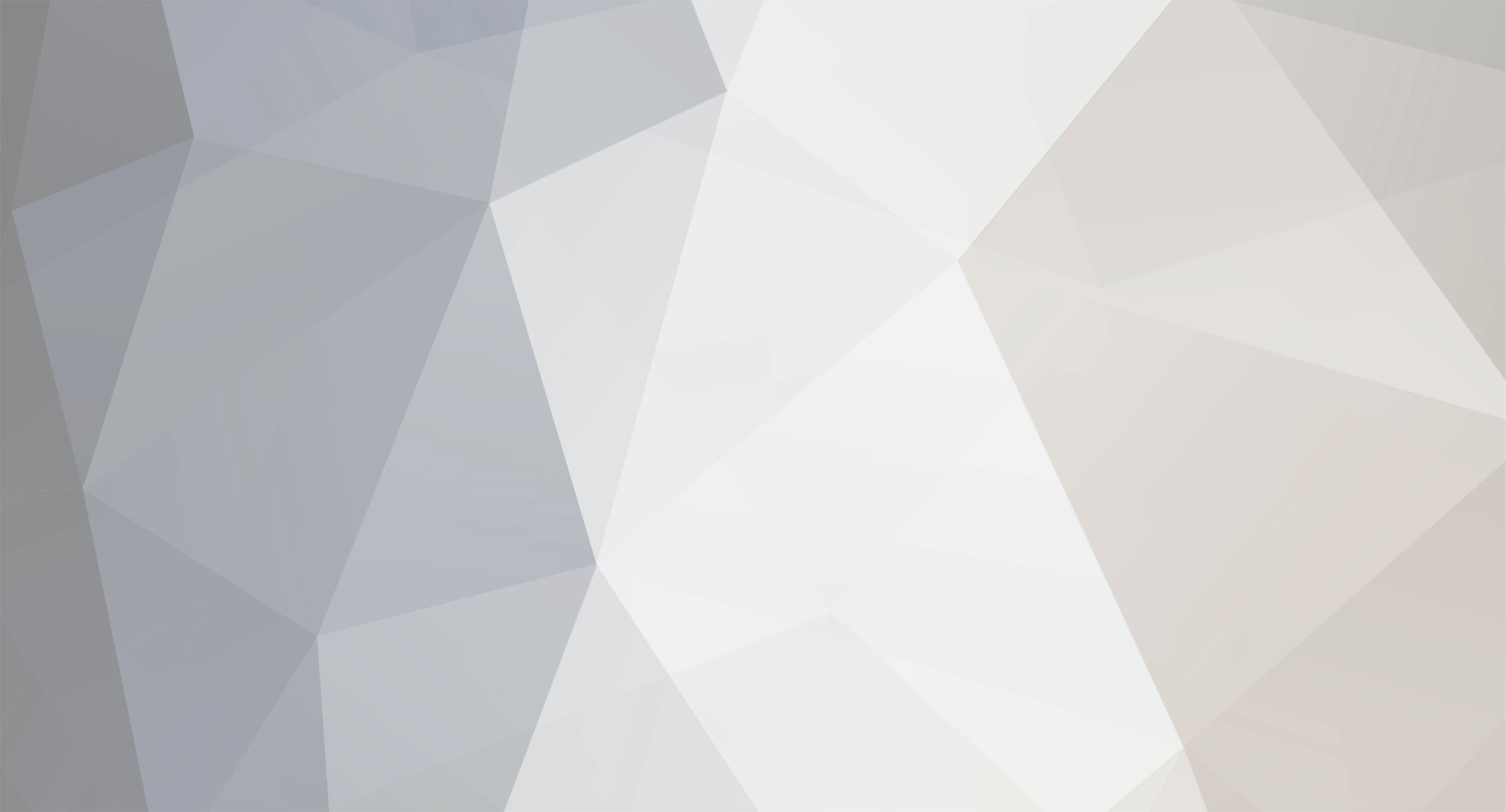
Dean Mc
Members-
Posts
29 -
Joined
-
Last visited
Everything posted by Dean Mc
-
Levelling Step Between Original Slab and Beam & Block Floor
Dean Mc replied to Dean Mc's topic in Floor Structures
Thanks all. The step is approximately 10 to 15mm. The join is just under 5m wide. The length of the beam and block area is over 10m long and perfectly flat, so I was looking to grade it in underneath the 100mm Celotex. -
Hi, Sorry, possibly a stupid ‘newbie’ Q. I have single story self build, which has two distinct areas of floor substructure; concrete slab and beam and block. The concrete slab was from the original building, but an additional limb was added which has a beam and block floor structure. There is a step where the two meet, which causes a void underneath when laying the 100mm Celotex insulation, which obviously flexes due to the lack of support beneath. The Celotex installation guide says ‘smooth with thin sand binding’ but I’m concerned that this may compact or move through time. Should I be using a cement / concrete mix? Or something else?
-
Insulated slab
-
Thanks JohnMo 👍 do you have any pics during the fit?
-
Apologies if this is in the wrong section, as I could think of numerous I could have put it in. I’m doing an ICF self build. Is there a standard / build regulation for how water / electric cable / broadband utilities must be passed through the foundations and wall and into the building i.e. are certain types, colours, diameters of conduit required for specific utilities?
-
Under Floor Vents for Block and Beam through ICF
Dean Mc replied to Dean Mc's topic in Insulated Concrete Formwork (ICF)
Thanks ChrisJ, I kind of dismissed that at the beginning, as I thought it may crush? I was thinking along the lines of.... I appreciate the Nudura takes the outward forces but has the internal ties increasing strength and preventing distortion. Does it resist 3m worth of concrete being poured on top? I've been thinking of far more complicated, time consuming and costly solutions including manufacturing stainless shrouding and ducts and all sorts. Although I had thought of inserting timber inside the duct, but didn't know how easy it would be to remove and I'd possibly end up with blocked Manrose vents and still having to core drill extra holes too 😬 -
Under Floor Vents for Block and Beam through ICF
Dean Mc replied to Dean Mc's topic in Insulated Concrete Formwork (ICF)
TY. That's just raised a few more Qs in my head now 🤯😆 -
Under Floor Vents for Block and Beam through ICF
Dean Mc replied to Dean Mc's topic in Insulated Concrete Formwork (ICF)
Awesome, thanks for that @Russell griffiths 👍 -
Under Floor Vents for Block and Beam through ICF
Dean Mc replied to Dean Mc's topic in Insulated Concrete Formwork (ICF)
I was hoping to get the floor in this weekend, so would / will have to wait to speak to BC. We're building on a hill, so the topography of the ground slopes away. We've had to build up above ground over 1m to get to floor level so the ICF is still exposed. -
Hi all, We are building our home from Nudura XR35 on a sloping site and have only stacked and poured up to floor level so far, ready to take our block and beam flooring. It's only just been noticed that there should have been some underfloor ventilation fitted for the cavernous void underneath, as per the approved architects drawings. They've advised a vent every 2m each side of a 12m run. The site is on the side of a hill, very exposed and regularly subjected to >50 MPH winds. We were supposed to fit something along the lines of the Manthrope telescopic underfloor vent, but I'm aware they are pretty flimsy and prone to shattering / cracking under the pressure of the next pour: https://www.screwfix.com/p/telescopic-underfloor-vent-black-220mm-x-215mm/12025 An option I have is to drill 4" / 100mm holes through the Nudura and concrete and fit a vent / tube / grill assembly. I maybe over thinking things, but one of my worries is wind whistling through the vents even if make a swan neck? Likewise, making something too truncated and it not providing sufficient ventilation. Anyone had similar experiences or had to address anything similar?
-
Sorry, should have mentioned, build is single story in the shape of a T. Bedrooms and bathroom in one limb across the top with the master bedroom at the end and en-suite vaulted. Open plan kitchen, dining room and lounge running north to south at the bottom part of the T, which are vaulted throughout.
-
Hi, I have another rookie Q for anyone who may be able to help? We’re about to build a house using ICF but the majority of areas, all bar the bedrooms and bathroom, will have vaulted ceilings. Our drawings have been submitted to our LABC and list MVHR, but we hadn't requested this be added, only discussed the potential. The primary heating will be ASHP with wet underfloor heating, with a wood burner but mostly just for effect. We’re down in Cornwall and I’m a little concerned about damp, having lived in many properties down here which have suffered from it. However, I don’t know whether this will be an issue with our building, or whether MVHR / PIV is the correct solution. Some people have mentioned MVHR and PIV, but; i. Is MVHR of any benefit or required given it’s an ICF house with ASHP? ii. Can this be done effectively with a mixture of ceiling types but mostly vaulted? iii. Do the benefits outweigh the costs, as we’re on a very tight budget? So, we're trying to ascertain whether we change the build regs application back to without MVHR or keep it with and take on the additional costs?
-
Newbie to the slaughter with Barn Conversion Warranty Woes
Dean Mc replied to Dean Mc's topic in Introduce Yourself
What would you say are the main pitfalls? -
Newbie to the slaughter with Barn Conversion Warranty Woes
Dean Mc replied to Dean Mc's topic in Introduce Yourself
Thanks saveasteading. In short, we had planning already approved, but it was to convert the block cowshed. Our new architect assured us he could draw new plans and have planning approve a demolition and new build. This was flatly refused. Tbh, it's not just planning we've had poor information on, which has made the build more time consuming and costly. -
Newbie to the slaughter with Barn Conversion Warranty Woes
Dean Mc replied to Dean Mc's topic in Introduce Yourself
It's really is a minefield, but I've learnt so much and will be more than happy to share my experiences with anyone who wants to listen. The only caveat I would add though, is there sometimes seems to have been little parity with some other cases I've heard of, with some quite extreme variations in decisions and outcomes. In hindsight, some people have used planning consultants which have had success and maybe I wouldn't be another 18mths down the line before we dig in anger and kept far more in the bank. Still, we're nearly there........ for the next part of the trials and tribulations 😄 Anyway, thank you all for being so helpful and for the fantastic advice. I just need to read through some of the small print and which to select, but it's looking like it's ProfessionalConsultantsCertificates.com or CMLC. Cost and number of visits vary, but has anyone had any experience of either of the companies when there are bumps in the road and their actual advice and services have been required? -
Newbie to the slaughter with Barn Conversion Warranty Woes
Dean Mc replied to Dean Mc's topic in Introduce Yourself
Thank you both. We seem to be experiencing errors due to others incorrect information. We were told to reapply for planning to knock down and start again by our architect. Thousands of pounds and 12 months later for numerous reason, it was rejected and we had to revert back to where we were. PCCs are looking favourable atm, but still waiting for other companies as a result of all your help 😎 -
Newbie to the slaughter with Barn Conversion Warranty Woes
Dean Mc replied to Dean Mc's topic in Introduce Yourself
Online quote done thank you. Just need to check there’s no small print that would exclude us -
Newbie to the slaughter with Barn Conversion Warranty Woes
Dean Mc replied to Dean Mc's topic in Introduce Yourself
Thank you. 👍 Their landline just goes through to answer machine. -
Newbie to the slaughter with Barn Conversion Warranty Woes
Dean Mc replied to Dean Mc's topic in Introduce Yourself
That’s great, thank you. Ironically, I’d just had an email from Buildit, advertising Protek this morning and was going to call them. -
Newbie to the slaughter with Barn Conversion Warranty Woes
Dean Mc replied to Dean Mc's topic in Introduce Yourself
Thank you. Yes, we’ve been through the mill already. No, sorry, not a new build. I probably may not have been too clear; it’s a field with an old cowshed in the corner, which we have to convert, even though there will be very little left, which will all be internal to the ICF and non-structural as it will be T-cosied. We’ve been informed that we need a warranty if there is a mortgage requirement. -
Hi all, 3 years ago we started the dream of building our own family home, when we came back to the fold in Cornwall, having previously dragged my Wife and family away to Lincolnshire due to my work. We are converting a cowshed which has been unused for decades, which on the face of it, seemed relatively simple. We currently have our architects drawings being reviewed by LABC after several issues to get to this stage already. The current rectangular breeze block building will be extended with an additional new build limb to form a capital T shape, with mostly only the rear wall and west gable remaining of the old building. This will then be T-cosied and extended using Nudura ICF. Schoolboy error, but I found out too late that our architect / structural engineer do not provide warranties. Likewise, Cornwall LABC do not cover barn conversions for buildings previously used at any point for livestock and each warranty company I have approached will only entertain new builds, not conversions. Site is cleared and I want to start strip footings as soon as possible, but cautious I can’t do so until I find someone to cover the warranty, in case they need to inspect before we poor. It’s been a torturous and expensive journey of fighting bureaucracy, red tape and being misguided by professionals, but still too stupid / stubborn / determined to build our forever home. Does anyone have any pointers please? Slowly dying from desperation in Cornwall 😁