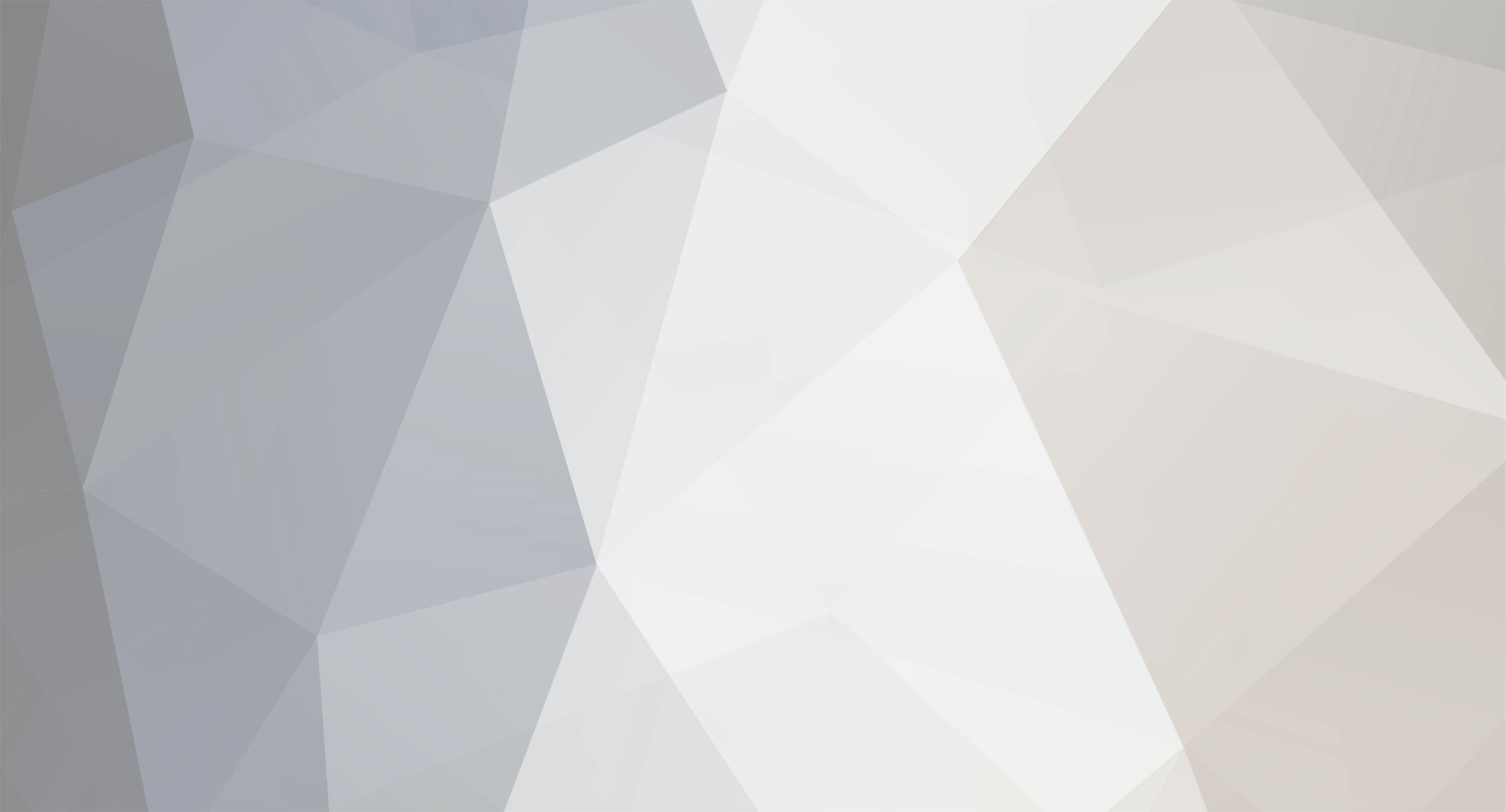
renovator123
Members-
Posts
15 -
Joined
-
Last visited
Recent Profile Visitors
The recent visitors block is disabled and is not being shown to other users.
renovator123's Achievements

Member (3/5)
3
Reputation
-
re solid wall insulation - wood boatds are a much less specialist option, Gutex or Lime Green Warm Shell for instance - level walls first though - both can be used as IWI or EWI. EPS/XPS is the popular EWI option. https://www.lime-green.co.uk/products/lime-systems/woodfibre we currently have a bag of Lime Green Ultra which can be used as render but we are actually using for patching plaster and holes, using that instead of gypsum plaster gives breathable walls that are mould resistant (alkaline) and greatly improved U value compared to uninsulated solid walls. Diathonite Thermactive you can also hand mix and buy per bag for small repairs and leveling https://www.lime-green.co.uk/products/lime-render/ultra_render re: EWI: with Diathonite (Evolution) at 55-60mm thick which is 0.60 U on rubble/sandstone (with original concrete render hacked off first, and a few mm lime green WP finish over the top), we did not need to extend the roof line at all. The walls were very uneven - especially thicker at the bottom and in places curving from one side to the other (kind of concave) over the, so that was a nice surprise. You would also lose the stone look with EWI (what we found was missing stone and old blocked off doorways etc). Diathonite EWI case here sums up a lot of our issues With Diathonite if you go IWI you can use Thermactive which has a better U value, with our EWI we still have gypsum plaster internally so unless we replace that on external walls they won't "breathe" (though it may not matter with MVHR in soon). The reason we didn't do IWI was need for new render and lowering outside ground level (which is still higher than inside), as well as less mess to live with. Diathonite needs hose on water tap and electric if machine applied. MVHR: you need an accessible room and unless sound proofed room (they are noisy), so under stairs, boot room, or shower room on left of stairs by bed 5/study. Central to the house is even better with air intake plus connecting to internal drain ie near plumbing - but the big issue we had was avoiding crossing the many exposed ceiling beams downstairs and ceilings way too low for false ceilings (under 2m in places). You would have to plan where the valves go for vaulted ceiling spaces - supply valves that are wall mounted are apparently really large. If you have a central chimney you can run ducting along it and box in and fit valve from there. You also need a recirculating cooker hood and to block/remove all bathroom extractors plus breather membrane in loft, and insulation on any loft ducting, and ideally avoid window vents in triple glazing. MVHR are extremely efficient and kitchen and bathrooms will always be warm and should dry laundry easily indoors. MVHR planning resulted in finding 2 unknown and well hidden ceiling beams. If you have never had oil before then it's really inconvenient - you end up having to buy over 1,500 litres at the (uncapped) Kerosene market rate at the time, in the month you need it, and it doesn't run without electrics anyway. Basically get fleeced once or twice a year, boilers are less efficient too. Skylights that aren't passive house standard will lose a load of heat especially with uninsulated floors - internal stone walls act as a cold bridge unless you de-couple walls from floor eg dry lining. Insulated lime based plaster is a good option for problem spots internally eg Lime Green or Aerogel ones (40% less heat loss compared to uninsulated solid walls). Weirdly we have internal damp at above electric socket height on 2 internal walls, one socket has been replaced multiple times from rust. Ground source heat pump is likely to be better than ASHP for the size of your house. If you do enough energy efficiency improvements eg towards EnerPHit standard then you probably won't need a central heating system. Good luck with the rest of the plans
-
Update: we weren't impressed at all with the Cork Sol info and found it easier to get Diathonite installers. The other options seem rarely used externally and won't help so much with air tightness or mould. Diathonite is excellent, not fully cured for a few months (but dry to touch and re-coatable). We had advice that we should have XPS plinth across the bottom where we get a lot of water spray - on to get a bead on it so that the XPS can be recoated in future years/decades if there is water damage. The same top coat is on both and it looks awesome. We had a few external concrete window sills so got those knocked out and replaced with XPS, which is ridiculously loud when it rains (or was until the top coat was on). Diathonite has greatly improved the air tightness (less drafty), and the mould situation too (because it's alkaline and because damp can move to the outside). It's a colored top coat so no painting needed. To keep moisture moving from inside to outside needs lime plaster or similar, although there's still a lot of benefits with gypsum... a lot of internal plaster is persistently mouldy or blown so needs sorting anyway. One part is so mouldy that the metal edging under the plaster has rusted through. It's very noticeable how warm it is overnight and the phase shift of the thermal mass. No good pics yet since top coat is still in progress and has to dry gradually before you get to the final color. It's already much better than the concrete render (which had a lot of damage). Diathonite evolution is a sandy color going on, drying to light grey. Top coat is by Lime Green in woad blue. The window bands need reforming unless you want to just paint them on after.
-
Just saw this and actually I also have an update: and lowering part of the ground floor is on the list for another year - there's no foundations here either. We got the EWI with Diathonite, great so far although not fully cured yet. Damp and mould were factors in the decision- Diathonite is very alkaline so inhibits mould, and with no floor insulation the internal solid walls have damp in a few places. We decided to go for MVHR in preference to heat pump and even just having the kitchen extractor recirculating with the wall insulation it's noticeably warmer and less drafty. The utility/downstairs loo extractor is gone in preparation for MVHR. Heating-wise it seems new builds and big renovations are going for heat pump and underfloor heating (at least for ground floor). That's not workable with low ceiling heights and low beams. We got an advice report drawn up from a charity that provides them and that's helped a lot with planning although the cost estimates are on the low side. The report broke it down into 3 stages and outlined risks eg condensation causing damp. With windows and glazed doors trickle vents are heavily suggested but optional- going the MVHR unit satisfies the ventilation needs and allows you to look more at EnerPHit/Passive House standard triple glazing, which is much better than argon filled double glazing. The "pink house" retrofit in Scotland is a mid terrace with real life figures on different combinations of options, and MVHR was particularly good value and was very good combined with ASHP, we have also discovered 2 further ceiling beams during the MVHR design process https://www.esru.strath.ac.uk//Documents/MSc_2015/MacLean.pdf It's been pretty crazy this year for us, and part of last year so we have a break planned for at least a year, which should mean we get time to patch the numerous holes in walls and ceilings (and floors). The planning is actually more hassle than having the builders in and the endless small jobs and mess.
-
Interesting, thanks. We are facing similar issues. Diathonite is actually a range of products with Thermactive being IWI and Evolution being EWI, plus extra products for areas with a lot of salt crystals, a tanking solution and top costs. They do a top coat cork spray which can be colored and is less prone to cracking and better able to move with minor movement compared to most render. I think we have given up with CorkSol, U value is not a good and they don't seem so good at getting back to you, and unsure of the quality / consistency of it. Another Diathonite EWI case, the House at the Northern Gate has it too (far North of Scotland and coastal). https://www.fca-magazine.com/features/product-specific-features/1396-ecological-building-systems-cumbrian-period-property-overcomes-issues-of-damp-and-mould-in-major-renovation
-
I live on a hill in one of the wettest parts of the uk, but the water runs down the hill into a river and French drains are typically as part of that, it is not such as issue with the type of ground and the fact it's so steep - it would be an issue if we had chalk ir clay but we don't. It drains without a problem. DPCs are perfectly good when you have cavity walls and a fairly modern build and you don't have any rooms below outside ground level. It's not exactly practical to expect a DPC on 600mm limestone and cob with render and gypsum plaster to keep the wall dry, especially not when you do not have a floating floor or real foundations - we've been down that route and not had it work. So the focus needs to be on what materials work for the existing building and the limitations of it. Keeping 100% of damp out is highly unlikely so going with traditional but updated building products means moving further to vapour open, and MVHR (heat recovery ventilation) will be reducing any excess humidity further, although I doubt we will see damp on internal walls in the same way later.
-
Yes about the lower walls, something not so vapour open it needed for the lower part of all of this, I should have said. Diathonite Demix and tanking are needed for the bottom 30cm+ for at least some part of the house given about a third sits on a concrete slab over rammed earth and house is 1830s and has never seen a DPC. By "breathable", think "vapor open". Figures for vapour permeability by diffusion and air tightness values are available for all the materials mentioned, although some (foil quilt and Supasoft) have to be filled in specific ways for EWI - supercoil have a breather quilt for instance. Currently we actually have some damp in a fully internal supporting wall coming up from this. Hopefully we will be getting this resolved as part of the work. The electric back box for unused sockets have rusted a second time after having measures done to fix it before.
-
The walls are nothing close to level so a flexible insulation allows you to fill any gaps and level things out. EPS or other boards must have the gap between them and the wall fully filled. It's a period house that was built as both vapour open and breathable and keeping it that way it's going to cause its less problems.
-
Any suggestions or feedback for comparing breathable EWI options for a home aiming for EnerPHit (U 0.15). These options we are looking at: * Diathonite (clay/cork/lime) * CorkSol / SprayCork - how does it compare to Diathonite? * Wood boards eg Steico, Gutex (Pavatherm prices seem crazy) - durability? Bowing? Water ingress? * Supasoft (recycled PET) * Superfoil is advertised as breathable All seem very similar U value, prices vary a lot and Diathonite installers are hardest to find. We have ruled out thermafleece wool for reasons I won't get into here. This is to go under render (existing concrete based render is cracked and will be removed first), for an old house (500-600mm solid walls) with no damp proof course. IWI we have ruled out due to construction/layout and internal issues. It's a semi with very limited space on one side (under 100mm thickness needed). Anything extremely durable and really good for non-coastal but very windy area would be good.
-
I'm wondering about your EWI options- do you have a price per sq m for Diathonite, and have you had difficulty finding an installer? We are also looking at breathable EWI and options seem limited- although Diathonite looks excellent it's very expensive. I wondered your thoughts on CorkSol / SprayCork, or wood eg Gutex / Steico for EWI instead? I am not sure about durability of wood or about the ability to keep it dry when render over it will crack/decay sooner or later. We had calculations done for EWI using Diathonite, giving approx 57-60mm thickness (evolution, agrathem, etc) over 500mm stone but have recently found some solid walls are not uniformly that thickness, which affects ability to reach EnerPHit U values. Diathonite is similar in U value to rockwool and supasoft/thermafleece options which leaves me wondering about value.
-
Cost comparisons - Aluminimum Clad Windows
renovator123 replied to DavidG's topic in Windows & Glazing
TL;DR: Internorm EnerPHit prices above Windows approx £700-1,000 each inc VAT, fitting, removal of old, larger windows would likely be cheaper per sq m. Internorm only do single panel windows (glazing bars are an option) and only tilt and turn. Doors were in excess of £5,000 inc VAT and fitting, with only the HF410 model able to made in the shallow height we needed for retrofit, and us having a custom design. With no porch or conservatory on the house, the doors have made an incredible difference. Door designer prices are online: https://uk.internorm.com/internorm-door-designer/ Thumb turns & split spindle were fitted after by installer included in price, which were Winkhaus - amazing for keyless emergency exit, and keyless locking from inside without risk of accidentally getting locked out. Trickle vents - England - current UK regs state trickle vents are needed, clearly not suitable for EnerPHit or Passivehaus - but this regulation has some exceptions including certain other ventilation methods. https://www.gov.uk/government/publications/ventilation-approved-document-f- 65 replies
-
- 1
-
-
- comparison
- cost
-
(and 1 more)
Tagged with:
-
Cost comparisons - Aluminimum Clad Windows
renovator123 replied to DavidG's topic in Windows & Glazing
Some prices are specs... we went with Internorm and the quality is excellent, really noticed the difference and they haven't even finished installing so it's not close to air-tight. Velfac V200E we also looked at - prices similar to Internorm. specs: Internorm Retrofit Timber/Alu Argon filled triple glazing 48mm (4b/18/4b toughened/18Ar/4) HF410 windows, 0.71 W/m2K stated, calculations were 0.73 to 0.84Uw HF410 doors, 0.73 W/m2K stated Doors had to be custom due to height, with 1/3 triple glazed obscure, 2/3 timber-alu. 9 windows, total 7.96 sq m 3 doors, 4.85 sq m with unusually low height that was unavailable from all major sellers (Solidor do Tinidor but no other big firms do). Dec 2022 price £14,435 excl VAT £17,320 with VAT included Fitting was all thermally broken eg compreband to our solid stone walls (EWI is planned). Extras: * Removal of old, retrofit, * 2 thumb turns and split spindles on doors * Hirest weather resistant color * 1 window obscure glass + Full fitting including removal of old and scaffold brought up * Cat flap fitted in 1 door * Presumably a charge for overnight accommodation (2 people, 4 nights) and travel due to distance Final cost: £24,342 incl VAT - May 2023 (discount of about 5 or 10% at the time) (£17,320 excluding 20% VAT). Skip costs extra. Not a single supplier in our county was willing to quote for any EnerPHit standard spec from any manufacturer so travel/hotel bumped our costs. Green Building Store wouldn't do fitting for their windows and doors and neither would local tradespeople. Well worth it but we absolutely need a HVAC for condensation since extra insulating the loft. Cat has been sunbathing near a window ever since it got replaced and the heating is on noticeably less despite it not quite being finished yet.- 65 replies
-
- 1
-
-
- comparison
- cost
-
(and 1 more)
Tagged with:
-
Cost comparisons - Aluminimum Clad Windows
renovator123 replied to DavidG's topic in Windows & Glazing
Do any of you have installation quotes given separately, especially for smaller windows or part-glazed doors? Those locally only want to sell UPVC (we want alu clad or hardwood/ Accoya), and withdrewoir U values. We are having a nightmare trying to find fitter for retrofit for Green Building Store, or anyone to fit - looks like all existing Passive Houses in the area were new build or full refurbs done by a single builder which isn't possible for us. We did find an Internorm fitter but Internorm's reputation is poor and £5,000 per door (on website) when you need 3 doors is ridiculously beyond budget. Any ideas on window costs? What are we looking for in a fitter, who would likely be doing their first fitting involving thermal bridging prevention/ insulation? * Joiner, or carpenter? * Crane or lift, or is scaffold manageable? (No large upstairs windows, will need partial road closure though it should be ok). * What is needed for insulation measures? Doesn't seem like much info is given on green building society website. It's a rural area so anyone fitting nationwide or English/Scottish borders would be appreciated. At this point, we are over a year into trying to get windows while patching up the increasingly rotted 1980s ones with sealant, plywood, etc, and hoping they don't fall out. Nearest experienced builder and fitter has 12-15 month timescale, which takes us past our expected heat pump install. As with OP, prices are significantly higher than previous threads here. Internorm and Green Building Store supply only £12,000 - £15,000 including VAT for 3 doors (2 part glazed), 7 windows of 11 sq m. No fitting estimate at all. Things tried so far - Green Building Store currently short of fitters and suggested someone we already knew about with long wait list - Internorm don't do supply and fit for renovations, second nearest distributor quoted for supply only with 100% down before delivery which is too risky - Asked a local carpentry / window making firm to quote but they couldn't give accurate U values and ignored our specs and just went with their regular (poor) offering. - Composite firms also not an option for doors since we are below minimum height (low ceilings so unavoidable), they don't have the U values although we did look at Tinidoor who cut down composites but no fitters in this area- 65 replies
-
- comparison
- cost
-
(and 1 more)
Tagged with:
-
Shower light with extractor fan - heat loss & air leaks
renovator123 replied to renovator123's topic in Ventilation
I think we will have to see on MHVR after windows are in, depending on air tightness given it's retrofit. Thank you all. -
Hi. We are in the process of renovating with the aim of getting close to EnerPHit standard. We have a large bathroom with small shower extractor fan extracting through loft area to gable end wall, and would like to keep shower light. Currently the room has fairly new argon-filled double glazing with 2 air vents (the only ones in the house), and we slightly open windows during or after showers to reduce condensation. We also sometimes use an other bath clothes drier with air vents open. Main concerns are: * low budget * reducing condensation after bath/shower or when drying laundry, without heat loss * reducing heat loss from shower extractor fan into attic What are the options here? I have seen decentralized heat recovery units for walls, but can these be combined with existing shower fan? Are they safe to place in shower enclosure, which is by far the main area of condensation? Any concerns about length of ducting? Removing the fan from the shower light but adding an additional ceiling extractor fan using existing ducting might work. Shower fan is perhaps 60cm from gable wall of house (plus about 60cm thick wall), plus there is attic ducting, mainly above level of insulation due to avoiding fan overheating plus height of external hole/grill. Outside temperature is almost always above 0C in the day in winter, rarely below -10C overnight. Tumble drier is out of the question and laundry is dried on washing line when possible, but it's a rainy climate. (We will not be doing a single/whole house MVHR due to difficulty with layout/age of house/disruption).