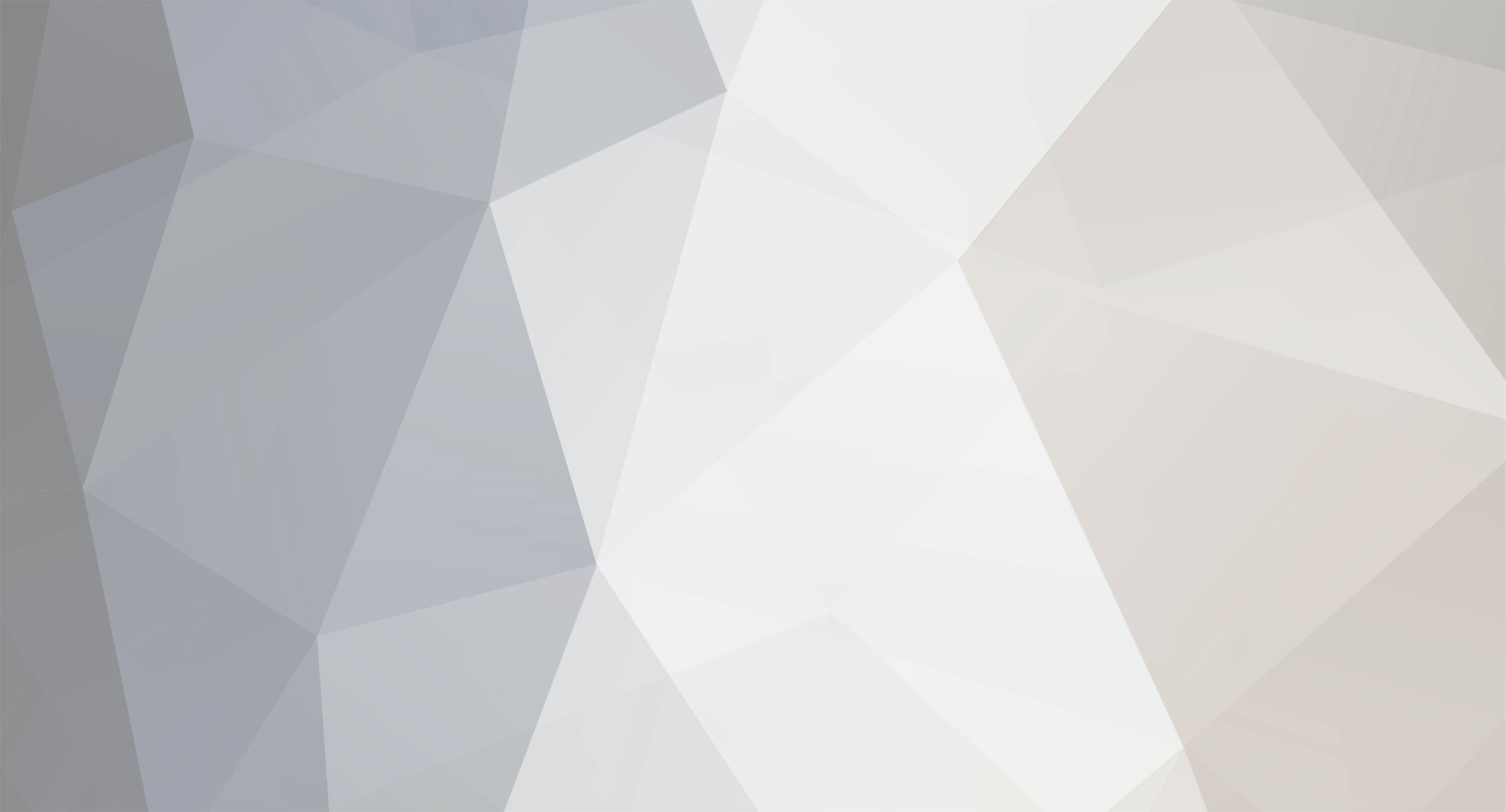
Ian79
Members-
Posts
17 -
Joined
-
Last visited
Recent Profile Visitors
The recent visitors block is disabled and is not being shown to other users.
Ian79's Achievements

Member (3/5)
0
Reputation
-
Minor works certificate who can sign
Ian79 replied to Ian79's topic in Regulations, Training & Qualifications
Update: We finally 8 weeks later got a certificate for our consumer unit! can I just ask advice - does the photo show the EIC? Is this all that we require from the electrician directly? If the electrician is qualified / registered to do this does that mean he is automatically qualified / registered to submit the building control notification? He hasn’t done this despite asking - is that as important as the certificate? -
Hi all - some advice please: As part of a room refurbishment / wider building project, our builders used an electrician (sub-contracted we assumed) to undertake the minor electrical work - addition of a spot light circuit. The electrician issued a minor works certificate (after some prompting!) which seemed appropriate, except it was signed / issued by someone else who has not ever been to the property. We were slightly surprised but thought no more of it. Is this acceptable (legal?) He also persuaded us we needed a new consumer unit (probably true!) and he did that for us outside of the building contract. We didn’t get quotes, but paid him the substantial price he was asking - not cheap - and we didn’t check qualifications / registrations etc., as assumed he was legitimate / above board as he was introduced to us by our builder. He has since (6 weeks+ on) failed to provide any installation certificate or notify building control, though he claims to have done the post installation tests, and that the certificate is now finally in the post (he sent a photo of the envelope!) What certificate should I expect as a minimum? I assume it *must* be signed by him, as he did the tests? Any thoughts welcome on what we expect / what we should do as next steps? Many thanks.
-
Some advice from the experts please: We have just had a single story extension renovated, including complete re-plaster. On painting one of the , I noticed several (maybe 5 out 6) patches that sound hollow on tapping - typically 5cm across. They are at different heights in wall. The worst one actually collapsed when I (relatively gently!) prodded it - see photo. Apart from that one, they are not obvious now painted, except under certain light, but I’m just trying to understand what the problem is. Is this an early sign of damp (walls were plastered at least 6-7 weeks ago and are completely dry) or is there some bad workmanship that could explain this? Keen to understand ASAP before our builders finally depart this week - wanted to seek views on here before approaching them, as they will no doubt be dismissive! The wall is a cavity wall (1970s extension) but is also a retaining wall as it is below neighbours ground level which is half way up it. There were signs of some mould here previously behind furniture, but we put that down to simply being an unheated / unventilated room over the course of last winter. Any thoughts / advice welcome - especially whether we should ask the builders to investigate…
-
Dormer construction - roofing felt as well as membrane?
Ian79 replied to Ian79's topic in Lofts, Dormers & Loft Conversions
One more question: this photo shows the drainage arrangement for the new dormer as built - it drains forward into a down pipe - this then exits over the last 3 rows of original roof tiles into the original roof gutter at the front. Just wondering if people feel this is appropriate - Is there potentially an erosion issue channeling the water over the tiles in this way? Any thoughts / advice welcome…thanks! -
Dormer construction - roofing felt as well as membrane?
Ian79 replied to Ian79's topic in Lofts, Dormers & Loft Conversions
it is insulated all round (roof, sides and front below / above window) with solid foam insulation (kingspan or similar). Think mostly 150 mm total thickness - all done on inside of structure (I.e a cold roof) before plaster boarding. This feels plenty…. -
Dormer construction - roofing felt as well as membrane?
Ian79 replied to Ian79's topic in Lofts, Dormers & Loft Conversions
-
Some advice from the experts, please: We have been having a dormer window constructed - no plans as such, though builders seem reasonably competent (mostly!) I didn’t know what to expect, and all looked reasonable to me - until got home to this anonymous note through the door, saying that the builders should have used roofing felt in the construction, and that we were storing up problems. So my question to this forum is: is this letter correct? Or is a waterproof (breathable?) membrane under the cladding considered sufficient? I have attached a few photos of the construction - thoughts welcome!
-
Blocking external door - advice sought
Ian79 replied to Ian79's topic in Bricklaying, Blockwork & Mortar
-
Have builders blocking up an external doorway - they have blocked it up with single skin - photo of inside attached. Want to make sure they are doing proper job finishing off, so seeking advice as to how this should be finished. Firstly, given it is single skin, does this look appropriate from inside - I sort of feel that there should be more mortar, extending the full width of the bricks….? There seem to be numerous gaps on the inside… Secondly, what should I be expecting/ looking for them to do internally - I guess a waterproof membrane next to the bricks, then kingspan (190mm?) / similar insulation, in a wooden frame, before plasterboard? (They assure me a dpc went in above second course of bricks) any thoughts welcome
-
Thanks all for the comments - much appreciated and learning a lot - though wish I’d had the knowledge to challenge sooner… Clearly we are missing a really important element of our roof and I now understand the theory. However I guess I’d like to understand real world implications (as opposed to theoretical) - with the best will in the world, I Imagine it is extremely difficult to get a VCl that is 100% joined up to the wall VCl at all locations, with no piercings - and I could believe that a majority of roofs would not achieve this (not wanting to be critical of the construction trade as a whole though, and apologies if being unfair!) In which case is a compromised (Pierced / not meeting the wall VCl layer) better than no layer at all? Are these roof types routinely seen to deteriorate rapidly (1 year, 5 years, 10 years? More?) due to compromised or total lack of VCl? interested in thoughts….
-
Ok, thanks for taking time to reply. I am really not sure I can face the big battle with the builders to do that - is that the consensus view that it is absolutely necessary to do so? BC seem happy to sign off as it is (not coming back until whole roof is sealed / room finished/ lantern installed - unless I ask them to) Don’t know how the insulation is fixed to the deck - or even whether it is at all- though deck is pierced with nails in quite a number of places so could be those. I didn’t watch the roofers so closely early on….! Membrane is glued to the upper OSB.
-
new roof timbers, OSB, foil backed kingspan insulation (untaped, I think!), OSB, rubber membrane. Interesting! So you mean paint the inside of the plastered ceiling with this, once plasterers are all finished? Guess sealing the spots is for the electrician?!
-
With apologies for repeating myself from another thread, but wanted to pose the question / seek advice under a relevant heading: We are in process of having a new rubber warm deck with lantern installed on an existing single story extension. The roof is externally complete and waiting for plasterboard ceiling to go on. However, my reading has highlighted the fact that the builders have not installed a vapour control layer as seems to be required as part of this type of roof construction. Should building control officers have flagged this as essential? They had plenty of chance to do so, having inspected at the roof construction stage, and did not raise it…. I’m not clear how much of a problem this is - how many future problems we are storing up? For context, it is not a room we will overly heat in winter / live in all the time - but it is south facing with a lantern / plenty of windows…. So at this point, I wonder what/ if anything I should do: Should I be insisting that the builders dismantle the roof to install a vapour barrier below the insulation (would be a very big battle i imagine, and very inconvenient for us, as well as them!) ? Or is there any other vapour control /mitigation that could be done from inside, before plasterboard ceiling goes on? Or do we just live with it and assume / hope all ok…! Any views welcome / appreciated.
-
I’m not impressed so far. Though equally, maybe naively, I expected a bit more rigour from the council building control officers… I at least am lucky enough in a position to watch them / technical enough to understand how things should be done (with help of Google and forums like this!). Should I be insisting that they dismantle the roof to install a vapour barrier below the insulation (would be a big battle, and very inconvenient for us as well as them!) ? Or is there any other vapour control mitigation that could be done from inside before plasterboard goes on? Or is do we just live with it and assume / hope ok…! Advice gratefully received…
-
Thanks for that. Just raised this with builders who seem surprised - said in their view it needed ventilation in eaves - but they have agreed to put in some kingspan…will be watching how much… building control seem unconcerned / relaxed about such details, which i find surprising. Also, having done some reading have concluded they have missed out the vapour control layer that seems to be required as part of the warm deck roof - fairly sure the kingspan went straight on the roof deck. Again, should this have been flagged by building control? (they have had plenty of chance, on more than 1 visit) How big an issue is this / should I be raising / demanding they put right? Very late in day as rubber membrane is on and roof all sealed - though joists still exposed…