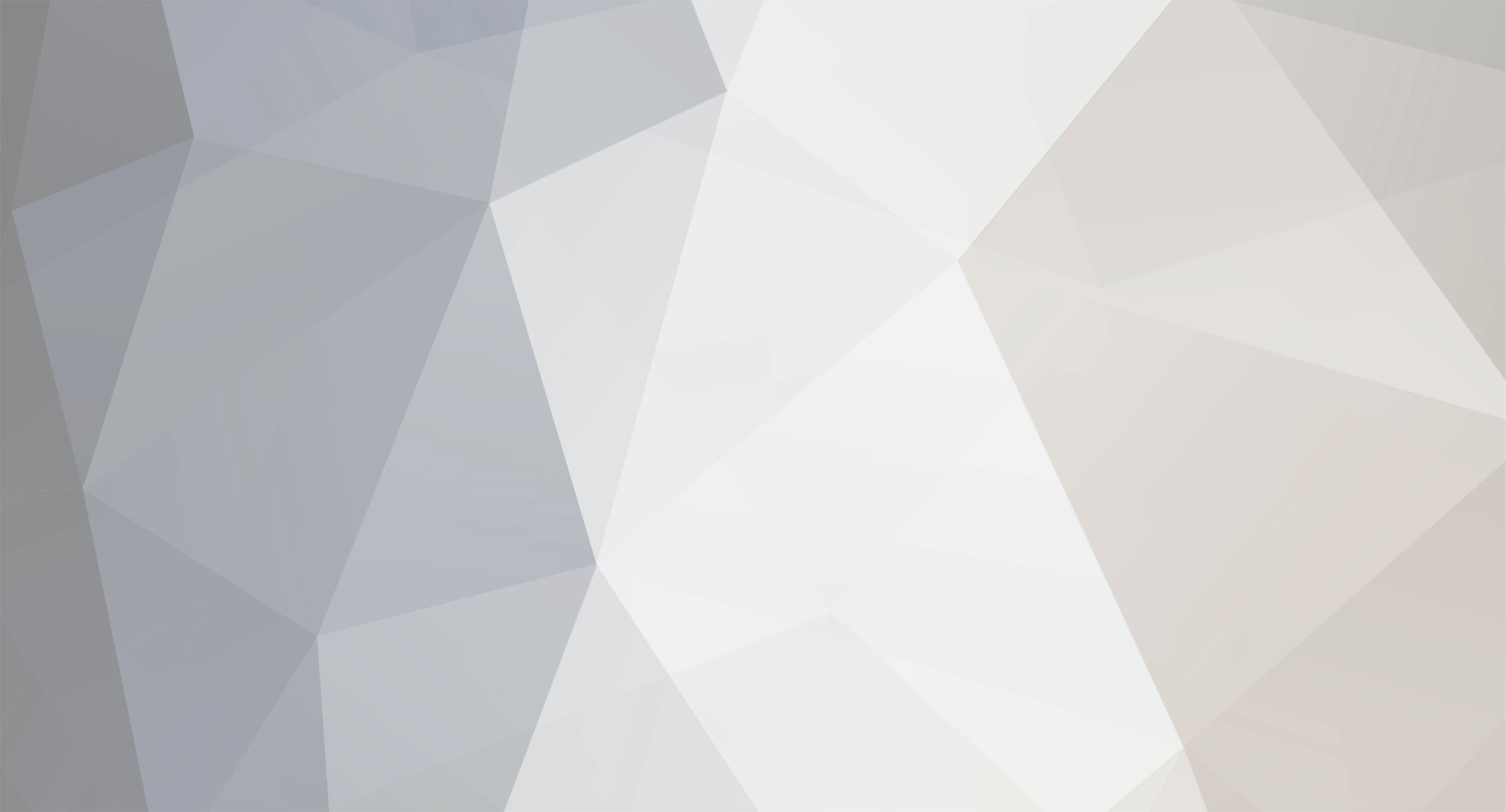
Adthrawn
Members-
Posts
26 -
Joined
-
Last visited
Everything posted by Adthrawn
-
Converting wooden workshop to office
Adthrawn replied to Adthrawn's topic in Garage & Cellar Conversions
With the plywood layer being sealed, should the plasterboard be foil backed or plain? Just ordering materials, and realised not clarified that... -
Converting wooden workshop to office
Adthrawn replied to Adthrawn's topic in Garage & Cellar Conversions
Would an aluminium foil tape (everbuild etc) not be suitable, or do the PHS tapes perform differently? -
Converting wooden workshop to office
Adthrawn replied to Adthrawn's topic in Garage & Cellar Conversions
I was concerned about condensate - but might be the way forward. Are those panels okay to screw into for fitting battens too? And guess no insulation, just air void? -
Converting wooden workshop to office
Adthrawn replied to Adthrawn's topic in Garage & Cellar Conversions
Thank you for the detailed reply! 1A) Windows - the two side windows will be removed in the next phase. The neighbouring wooden garage is in a very poor state, so I'll pull that down and rebuild it. Longer lead time as will need planning, as want to change the roof direction for solar panels, and absorb space taken by other wooden "things" that have been built around it. The plan is to join the two buildings by a wide link, that will be both a passage and storage etc. This will take in the two Windows (single glazed and not very useful). 1B) Doors - replacing them with a 3-door bifold. Obviously wider opening needed, and that will be closer to the left-hand wall. The front wall appears to have been made from three "modules", so I'll have to rebuild some of the framework, but less of a job thanks to how the front has been built. I still need to source a threshold for the bifold, as want to account for the increase in floor thickness (circa 70mm with the 50mm PIR and 2x 9mm OSB (for amtico or less if a floating laminate flooring). 2) French gutter at front - totally agree with that, and around the sides and rear it's soil and been overgrown, so will scrape back soil but soil membrane down and put gravel down. Planning to leave the gravel until after building work, but if I'm just doing the inside now, then could be a "quick" job to get done first (already spent a couple of days clearing the overgrown ivy and weeds etc). The front path however will have to wait for the electrics... 3) Electrics - quite my forte, was planning to surface mount, but if I have a void, may as well hide the cabling and create a nice crisp white box... Linked to the above, the current power supply is an armoured cable buried in concrete. Not to my liking, and makes changing the path near impossible. I've already laid ducting along a fresh route, so when I pull the new cable in, I'll be free to cut the concrete in front. 4A) Ply sandwich - fair point, it's been standing for 15 years or so. Internal ventilation is definitely the big issue, as when I cleared out the old workbenches, shelving etc, the majority of the musty smell went. Still not completely gone, but a good bleaching of surfaces and properly ventilating the place should get rid of that. 4B) Air tight tape - just any foil tape, or something specific? Also, if taping the plywood, does this in effect become a vapour barrier? Is the insulated stud wall on the cold side or the warm side? Are you for/against the addition of ventilation in the top of the cladding panels? 5) The stud wall does seem the best option, and something I can chip away at progressively... Because it's a metal roof (insulated panels), is there any special treatment of the top of the frame, like extending a tape or barrier between the frame/plasterboard and the plywood? I'll use skirting and trim at the roof to finish the plasterboard off. Or is the frame/plasterboard happy to just butt against the roof as-is? 6) I plan to lay a vapour barrier poly sheet under the PIR - I'm not sure if a barrier was laid in the concrete floor originally. I'll seal that to the plywood walls as well - would that be a sufficient DPC for the stud wall? Thanks Jon -
Converting wooden workshop to office
Adthrawn replied to Adthrawn's topic in Garage & Cellar Conversions
Okay, so adding vents to the top of the cladding should alleviate any moisture on the outside layers. I'll be putting a heat exchanger of some kind for ventilation - we need the fresh air through, and want to retain the heat. -
Converting wooden workshop to office
Adthrawn replied to Adthrawn's topic in Garage & Cellar Conversions
I'm not sure how it's been fitted, whether it wraps under the frame or not. I'm hoping it's "loose" at the base, but it'll still be held against the bottom of the frame by the cladding. The poly is very much not a breathable moisture sheet. There's no ventilation in the panels, so the poly seems to have been fitted as a water barrier without consideration of condensate/ventilation. It's fairly lightly filled with a fibre glass insulation of some kind. So, to add ventilation, it should be an easy job of cutting a 60-80mm hole in the top of each void and putting a vent. Do you mean the poly sheet under the cladding or when the plywood skin is taped up and that'll be an airtight barrier? -
Converting wooden workshop to office
Adthrawn replied to Adthrawn's topic in Garage & Cellar Conversions
I’ve cancelled them… will still get some PIR for the floor (50mm). Still deciding on finished floor - would have liked an amtico etc, but need floating flooring. That said, if I put double lapped OSB down, is that secured in anyway and suitable for adhered floors, or is that still left as a floating floor? anyway, I’ll build an internal stud frame now. Still need to figure out the external poly sheeting under the cladding. With a new stud frame, I’m guessing okay to tie it to the plywood; there’s no issues with damp etc? I’ll probably put a poly sheet under plasterboard, unless I can foil tape the uprights and silicon seal as they go on etc. -
Converting wooden workshop to office
Adthrawn replied to Adthrawn's topic in Garage & Cellar Conversions
Okay, so would require removal of the old poly sheeting (it’s under the cladding at the very outer)? or would high level vents that cut through the poly be sufficient? I wouldn’t have to remove all of the cladding - I could even maybe get away with removing internal plywood as well to remove the poly if needed. -
Converting wooden workshop to office
Adthrawn replied to Adthrawn's topic in Garage & Cellar Conversions
-
Converting wooden workshop to office
Adthrawn replied to Adthrawn's topic in Garage & Cellar Conversions
-
Converting wooden workshop to office
Adthrawn replied to Adthrawn's topic in Garage & Cellar Conversions
-
Converting wooden workshop to office
Adthrawn replied to Adthrawn's topic in Garage & Cellar Conversions
-
Converting wooden workshop to office
Adthrawn replied to Adthrawn's topic in Garage & Cellar Conversions
I’ll post some pics in a minute… The plywood is painted internally - if that’s taped at joints, will that not create a trapped void between the existing poly sheeting under the cladding and the ply? -
Converting wooden workshop to office
Adthrawn replied to Adthrawn's topic in Garage & Cellar Conversions
It’s definitely something I’ll be fitting, but not quite sure what form it’ll be yet. To what degree would that change the wall buildups? -
Converting wooden workshop to office
Adthrawn replied to Adthrawn's topic in Garage & Cellar Conversions
Yeah, I can cancel them tomorrow. I do plan to use some for the floor, so will keep that. The tricky bit is the current wall build up. Starting with cladding/poly/void/plywood, I’m not sure now what to do. Not sure if I can loose 160mm internally by building out, but could be the best option now. Either way, a big concern is outfitting internally to find the external shell has a damp issue etc. or all of the internal materials get damaged. -
Converting wooden workshop to office
Adthrawn replied to Adthrawn's topic in Garage & Cellar Conversions
What software are you using for calcs as well? I’m trying to figure out the layers, and where the vapour barrier should go, and if it’s okay to sandwich the existing plywood, a barrier and then thermal plasterboard together - or if there needs to be an air gap for the plywood. My principle aim is to reduce/mitigate damp AND massively boost the thermal properties of the building. I could put a 63mm gap between the plywood and vapour barrier with studs. Also addressing your comments about the existing external barrier - I wanted to remove it (mostly as it seems to be a potential cause for any damp there is now), but also my thought was to fit ventilation for the exterior void. I might fit a breather membrane in to stop water ingress. The cladding is not perfect, so water ingress is possible. I’m very confused now, and back to square one having thought I’d figured this out! Materials on the way too 🥴 -
Converting wooden workshop to office
Adthrawn replied to Adthrawn's topic in Garage & Cellar Conversions
Thanks for that! The building is definitely trapping moisture inside - I don’t think the polythene sheet is helping matters. Ventilation will help of course. I’ve ordered both the PIR and thermal plasterboard (plus vapour barrier). Will be using the 50mm on floor too. Taking the cladding off, affords me the opportunity to check the structure. Ivy has gotten under the frame in a few places, plus there may be some damp patches too. As I’ll need to take the metal roof trim off as well, it’s also going to give me a chance to refit that and improve water tightness all round. I’m also fitting a large bifold door, so will have rework the front wall anyway! I know we’re putting quite a bit of money into it, but it’s going to be our workspace for the next 5-7 years easily and we’ll have some specialist printers in there that need to be kept warm… -
Converting wooden workshop to office
Adthrawn replied to Adthrawn's topic in Garage & Cellar Conversions
I’ll add, that the conversion for us is to turn it into a proper office/studio building - we’ll have print equipmen in there, and some needs to be kept around 20C. I’m trying to do what I can to retain as much heat as possible. Even now, during very hot days, it’s warm, but it’s not hot. That gives me hope that during winter the heat loss won’t be too bad. With the refurb we’re doing, it should perform better than our concrete block/steel frame office in a business park 😂 -
Converting wooden workshop to office
Adthrawn replied to Adthrawn's topic in Garage & Cellar Conversions
From what I’ve read up, ventilation in the insulated void is key. I think a rock wool is your best bet. You could always internally insulate as well, and put a vapour barrier over it (or just seal the edges of PIR with silver tape). -
Converting wooden workshop to office
Adthrawn replied to Adthrawn's topic in Garage & Cellar Conversions
-
Converting wooden workshop to office
Adthrawn replied to Adthrawn's topic in Garage & Cellar Conversions
I've been back and forth on what to do, but thinking of something like this: [external cladding] -- [2x3" frame]+[50mm PIR inside frame] -- [18mm plywood] -- [vapour barrier] -- [62.5mm PIR insulated plasterboard] I want to avoid removing the existing 18mm plywood internal walls, as the frame was built with it in panels, and has been overlapped, so in corners I'll have to cut the plywood in order to remove it. Instead, I'll just be removing the external cladding, pulling the old membrane out and removing the old insulation. I'll check the inside face of plywood and the frame as well. The old membrane is definitely in the wrong place, so that really has to go. I then plan to fit 50mm PIR into the frame, pushed against the internal plywood skin - and PU expanding foam in gaps. That'll give me a 20mm air gap between the cladding and the PIR. I'm hoping the exposed frame is enough to allow moisture in the frame and plywood to dry. At the top of each frame void, I'm planning on cutting a ventilation vent, with something like a 50-60mm vent. I don't think I need a bottom vent, as the overlap of the cladding isn't amazing anyway so should air out. If there are noggins, need to figure out how to allow ventilation around them. Over the internal plywood skin, I'll fit a membrane - and will seal that with the membrane I'll lay on the concrete pad (I've made assumption it's not insulated). I'll then put 50mm PIR onto the floor, and will fit 50mm insulated plasterboard (it's 62.5mm finished thickness) over the plywood. Now, my next concern is if the plasterboard needs to be kept away from the vb/vb away from the plywood layer? The drawings I've seen show the plasterboard on the vb, which is fine - but rather than having OSB etc on the outside of the frame, I've got plywood on the inside of the frame. I don't know if I'm trapping the plywood to the degree it'll never be dry... Or if the exposed timber frame will be sufficient to allow the plywood to dry out. Frustratingly, the manufacturers provide very contradictory information - Kingspan's site says one thing in the PDF, their calculator shows completely different installation, and then advice is differing again. -
Converting wooden workshop to office
Adthrawn replied to Adthrawn's topic in Garage & Cellar Conversions
Hi, Is it worth putting a breathable membrane under the cladding? Or just cut the poly out, re-insulate the studs, and put a poly over the ply? So I’m guessing the objective is to leave the insulation and the studs open to the external air, and stop moisture from passing into the plasterboard/top layer (we might skin in plywood as the decor finish)? Your comment regarding the PIR - is this a bad thing that the damp will go through the studs? Or do you mean that it will need to be exposed in order to dry out? Thanks -
Converting wooden workshop to office
Adthrawn replied to Adthrawn's topic in Garage & Cellar Conversions
I’ll also add, I may need to work from the inside if I’m not going to get a straight run to do outside (kids etc, so don’t want to leave exposed). I’m hoping I can cut the barrier from the inside, and pull as much from between the frame edges and the cladding. -
Converting wooden workshop to office
Adthrawn replied to Adthrawn's topic in Garage & Cellar Conversions
Thanks! I don’t know the stud centres yet, I should probably measure the screws in the plywood. I’m U.K. based, so would hope the guy who built it did 600mm. Regards to vapour/breather membranes, which is better to fit? An external breather or internal vapour, or both? If I use PIR, then effectively I have a vapour barrier with the foil backing? I could look at insulating the frame, and also fitting plasterboard with integral insulation, but then with the plywood sandwiched in there, where does the vapour barrier go? Should the vapour barrier go under the plywood layer, as there’s also foil backed plasterboard that could be vapour barrier, but again that’s over the plywood. Making sure the place stays dry is the objective, so whether that’s no membranes or putting new membranes etc somewhere - I just don’t want to end up causing/continuing issues by putting something in the wrong layer. 🥴