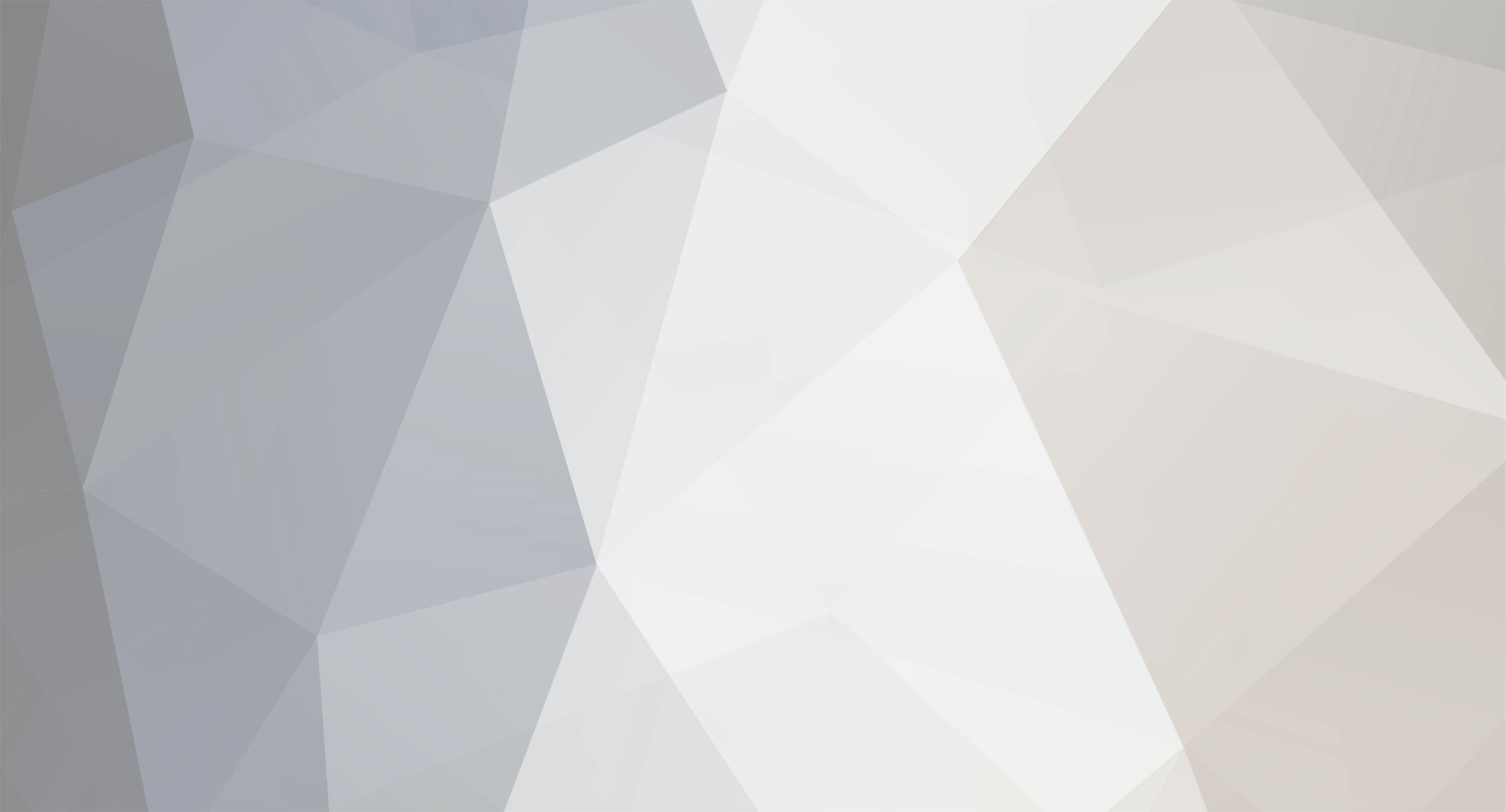
btm3055
Members-
Posts
12 -
Joined
-
Last visited
Recent Profile Visitors
The recent visitors block is disabled and is not being shown to other users.
btm3055's Achievements

Member (3/5)
1
Reputation
-
That internal wall took me about 5 hours, going slowly and drinking lots of tea. I imagine I’ll get faster when I’m not triple-checking everything. I’m aware it’s a big task, but objectively: The last place I lived was smaller, with one fewer bedroom, was made of flint and had zero insulation, was rodent infested, had rising damp, and black mould. Plus it cost me £1500/month to rent with zero legal guarantees. And that was probably the best place I ever rented — there aren’t that many options. This place is basic, but liveable. We have mains electricity (although I’m having that updated now), we have running water (albeit only one tap), we have a toilet and a septic tank, most of the work that needs doing is doable by me, with the tools I already own (excluding the electrics). Plus it’s free and we can live in it while I work. The key (I think) is to keep the plan nice and simple. Get it signed off by building control so I’m confident I’m not doing something really stupid, and then go section by section until it’s all good.
-
@Iceverge — thanks, I’m going to have a second look at the foil. It’s starting to sound like a waste of money. I’ve attached a before and after image of an internal wall. Left: 3x2 frame, verticals ~80cm on center. Right: 4x2 treated CLS, 40cm on center, left the original frame in place where possible and added battens to the 3x2 to get it roughly level. This wall’s urgent because I need to run electrics along a utility channel in here. (The current wiring is very old and probably dangerous, so the sooner the better.) However, because it’s internal, I can get to the other side no bother, so as long as I don’t need to change things like the membrane, I can do most of the work from the other side. I may just put up some sheeting, add battens for the utility space and call it done. (Incidentally, you can see the end wall that’s an emergency repair to an external wall. That moved about 10cm in each direction when you leant on it. So that frame got hastily patched up this summer. However, it needs to be rebuilt again as it’s just a frame the outer T&G and some membrane to stop drafts.) The budget is more about time than money. I can afford to spend £1000–£2000 per month. I’m expecting it to take five years, and cost in the region of £100k. As I work full time I can only work on it evenings and weekends, so at the moment I run out of time before I run out of money. However, once I have to pay people (like electricians) I will eat through the budget pretty fast. The T&G on the outside is dirt. It was replaced in the 70s and they’ve used untreated softwood painted with some kind of gloss paint. Somewhere around 40% is rotten, so it all has to go before it gets into the frame. However, I can probably save ~60% of it and make do for now until the price of wood comes down. (Oddly, the side of the building that faces the sea isn’t so bad, it’s the sheltered side that seems to be worse. @George — thanks. Yeah, the foil is probably off the table by now. No one seems to rate it. @Temp — Nope, no DPC at all. Just a wooden frame fixed to a concrete slab at the back, and a wooden frame on stilts at the front. I’m planning to build a short 30cm concrete wall and rebuild the external frame on top of that. But I need to work out the width of the wall first. The damp course will get slotted in there somewhere once I’ve worked out the details.
-
Thanks for all the replies. I have the winter to make these decisions, because the weather’s just too unpredictable now. But I do want a plan soon, if only to get a budget in place. @saveasteading — I went for foil because the front part of the building is on stilts, so weight is an issue. I thought foil in the roof would save a bit there, and it seemed to make sense to continue the same insulation down the walls. The external cladding is likely to be larch, and possibly beaten brass or copper for the bottom 30cm to keep the wood off the ground. We’re still debating that, and the price of wood means it’s likely to be recycled from the current cladding for a year or so (the whole building is tongue and groove inside and out). @Iceverge — No, renovation. We’re living in it, and funding the build with what we save in rent/mortgage. So yes, it’s a bit of a jigsaw, and flattening it and starting from scratch would be easier and cheaper. But for a few reasons, that’s not happening. I have spent an unexpected amount of time reading about the difference between OSB and ply. It seems to be more polarising than brexit. I guess I opted for ply because I’ve used it in the past, so I was going for something I was familiar with. Literally everyone else says OSB though. The insulation we like is hemp (https://www.ecologicalbuildingsystems.com/product/thermo-hemp-combi-jute). Mainly because it doesn’t require any specialist equipment to install. The manufacturer recommended a moisture barrier on both sides of the frame to keep it in place, but I guess the racking would do the same job. Thanks for the Ubakus tip, I will play with that. @George — The foil insulation needs an air gap on both sides to be effective (minimum 38mm). I bumped it up to 50mm on the side closest to the plasterboard to give me a more generous service void (just in case). If I dropped the internal ply/OSB, I could probably fix the foil straight to the frame instead of one of the vapour barriers — but maybe I should rethink the foil anyway.
-
(Apologies if this is in the wrong section.) For context, I’ve zero experience of house building, but I am pretty experienced with wood (furniture etc). I have a timber-frame wooden building on the shoreline in Northern Ireland. The weather can get a bit wild, and we’re quite exposed. However, it’s stood up for 100 years, and I’ve been told by locals this is in part due to the materials being pinched from the Belfast shipyards (and therefore treated for marine conditions). The walls (internal and external) currently consist of 3x2 frame, clad with 12mm tongue and groove, and stuffed with sawdust and wood chippings. Obviously that’s not adequate. I’m trying to arrive at a final plan for the walls before sending the plans off the building control. I’d really appreciate people’s opinions on the structure. Am I missing something, does something need to be chunkier, is there a newbie error in there, etc. (For example, I’m unsure if I need a moisture barrier between the frame and the plywood sheeting on the outside, given that there’s also a weather shield — I’m guessing it can’t actually hurt anything but my wallet.) My priorities are structural rigidity, wind/weather-proofing, insulation, a utility channel for electrics etc., and to be realistically achievable. Cross-section diagrams of external and internal walls attached. All opinions appreciated.
-
@ProDave thanks for the advice. I hadn’t really thought of that. We’re planning to build an outside machine room connected to a bank of solar panels, and relocate the box and the mains meter out there. But I suppose a cheap meter and a couple of plug sockets wouldn’t cost that much in the meantime. Thanks
-
Hi, Long story short, I have a timber frame bungalow that was built sometime in the 1930s. The wiring is all round-pin, and I believe pre-1946 when my wife’s grandmother bought it. The bathroom has a lean-to extension on the side where the outside toilet was attached to the main building sometime in the mid-60s. Both the bathroom, and the lean-to extension have mains electric with ceiling lights and plug sockets. I am going to demolish the lean-to, and retain the main building. I will obviously need a qualified electrician to install anything electrical in the bathroom because building regs would apply to any new work. However, can I safely remove the old wiring myself? My plan is to trace the wiring back to where it branches off from the rest of the building, turn the mains off, cut the wiring as close to the source as possible, wrap the connected end in electrical tape, pull the newly disconnected wires out, turn the mains back on. Does this seem safe? Is it the best approach? Would appreciate opinions.
-
I have a small amount of asbestos that I’d like to get professionally removed. I think it totals 5sqm of lean-to roof, a chimney, a heat screen behind an old range, and a few broken bits I’ve found around the site, the origins of which I’m not sure. I’ve contacted three local companies that are listed by my council to ask for a quote, and none of them have got back to me after more than a week. (Maybe the job’s too small?) Can anyone recommend an asbestos removal company that operates at domestic property scale in Northern Ireland? Demolition has ground to a halt until I can get this dealt with. Thanks
-
@dpmiller oh very close then. We’re just south of Ballywalter
-
Thanks for the advice on building control, I’ll speak to them just in case. @dpmiller very up the road a bit, Newtownards is my weekly Tesco shop
-
Thanks for the replies. I should probably have said Northern Ireland. We’re on the Ards peninsula. We could probably get some kind of mortgage, once it’s legally ours. For now, it’s still my mother-in-law’s. so we can do what we like, but not being legal owners until we inherit, I doubt we’d get any form of finance. And to be honest, I’d rather not owe anyone anything if at all possible. The whole row of bungalows has been replaced with block and render (we’re the last timber) and a couple of huge modernist mansions, so I’m pretty confident precedent has been established should we require planning permission. That said, I was surprised at how lenient the local planning is. Building regs is another matter, but I presume that things like removing asbestos and replacing like-for-like timber is fine. As far as I’m aware, there’s nothing to say we can’t occupy it full time — no covenant or anything like that, it’s just that traditionally my mother-in-law has only used it in the Summer. As far as I’m aware the asbestos is behind the old range, on the lean-to roof that covers the toilet, and the old chimney. I’m not touching that myself, so whatever it costs we’ll just have to pay. Photo attached. You can see the dodgy chimney, asbestos roof leading to the toilet, and my lovely outside shower that needs to be an inside shower before November.
-
Hi, My wife and I always wanted to build our own house, but self-employment meant financing was unlikely. However, we’ve been incredibly fortunate that my mother-in-law has all-but gifted us a beach-front timber frame bungalow with around a third of an acre in Ireland. This means living rent-free (and mortgage-free). So rather than knock it down and rebuild, we’re going to renovate without borrowing. The downside is that it’s a 1930s building that’s been in disrepair since the 1970s, and has only ever been used as a holiday home in the Summer. The toilet is semi-outside, there’s no bathroom, no insulation, the cladding is all rotten, the frame is rotten in places, the window frames are more putty than wood, at least one of the concrete slabs is subsiding, there’s no heating, 1930s electrics, and asbestos. Being positive, the outside toilet is a working toilet, the 1930s electrics do work, and the frame isn’t rotten everywhere, mostly just under windows. That is more than we had 2 months ago. Thanks to being rent-free, I have a budget of at least £1000 per month for as long as it takes. (Potentially more, depending on work contracts.) I’m estimating 4–5 years doing everything (except the asbestos, and the electrics) myself. The mixed weather we’ve had in the last few weeks has shown us that we won’t survive a cold Winter here, so I’ve got six months to try and make it weather-tight and warm. So much to do it’s a little overwhelming, so naturally I have started with a shed. Wish me luck :)