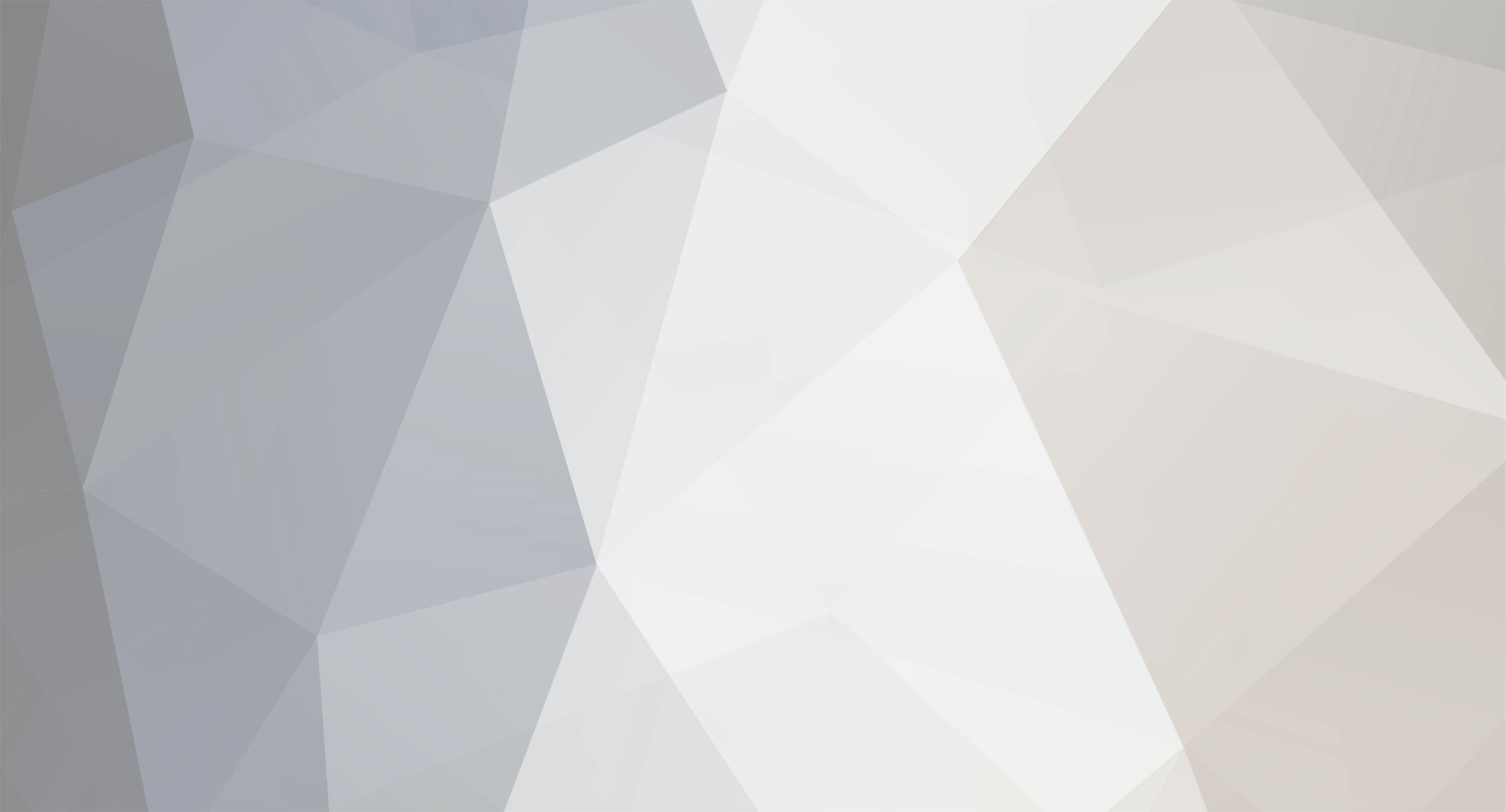
Kgthomas
Members-
Posts
38 -
Joined
-
Last visited
Everything posted by Kgthomas
-
Thanks, that makes a lot of sense about the overhangs and looks well constructed.
-
Good to know, especially that the storms didn't move it. I live at the bottom of a mountain range and the house is in a dip between 2 hills, so do tend to get some wind coming through. Is your garage roof made from steel also? If so why do you have the overhang on both sides? Thanks
-
Definitely, that is my concern and was why I had considered having the roof on a steel frame extending to the slab. Though then the weight is more on isolated spots rather than spread and has the issues of rendering the block and steel.
-
Good to know about the 16x wall thickness for being without piers. Happy to have piers in it. Wanting to avoid putting partition walls in it as it is for use as a garage and if I did put a partition wall in it would be very close to one of the end so would still end up with a long wall with no partitions. Hopefully the piers will be sufficient
-
Yes I agree the price of steel in increasing quite a bit but block has stayed steady. So think given that and the extra issues with adding steel, think I agree 6” block walls and then roof makes more sense, that was my original plan until I was told I’d have issues with damp. Makes sense about planning where the piers will be to allow for racking etc. Need to think about that too. Thanks again
-
Thanks for that. I am considering going with concrete block with piers rather than steel frame. Will at least remove one issue. Would be planning to use 150mm blocks so that should help. Then that removes any risk of the steel rotting. Had a look at the silicone system you mentioned and understand what you mean. Thanks to everyone’s help I think this is becoming clearer in my head.
-
That’s a good idea, I will speak to them about that thanks ?
-
Sounds like the best plan ?
-
Had a look this morning on building control regs for NI. It does state a maximum floor area of 70m2 so don’t know if that will allow me to use the info I found. I will have to check with them. It says the wall has to be at least 90mm thick with piers every 3m. Doesn’t say anything about if the blocks are thicker. I was considering using 150mm anyway and the piers have to be at least 3x the thickness so that would work out ok. I think.
-
Thanks, I must check that out with building control.
-
Ah good to know. Did you build piers into the block work too?
-
Thank you so much for such a detailed response. It is great to know that you have a similar setup to what I have in mind and not having issues with damp. Makes sense to take the bellcast to just above the slab. The path around the slab will be below the level of the slab and if I slope the path towards the rear of the garage, as I have a land drain behind the garage. Using silicone to seal the bellcast and sand / cement with waterproofed below makes sense. Then paint to add another layer of protection. I do prefer the option of block and if I could include a steel frame for the roof then that should give good strength there too. Just need to look at options for getting mortar to adhere to the steel. I’ve seen an adhesive for attaching block work to steel from CT1.
-
Good to know you have done something similar and not had damp problems.
-
Thanks, you are right - first of I need to figure out how I want to build it. If going with the block and steel framing, I will have to see how I can get the mortar to adhere to the steel.
-
Have seen that you can get non drip panels for the roof also. Though was told if you put skylight panels in that’s where you are most likely to get condensation.
-
Thanks for the reply. The DPM does not extend beyond the slab, the person who laid the slab did not do that. So if I brick it up, I might have to look at options for that. I was thinking I might need to put internal piers in the walls given the lengths. I had also considered the idea of supporting the roof on steel framing and using concrete blocks in between. So for the side walls I’d have 5 uprights so roughly 2.75m of wall in each section and for the end there would be 4 uprights so roughly 2.7m of wall in each section. Only part which may be difficult is the end with the garage door. Obviously the corner uprights would double up between sides and end. Though don’t know how well the sand and cement would adhere to the steel? Or if that would bring moisture into the steel and cause it to rot. Though, maybe I am over complicating it?
-
Ah ok, that makes sense. So am I right in thinking if the block work was taken to the edge of the slab and then a sand and cement render applied to the block work, this extends the exterior past the slab? Or is there another way around this? Thanks for the reply
-
Hi All, Several years ago, we poured a concrete slab with the intention of building a garage. Unfortunately for several reasons the project came to a halt, mostly due to funding and needing to replace other items in the house, such as heating. Now we are in the position to complete the garage. The slab is 8x11m and the intention is for the garage to be the full size of this. The slab was poured in 30N concrete and was 12" deep at the edges and 6" deep at the middle, the base was reinforced with steel and had a DPM installed. The slab was dug out and backfilled with gravel also prior to having the slab poured. There is a pathway around the slab which will be below the level of the slab and will be concreted. I have priced the garage in steel however I am wondering if concrete block may be a better option? Either way we intend to have a steel roof on the garage. I was considering a single block wall but was advised by a retired builder, that I would suffer from damp due to having poured a slab rather than using a trench foundation with a floor installed after a couple of courses of blocks. The retired builder said we would be better with a steel garage as there would not be any issues with damp. This does confuse me, I do not understand how the steel would prevent any damp? I know concrete blocks are not watertight but I think sand and cement render is? If the retired builder was suggesting damp could rise up from the slab then I would imagine that would be the same with a steel garage? The retired builder said the only other option would be a cavity wall to prevent damp. I had asked a builder for an estimate to build a cavity wall structure with steel roof and his estimate was approximately £3-4k more than steel. I have priced concrete blocks locally and they do appear to be a cost effective option, I know that is only part of what I would need. To me, if I opt for the steel garage then there will be no insulation and more importantly, I am limited on where I can put items like plugs etc. The solution around this is that I clad the inside of the shed and put insulation in, this however increases the costs again. If I was to opt for the concrete block and steel roof construction, then if I go cavity wall I have an increased construction cost. If I go single block wall with sand and cement render, that should be waterproof? Then again I could clad the inside of the shed and put insulation in? Don't know if that works out cheaper or not? We live in a rural area and as such we do get quite high winds at times so do have some concern over a steel structure also, it will look completely different to the house which has a pebble dash render. Whilst the sand and cement will not be pebble dashed it would be painted to match the house. Or I believe it can be coloured white also? Any advice or suggestions are welcome. Thanks
-
@Onoff the strange thing is I'd brakes to change on my car so I decided to use the concrete base to work on. Initially I thought I would comfortable get 4 cars into my Garage but seeing my car in there it seemed a little short length wise.
-
@Alexphd1 as @JSHarris said it was more of a practical idea for hanging tool boards on etc. Looking at cost I’ve seen cladding sheets advertised on gumtree for £2 per metre. Don’t know how good it is but if I take my dimensions of 11x8m that is 38m times the 3m height so 114m costing £228 for block I think I will need 1300 at £42+VAT per 100. Therefore £655; I had thought that I wouldn’t need to insulate the inside and the lower cost of cladding would have been eaten up in having to clad the inside. Using the steel framing as my father in law (retired builder) told me an 11m single block wall wouldn’t stand under the weight hence why I’m combining both. He said this based on me not having any internal walls etc to brace the structure.
-
@StructuralEngineer yes that is what I am thinking of doing. If I tie the block work to a cross member I am hoping to get the block to 2.5-3m high. Then put the steel roof on top of it.
-
Yeah must have a look at icf blocks. I think a house beside me was built with them recently.
-
Yeah to be honest looking at the costings it’s probably as cheap if not cheaper to use blocks.
-
They look like a good option. I’m also thinking with cement in them they should be strong so may satisfy Insurance requirements.
-
Ah that is good to know and could ultimately sway the decision on materials.