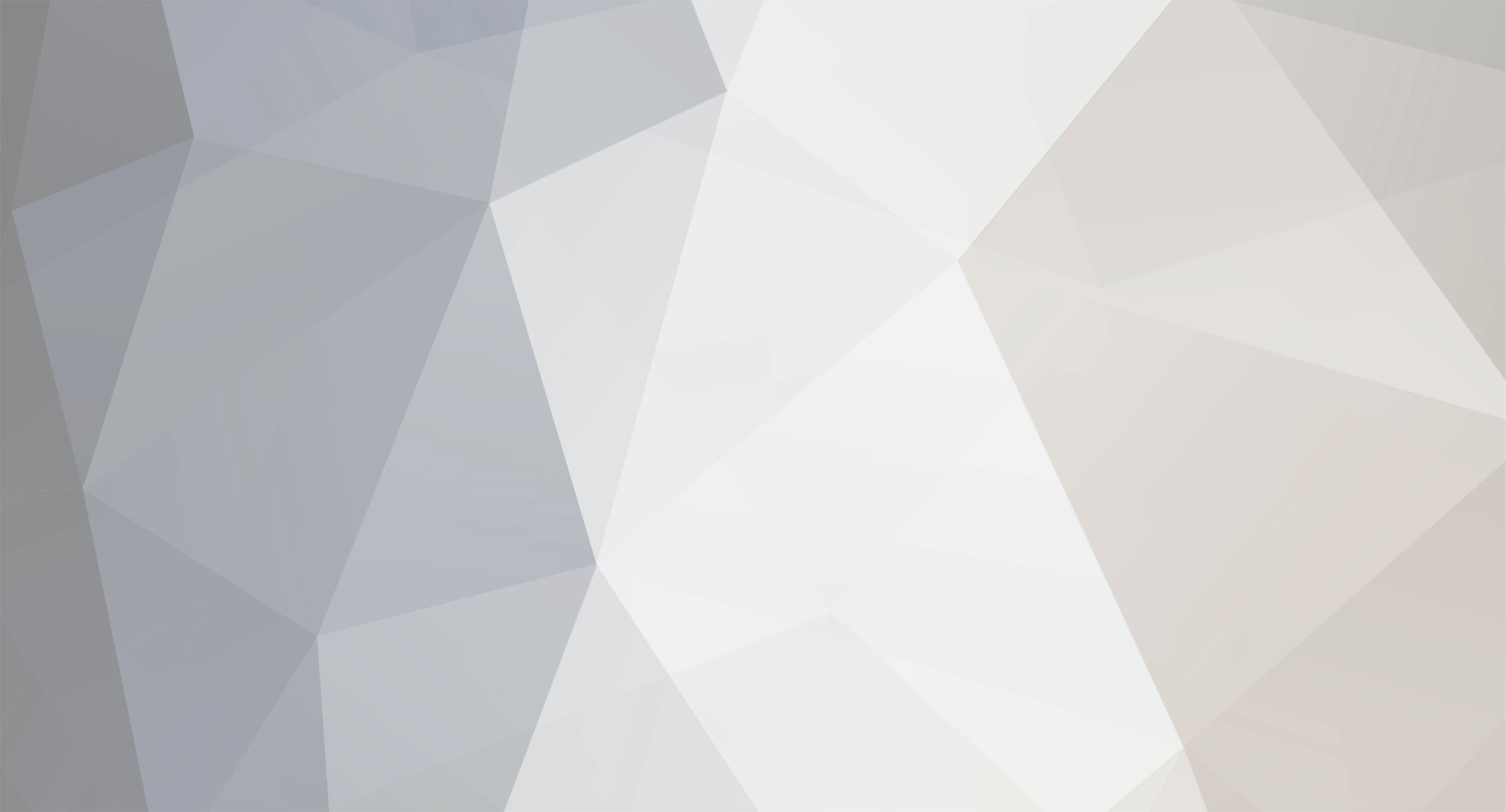
DanB
Members-
Posts
14 -
Joined
-
Last visited
Everything posted by DanB
-
Many thanks. Final answer (as they say on Millionaire) - I've given it some thought and I'm going to go with PIR sensors in the en-suite bathrooms, and a demand push button at the kitchen sink (don't want to use PIR in kitchen as it is an open plan kitchen/dinning/lounge so would trigger all the time). Just so that I learn something, I understood a lot of what you said...but what is "HRC"? - from context I'm guessing that is the recirculation loop?? And "UVC" I couldn't figure out at all? Sorry for my ignorance!
-
Thank you Nick, from Wales, much appreciated. Will do on the insulation and will do on the pipe sizes. But I thought that the pipe stat on the return pipe was a good idea? Set to something like 40 deg C kick in, it would recirculate for a couple of minutes and then switch off circulation pump when circuit back up to temp, what am I missing (I'm missing lots these days I've realised, but I mean specific to this!) I personally don't mind running the pump continuously as we are 100% off grid/solar, it was only the heat pump HW cylinder manufacturer instructions that spooked me on that. This is what it says in the manual "Stiebel Eltron advises against the installation of this appliance in any recirculation loop. Always install a recirculation loop with a thermostat cut-off or a timer. Installation without these devices will cause the appliance to run continuously, resulting in high electricity use and extended compressor run times which will reduce the life of the appliance and void the warranty. The Accelera energy efficiency will drop when installed with a recirculation loop due to the reduction in thermal stratification of the tank." Thermal stratification I think is the key point I suppose, as continually mixing up the water will keep triggering on the compressor.
-
So I had thought about that, but had ruled it out because I had reasoned that once you open the tap then you are wasting water and you still have to wait for the hot water to come around? So would it make any difference even having a recirculating pump in that case? What I really want is for the water to be hot locally before opening the tap.
-
Thanks for confirming that on the pump head, that's exactly what I thought but just couldn't get my "head" around it!? (sorry, that is truly terrible humour). I do like pipe stat (in combination with a timer). I think I've decided to try and keep it flexible for now (i.e. put in conduit and a few spare control / signal wires to a few different locations during construction) then as you suggest I can see how the cylinder operates once I actually have it.
-
Thinking about it more, pipe stat is a good shout. If I put a stat on the loop at the furthest distance away, and also use a digital timer to turn off the pump completely at night, and finally use pipe insulation then I think that will do it with the least amount of cycling and be the simplest solution...
-
That's interesting, so I suppose I would put the pipe stat on the loop just before it returns to the tank? I had done a few calcs to work out how often I might need to recirculate.... With 60 deg c water and 30 c ambient, using Q = c m dT I've calculated that a 1ft length of 1/2" pipe full of water holds around 1.2 Wh of energy and heat loss using Q/t = σeA(T24- T14) is around 2.5W ...so in other words the uninsulated pipe would lose most of it's heat in about half an hour. Also my total volume of loop pipe is around 40 litres so if I had a 40 LPM pump then I could program it to run for 1 minute every half hour. If I insulated the pipe I could probably get that to 1 minute every hour, and also have it turned off overnight. What about pump head? Most are quoting max 5m, but height difference from top building to bottom is around 20m in my case (with the pump sited roughly in the middle).. If the system is closed and pressurized this doesn't matter from what I've understood, is that correct?
-
Sorry for lack of build updates from Antigua, but construction site has been hectic and not had much time...Will upload some new pics in coming weeks. I do have a potential snag in designs this week with the plumbing – specifically hot water. The issue is that the house design is several buildings, spread out over the site: one main building (which will contain the hot water cylinder – an air to water heat pump HW cylinder) and 3 remote bedrooms. Now water is more precious than electric for us (since the HW cylinder will be solar powered, but water is 100% harvested from rain water and we can have months of drought) and so there is a problem in that the furthest bedroom with have around 200ft of pipe from the hot water cylinder. Using ½” pipe then 200ft gives aprox 2 gallons / 8 litres of waste water in order to get hot water through… Solution is obviously a recirculation pump, with a dedicated return line (or in fact one big HW loop encircling all the buildings, with a short spur off the loop to each building). But I’m looking for suggestions on how to manage the pump. Since the HW cylinder is a heat pump, then the manufacturer recommends against a continuous recirculation pump because it will cause a lot of compressor short cycling... So I was considering perhaps fitting PIR motion sensors in each bathroom with adjustable timers to activate the pump. Or alternatively a fixed interval timer that runs the pump for a couple of minutes at a time (and switched off at night). Any suggestions on the fixed interval time? (Assuming ambient temp circa 30 deg C and water temp 55 deg C, with plastic pipe uninsulated and buried in ground – probably want it to recirculate when it drops to 40 deg C) And also does anyone have any recirculation pump recommendations? (Final thought, I also have around 70ft altitude difference between highest and lowest building…obviously the water will be sufficiently pressurized but wondering if this “head” difference might present a problem to a recirculation pump…)
-
Exactly. And those are the skills that I have (since my experience is mostly in renovations and extensions etc). I also do cabinet making so will be making my own kitchen and bedroom furniture from local raw materials, and anything to do with joinery, plumbing, and electrical I'm good with (my formal training back in the day was electrical engineering). I'm planning to do a 20ft container from the UK in a few weeks time with bathrooms, kitchen worktop, etc so I have everything ready.
-
Assumed wrong! 😂 I've done about 50% of what you see so far in the pics (very very tough going in this heat). But I've got local guys in now to get me to roof level. I'm estimating a total of £70k pounds for all my outsourced labour. My own labour costs...priceless!
-
The key to that is increasing the minimum concrete cover by at least 25mm. So I'm aiming for the rebar to be at least 50mm off the sides of the form work, and 75mm off the ground.
-
Yep, I've heard similar, I think this applies to wood frame houses. The spec with concrete (with wood roof) is having a concrete ring beam all along the top of the walls 16" deep x 8" wide with 4 x 5/8" longitudal rebar & 3/8" stirrups (like a wall plate but much much stronger!) and you have 2 lots of 1/2" rebar coming up through the cinder block wall all the way from the foundation, bent and wrapped over every 3x6 rafter and back down into the cast beam... So you build up the wall, fabricate all the steel work and form work for the 16x8 RCC beam, built the roof frame, and finally cast in the concrete (which also fills up the cinder blocks with concrete all the way down). That way you could virtually pick up the house by the rafters (and certainly if the roof is coming off it won't be due to the wall connection). Here is the drawing:
-
Been on the forum barely 5 minutes and already the guy wearing nothing but an acid smiley face and a bag of crisps wants to travel half way across the world and meet me in person...what could possibly go wrong?! Joking aside, yes of course with pleasure. If you book then let me know and I'll share my local whatsapp number. Budget USD, I paid 200k for the plot. I originally had a build budget of 450k, but funnily enough I've spent the day on excel as I've been getting more firm numbers back in...think I was too optimistic, but not only that I'm finding a lot of material costs (and shipping, given that everything is imported) has gone up since I started planning. It might end up closer to 600-650 for build so absolute max 850 all-in with the plot. That's all in USD, so divide by 1.3 for sterling.
-
Thank you both for the warm welcome! ProDave - yes I would say so, crime rate here is virtually non existent. To give you an idea this is the photo below of our current house (didn't build it) which I've just taken for you now. As you can see apart from some sliding bug screens it is completely open to our lounge/dining, and open through to the bedrooms and not had an issue in 6 years. Even if we go out for the day it is open. If we ever go away on holiday we can board it up, but honestly only for storms, not crime. Building regs...what are those?! Only kidding, but they don't really exist here. Nor does planning really...the process is that you do have to submit an application (which costs £0.15p / ft) but it is just a rubber stamp job, nothing has ever been refused / rejected. In terms of building regs, no one ever comes to the site or finished build to inspect, there is no "code" and no final sign off. If you believe that you may need an engineer then that is up to you, but no calculations are required to be submitted. That being said they do seem to build structurally to a very high standard here - don't forget that we are in an active earthquake zone, and high risk hurricane zone. So people here tend to do things out of self preservation rather than being told what to do. Builders here rely heavily on reinforced concrete "rules of thumbs" for column, beam, and slab sizes - as is very common in other emerging economies such as India, Pakistan, and much of South America.
-
Hi, new to the forum, have kept coming across the forum every time I've googled for a solution to a problem, so thought I ought to finally join! I'm English but moved to Antigua 6 years ago, and finally bought a plot of land last year and started building in the new year. Quite a few challenges building out here, but also quite a few advantages too. I'm doing a self build (although I do now have a local builder helping me to get out of the ground on 2 of the 4 buildings - cheating a bit I know, but it was taking me forever plus I was missing some key bits of knowledge/experience). It's also my own design, and I don't have an architect or project manager (other than myself)...so a text book case of "how not to build a house"? I do have some experience from doing my own extensions and house gutting and renovations in the past, but I've never done a complete house or new build before. The plot is one acre, on a 6/12 slope (aprox 26 degrees) and the key unique concept is modular buildings - instead of one big house there will be 3 bedrooms and one main house all as completely separate buildings and not connected. The advantage being that, given the relatively steep slope then the construction can sit into the landscape much better with less excavation of granite (and the disadvantage is that you get wet if you want to go to bed and it’s raining!) The main house is 40’ x 28’ and is one single open plan space of kitchen/dinning/lounge that is also open on 50% of the walls – there is no glass or windows at all in this building...in order to benefit from the cooling trade wind breezes. There will be integrated roller hurricane shutters for storm conditions. Construction is mainly cast reinforced concrete columns and beams (with 16” cinder block shear walls) with open/cathedral ceilings of 3x6 rafters and 1x6 v-joint/t&g roof boarding. The entire construction is 100% off-grid. Water is collected from roof gutters, fed into a 30,000 gallon water cistern for domestic fresh water. Self composting septic tank & soak away. 12kW solar array with 25kWh lithium-ion batteries and 18kW LF inverter. Hot water via a 300L all-in-one heat pump. Another interesting feature is UFH in the main building. Since there are no windows then air conditioning isn’t possible (and shouldn’t be needed) but in order to prevent the concrete floor slab and superstructure building up heat and radiating it back, then hydronic UFH will be embedded into the concrete pour and supplied by a monoblock heat pump (obviously running in reverse / cooling mode!). Heat pump will only be active during the day (when there is sun on the PV and excess power) and the thermal mass off the concrete will store much of the energy (along with a large buffer tank, circa 500L). Tons of other details but don’t want to send everyone to sleep on my first post. I’ll include a couple of pics of progress so far. I also have a few questions to ask so will try to make another post or two during the week. Pics: (Front half of main building, forming utility/basement. Rear half will be 30k gal cistern. Then main house floor will be over the top) (Master bed, up in trees overlooking the whole plot down to the road)