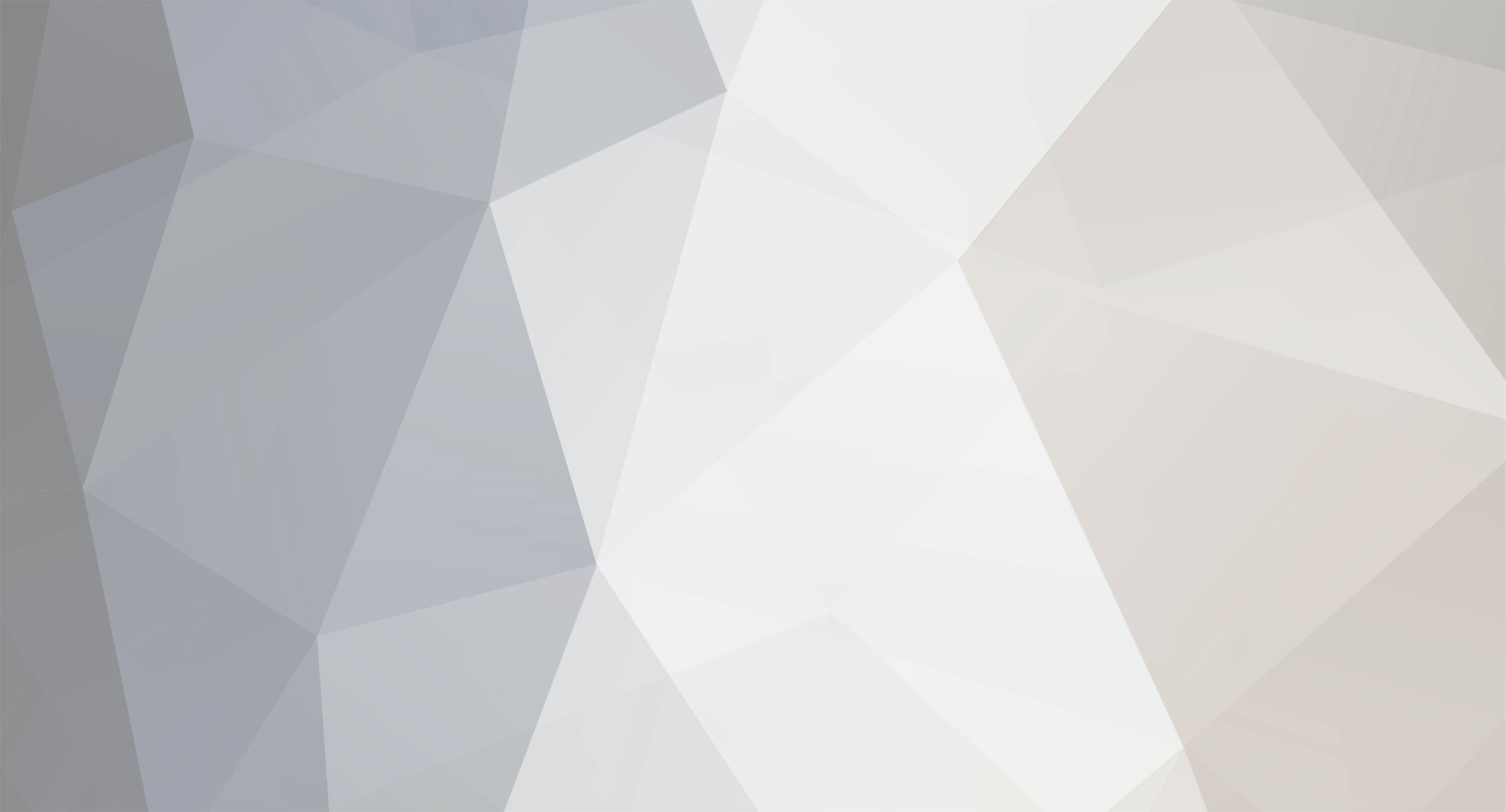
HJB
Members-
Posts
25 -
Joined
-
Last visited
Recent Profile Visitors
The recent visitors block is disabled and is not being shown to other users.
HJB's Achievements

Member (3/5)
2
Reputation
-
Hi As per my other post I have been subject to a landscaping disaster. I will be having a professional look at this, but I am just look for some advice, on lift and re using the sand stone paving? Are these fairly easy to come back up and then re use? Looking at some you tub vids it does seem to be that they lift up, with the mortar bed attached and a couple knocks with a hammer and chisel and it falls off leaving the slab in tacked. Anyone able to provide ant advise? Thanks
-
I showed them the paving suppliers guides that have no mention of the word sand, they still claim this is the proper way and and done this 1000s of time and no issues! They said the DPC is not an issue as the patio stops short of the house, and water has to cross a aqua channel drain, plus a 15mm soakaway chips channel before getting to the vents. I did kind of bring work to a hault, but as I stupidly paid out 50% up front to cover material and the initial labour and also I cant have the garden left as at is over winter until I can get it sorted, plus they were starting to bang on about labour so far has been over the 50%. `I thought best to proceed, challenge this at the end and potentially withhold final payment until its checked out, although I think they may have done just enough to cover themselves. I have all emails kept where he states what he is doing is correct, and that he offers a guarantee for 10 years, so if I want to stand any chance I think I have to get some flood defense items, and when the next down pour happens film it and they start the battle with him. As you rightly mentioned I have enough info supplied here and thank you to all you kind people for your help, unfortunately for me the war is just beginning, and least I still have final payment to make, but not sure who I can get to back me on this, doesn't seem to be regulated. I could email my local council planning office with some photos for advice but not sure they will be overly interested. Sadly I think I will have to admit defend and wait for battle to commence down the line. The best bit for me is the suppliers guide to a sub base and has a photo of a guy laying the paiving on the mortar mix and guess whats under the mortar, type 1!!!!!
-
It’s too far gone, only thing I can do is get someone in to check but then it’s just one word vs another not sure what I would be able to achieve. I may have to ride it out until something happens like water into the vents and then I have evidence to go back to them on. My other option is rip it all up in the summer and start again, losing out on thousands! I don’t get why they didn’t dig it out, I pay for the digger, labour, and skips!
-
I suspect making it up as they go along to suit there needs to complete the job. Nothing worse when things like this happen, trust in someone to deliver to your spec and within standards set by the industry. Anyone ever had to sue a trades person before. I suspect they will have done just enough to keep they head above water. No idea how their reviews are so good. Maybe people don’t take note during the build.
-
I presumed the bottom of vents were the DPC? They are prob going to be 50mm at best below the vents
-
Does anyone know if there is a governing body that you can get to check this kind of work? Major concern now is that the level is not 150mm below the air vents. They have said a thin row of chips and the aqua channels means it will be ok but tbh I am at the stage now I would like someone authorised to check the work.
-
I think I found what he meant when he referred to sealed. This is for larger construction work form what I can read this blinding layer. “In construction, blinding is a base layer of weak concrete or sand that is laid above a layer of hardcore to provide a clean, level and dry working surface. A thin layer, usually around 50 mm (2 inches) thick, of blinding is poured over the hardcore, sealing in the underlying material and leveling off the surface”,
-
I also think he lays the gro fabric on top of the sharp sand before the mortar mix which would make the bond even worse...?
-
I yes typo on my part 30-40mm Yes what you are saying is spot on about it lifting, the sand to type 1 is weaker than mortar to type 1.
-
Partner is a solicitor so that’s covered, I imagine it will be a claim against the full lot not just a repair. yeah I checked and it will be a proper pointing that’s wet.
-
I'd say a lot of wasted unneeded materials and labour going into it, just to increase the chances of something going wrong
-
yeah fully agree with you. I cant understand why they are so amendment by this way. Like I said before cant be cost, and its not to save on labour as its more work, work comes with 10 year guarantee also so in my eyes they are setting themselves up for a massive fail. I just cant comprehend why they would do more work for something that isnt needed, its normally the other way round. There are amendment that the sand is needed to provide the bond and fill the space in the type 1. It seems to be a bed of about 300 -400mm sand, its hard to tell.
-
My question to them was what is the added benefit of this additional layer of sharp sand. The response was and I quote "for all sandstone paving is a sub base of type1 then compact, then the layer of sharp sand and compact followed by the mortar and slabs. " No other evidence other than that. They have photos going back 6 years on Insta/facebook...have 5 stars and recommended a lot. I cant be the only one to have questioned this...surely! Maybe just nothing has gave way yet on the work they have done.
-
Too far into in now, and cant have the garden left the way it is over winter. I've taken photos through their work, have it in writing what they are saying so if it all goes wrong I will hopefully have some come back!
-
The slabs are sandstone though not Concrete slabs The sandstone will be going on a full bed of cement and sand mix as per how sandstone should be. Everything I read or watch says that above the 100mm type 1 should be sand/cement full bed mix, but these guys are putting in a layer of sharp sand, it just makes no sense, and its more work...I am hoping someone can shine some light to it. Its not cost as from what I can see type 1 and sharp sand is about the same, so if anything if costing me more for this layer, and costing them more time...pointless As it turns out the Geo Fab has not been placed between the Type1 and Sand, so god knows where this is going now possible between the sand and sand/cement mortar mix